徐工起重:淬炼中领航 构建行业独有质量管理体系
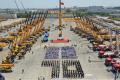
可靠性作为衡量产品质量的重要指标,被企业视为永无止境的追求。作为我国系统工程理论与应用研究的创导人钱学森曾指出“产品可靠性是设计出来的、生产出来的、管理出来的。”可见,只有经过一套完整的质量管理体系的保障,才能实现最终产品可靠性有步骤、有计划地持续提升。 我国工程起重机械行业已有70年的发展历史 我国工程起重机械行业在近70年的发展过程中,曾一度因为缺乏核心技术、产品质量不稳定等因素,受到国
可靠性作为衡量产品质量的重要指标,被企业视为永无止境的追求。作为我国系统工程理论与应用研究的创导人钱学森曾指出“产品可靠性是设计出来的、生产出来的、管理出来的。”可见,只有经过一套完整的质量管理体系的保障,才能实现最终产品可靠性有步骤、有计划地持续提升。
我国工程起重机械行业已有70年的发展历史
我国工程起重机械行业在近70年的发展过程中,曾一度因为缺乏核心技术、产品质量不稳定等因素,受到国外品牌的牵制和市场挤压。进入21世纪后,国内企业在研发、技术、制造方面取得了长足的发展与进步,其中,以徐工起重为代表的本土企业及其产品,更是成为中国工程起重机行业在全球舞台的名片。