北方交通浅谈起重机臂体设计的优化与应用
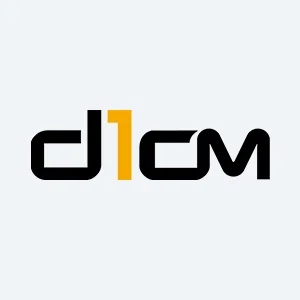
近年来,随着汽车起重机的不断发展,汽车起重机吊臂截面形状也由四边形,六边形,八边形等逐渐进化成U形。U形截面可以显著提高截面的抗弯能力,试验表明,起重机主臂截面相同周长相同厚度情况下,使用U形截面和使用六边形截面相比抗弯性能提高近10%,因此U形截面主臂已被广泛采用。利用有限元分析方法对U形截面吊臂进行分析与优化,对提高材料的利用率,提高吊臂的强度、刚度和稳定性是非常有必要的。1 工况分析 某型号
近年来,随着汽车起重机的不断发展,汽车起重机吊臂截面形状也由四边形,六边形,八边形等逐渐进化成U形。U形截面可以显著提高截面的抗弯能力,试验表明,起重机主臂截面相同周长相同厚度情况下,使用U形截面和使用六边形截面相比抗弯性能提高近10%,因此U形截面主臂已被广泛采用。利用有限元分析方法对U形截面吊臂进行分析与优化,对提高材料的利用率,提高吊臂的强度、刚度和稳定性是非常有必要的。
1 工况分析
某型号汽车起重机为5节伸缩主臂,双油缸加绳排式伸缩机构。根据吊臂的形式可知起重机工作状态下各节臂搭接处应力值最大,为危险截面。一般情况下,每种臂长在相应长度的最大起重力矩工况时应力达到最大值。双缸加绳排式伸缩机构的起重机性能表一般为7列,我们选取每列中最大起重力矩的工况进行分析。共7种工况。
2 几何模型
