智造全解析!探秘中联重科全球最大塔机“宝藏”智能工厂

作为工程机械龙头企业,中联重科正加速智能化、数字化、绿色化转型升级。10月25日,全球最大上回转塔机在常德中联重科塔机智能工厂下线。中联重科塔机智能工厂目前可生产覆盖80吨·米~20000吨·米的全系列建筑起重机械产品,已先后获评国家级和省级绿色工厂、国家级绿色制造示范工厂。11月1日,《经济参考报》以中联重科为行业数字化转型标杆,报道了中联重科全球最大塔机“宝藏”智能
作为工程机械龙头企业,中联重科正加速智能化、数字化、绿色化转型升级。10月25日,全球最大上回转塔机在常德中联重科塔机智能工厂下线。中联重科塔机智能工厂目前可生产覆盖80吨·米~20000吨·米的全系列建筑起重机械产品,已先后获评国家级和省级绿色工厂、国家级绿色制造示范工厂。11月1日,《经济参考报》以中联重科为行业数字化转型标杆,报道了中联重科全球最大塔机“宝藏”智能工厂。以下为文章全文。
一座“智能工厂”,二间“灯塔车间”,三座“智能立库”,四条“黑灯产线”……10月25日,在湖南常德举行的全球最大上回转塔机下线仪式中,历经5年时间打造、拥有“一二三四”“宝藏”的中联重科全球最大塔机智能工厂,迎来与会专家的“探厂”。
与会专家、客户观摩中联重科塔机智能工厂
全智能制造,每18分钟产出一台塔机,每72分钟产出1台施工升降机,生产规模在国际遥遥领先,生产方式及效率令专家频频点赞。
中联重科塔机智能工厂2016年启动规划,占地740亩。园区固定投资17.7亿元,规划年产值200亿元,主要生产80t.m~20000t.m的平臂、动臂全系列塔式起重机和4S2050等机型施工升降机。
“智能工厂分两期建设。二期于今年5月建成投产。”中联重科建筑起重机械公司副总经理梁岱说。
“24+3+9”,塔机工厂很智能
“智能工厂基于国内一流、国际领先的规划理念,对标30年都不落后的工艺质量标准,投入24条智能化产线和3座智能立库,实现从原材料、下料、焊接、机加、涂装、机构装配、包装、物流和实验的全面工艺升级,从而达到大幅提升产品质量的目的。” 梁岱介绍说。