究其根本,在整体质量水平参差不齐的中国工程起重机制造行业,与其说徐工起重的技术与产品推动和引领着行业的发展,不如说徐工起重建立的一套完整的质量管理体系,才是对行业最具价值的借鉴与贡献。
始于“优生” 打通可靠性闭环通道
概括地讲,可靠性研究可分为前端和后端。在我国工程机械行业,后端可靠性研究主要指可靠性试验检测,该过程与工程应用、产品制造过程结合相对紧密,积累了大量的数据,对于产品生产制造起到了积极地指导和改善作用。而前端可靠性设计决定了产品的“优生”,但由于思路的滞后、数据的缺乏、建模的缺失等,大多数工程机械企业在此均为短板甚至空缺,或仅处于定性而非定量的研究,难以对设计进行针对性的改进。
从1999年开始自主研制工程起重机起,徐工起重就在不断打磨中完善和提升产品可靠性设计,以期打通产品从设计到应用的可靠性闭环通道。2016年,基于产品全生命周期价值提升的G技术平台和可靠性数据管理体系的诞生,构建了徐工起重包括前端可靠性设计在内的产品全生命周期的可靠性管理体系。
徐工G一代技术平台发布仪式
以其专业、全面、强大的测试实验体系及其数据管理为例。徐工起重的产品检测体系覆盖产品各个研发生产阶段,从最初的图纸设计阶段开始,就不断对板材、各系统、零部件、高低温环境等进行实验,第一环节确保设计阶段的可靠性。新产品样机下线后随即进入控制中心,主要系统再次进行检测试验、吊臂接受反复伸缩试验、电器元件经历上百万次检测等,确保产品的绝对性能。进入批量化生产阶段,制造过程中将通过智能化设备完成各个点的检测。直到最后交付用户,依旧会对设备运行状态进行数据采集,及时掌握各类问题,最终通过这些数据进一步反哺设计。
徐工起重机
对于徐工起重而言,从构思开始,关于产品的每一项数据都是有生命的,以产品实际使用信息为基础,结合试验数据统计分析,进而改善产品设计缺陷,实现产品设计能力的不断提升,最终保证产品质量管理的良性闭环。在完善自身的同时,徐工起重更为行业先,以先进、求实的理念与行动,竭力为行业树立可靠性闭环管理体系的典范。
从“制造”到“智造” 实现看得见的质量生产
20年前的中国起重机行业的制造水平还处于一个非常低端粗犷的阶段,与国外成熟的企业相比,制造上的差距要比技术上的差距大得多。为了确保产品在生产制造阶段的可靠性,在国内尚没有成熟、完备的现代化工业体系支撑和参考的情况下,徐工起重自强不息,既在改造传统制造方面“补课”,又在绿色制造、智能升级方面“加课”,不断引领着我国工程起重机行业制造变革的路径与方向。
