田志成:工程机械产品质量控制及提升路径分析

【第一工程机械网 现场报道】2017年3月27日,由中国工程机械工业协会、国家工程机械质量监督检验中心指导,工程机械与维修主办,卓众企媒承办的“2017工程机械产品发展(北京)论坛暨中国工程机械年度产品TOP50颁奖典礼”在北京隆重举行。来自中国工程机械工业协会及下属分支机构、国家工程机械质量监督检验中心、相关行业协会以及工程机械制造企业、施工企业、科研机构、高校的200余位嘉宾出席本次年度盛会。
【第一工程机械网 现场报道】2017年3月27日,由中国工程机械工业协会、国家工程机械质量监督检验中心指导,工程机械与维修主办,卓众企媒承办的“2017工程机械产品发展(北京)论坛暨中国工程机械年度产品TOP50颁奖典礼”在北京隆重举行。来自中国工程机械工业协会及下属分支机构、国家工程机械质量监督检验中心、相关行业协会以及工程机械制造企业、施工企业、科研机构、高校的200余位嘉宾出席本次年度盛会。
第一工程机械网为您现场报道:
国家工程机械质量监督检验中心总工程师田志成出席2017工程机械产品发展(北京)论坛,并发表主题为《工程机械产品质量控制及提升路径》的演讲。
演讲嘉宾:国家工程机械质量监督检验中心总工程师田志成
演讲主题:《工程机械产品质量控制及提升路径》
互动嘉宾:太原科技大学教授、副校长 徐格宁
国家工程机械质量监督检验中心总工程师田志成发表主题为《工程机械产品质量控制及提升路径》的演讲
以下为演讲实录:
新产品鉴定时,通常会得出这样的评价:其主要技术性能和参数达到国际先进水平……
建议:进一步提高产品可靠性……
定型产品早期故障多,故障无规律,管控效果不明显……
如何解析?
关于先进技术和设计方法,我们的产品该用的都用了,本次会议会有不少专家进行分析和探讨。
在这里我想从试验检验的角度探讨如何有效地控制产品质量,如何提升产品可靠性水平,为此提出技术路径和技术手段,供大家参考借鉴。
分析基于三点:
其一,对国内外企业质量管理的多次评审与对比分析;
其二,对国内外企业试验检验能力的多次考察与对比分析;
其三,对国内外产品可靠性数据采集与分析。
关键问题:
定型产品没有形成完整的质量控制闭环
研制新产品没有建立完整的零部件可靠性验证手段或评价体系
说明:
指出的问题,大部分企业,特别是中小普遍存在,或多或少,但不是所有企业。#d1cm#page#
1.工程机械行业主要特征
1.1产品设计
·设计相近、配置相近、复制为主,创新较少
·部分企业呈现高低配置不同产品,适应高端客户和出口
1.2企业情况
·企业众多、产能过剩、价格相近、薄利多销,生存困难
1.3市场营销
·价格竞争为主、品牌竞争为辅
1.4产能情况-装载机
销量从10万台(2004)→22万台(2011年)→10万台(2014年)→6.7万台(2016年)
轮式装载机2004年-2016年销量
1.4产能情况-挖掘机
销量从2.6万台(2004)→15.8万台(2011年)→7.5万台(2014年)→7万台(2016年)
履带挖掘机2004年-2016年销量
#d1cm#page#
1.4产能情况-世界产能占比
轮式装载机:中国产能420000台,全球销量167000台,市场如果全部给中国,过剩产能也要达到253000台;
轮式装载机产能情况对比
履带挖掘机:中国产能538000台,全球销量418500台,市场如果全部给中国,过剩产能也要达到119500台;
履带挖掘机产能情况对比
1.4产能情况-全球工程机械销量走势
2000-2019年全球工程机械销量(含预计)
2006-2009全球工程机械市场销量走势
#d1cm#page#
1.4产能情况
2017年一季度销售情况
1.5产品质量
目前市场上工程机械产品质量存在的问题:
·大小企业产品质量相近、可靠性相近
·管理水平难以提高,质量长期徘徊不前,没有形成完整质量控制闭环,产品质量提高缺少长远规划;
·可靠性水平增长缓慢:
可靠性管理仅限于三包期(1000/2000/2500/3000h);
没有建立可靠性研究和管理体系;
没有建立完整科学的故障数据库;
零部件缺少试验验证手段和遴选评价体系;
没有设立可靠性工程师岗位;
·可靠性指标水平较低
三包期内:轮式装载机(3-8吨): 300-600h;内燃平衡重式叉车(3-5吨):200-400h
例如:从港口、仓库和工厂三类用户采集维修保养记录完整的3吨内燃叉车235台,进行可靠性分析。
从港口、仓库和工厂三类用户采集维修保养记录完整的3吨内燃叉车235台,进行可靠性分析。
(1)国产3T内燃叉车1000h MTBF为143.7h;
(2)MTBF随着使用时间逐渐升高,在5000h最高为309h,然后随时间下降;
(3)8000h MTBF为225.2h
(4)国产3T内燃叉车,动力系统、传动系统、液压系统、电气系统为前四大故障系统,占总数近3/4。动力、传动系统依然是叉车行业面临的问题;
(5)损伤型、失调型、堵漏型为前三大故障模式,损伤型故障占近1/3,零部件损伤、堵塞、泄露等问题突出;
(6)一般故障和轻微故障占近3/4,小病不断是叉车行业的重大问题。
结论:已经做大,还没有做强;虽然技术水平已经与国外先进水平接近,但产品质量进步缓慢,因此质量控制必须向国外先进企业看齐。
中国与国际销量利润对比
#d1cm#page#
2.国内企业存在的问题
从质量角度讲,试验检验是产品设计、试制、生产和装配中的重要一环,设计、制造的好还最终需要试验和检验获得验证。试验检验不充分,漏缺试验检验,最终体现在产品质量方面。
2.1新产品试验方面存在的问题
·没有试验规划
