“世界第一臂”徐工开启全地面起重机巨章
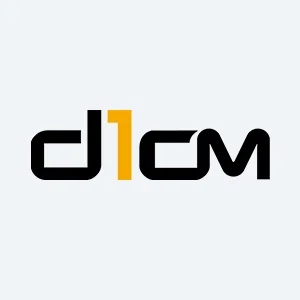
2012年6月25日,一个令所有徐工人为之骄傲和感到自豪的节日,在徐工全地面起重机智能化制造基地内,掌声齐鸣、彩带纷飞,伴随着全球最大吨位1200全地面起重机的下线,预示着有着“世界第一臂”之称的徐工已真正走上了国际领跑、世界之最的新征途。 徐工圆弧臂展示区 世界第一臂 徐工起重机新基地,起重机械齐亮相 在全地面起重机领域,徐工的深耕“由来已久”,但真正爆发,尤其是在世界峰极——超大吨位全地面
2012年6月25日,一个令所有徐工人为之骄傲和感到自豪的节日,在徐工全地面起重机智能化制造基地内,掌声齐鸣、彩带纷飞,伴随着全球最大吨位1200全地面起重机的下线,预示着有着“世界第一臂”之称的徐工已真正走上了国际领跑、世界之最的新征途。
徐工圆弧臂展示区
世界第一臂