除了“肉眼可见”的24条智能化产线和3座智能立库,这里还暗藏了九大黑科技,只为拼工艺。
为检测金属、非金属材料各种物理和化学性能,这里建有一流的原材料理化试验中心;
投入2条自动化率100%的黑灯下料产线,集成原材料自动分拣、智能锯切、高频加热、在线检测、激光打码、机器人自动分拣和无人叉车配送等7项“技能”,原材料锯切精度可控制在±0.5毫米;
200余台自动化机器人,CLOOS双丝焊接技术和双丝三弧高效焊接技术,让焊接自动化率提升至52%,质量一致性达成98.8%。激光在线检测和焊缝探伤技术,确保焊接质量100%全检;
中联重科常德智能工厂的自动化机器人
20台钻铣镗一体化高精机加工中心,实现柔性化、自动化作业,大幅提升加工工艺,整体焊后加工精度可达7级;
5条环保水性漆涂装线,“1洗3烤”先进工艺、集成温湿度自适应控制技术、重型积放链输送技术、全自动抛丸技术、全自动独立式脱脂水洗技术、自动配比输调漆技术、触媒远红外烘干技术……实现绿色、节能、高效涂装工艺,涂装质量可保五年不生锈;
机构装配产线变革传统工艺,可实现自动取料、自动绕绳、自动计米、自动熔断,在线检测,传动试验于一体的装配工艺;
流线化包装作业工艺,一次性包装,提升装卸效率,包装工艺简化又高效。
此外,这里还集成了3座智能立库和40余套AGV、RGV无人化搬运小车,实现厂内配送无人化。物流信息化系统,一键掌控发货物流进度,内外部物流协同,大幅提升工厂的物流效率。打造的集行走、内爬、电控系统、传动机构实验于一体的大型试验场,则能满足2万t.m及以下机型的全生产周期的可靠性试验,断绳等极端工况破坏性实验。
中联重科塔机智能工厂的智能立库和AGV运输线
“这一塔机智能工厂的建成,标志着中联重科,也标志着我国建筑起重机械规模达到了世界一流,质量也达到了世界一流的‘双一流’。”相关专家表示。
绿色环保高效
智能工厂树起行业数字化转型标杆
“灯塔工厂”一词,最早源于航海行业,后来则代表着世界先进的制造业企业,通过前沿技术应用整合,加速整体产业智能化进程所打造的智能化工厂。可以说,拥有“灯塔工厂”的企业,也是行业内这一领域技术创新和数字化转型的标杆。