·缺少部分核心零部件试验验证手段:如,工作装置、车架结构件应力测试试验台;变速箱、驱动桥的齿轮和轴的应力测试试验台;齿轮副啮合可靠性试验台;液压油缸、液压泵、液压阀可靠性试验台;发动机变速箱匹配性能试验台。
·有试验设备不能有效使用;
·缺少试验验证和可靠性工程师;
·没有建立完整科学故障数据库;
·产品质量可靠性管理水平低,控制时段局限于三包期;可靠性考核和管理难度大、周期长、成本高,可靠性试验手段,有限很难获取;国外企业产品质量控制目标:全寿命可靠性增长 国内企业产品质量控制目标:三包期可靠性增长;没有寿命设计概念,也就没有全寿命周期可靠性指标的要求;大部分企业不知道产品的寿命数据,产品没有进行等寿命方面设计;
·缺少试验规程与试验方法。
2.2定型产品检验方面存在的问题
△没有长远产品质量规划
△表中问题构成质量控制链条上 的多个断点,不能形成质量控制封闭链
△可靠性管理局限于三包期时段
△产品质量一致性难以保证,可靠性水平难以提高。
△没有建立供应商定期审核及淘汰机制
△没有建立零件质量风险管控机制(及时采取遏制措施)
定型产品检验方面存在的问题
#d1cm#page#
3.如何进行产品试验与检验
产品试验:为了解某物的性能或某事的结果而进行的尝试性活动(词语解释)。
一般是指产品的研发和定型过程中所进行的相关尝试性工作;
产品检验:检查并验证(词语解释)。为保证产品持续符合相关要求的检查验证工作。
产品检验
3.1产品试验的核心工作
探知所设计产品的功能与预期是否相符,为改进提供依据。
试验工作主要包括:零部件试验、比对试验、整机试验、工艺性试验、可靠性试验、工业性试验等;
其核心内容主要有:试验规划、产品发展规划、可靠性增长计划、试验验证/可靠性工程师培养、外部开放试验室利用与合作关系建立、竞争对手试验能力情况、检验设施需求、载荷谱采集、外部专家使用、焊接工艺试验遴选、试验台建设、预算编制、试验规程与标准制定
3.2产品检验的核心工作
确保产品的性能与质量持续一致,符合设计要求。
检验工作主要包括:原材料、零部件入厂检验、工艺性检验、过程检验、出厂检验等;
其核心内容主要有:钢材理化检验和屈服极限试验、重量检验、尺寸检验、硬度检验、焊接质量检验、无损探伤检验、扭矩检验、运行检验、外观检验、漏缺检验、出厂运行检验和性能检验、编制检验方法和质量标准。
试验与检验二者的关系是探知与遵从的关系,如履带行走模式一样,形成闭环,才能不断提高质量。#d1cm#page#
4. 控制产品质量的建议和提升路径
4.1新产品研制的要求:
·设计开发阶段的质量规划(APQP:先期产品质量规划)
·体现等寿命设计思想
·可靠性试验验证计划
·建立力所能及的可靠性试验台,或者制定利用外部试验台方案
·进行焊接工艺参数试验优选,确定焊接工艺参数
·探索试验工艺参数,制定试验规程
·充分利用外部试验资源
4.2定型产品的质量控制
全面覆盖一环不少
a.钢材理化检验、b.屈服极限检验、c.重量检验、d.尺寸检验、e.硬度检验、f.焊接质量检验(熔深)、g.运行检验、h.外观检验、i.无损探伤检验、j.扭矩检验、k.漏缺检验、l.出厂运行检验、m.出厂性能检验、n.供应商过程及能力管控
定型产品的质量控制
探索制订主要环节质量标准
·建立基于可靠性数据管理软件系统、建立科学可行的零部件遴选评价体系、利用供应商的试验台进行检验试验、使用优秀企业的供应商队伍。
卡特彼勒在国内有百家以上的合格供应商,遴选合格供应商很重要,需要手段。
·可靠性管理时段应不断扩大:
第一阶段:从三包期延伸到5000h;第二阶段:进行全寿命期管理。目前已有企业三包期延伸到3000h,加价延长三包期服务。
·为满足以上要求,企业需要合理配置资源
4.3 综合建议
试验检验工作需要领导重视;持续做好试验规划工作;重视试验技术研究工作,重视试验技术方面的情报工作;做好可靠性试验工作;培养一批试验研究和可靠性工程师;重视焊接工艺优选和焊接工艺评定工作;研制核心零部件试验台。
虽然骨干企业建立了试验中心,但大多是通用设备,性能试验设备,仍然缺少结构件试验装置,可靠性试验装置。
总结:
市场在未来数年不会持续增量,大部分工程机械产能严重过剩。在国外中国产品质量表现不好;我们需要调整质量与产量关系;现实说明:销量=虚荣,利润=理智;需要从重视销量调整为重视利润率;改变企业命运的应该是产品的品质;需要构建完整可靠性试验评价体系;核心竞争力需要核心的试验手段和试验人才;掌控产品品质应从三包期延伸到全寿命周期;企业需要塑造品牌,品牌需要构建一流的质量管理水平;当我们的产品具备国际竞争力时,我们的产品利润率也会很好。我们企业也就拥有了一个持续美好的未来!#d1cm#page#
互动嘉宾:太原科技大学教授、副校长徐格宁
太原科技大学教授、副校长徐格宁
以下为互动实录:
感谢田志成总工程师给我们分享了客观、务实的报告,通过这个报告有三方面的分析控制产品质量提升的路径,听过以后引发我三个想法。
第一:产品设计可靠性前端收入,它决定了产品的固有可靠性。田志成总工程师讲的试验和检测和产品的后端输出,是验证现有的产品可靠性,想形成一个闭环,我觉得还有更多要做的。
第二:可靠性仅从流程,一个企业、一个行业乃至一个供应链是不能实现的。
第三:可靠性是一个大系统工程,包括了理论体系、分析体系、设计体系和标准体系,还有一个试验体系,是一个科学体系,我想更是一种只有量化评价的产品理念。
基于这三个思考,我现在更关注的是可靠性的设计和可靠性的指标,我认为这两项是整个行业大家所共有的一个短板,所有后端输入检测的数据能不能有效的反馈到前端去,以形成一个闭环,这是我们面临最重要的问题。田志成总工程师作为我们行业乃至国家工程机械中心的总工,您代表这个部门,如何领导和推动行业的考评工作?