徐工起重机新基地,起重机械齐亮相
在全地面起重机领域,徐工的深耕“由来已久”,但真正爆发,尤其是在世界峰极——超大吨位全地面起重机上的爆发,却是始自近几年。从25吨到1000吨,8年时间,徐工重型走过了国际同行50年才走完的道路,在全地面起重机产品上再次完美诠释了“中国速度”的深刻内涵。
这场中国全地面起重机的创世之举,喊出的是一个企业科技创新的无穷力量,谱写的是一个产业践行者、担当者的血气方刚!
忆往昔,峥嵘岁月
随着新世纪的钟声敲响,中国经济前进的步伐也有了突飞猛进的变化,国内基础设施建设需求增多、建项目逐步呈现大型化发展趋势,尤其石化、能源等大型建设项目中起重安装作业,对于大型、超大型全地面起重机的需求逐步增长。但囿于国外企业在全地面起重机领域的垄断,国内使用的大型起重机完全依赖进口,施工成本较高、维护耗时费力。
为了打破这种格局,为中国用户提供国产化,性价比更高的全地面起重机。2001年,作为中国工程机械,尤其起重机领域的领头羊,徐工决定倾全集团之力打造全地面起重机研发、制造体系,开始研发我国第一台25吨全地面起重机。
2002年春天,经过1个多月艰苦卓绝的攻关,在徐工重型诞生了第一根拥有中国人自主知识产权的百吨级起重机圆弧臂,同时攻克的还有全地面底盘悬架等技术,由于抓住了起重机核心技术的关键因素,徐工一举奠定了十年来在中国起重机核心主流技术上的领导地位。#d1cm#page#
看今朝,独领风骚
今天,在研制并产出30吨至1200吨总量7万根高端圆弧形吊臂,制造规模远超世界吊臂制造鼻主-比利时Vlassenroot公司后,徐工新基地再一次突破,大量创新应用了国际领先水平的智能化制造工艺技术,使得我国起重机向世界第一、更大吨位迈进触手可及:
1、超大型板材数控成型专有技术:超大型起重机圆弧臂成型技术在新基地实现又一个行业新突破:大吨位起重机主臂板材无需对接一次成型。