处理吊臂几何模型建立完成后,通过parasolid格式导入ANSYS workbench中。之后,根据不同臂长工况下伸缩油缸的行程,对二、三、四、五节臂进行平移操作,共建立7种不同长度的几何模型。危险截面处于吊臂的搭接处,而各节臂的臂头臂尾处应力值较小。将螺栓、销轴、垫板、油杯等对吊臂整体分析影响很小的零件删掉,并且去掉板上的焊接坡口,只留下包箍、滑轮支座、绳排拉板和滑块等主要承力结构。然后对一些不规则的零件进行切割处理,使之变成比较规则的形状,以便于划分网格。
3 网格划分
由于吊臂结构复杂,如果抽中面用壳单元来分析将会在几何处理时花费大量时间,故采用实体模型。吊臂板采用solid186单元用sweep的方式划分成规则的网格,个别不规则的零件采用自由分网。主要承力零件如上下槽板,在厚度方向划分为2层单元,有5个节点,可以比较准确的得到该处的应力情况。solid186单元是一个高阶三维20节点固体结构单元,solid186单元具有二次位移模式,可以更好的模拟不规则的几何形状。吊臂中各节臂之间力的传递是通过伸缩油缸和伸缩绳排来进行的,故而要把伸缩油缸和伸缩绳排也建立到模型中。伸缩油缸共有2根,分别连接在一节臂二节臂尾部和二节臂三节臂尾部。伸缩油缸采用beam188单元来模拟,beam188的截面尺寸即伸缩油缸的真实尺寸。伸缩油缸和吊臂尾部油缸支座处为销轴连接,可以相互转动,即不传递弯矩。销轴也采用beam188单元来模拟,销轴与伸缩油缸、销轴与吊臂油缸支座处采用MPC revolution的方式进行连接,使之可以相互转动。伸缩绳采用link8单元进行模拟,一端连接到吊臂的绳排支座处并绕过滑轮连接到另外节臂的绳排支座。
4 约束与载荷