中联重科全球最大塔机智能工厂,拥有两个标准意义上的塔机“灯塔车间”。
一是标准节“灯塔车间”。所谓标准节,是指塔机的基础构造件。过去,焊接作业场地里,工人一手持面罩,一手拿焊枪,在飞溅的焊花中作业。但在标准节“灯塔车间”厂房里的5条标准节智能化焊接生产线上,过去的场景不再重现。有的只是百余台机器人挥动“手臂”,有序作业。
中联重科标节灯塔车间
“车间拥有30余套AGV、RGV无人化搬运小车,10余套钻铣镗一体化高精机加工中心,实现柔性化、智能化生产。在人员减少73%、场地减少56%的情况下,车间每5分钟可产出1节标准节。”中联重科副总裁、建筑起重机械公司总经理唐少芳介绍。
另一个,则是塔机机构装配灯塔车间。据悉,这是这一行业首个集智能仓储、无人化配送、机构装配、自动绕绳、在线检测于一体的装配车间。在这里,自动扫码智能识别、自动化叫料精准出入库、无人化物料配送、成品自动化出库和路障智能化识别等自动化物流技术,让场地使用同比节约6000平方米,出入库效率同比提升30%。
中联重科常德智能工厂车间
“基于数字化规划理念,塔机智能工厂集成大数据分析和工业互联网技术、智能化产线、信息化系统和可视化技术,实现‘物物互联、人机互动、虚实互联、价值驱动’。”中联重科塔机智能工厂相关负责人介绍。
智能工厂好不好,使用者最有发言权。中联重科塔机智能工厂智能制造技术室主任郑鹏向记者分享了自己在这里工作的“体验感”。
“相比过去,这里的自动化程度更高,产线最高自动化程度可达95%。在原先基础上,可节省人力40%以上,场地利用率则提升了35%。” 郑鹏说。
衡量一家工厂的好坏,效率无疑是个硬指标。在他的大致评估中认为,智能工厂采用流线化生产,整体效能较原来可提升30%-50%,最大效能提升可达到50%以上。生产周期也大大缩短。常规塔机机型由原来的5天缩短至3天。
“比较突出的一点还体现在生产的‘柔性化’上。过去,我们一个工装最多只能生产一到两个产品,但现在一个工装,可实现全系列产品生产。一个装备,N种用法,大大提高了场地利用率,也在面对市场定制化需求上,会变得更强大。” 郑鹏说。