田志成:徐老师对质量可靠性很有研究,长期为工程机械行业做设计、验证工作。我补充一下,我们的试验,从道理上而言,对新产品可靠性水平已经做了探索,鉴于检验,是对质量稳定性做一个管控,他们俩的分工是这样的,保持批量产品质量是符合要求的。就产品设计来讲,总有参照的,比如装载机C、B、D系统,肯定从A和B开始的,A和B的产品在销售过程中已经有很多问题反馈回来,质量的好坏都是可以知道的。企业作为新产品设计时,应该到市场上进行调查,比如235台的车是从市场拿来的,不是从三包期来的,市场调查比如50B产品有80台还在用,已经超过的五千小时了,那么这个车价有没有问题?工作当中有没有问题?如果没有问题,设计C系列时,这个变型尽量参考B系列产品进行设计,这有一个基本的数据了。这个过程中改进设计或者加强,来想办法延伸,然后进行试验。
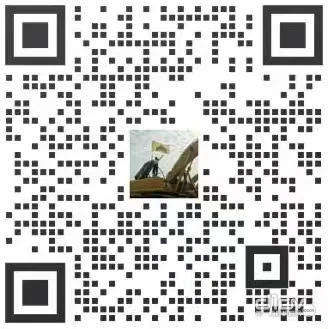
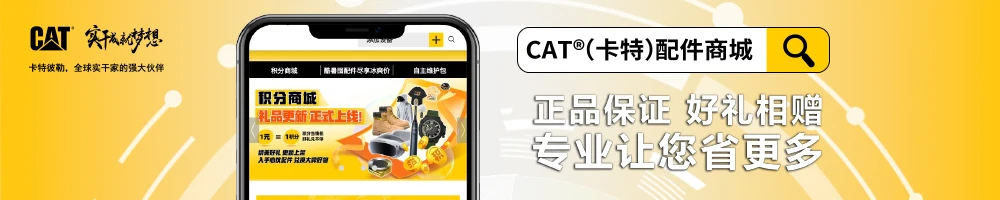
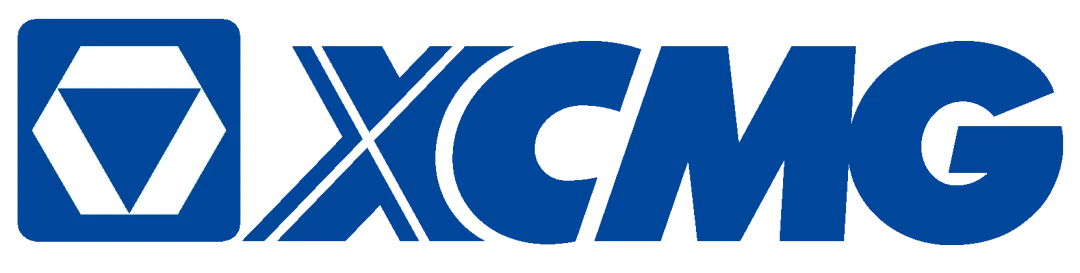