从“制造”到“智造”的徐工起重机
起步总是困难的,“补课”的过程既是对基础的打牢,也是对心性的煎熬。徐工起重在我国行业内无先例可借鉴的情况下,解决了生产过程专业化和线性化的改造,攻克了产品自身工艺手段解决不了的难题,于1999—2005年之间,率先在行业内完成了按生产工艺流程形成下料(成型)、焊接、机加、装配(底盘及总装)、涂装、调试(检测)六大工艺的建设,使过程质量与生产效率迅速提升。而后全面部署SAP、SRM、MES、ERP物联网等信息系统,走上了生产制造业务信息化道路及拉动式生产组织模式。
其中,2003年行业第一条工程起重机总装流水线和2005年亚洲首条起重机专用底盘流水线的投入使用,使得徐工起重实现了线性化与信息化生产并举,保证了企业在产能提升的同时产品质量的持续稳定。随后的2009—2012年,徐工起重大力投入大吨位基地建设,打造高端制造技术平台,形成大型结构件线性化焊接、装配流水线柔性化生产模式,成为行业标杆。
从“制造”到“智造”的徐工起重机
彼时,智能制造已经开始悄然改变这个世界的方方面面。得益于传统制造能力的扎实铺垫和不断升级,与新一代信息通信技术的深度融合,对于徐工起重而言一切都显得那么“水到渠成”。
近年来,徐工起重紧贴“中国制造2025”发展战略,结合产业特点,围绕“设施互联、系统互通、数据互享、业态互融”四个原则,聚焦核心信息系统的集成与优化,自主研发了全球首条起重机转台智能生产线等九条智能生产线,建设了轮式起重机智能工厂……一系列智能制造举措的落地让徐工起重完成了产品全制造流程数字化管理,对生产过程和产品进行性能与安全可靠性分析与验证,极大地保证了产品制造与设计的一致性,实现看得见、可掌控的产品质量。
从传统制造能力的健全与完善,到生产制造网络化、信息化、数字化、智能化的升级,徐工起重对于质量管理体系中制造环节倾力打造的同时,推动了整个产业链向智能化生产方向的一路向前,为离散型行业智能制造的推进提供了示范和引领。
破冰标准零制定 掌握质量目标话语权
质量管理体系中有一项原则称为“领导原则”,即领导者需确立组织统一的宗旨和方向,也就是常说的质量方针和质量目标。在制造业领域,能够对产品质量目标进行统一度量的就是标准。