不止如此,为实现资源投入、生产过程、工艺参数、物流效率、能源消耗和VOC环保指标的过程化管控,工厂还投入了2万多个传感器,实时采集生产数据,实时监控各项指标,并通过大数据分析决策,智能化数据驱动业务改善,实现生产数字化转型升级。
工厂还有着全生命周期绿色设计,综合运用绿色设计、绿色工艺、绿色包装、绿色生产等技术,实现焊接、加工、涂装、设备节能、驱动节能、三废处理的全面绿色化升级,制造技术绿色化率达98.7%,制造过程绿色化率达97.3%。工厂绿色化运营,VOC排放同比减少60%。2019年获批湖南省绿色工厂,2020年获批工信部认证的国家级绿色工厂。
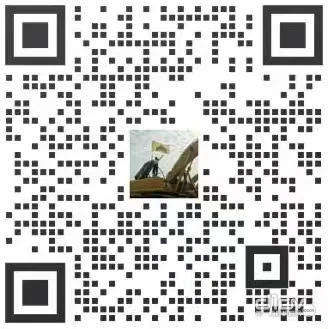
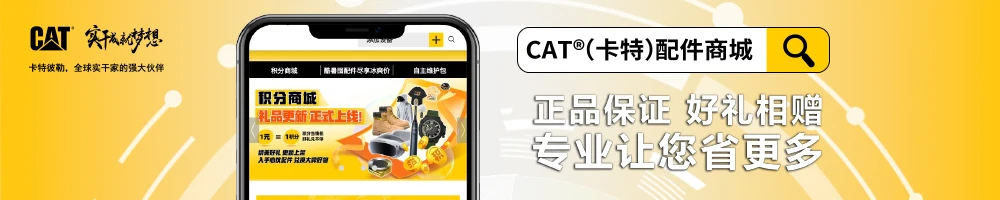
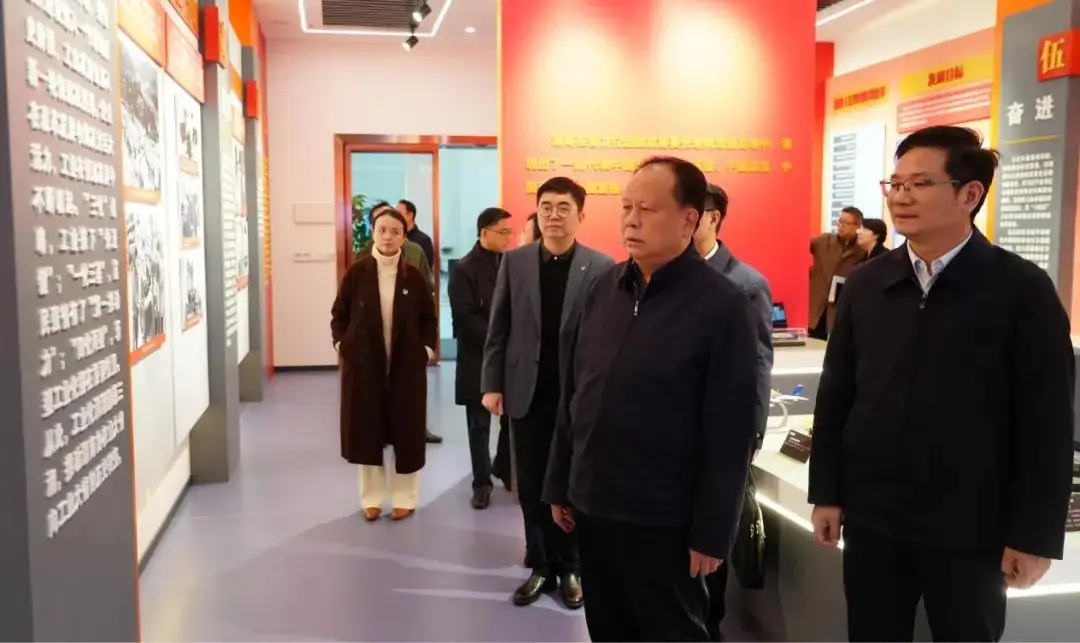