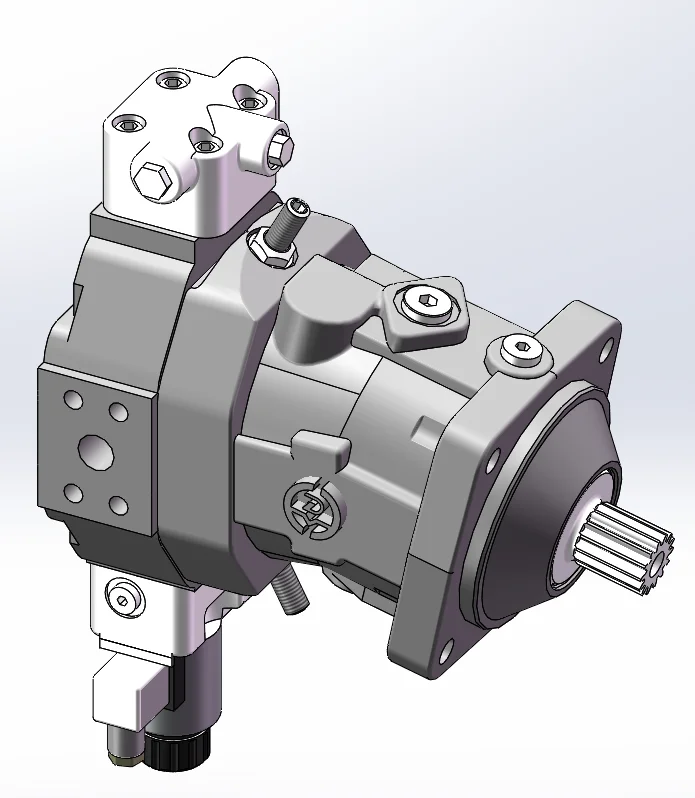
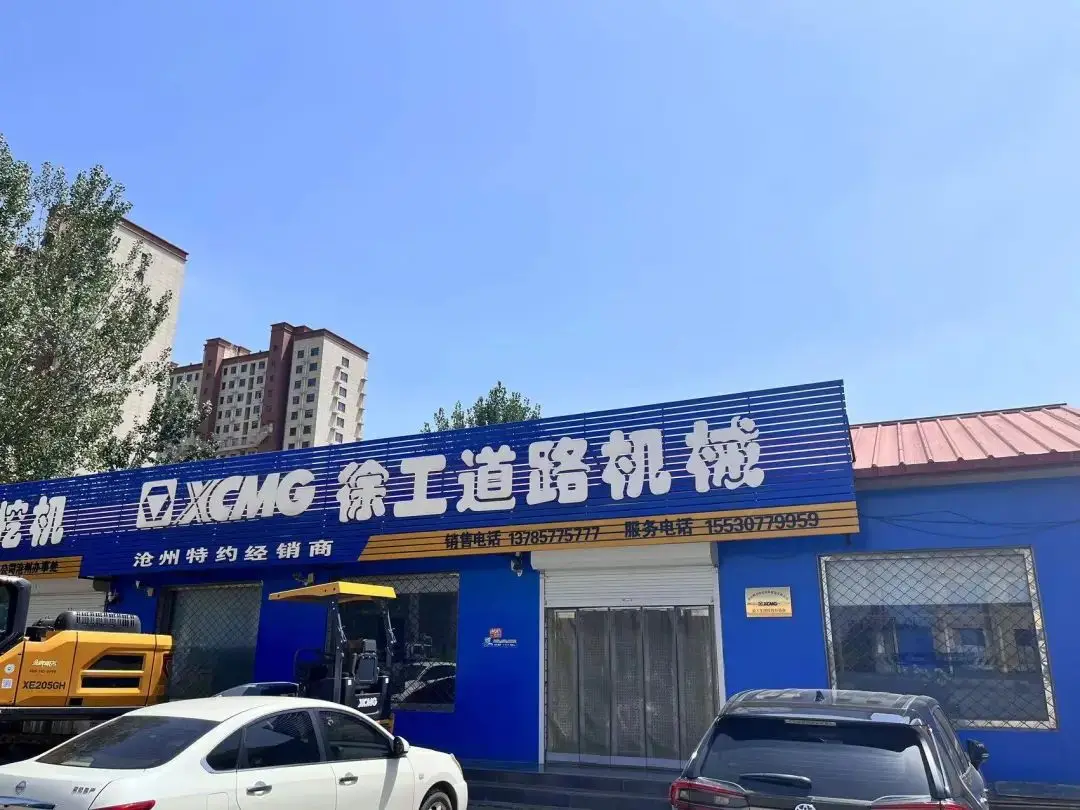
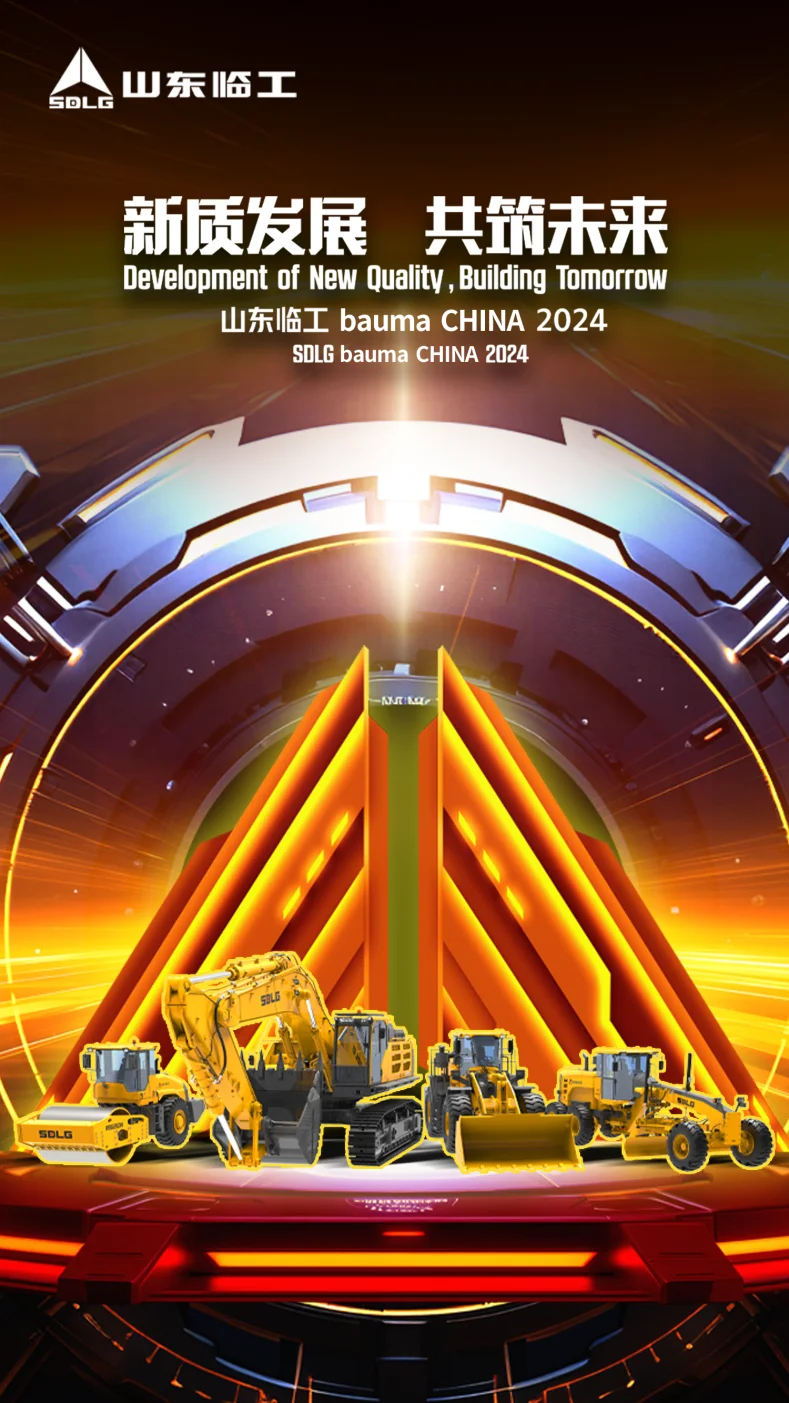
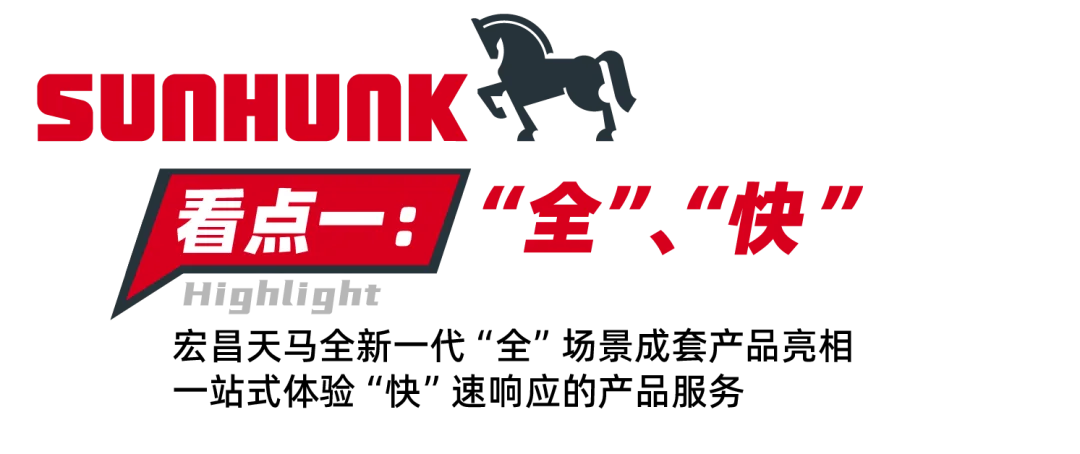