经济合作与发展组织研究表明,标准和产品合格评定影响着全球80%的投资和贸易,技术标准可以促进经济全球化、投资便利化。一直以来,95%的国际标准制修订都由欧美等发达国家主导,涉及起重机产品设计、安全等核心技术标准常年被美、德等国家控制,中国起重机生产企业想要不被牵着鼻子走,就必须迎头赶上,掌握国际标准话语权。作为中国工程起重机行业的领军者,徐工起重高掌远拓,笃定前行,在积极致力于国内外标准制订工作的道路上,贡献着代表中国工程起重机质量水平的“徐工智慧”。
徐工起重代表着“徐工智慧”
2008年,徐工起重获得国家标准化管理委员会批准承担流动式起重机分技术委员会秘书处工作,成功组织筹建了全国流动式起重机分技术委员会,并主持制定流动式起重机国家标准。从作为唯一起草单位制定《起重机图形符号第2部分:流动式起重机》等在内的五项国家标准,到主持制定的《全地面起重机国家标准》通过国家标准化主管部门验收审核,并于全国范围内实施,再到提出中国首个流动式起重机安全使用国际标准项目成功立项……多年来,名列流动式起重机全国第一和全球三甲的徐工起重,已累计主持完成了流动式起重机领域2/3的国家和行业标准制修订工作。