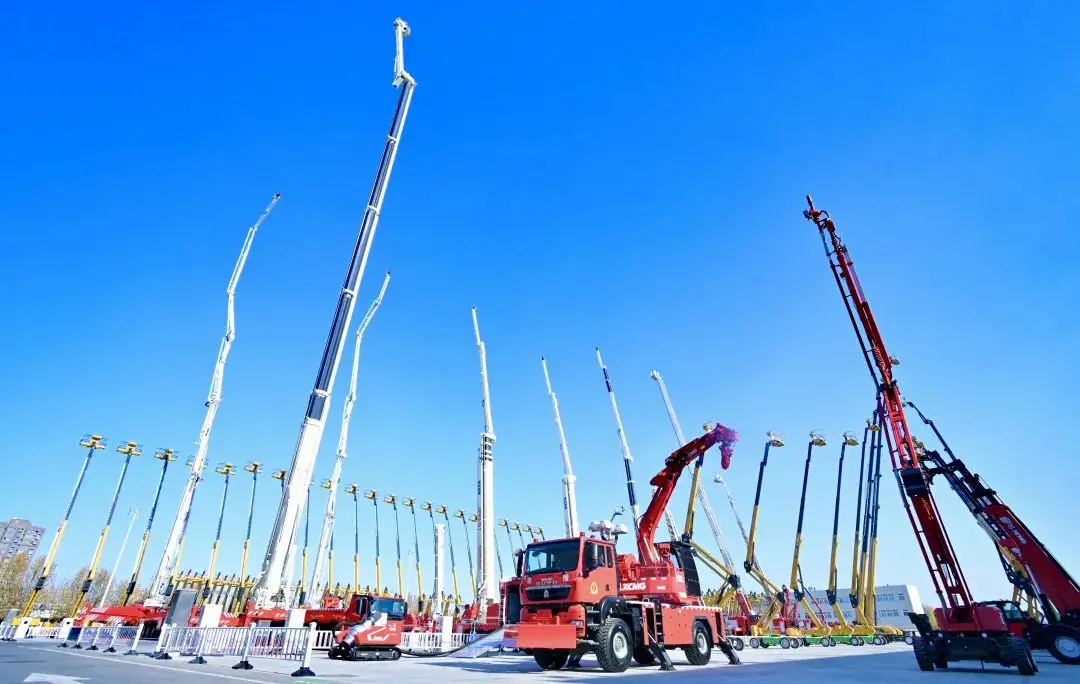
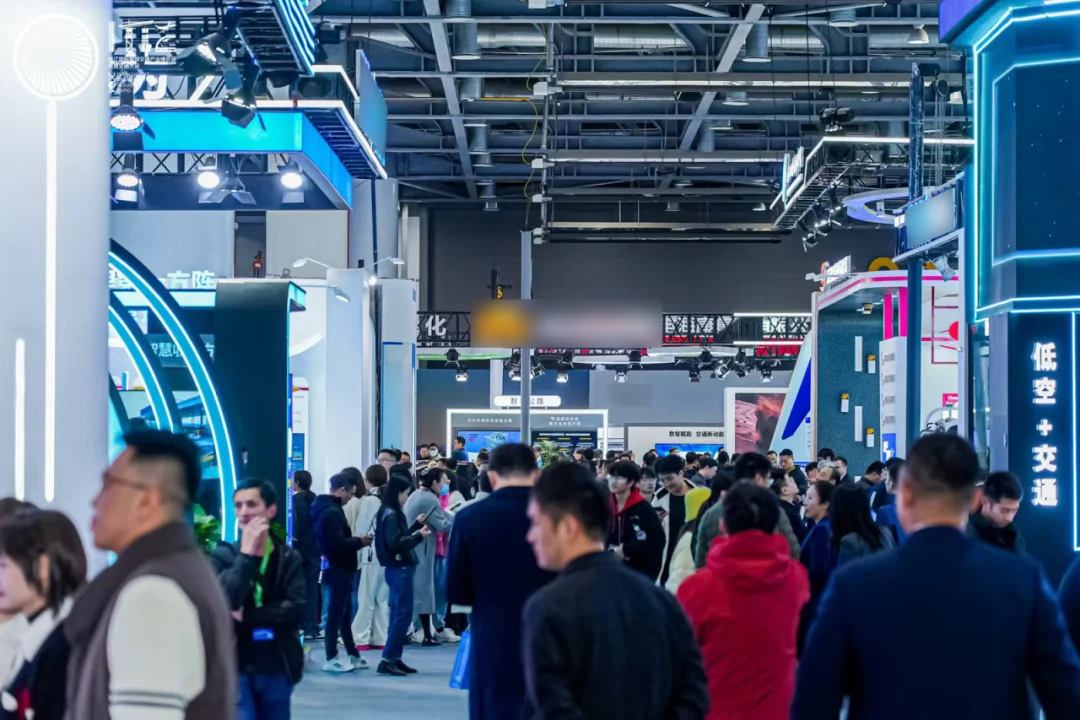
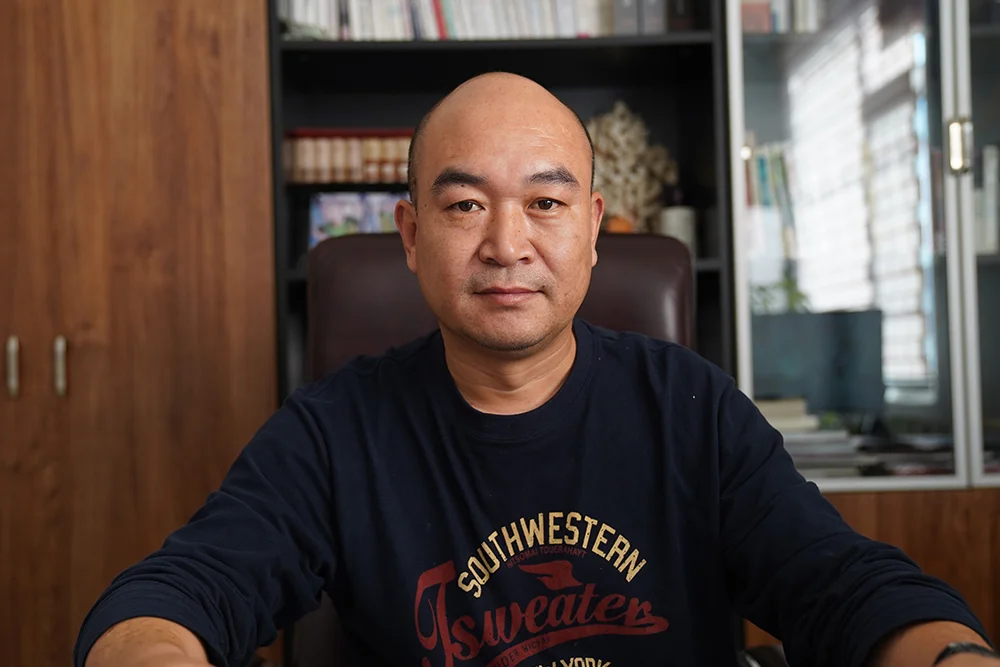
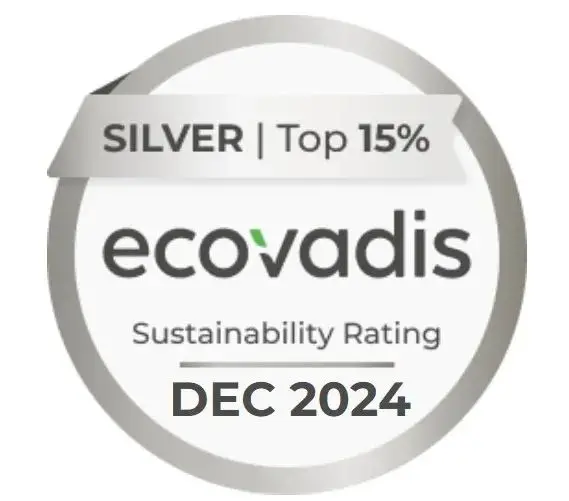
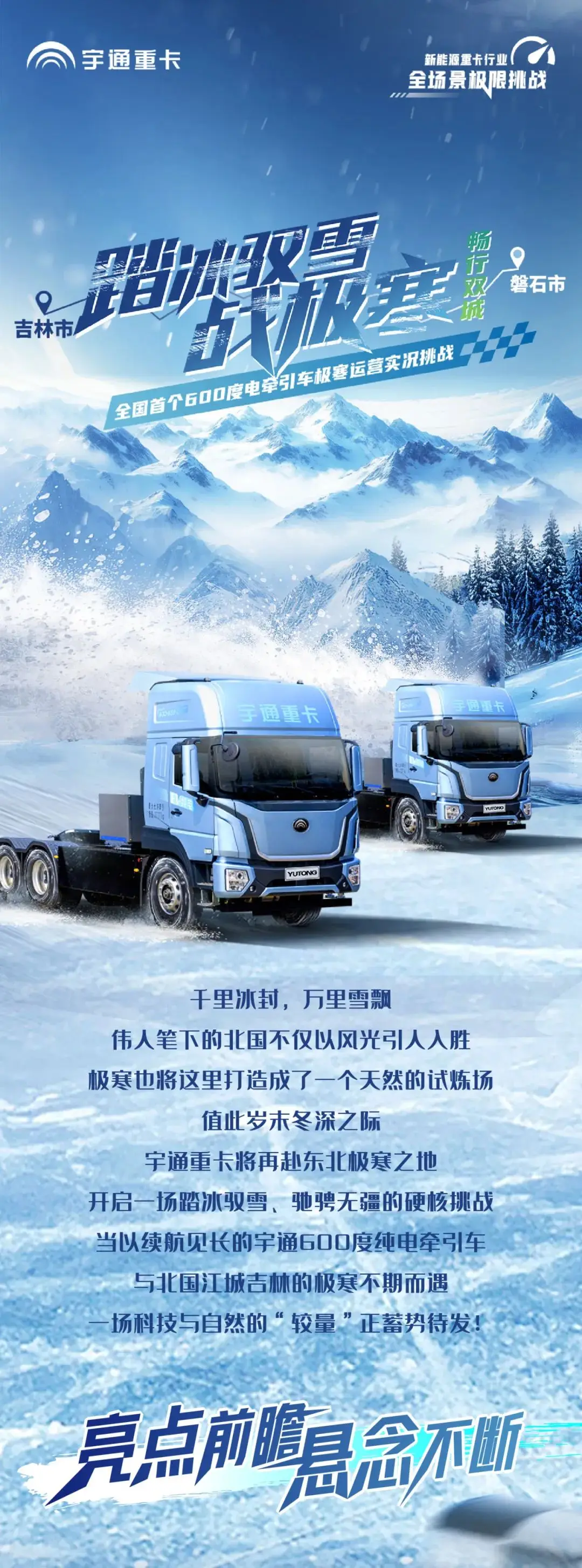
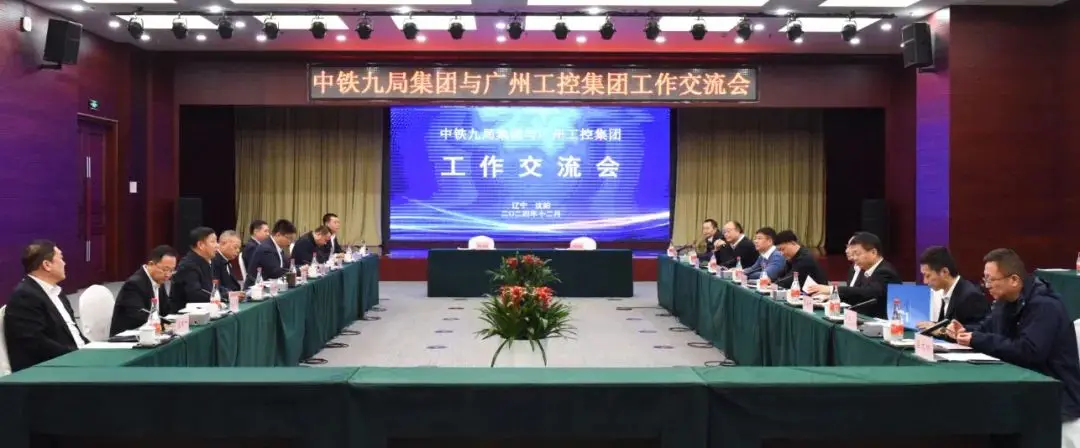
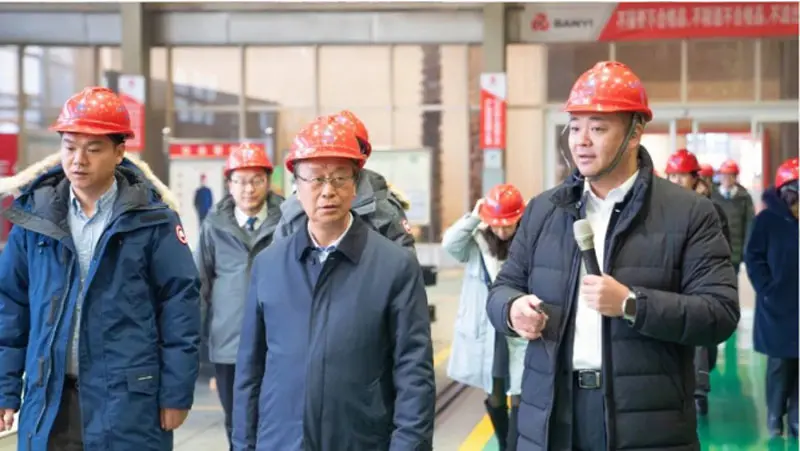
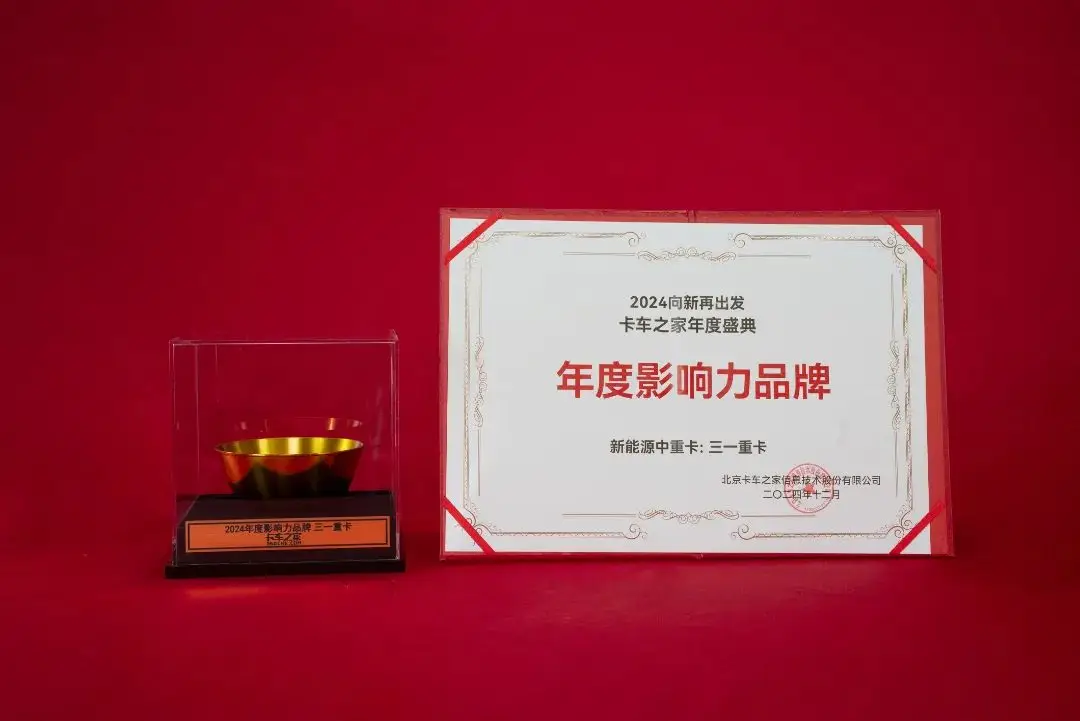
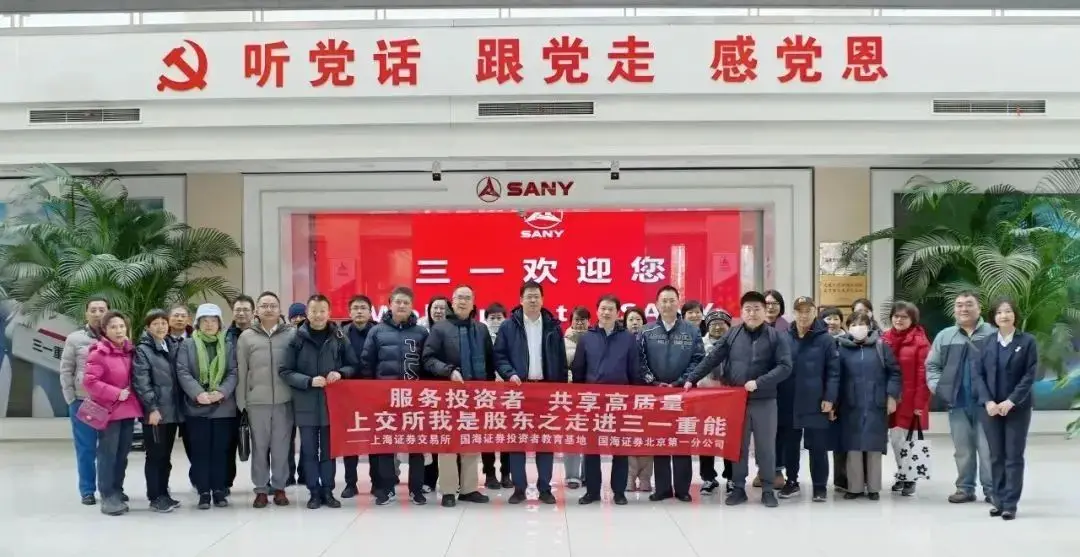
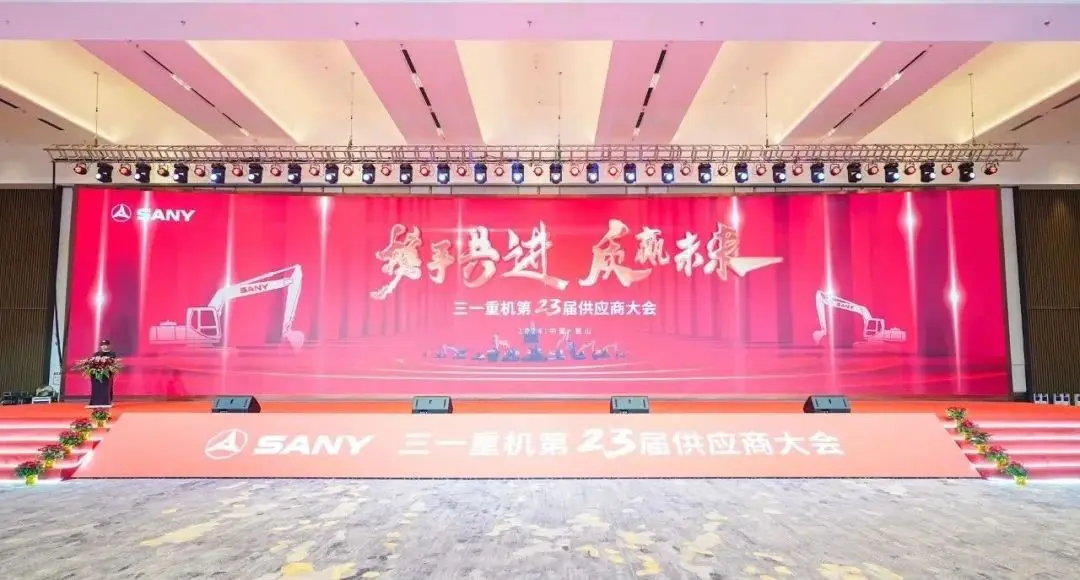
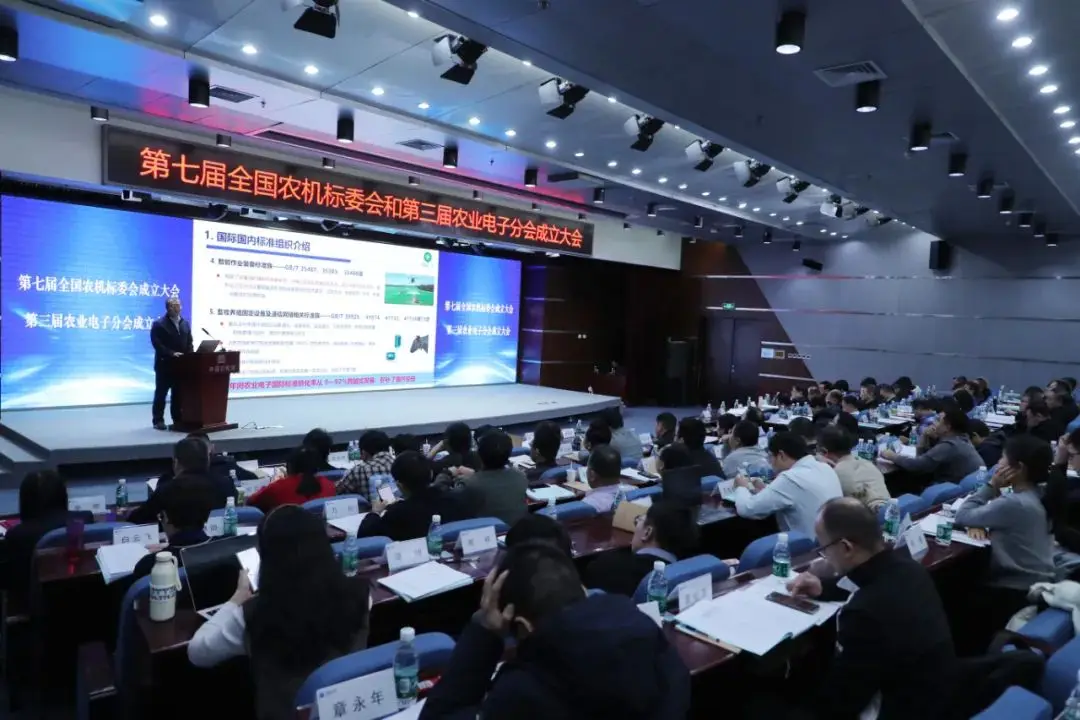
期待你的精彩评论