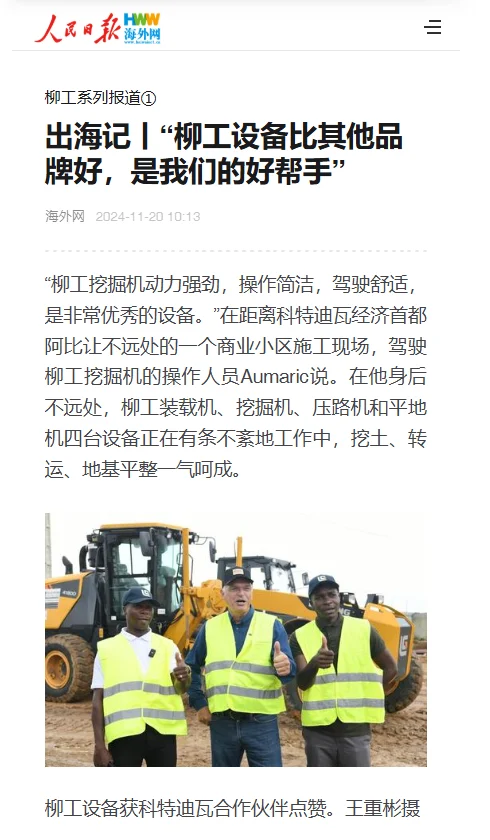
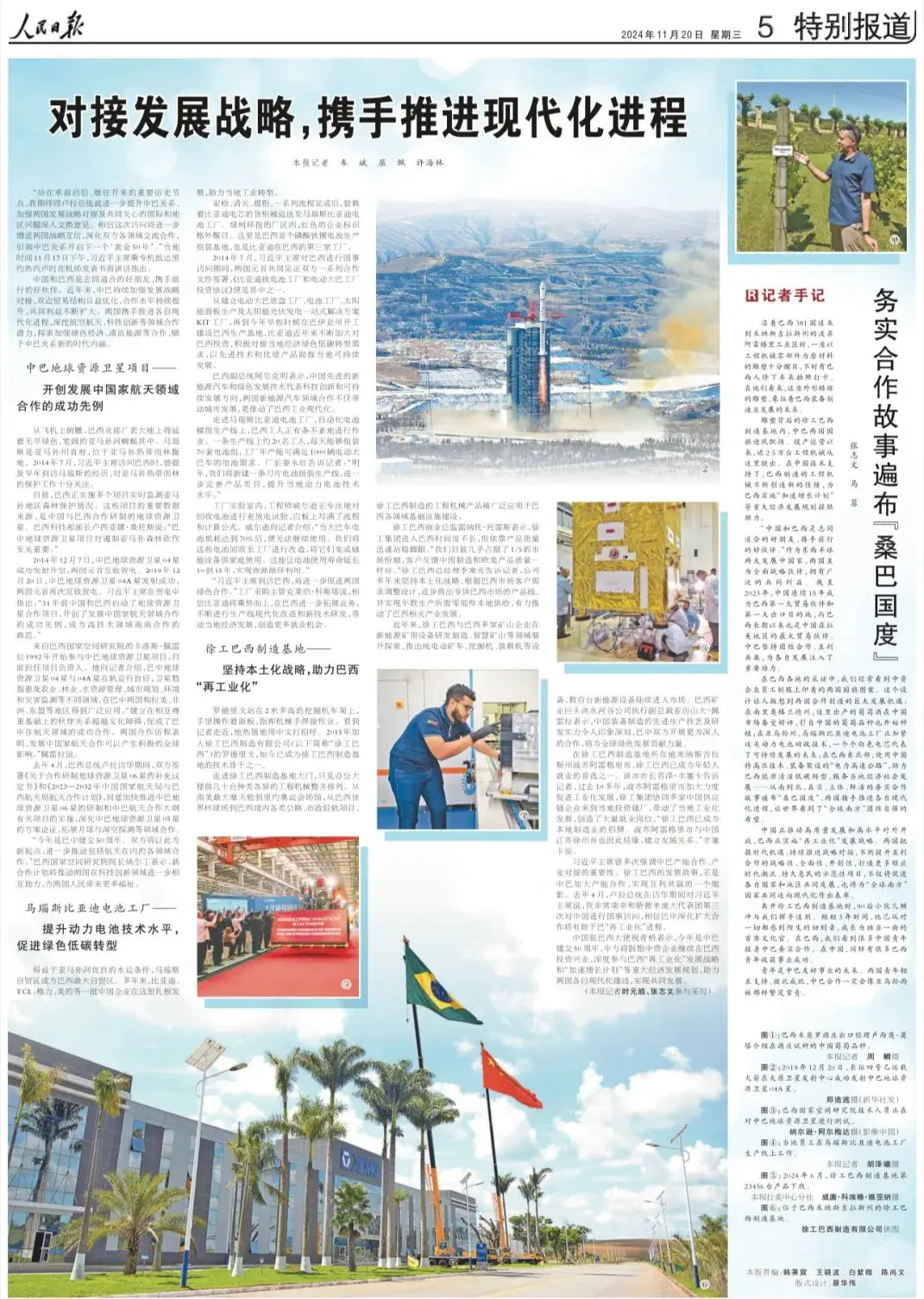
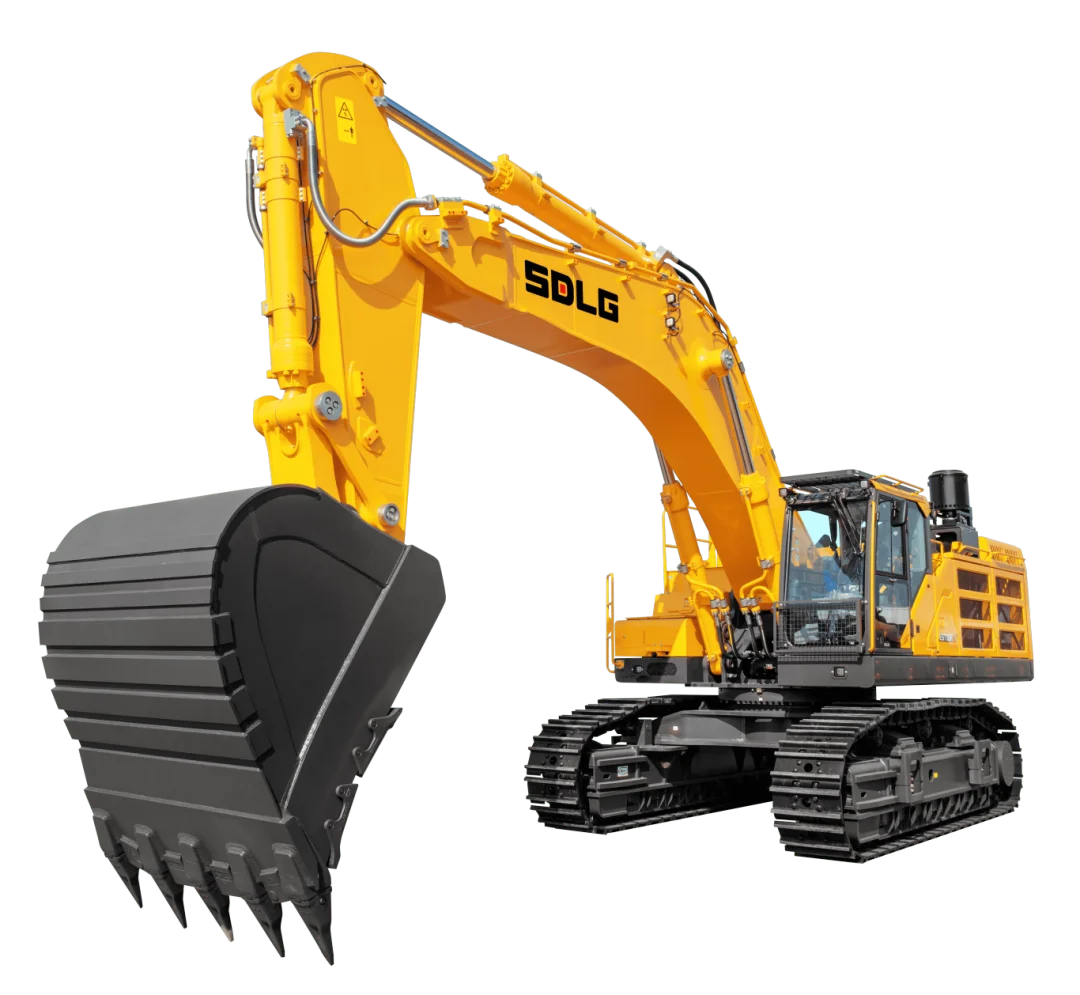