从开始起草到主持制定国家标准,再从参与修订到主导制定国际标准、填补国内企业在国际标准领域的空白,除徐工起重之外,业内无能出其右者,徐工起重当仁不让的成为了行业标准制定领域的破冰者和推动者,并在世界舞台彰显着中国质量的自信。
第五届中国工业大奖发布会
质量管理体系的发展是一个稳健成长的过程,非一蹴而就。国际对此公认的五个标准级别包括入门级、接受级、一致性保障级、持续改进级和卓越级。在国内其他企业仅达到初步可接受和尽量保障制造过程一致性的第二、三阶段时,徐工起重早已做到能够持续改善自身系统的第四阶段。
今天,当我们站在审视者的角度去梳理一套完整的质量管理体系时,会发现在每一个决定产品质量的节点上都有徐工起重的身影——我们看到的是徐工起重在设计、制造、应用、标准化等看似4个没有直接关系的环节上分别作出的努力、探索和对极致的追求,看不到的确是其基于此已经建立起来的一套无形但强大的产品质量保障体系。在此过程中,徐工起重在困境中领航,在领航中淬炼,在淬炼中收获,这是其杰出之处,也是其伟大所在,杰出源于它对自身的要求,伟大则是其对行业乃至全球工程起重机领域质量提升的贡献与引领。
历史会铭记领航者的名字。
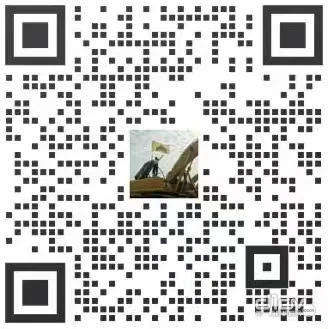
