自卸车货箱举升缸开裂原因分析
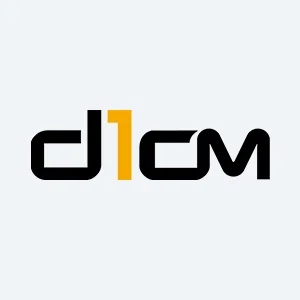
1.故障现象 1台由华俊集团改装的ND3312D41型北方奔驰自卸车,更换举升缸20天后在平整地面上卸料。当货箱举升不足1m时,举升缸底部焊缝开裂,造成货箱突然重心失稳,导致车辆倾翻。 该自卸车货箱采用单举升缸中置式举升机构。更换的举升缸为HG220×900型,额定压力为20MPa。缸筒、底座的材料均为45号钢,缸筒钢板厚度为12mm,底座钢板厚度为40 mm,缸筒与底座焊接在一起,焊缝高度为5m
1.故障现象
1台由华俊集团改装的ND3312D41型北方奔驰自卸车,更换举升缸20天后在平整地面上卸料。当货箱举升不足1m时,举升缸底部焊缝开裂,造成货箱突然重心失稳,导致车辆倾翻。
该自卸车货箱采用单举升缸中置式举升机构。更换的举升缸为HG220×900型,额定压力为20MPa。缸筒、底座的材料均为45号钢,缸筒钢板厚度为12mm,底座钢板厚度为40 mm,缸筒与底座焊接在一起,焊缝高度为5mm。焊接前在焊缝处制作了Y形坡口,并进行了加热。焊接时采用CO2气体保护自动焊机进行焊接,焊后进行了保温。为查明举升缸开裂原因,我们对开裂的举升缸进行了相关的检验和分析。
2.理化检验
(1)化学成分分析
我们对举升缸取样进行化学分析,分析结果表明,该举升缸符合45号钢的化学成分要求,如附表所示。
图1
(2)焊缝断口分析