仅此一项技术突破,就创造出年钢材节约15000吨,起重机综合性能反而提升30%的惊人效益。同时还意味着国际市场上,我国大型和超大型高新起重机产品的地位将被重新确立,更高附加值将取代价格优势,展现中国创造新实力。
2、超大型构件智能化反变形控制技术:工程起重机是我国装备制造业、工程机械产品中工艺制造技术含量最高的品类,尤其是在起重机主体受力结构件变形控制技术上,与飞机结构件制造技术相当,其共同难点在于超大超长板材在塑型、焊接、变位过程中均会产生难以控制的不规则变形。徐工在行业通用Ansys分析软件的基础上,自主开发出轮式起重机专用结构设计软件,结合对关键件360度破坏性试验,构建起变形量数据库分析系统,自主创新推出了智能化反变形控制技术,切实解决了这一大型结构件成型的国家级难题。在1600吨“世界第一臂”成型现场,世界最高水平的数控成型技术作用下,工程起重机行业最高强度级别的1100型钢材被精准地折弯成圆弧形。不仅如此,在大型吊臂焊接、变位的全过程,这种反变形技术会根据部件受热位置和变位角度的不同,以不同的变形控制和应力释放方式呈现。
3、智能化激光复合焊接技术和高效双丝焊技术:双剑合璧的创新,使刚刚开始摸索完成双丝焊技术的起重机行业,一下子站到了更高层次制造技术平台。两项技术联动,不仅使焊接速度提升1倍,更重要的是确保了每一个焊缝质量一次性达标,真正实现对设计理念的精准还原,为徐工能够攻克“世界第一吊”立下汗马功劳。
4、智能化焊接变位技术则更具神奇:记者现场看到,焊接机器人根据指令,精准地在部件上滑出一道道令人目炫的焊弧光,而同时,长达15米的“世界第一臂”的构件在变位工装的辅助下,为保证焊缝始终水平而不停地转换着位置,在短短30分钟时间内,“世界第一臂”对焊成型。
5、高端测控技术引领数字化革命:真正的数字化革命,不仅是配置一套可在线查询图纸的可视化终端那么简单。