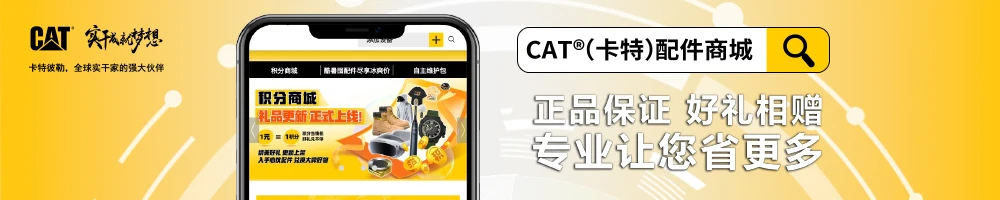
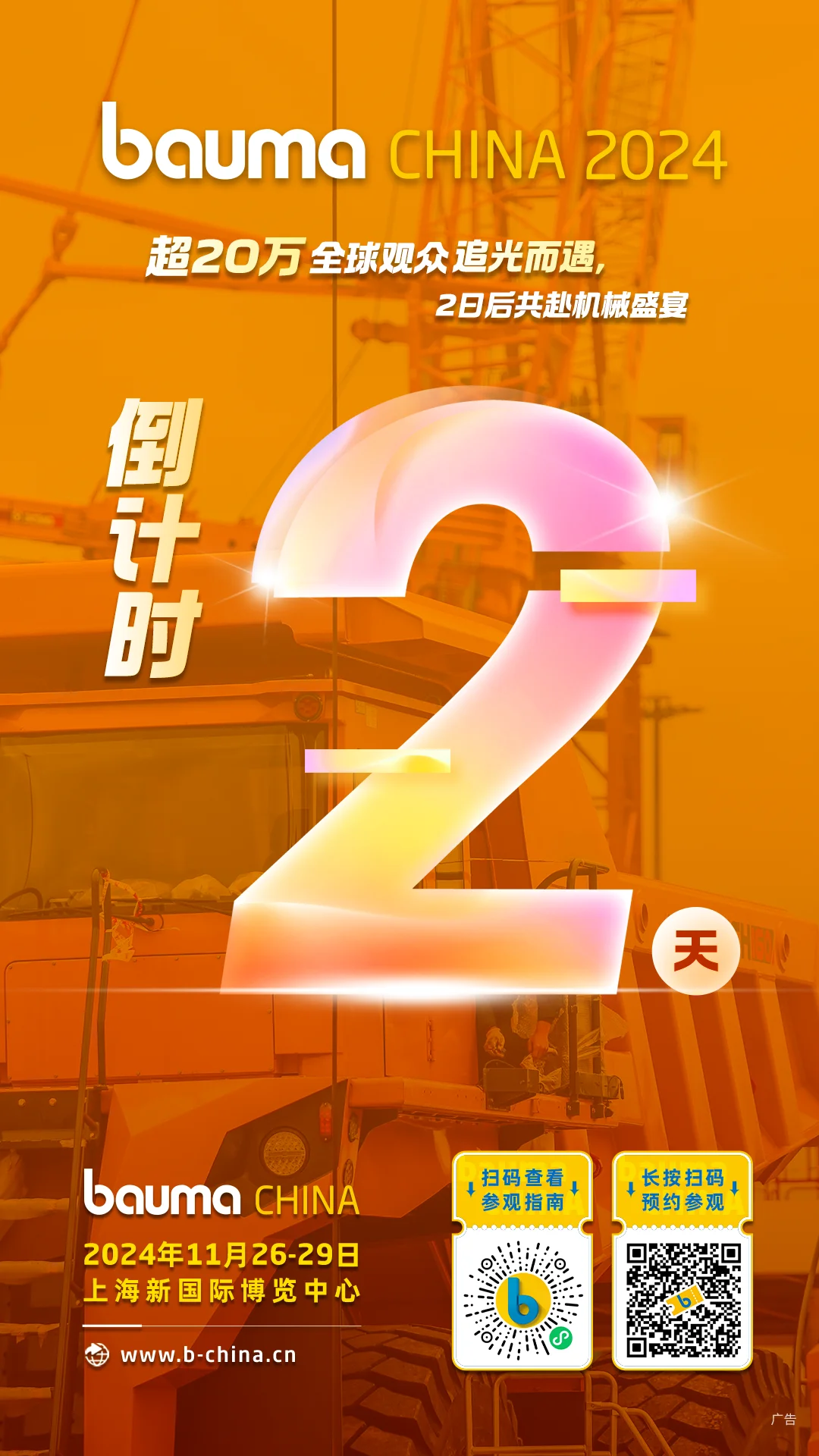
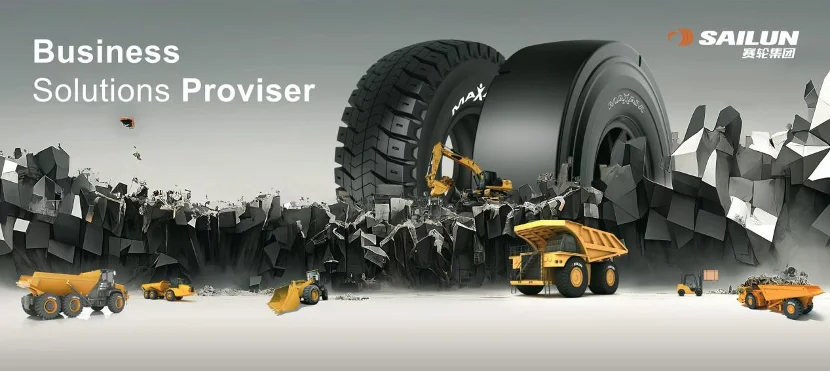
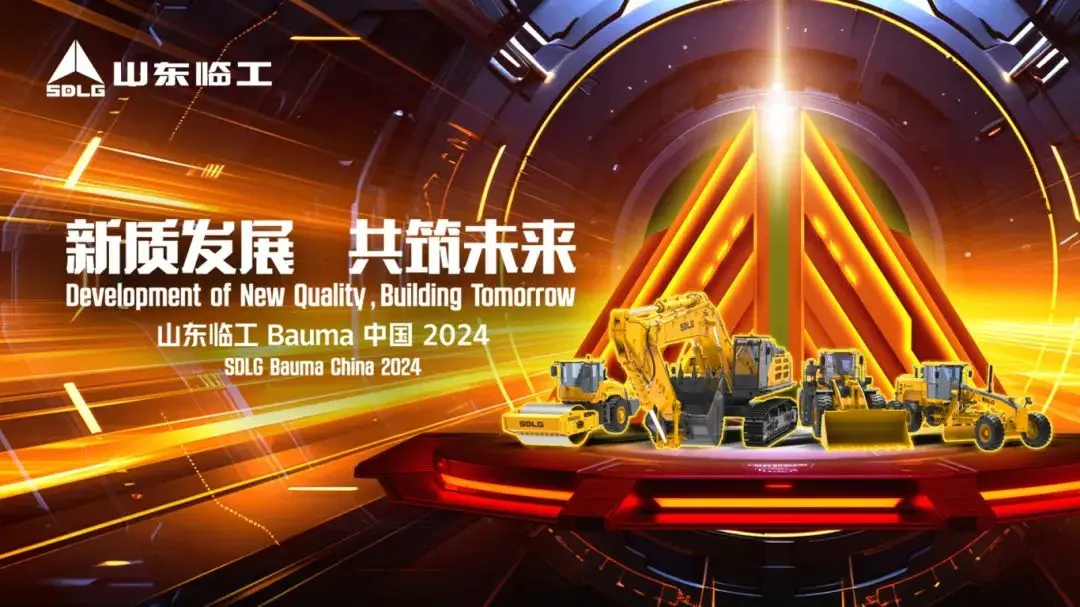
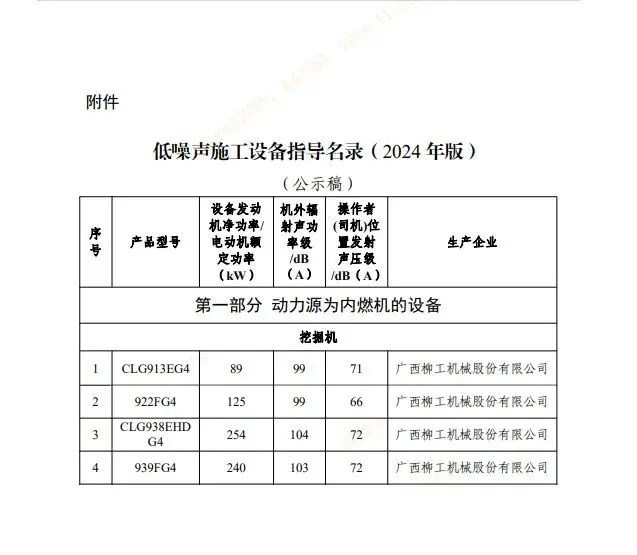
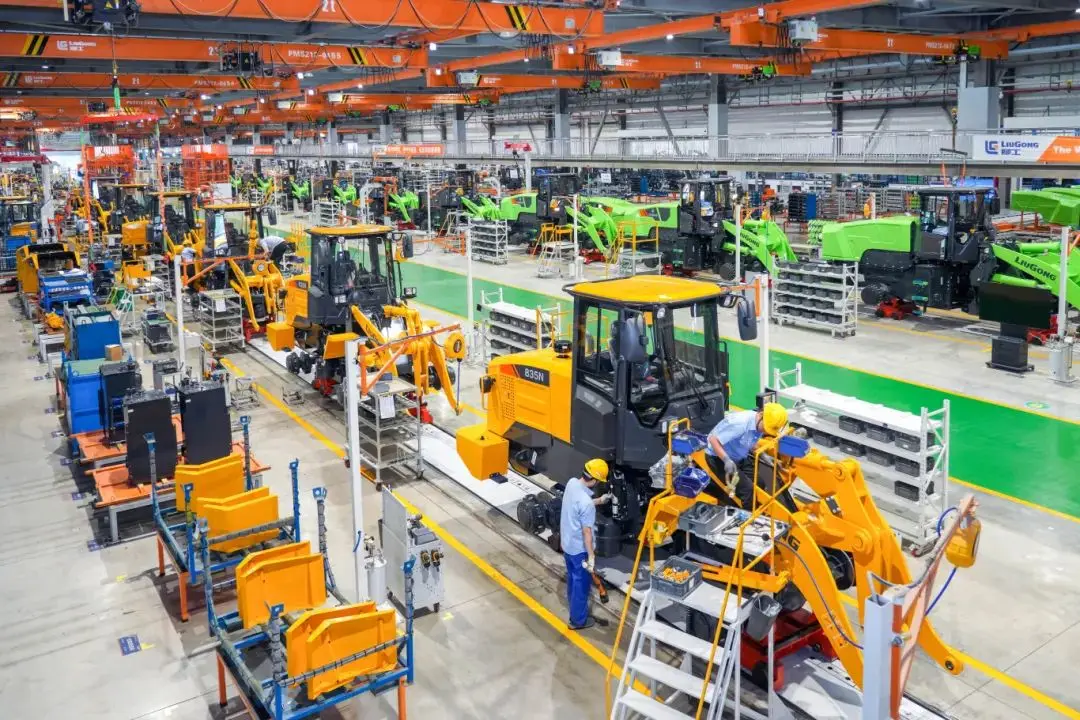
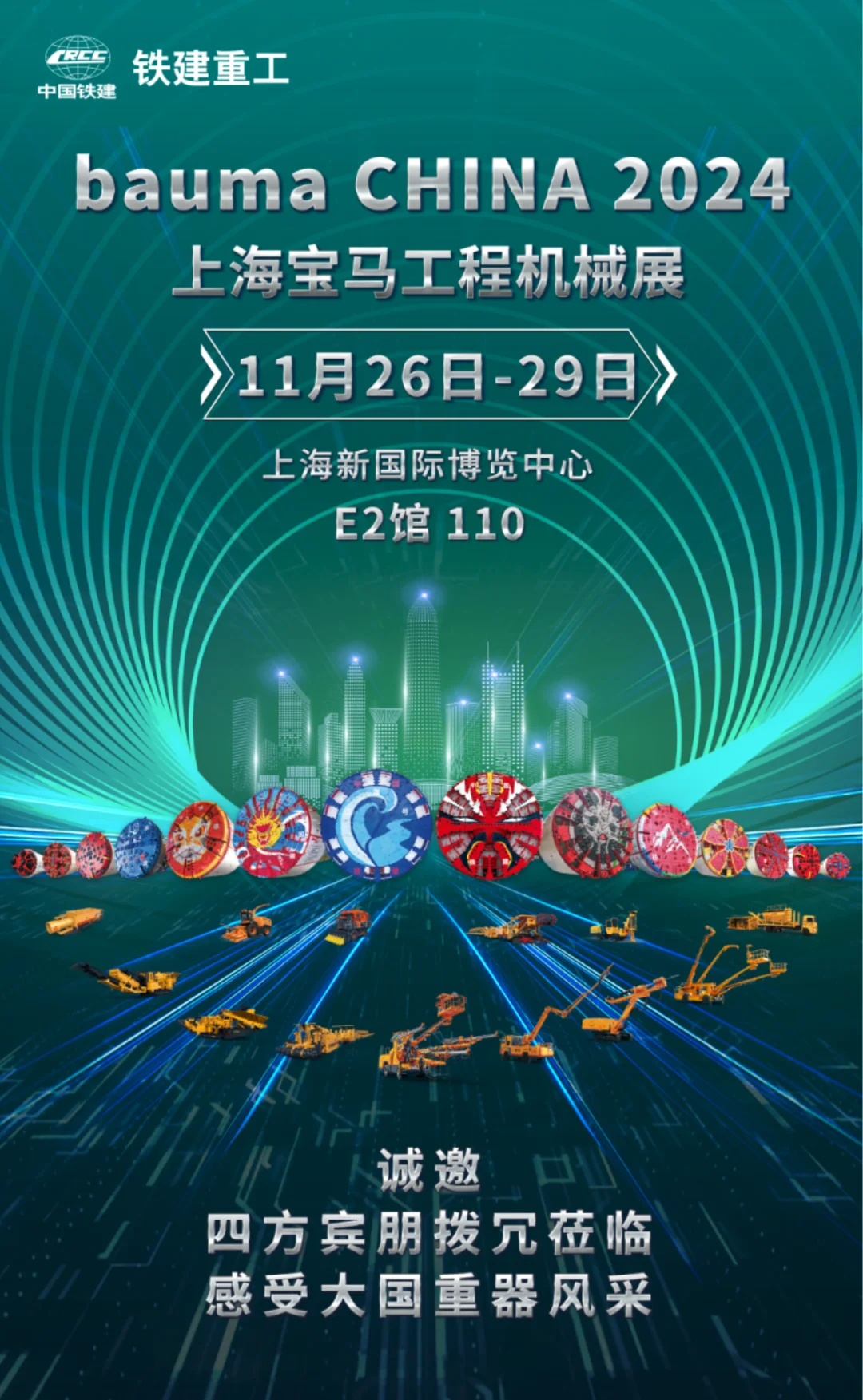
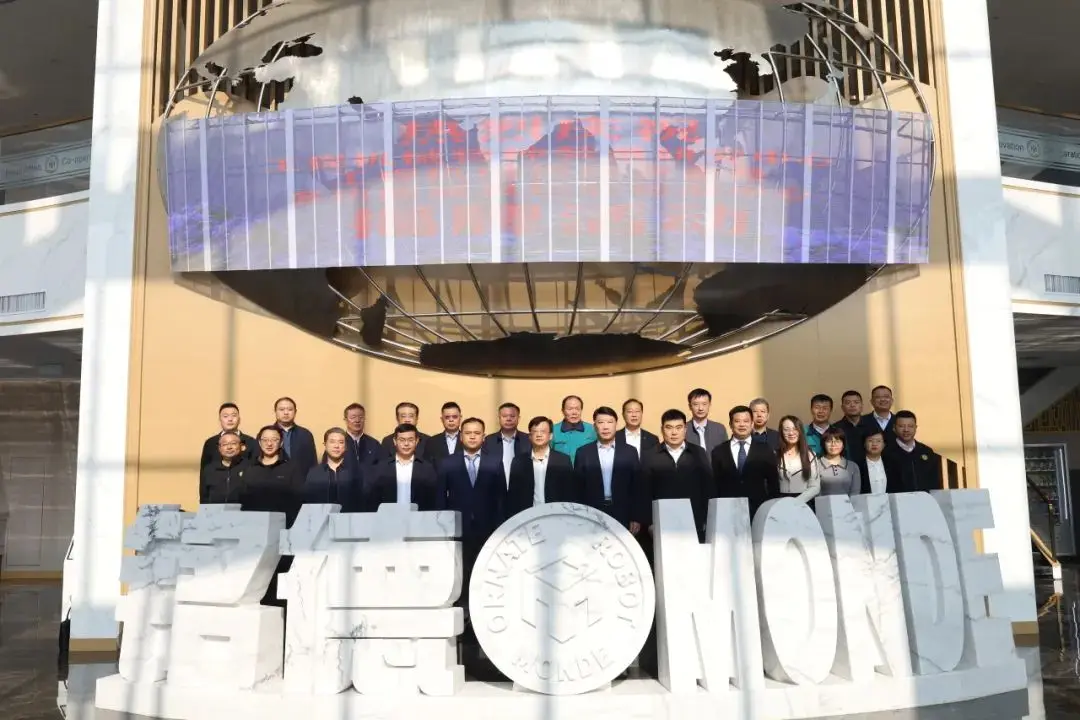
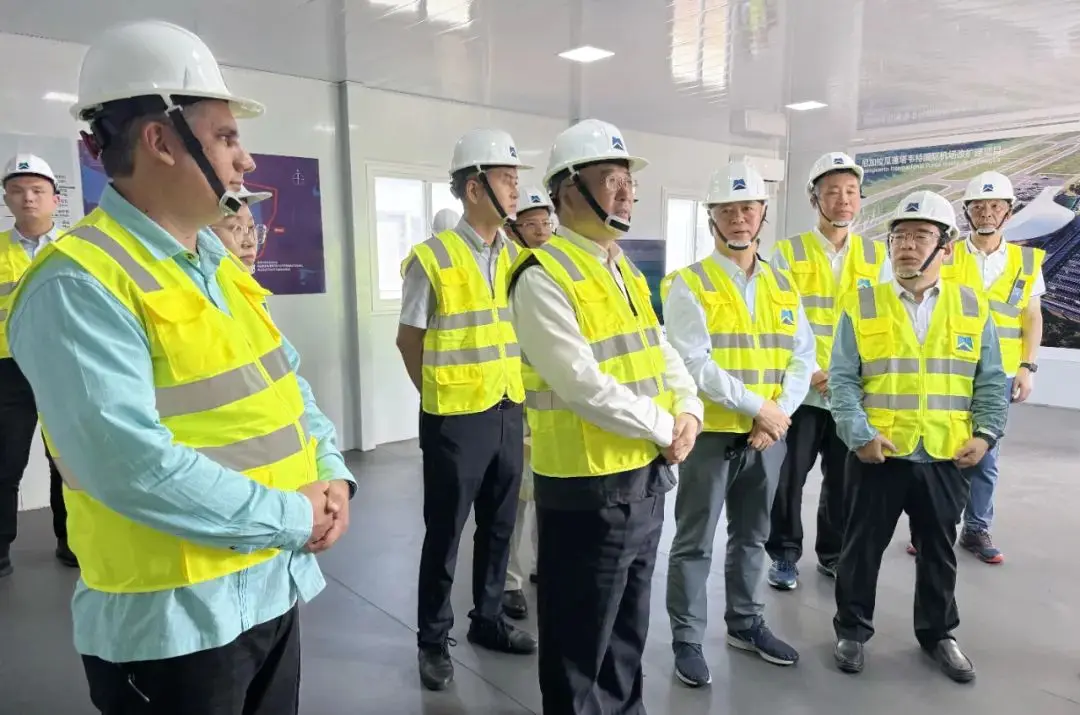

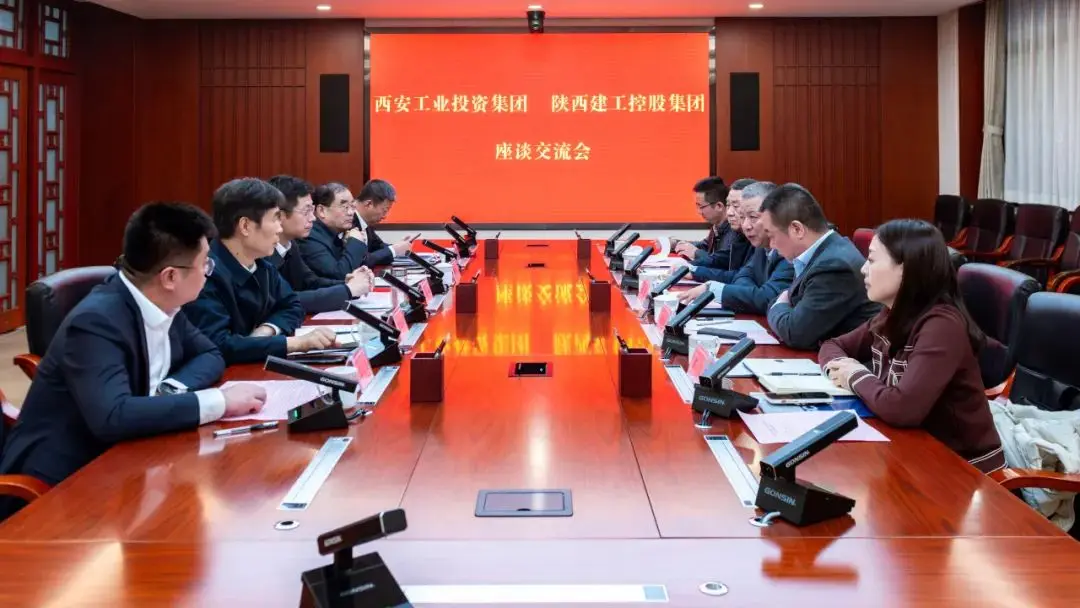
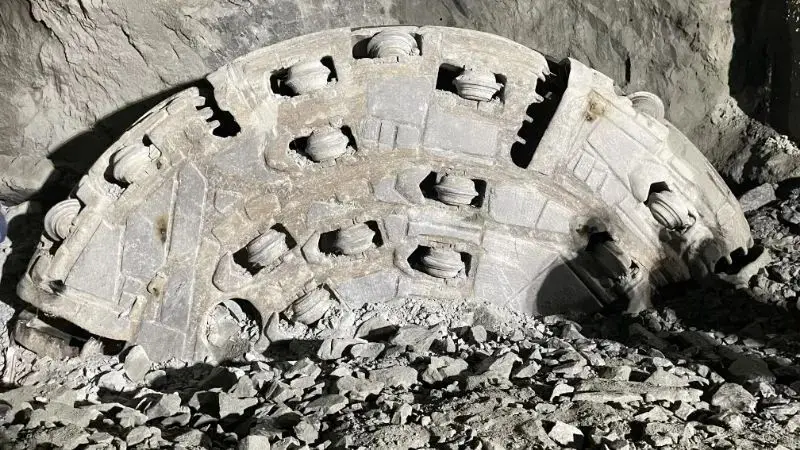
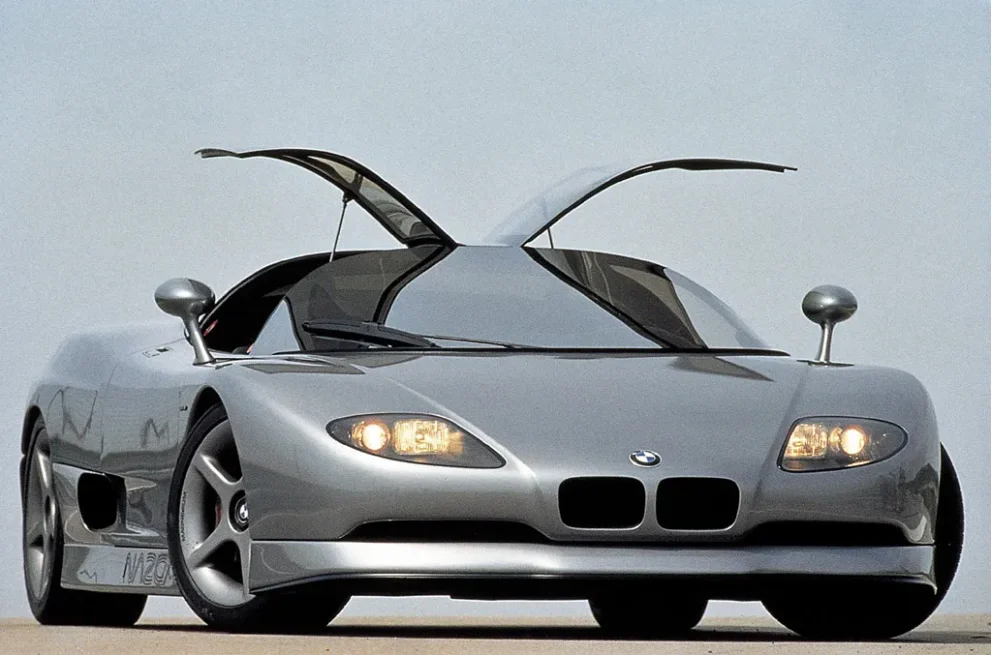
期待你的精彩评论