举升缸缸筒与底座焊接部位焊缝开裂情况如图1所示。从图1看出,焊缝沿圆周方向,其长度约为78.5cm,开裂部分长度约为65cm,尚有13.5 cm没有开裂。
将没有开裂的部分切割,使缸筒与底座分离。将二者分离后看出,断口金属呈颗粒状、色泽较灰暗、无明显塑性变形,焊缝为瞬间断裂,如图2a所示。大部分焊缝金属保留在缸筒上,焊口开裂处位于焊缝与底座连接部分,仅有少量焊缝金属残余在底座部分,由此说明焊缝发生了偏移,偏移量约为5mm,如图2b所示。
(3)金相检验
我们对举升缸底座进行金相组织分析,将金属切片放大500倍可以看到,举升缸底座基体金相组织为网状、块状铁素体和大块珠光体,如图3a所示。焊缝组织较为粗大,热影响区组织为针状铁素体、黑色屈氏体、羽毛状贝氏体和灰色针状马氏体,马氏体含量约为5﹪。如图3b所示。
将金属切片放大50倍可以看到,焊缝与热影响区均出现晶粒明显长大。焊缝与热影响区交界处有未熔合的裂纹,有部分晶粒生长过程中产生了较长裂纹。如图4所示。
3.原因分析
根据焊缝断口分析及金相组织检验结果,我们认为该举升缸焊缝设计、焊接工艺和焊接过程存在以下严重缺陷:
图2
(1)焊缝过窄
该举升缸缸筒与底座仅用自动焊机焊接1遍,有效焊接厚度仅为缸筒壁厚的41.7﹪,由此造成此处接头未焊透、焊接强度严重不足。
(2)焊口偏移
焊接坡口位置出现了5mm 的偏移,焊口偏离有效位置,且安装间隙过大,造成实际有效焊缝变窄,焊接有效面积过小,焊接强度大大降低。