从大型激光切割机启动切割的那一刻起,作为“世界第一吊”结构件的一部分,编号为XZQ10002201的板材,就在庞大的数字管理系统中留下了自己的印迹。同样,组成起重机庞大身躯的上万种大大小小的部件,包括液压、电器都在数字管控中枢中留下永久的身份编码。微小异动会在第一时间传递到指定工位,以便于工人及时纠偏。
徐工装配检测线上一组不起眼的装置让实时体检、全程掌控变得简单,这是由上百个肉眼难以察觉的感应“电子眼”组成的监控装置,机器每行进到一个关键工位装配完工时,都会被自动“体检”一遍,时间只需5分钟。全部装配完成后,整车还将接受检测系统对其“回转、伸缩、卷扬”等等多个主系统和子系统运行的大考。10分钟后一张全方位的体检表呈现在系统终端,问题点会通过报警的方式同步显示出来。
徐工集合十年的吊臂检测经验,自主研制开发的智能化吊臂试验台,可以模拟各种实际作业工况,在线完成吊臂内部机电液、以及所有功能和性能的测试。
测控技术不仅仅覆盖了焊接中心、整机装配线、吊臂试验台、底盘检测线,在徐工大型高新起重机研制基地20条现代化生产线上,乃至正销往世界各地的设备上,都实现了物联网技术和ERP、MES、SRM、CRM、BI等现代化管理系统全面融合,实现了产品全生命周期管理。徐工重型的高管,只需通过系统,就能实时查阅到各类数据报表,和自动呈现出的各类异动分析。
在徐工智能化专有技术的支撑下,决定“世界第一吊”核心构件可靠性的关键问题已迎刃而解,等待它们的,是世界级测控技术的考验。藉此,经过多年磨砺磨合,徐工超大型全地面起重机制造航母终于全面拔锚起航,开始为中国石化、风电、能源等大型项目建功立勋。
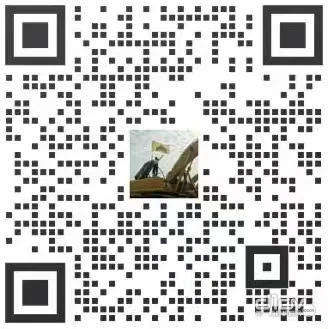
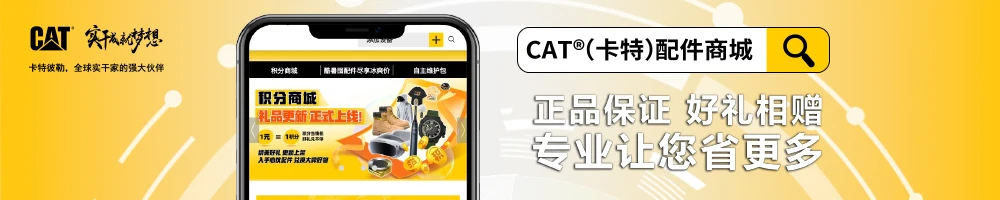
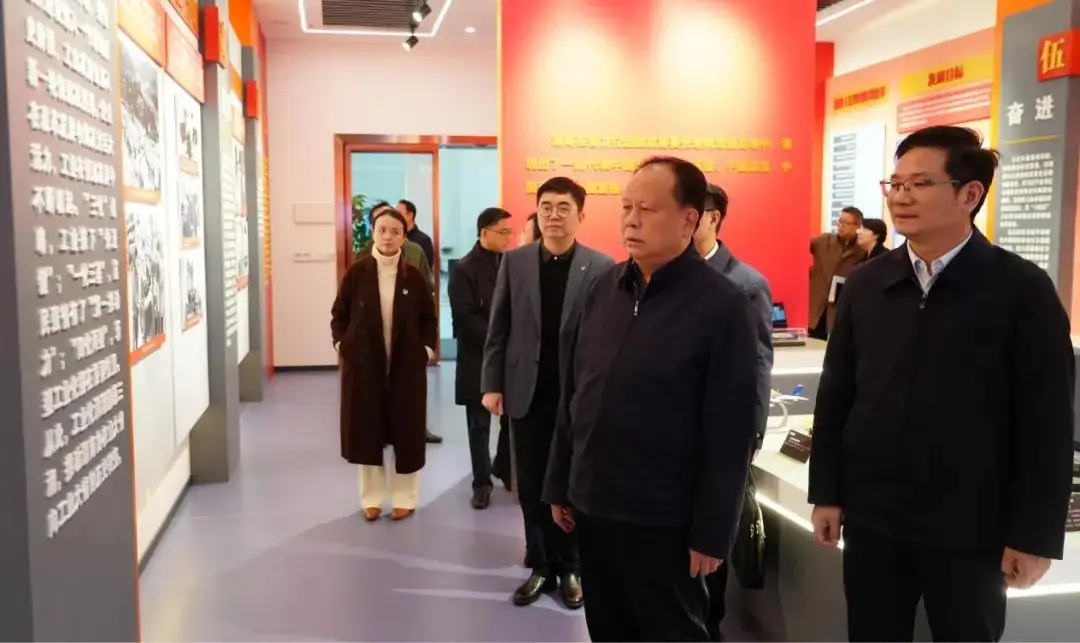