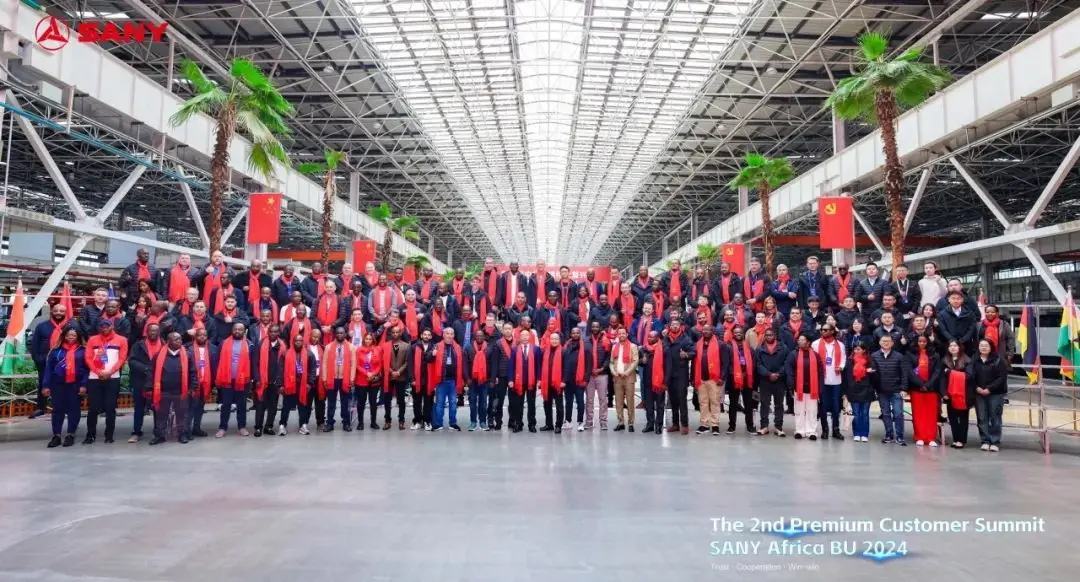
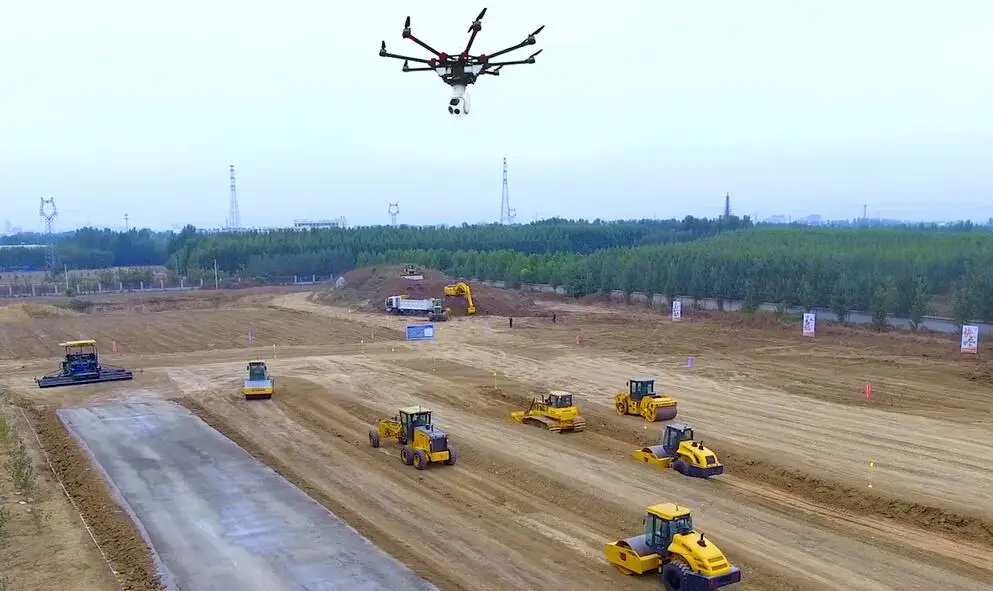
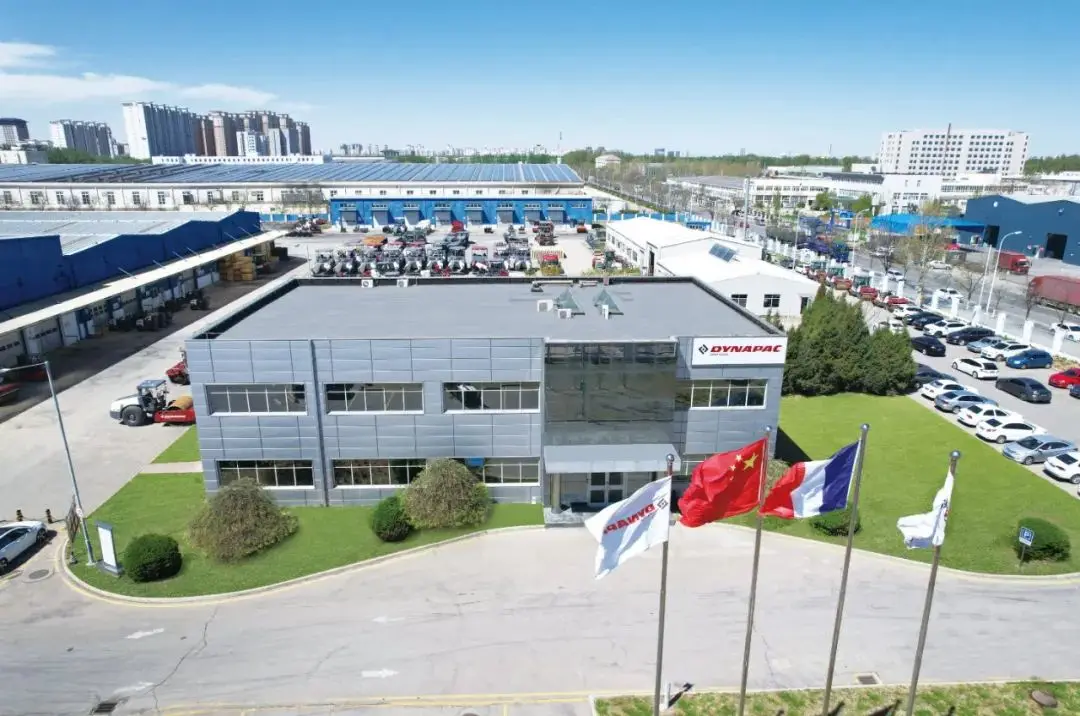
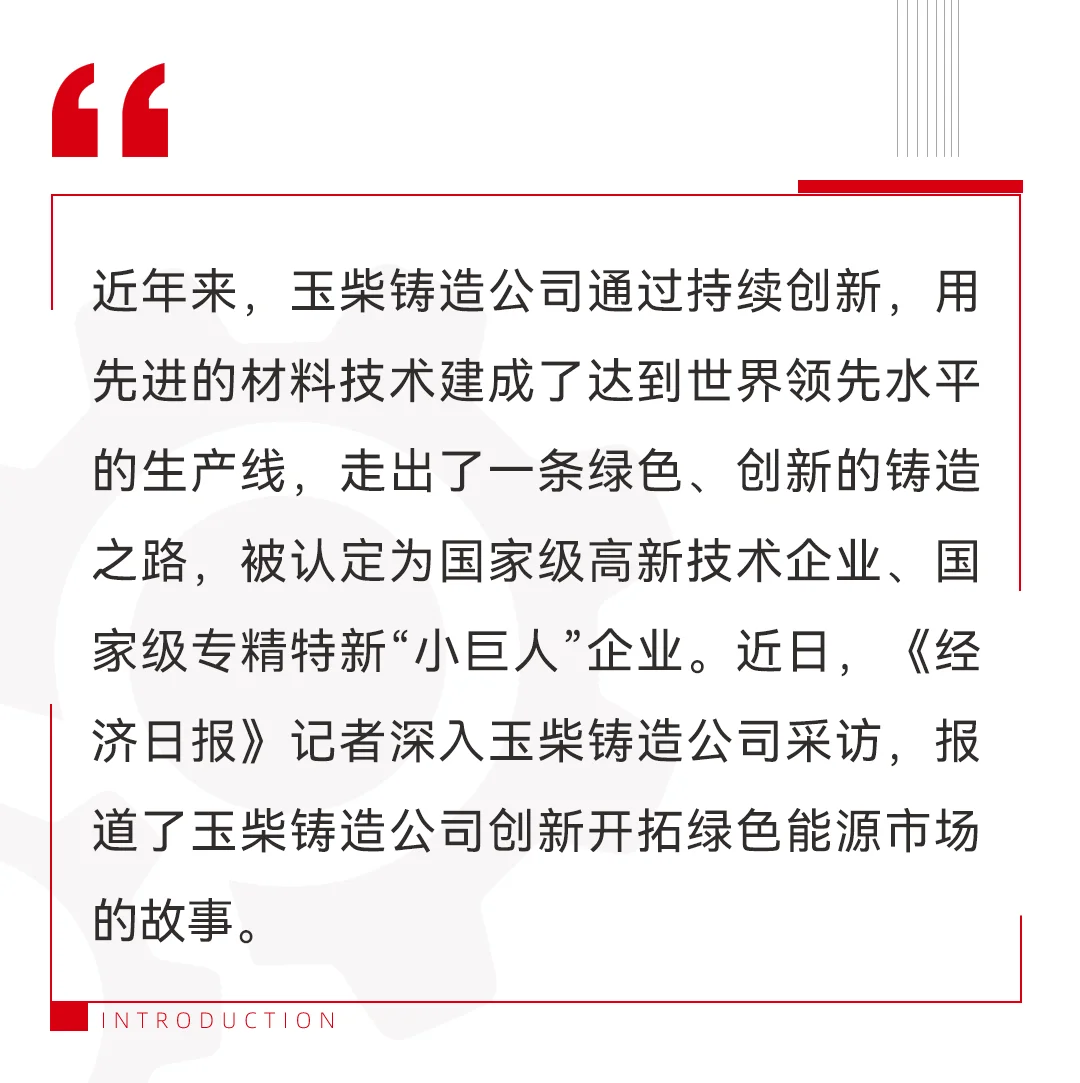
期待你的精彩评论