(3)焊接电流小
举升缸裂纹基本是沿焊缝熔合线开裂,焊缝与热影响区间边界分明,从金相组织中发现,焊缝与热影响区间存在较长的裂纹。以上这些说明,焊接电流等工艺参数选择不当,焊接时输入热量不足,焊接没有真正熔合,造成焊接疲劳强度下降,产生片状结构,导致焊缝脆性开裂。
图3
图4
(4)加热保温不到位
45号钢焊接性能较差,需要做焊前加热、焊后保温,否则容易产生热裂纹、冷裂纹、气孔、焊接脆化等缺陷。在举升缸底部的焊缝热影响区发现,有部分针状马氏体、羽毛状贝氏体等淬火
组织。这些都说明焊前加热温度不够,焊后保温时间不长。
我们认为:该举升缸焊接部位的焊缝和焊接工艺设计、以及实际加工过程,均存在较严重问题,由此导致举升缸在早期使用过程中的脆性断裂。对于这种承受大载荷、涉及安全使用的举升缸,应当选用充分焊透的焊缝形式,且焊接有效厚度应当与缸筒壁厚相当。对于这种厚度的钢
板用CO2气体保护焊接时,应当用电焊机焊接2遍,或手工焊接3遍。
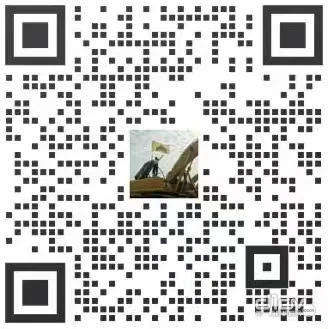
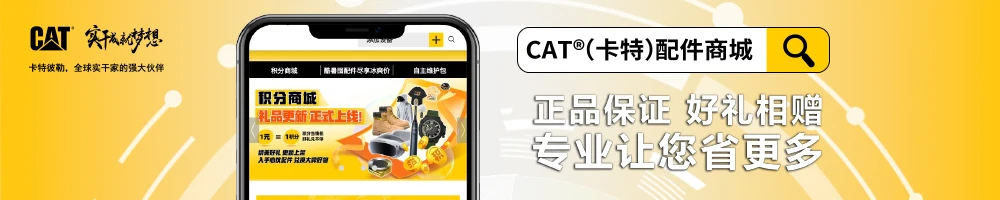
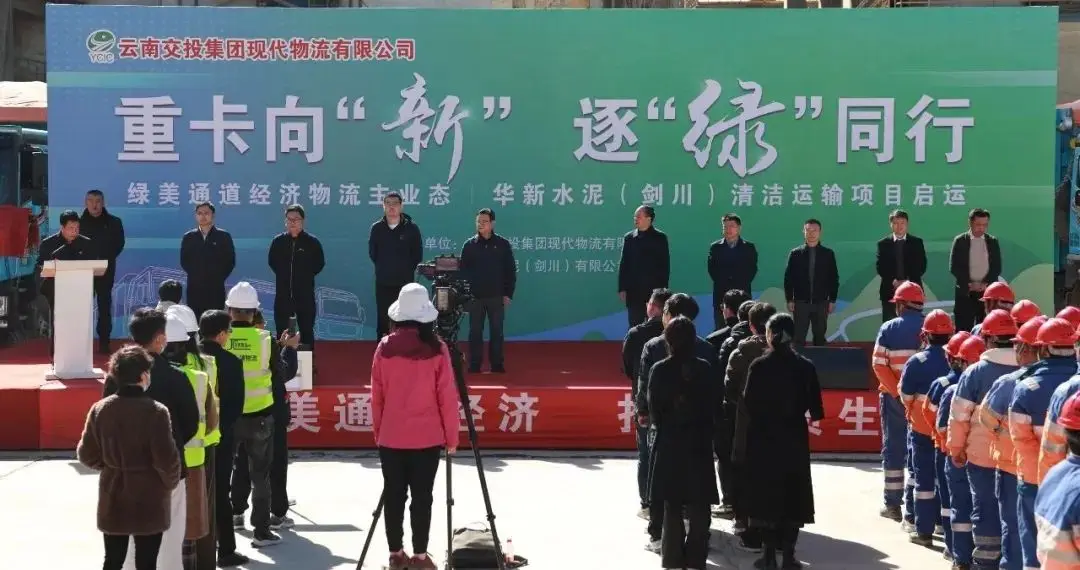

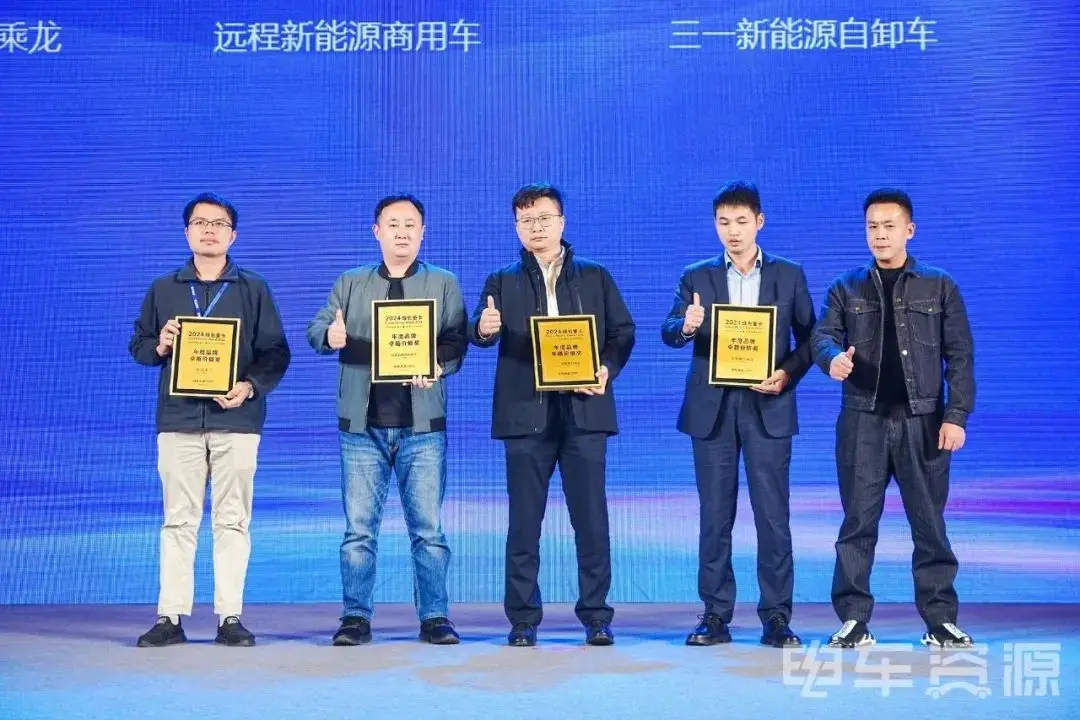
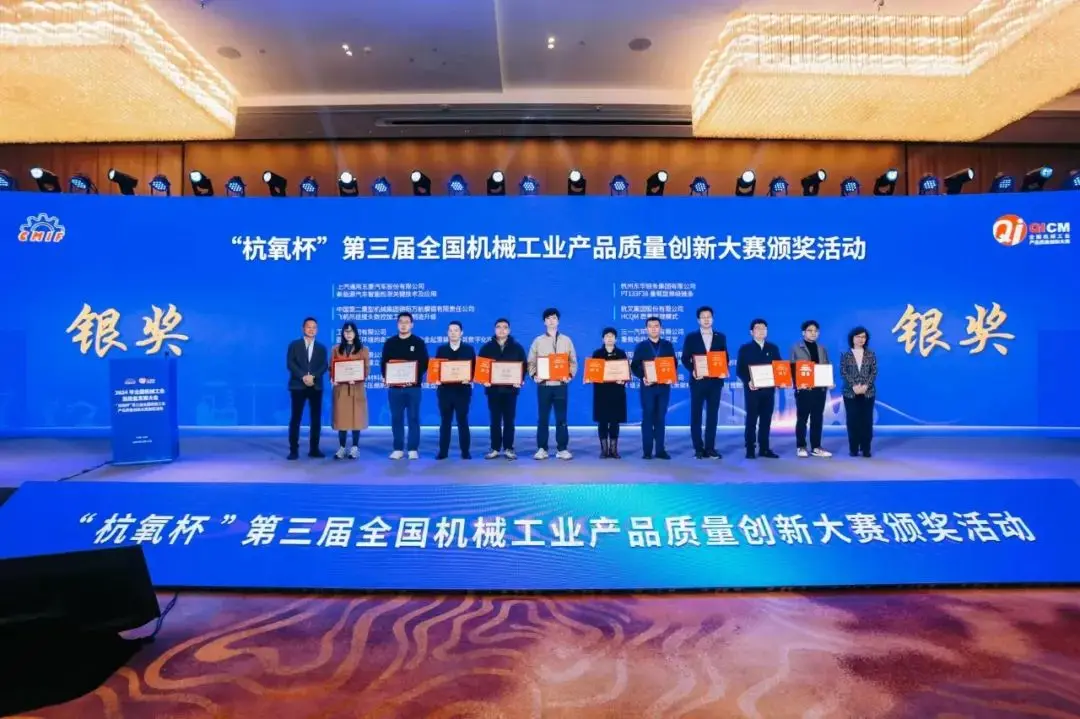