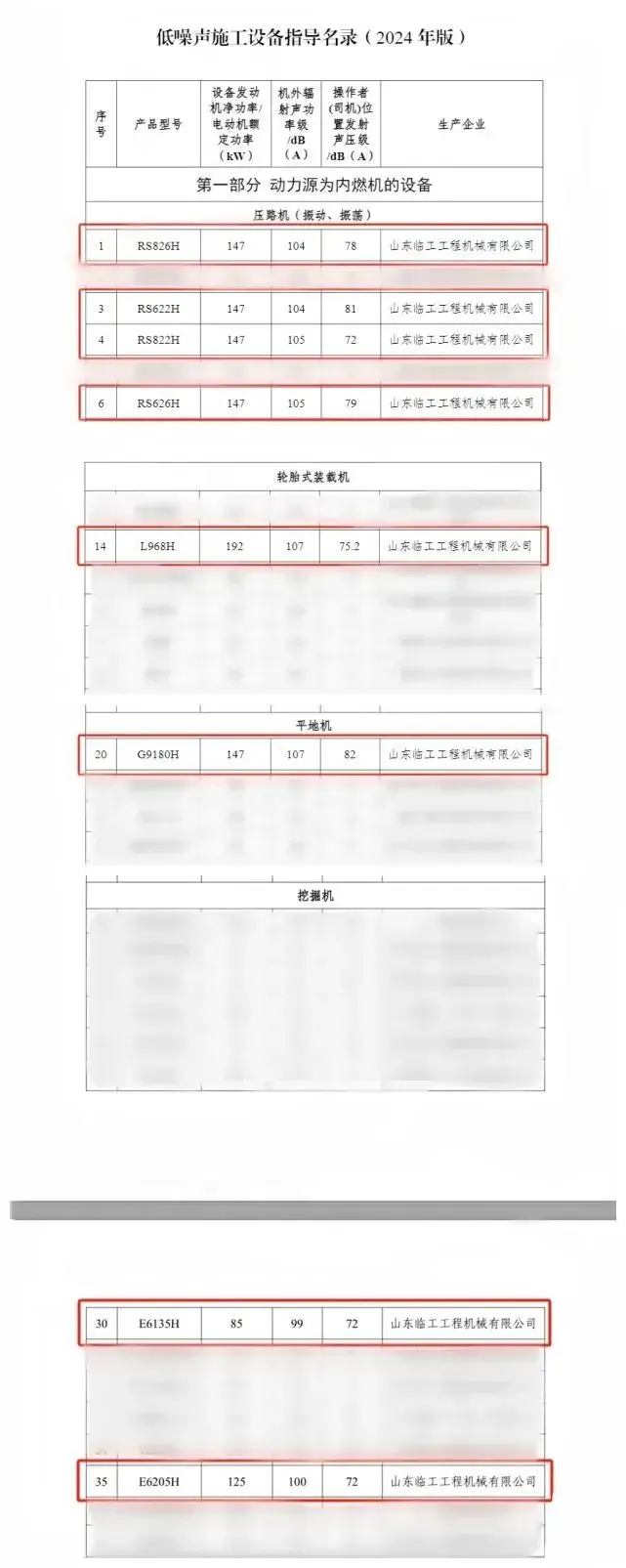
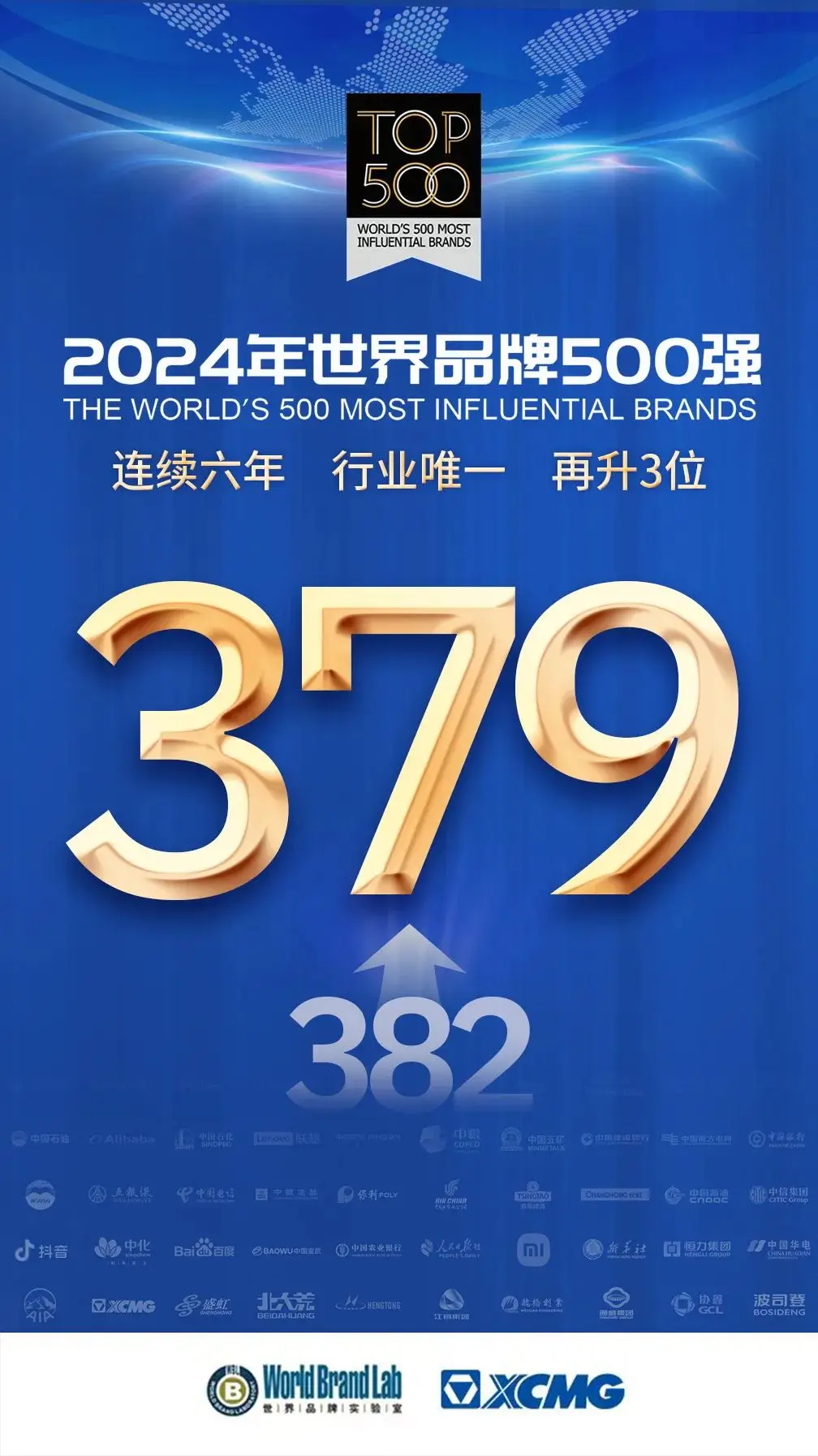
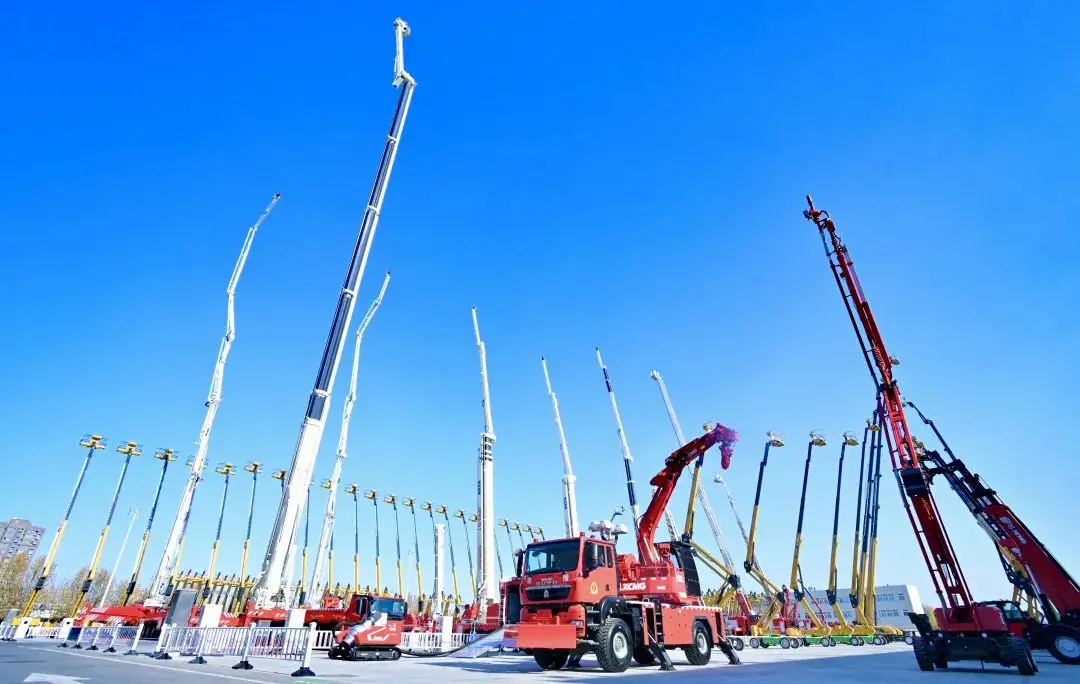
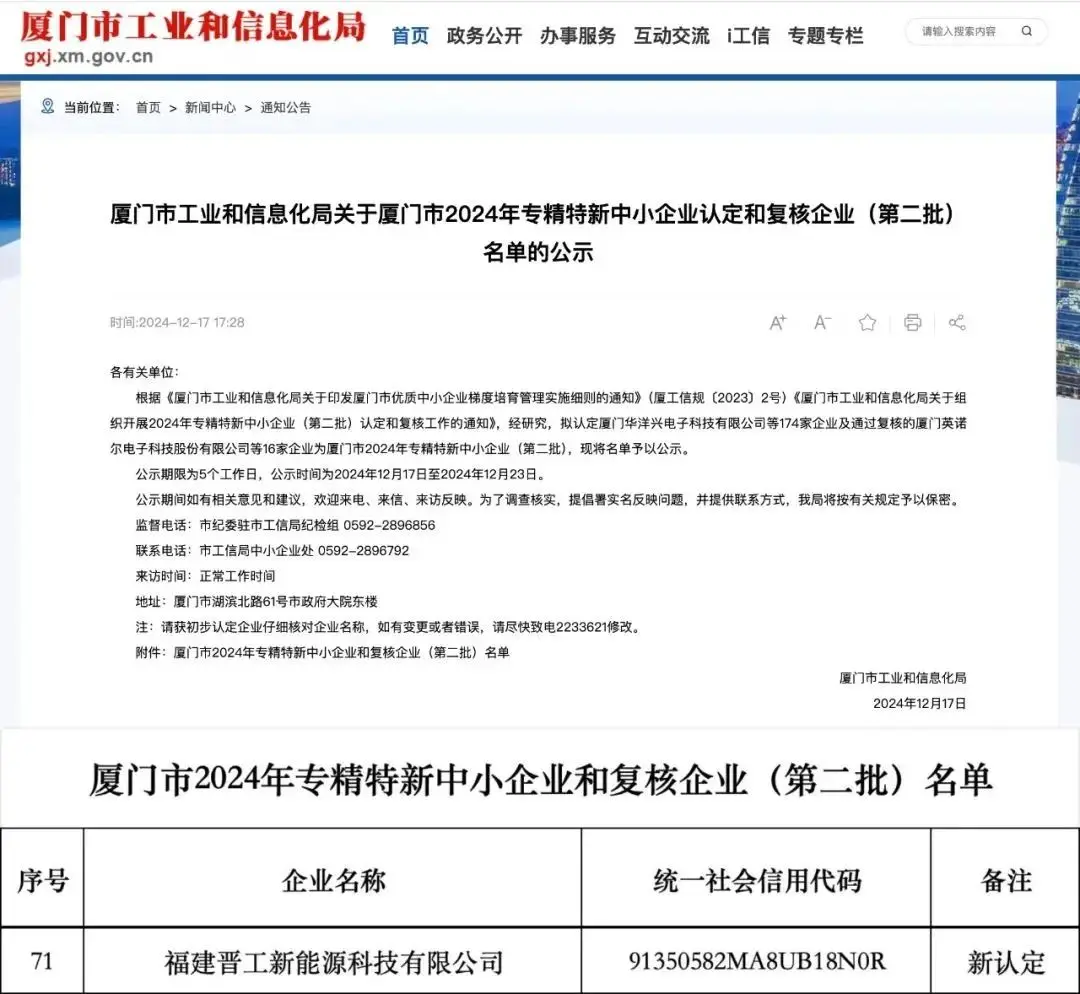
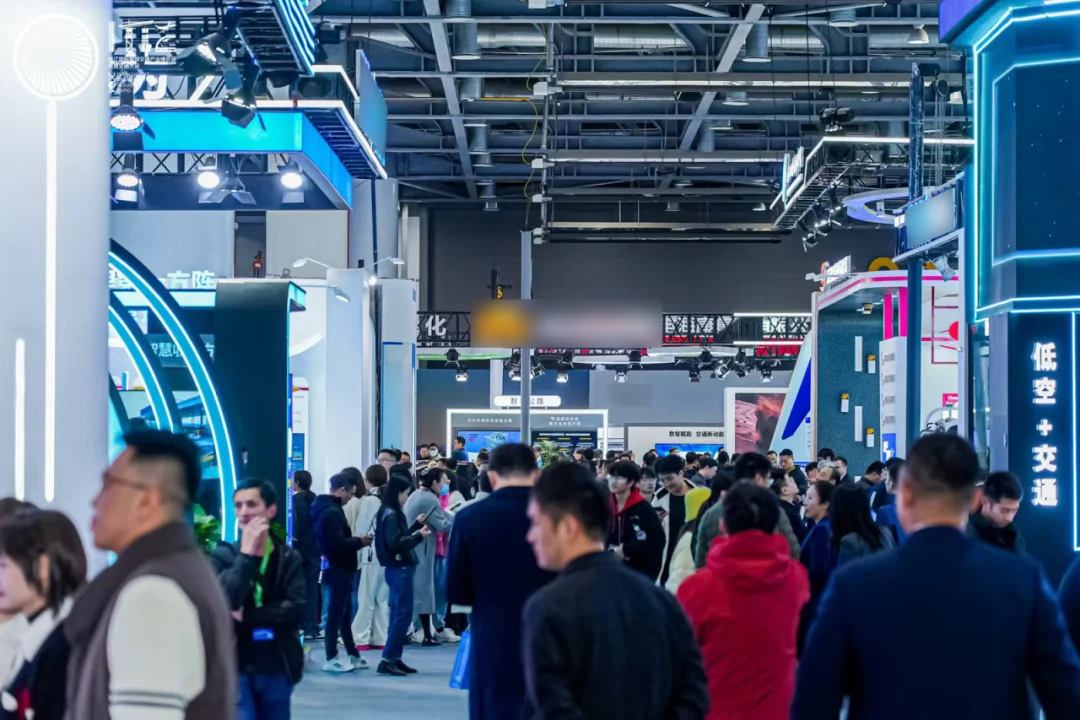
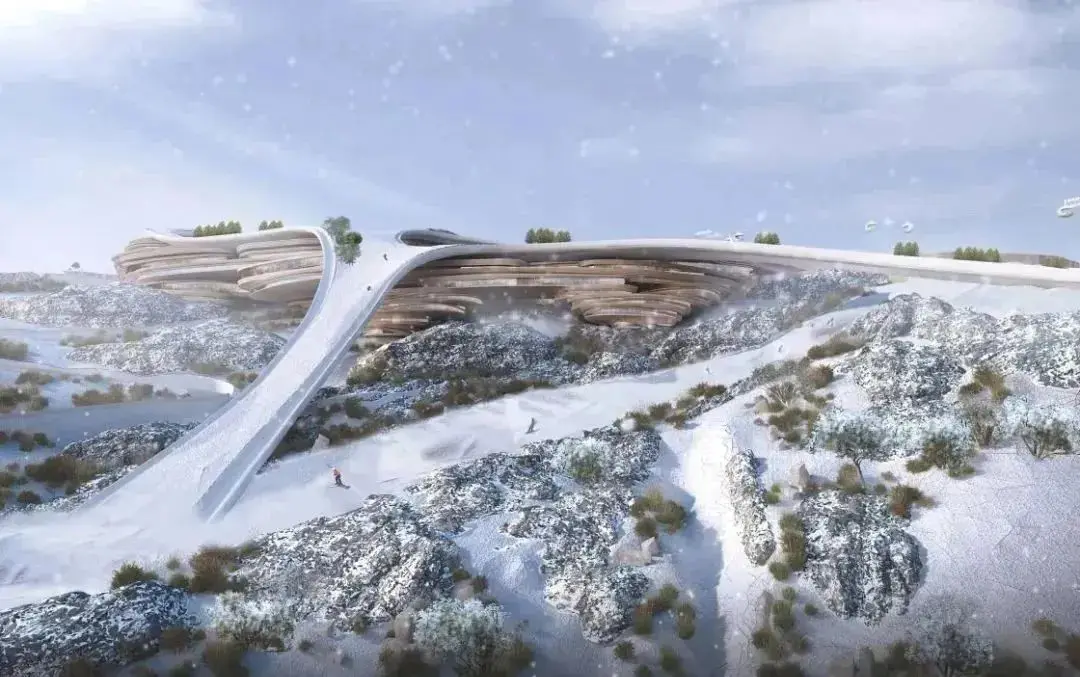
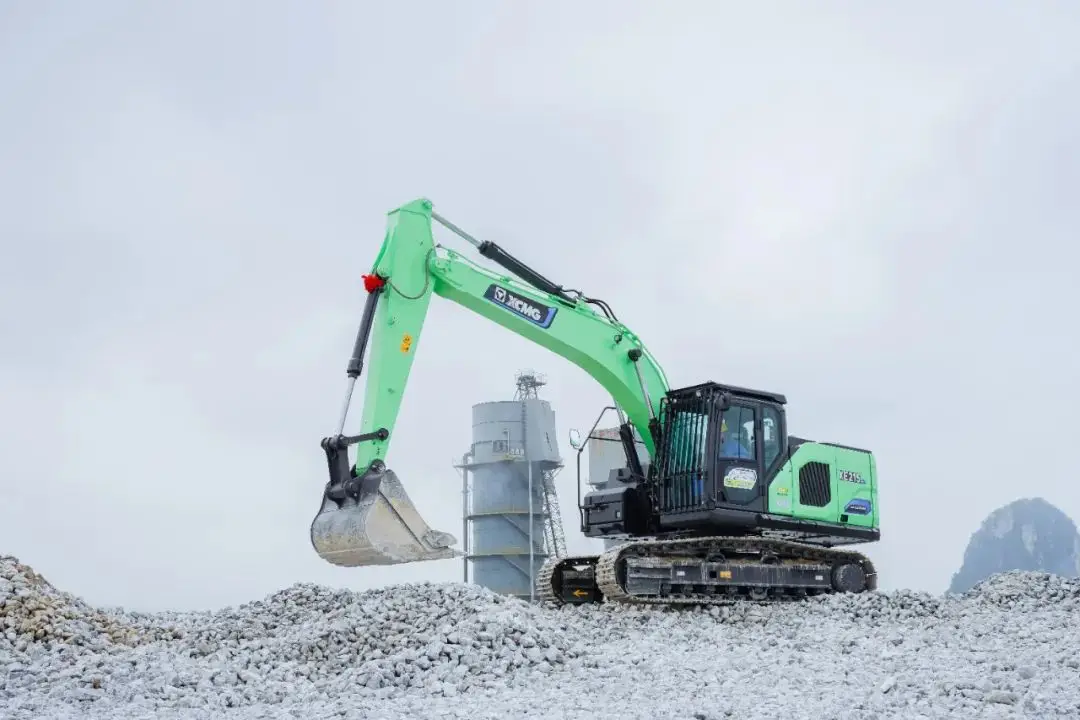
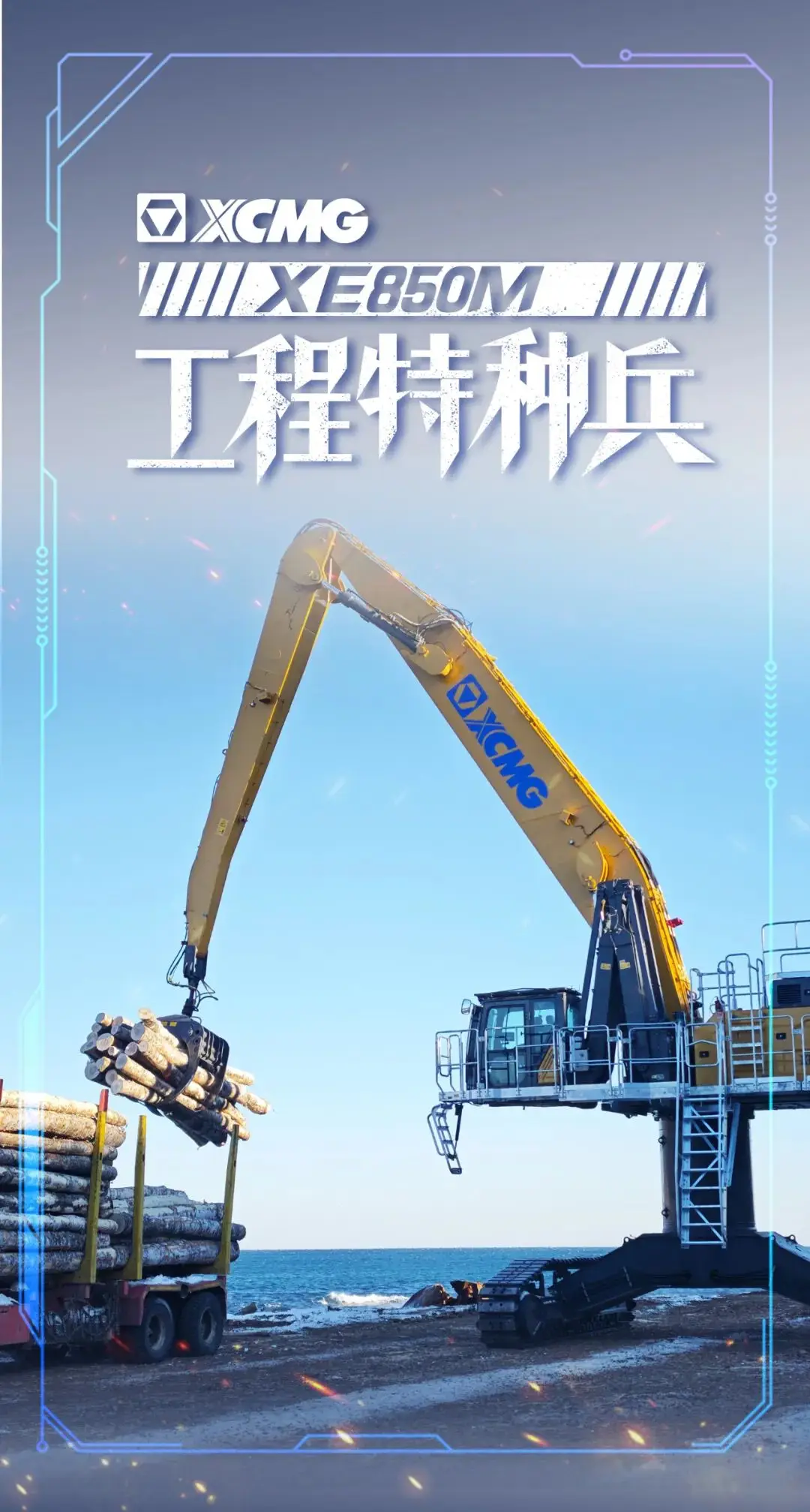
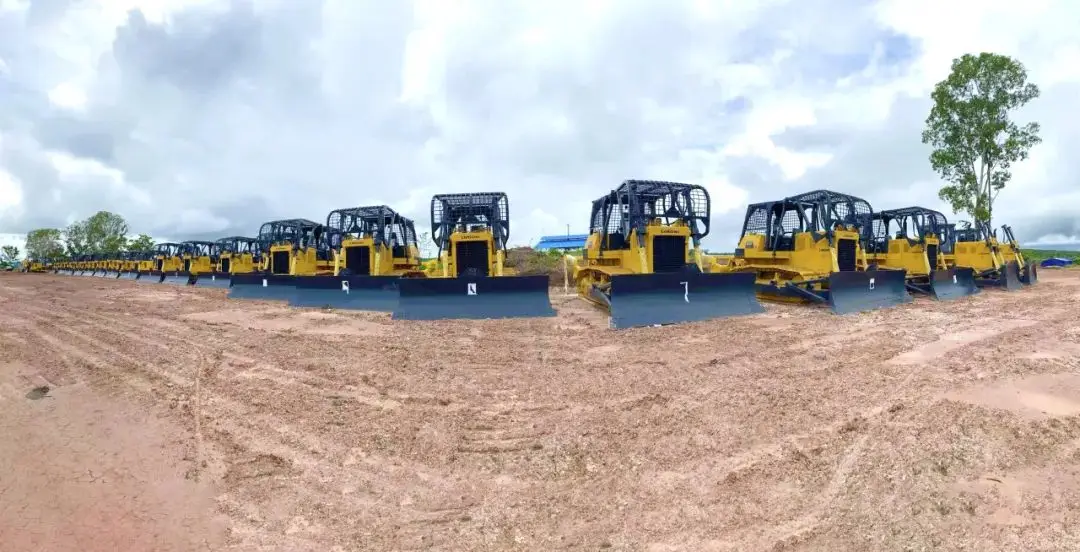

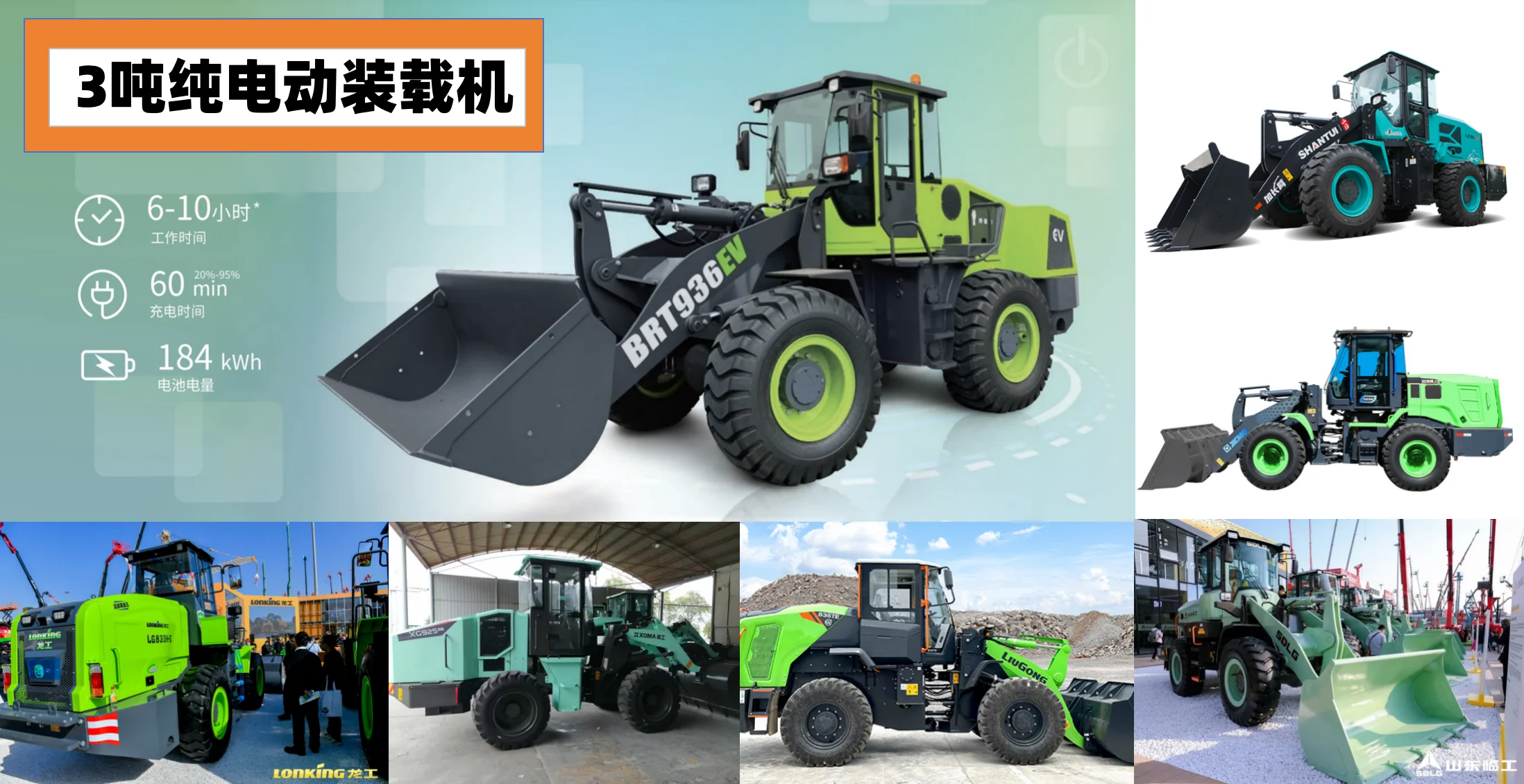
期待你的精彩评论