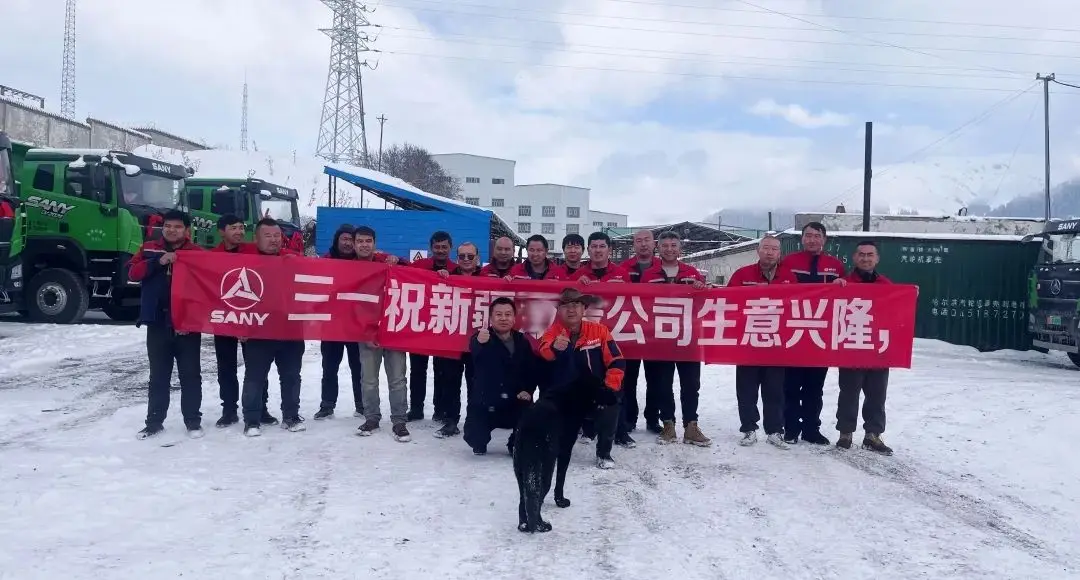
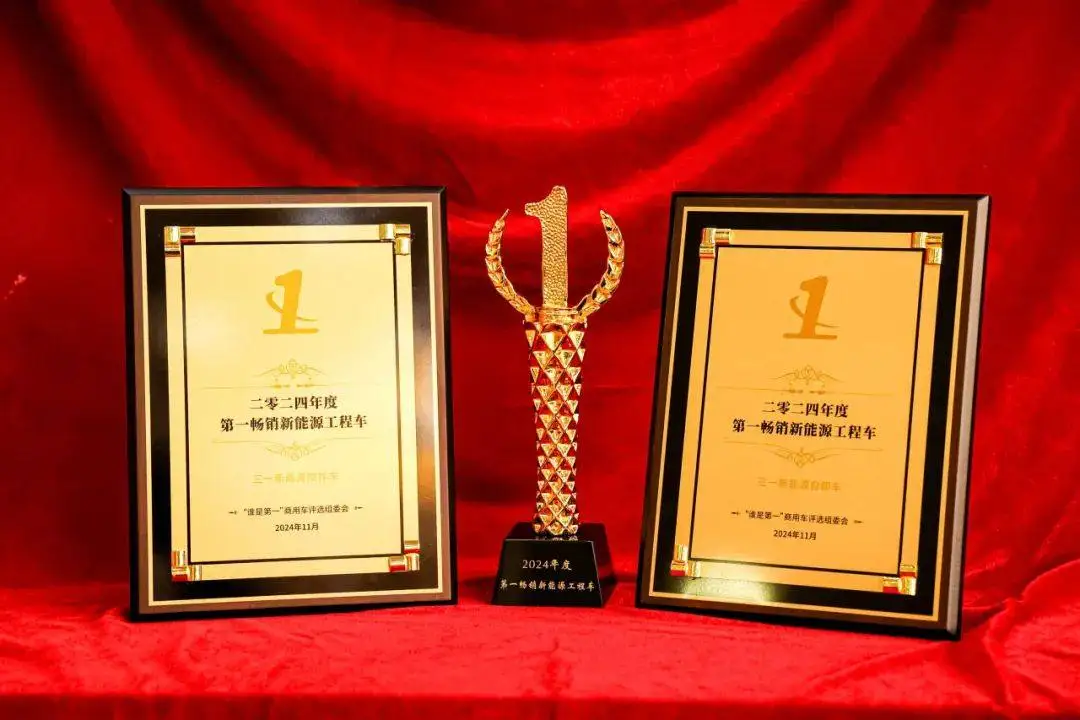
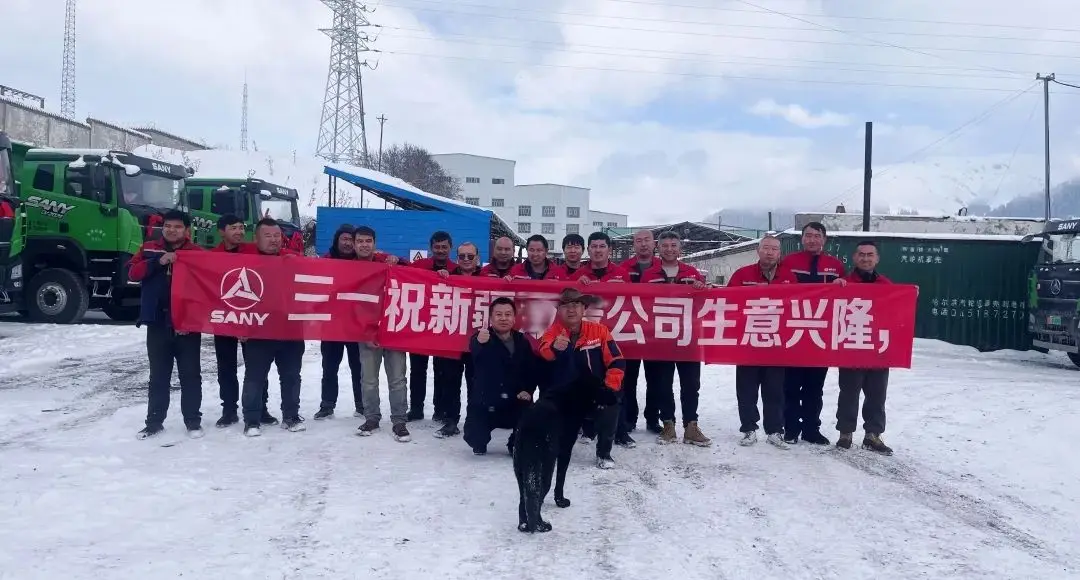
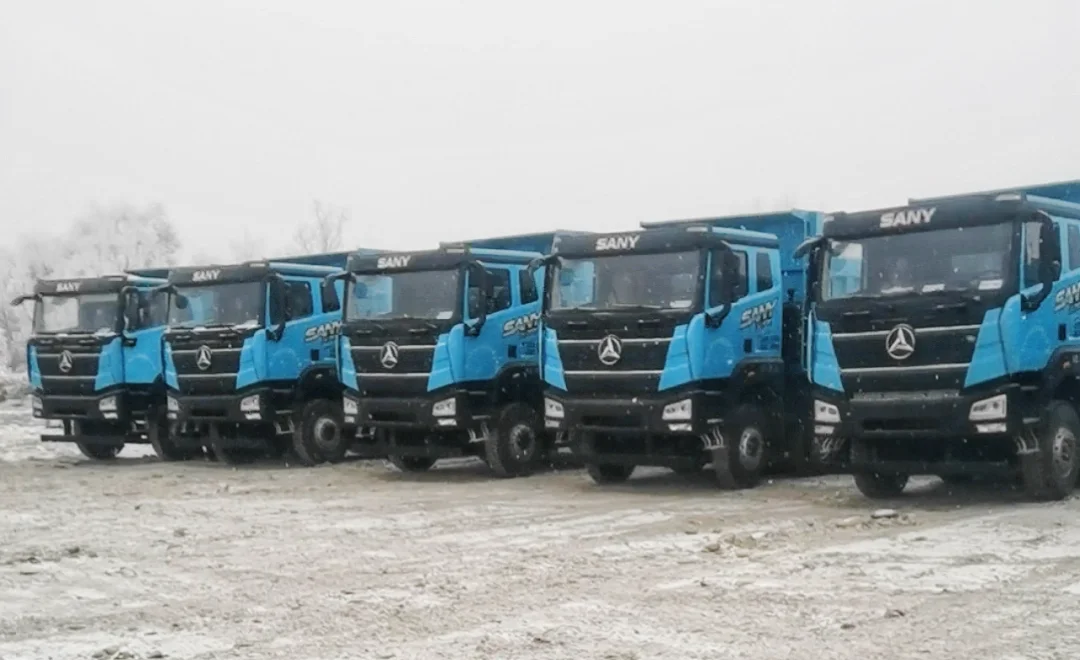
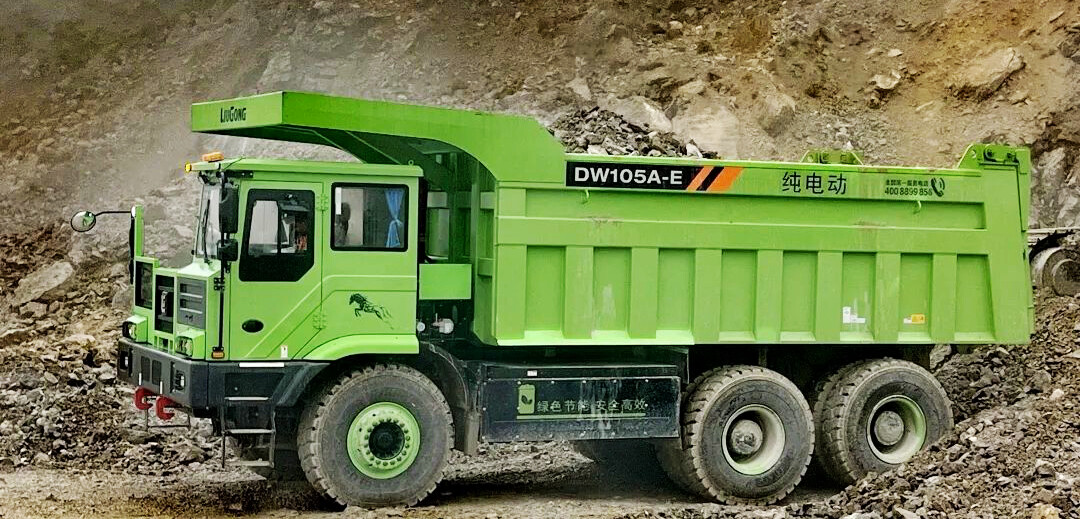
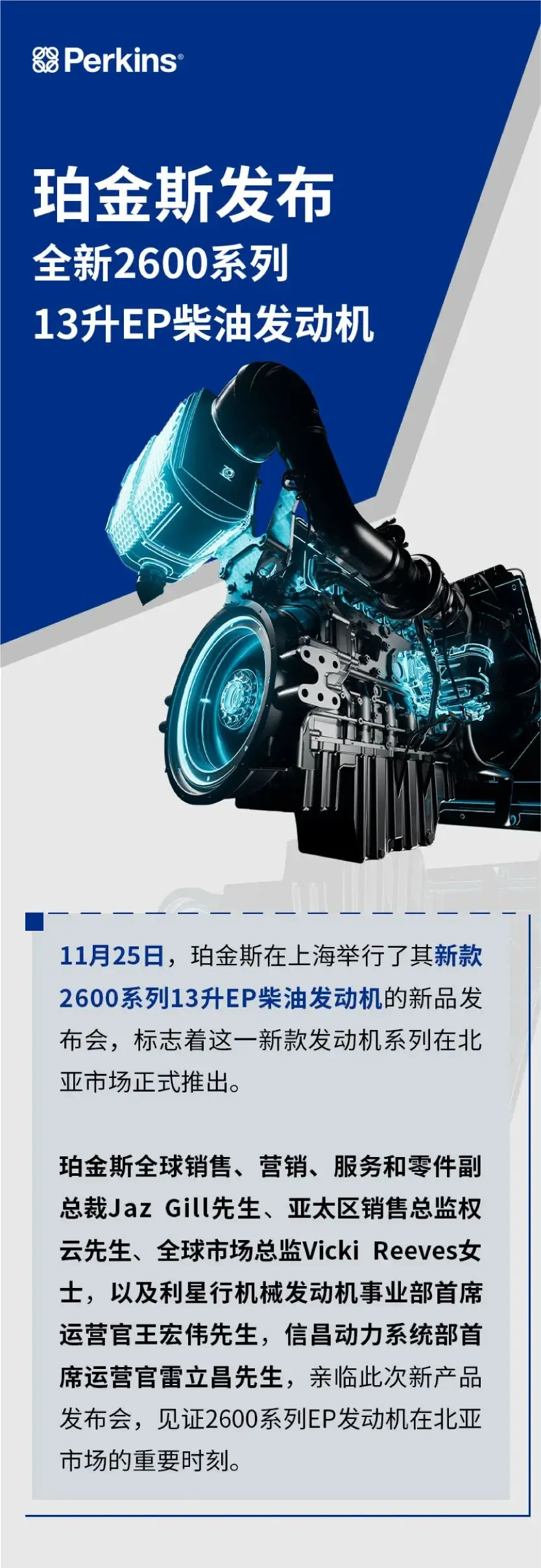
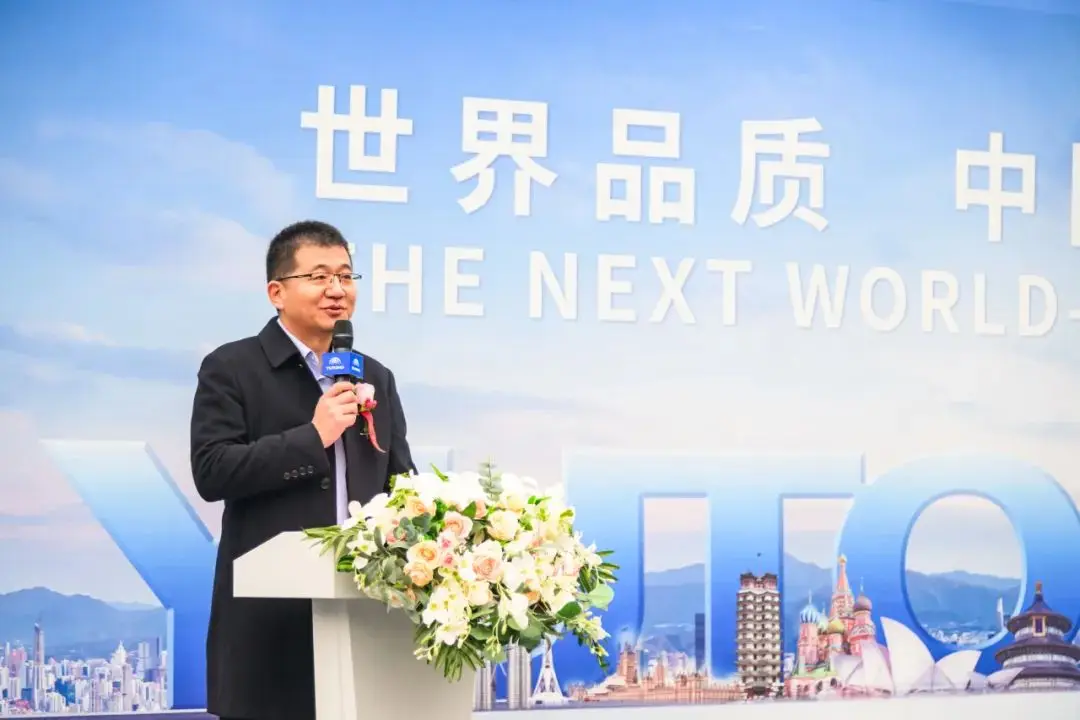

期待你的精彩评论