滑块材料为MC尼龙,刚度与钢材相比相差很多,故采用No Separation的方式连接,此种方式连接对整个吊臂的刚度影响很小,而且NoSeparation连接方式是线性的,计算速度快。基本臂尾部与转台连接处约束UX、UY、UZ3个平动自由度和RotY,RotZ2个转动自由度,即使吊臂可以绕根部在变幅平面内转动;变幅支座处采用同样的方式进行约束。五节臂头部导向滑轮处施加朝向卷扬方向的单绳拉力,起升滑轮处施加吊重载荷,2个滑轮之间有大小相等方向相反的单绳拉力。重力加速度取10m/s2,以加速度的方式添加。
5 应力测试结果
按照该有限元分析对样车原设计与工艺进行了优化处理。样车试制完成之后,对吊臂进行了应力试验,选择与有限元分析相同的工况进行测试,贴片位置为每节臂搭接处,应力测试结果与有限元分析结果比较可以看出,实测值与有限元分析值比较接近,但是还是有一些误差,主要原因是对吊臂两铰点的约束是全约束,没有反映出吊臂工作中下车和转台的变形对吊臂造成的影响。
6 结 论
通过使用ANSYS软件对汽车起重机吊臂进行有限元分析表明分析结果与实际测量值接近,在可以接受的范围内,说明使用该方法分析得到的结果比较准确,并且该方法过程简单、操作简便,可以有效地指导实际设计工作和生产制造。
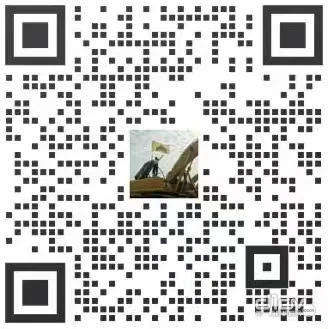
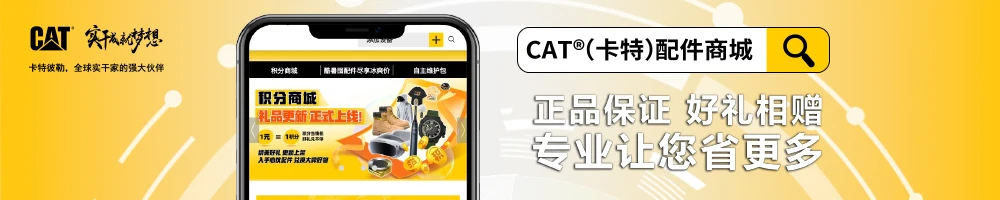
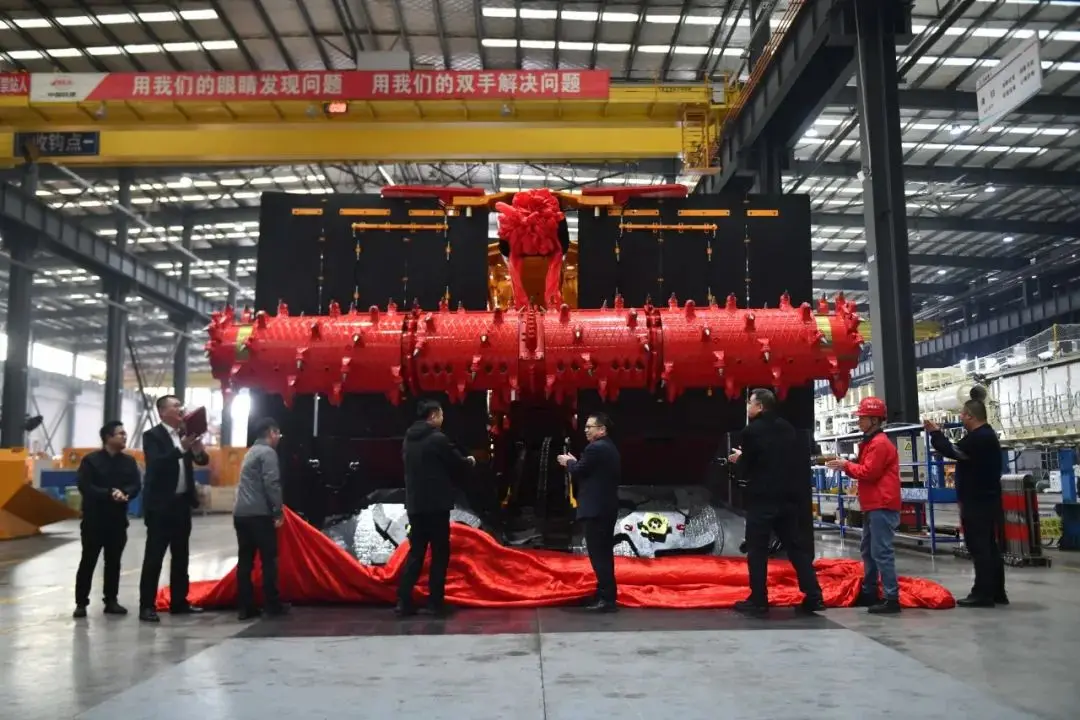
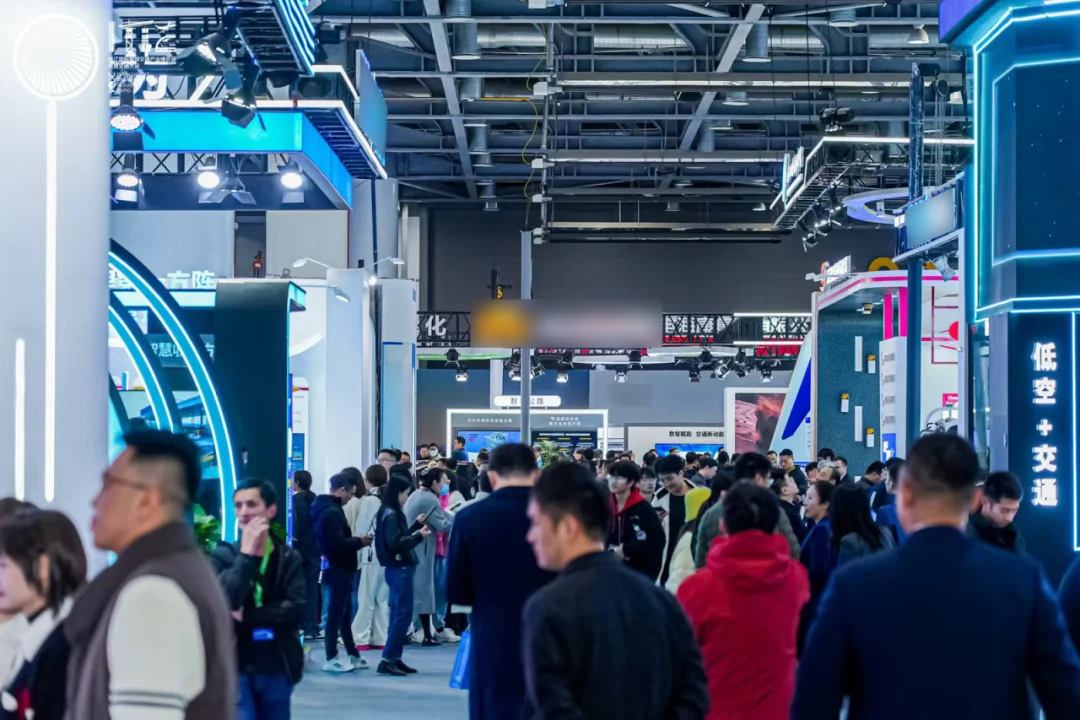
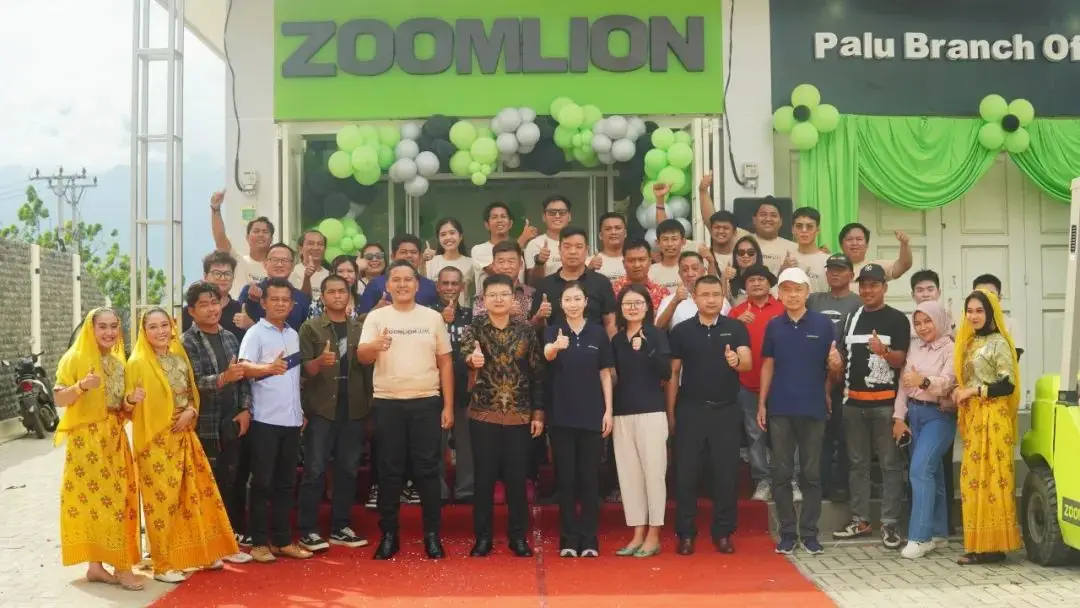
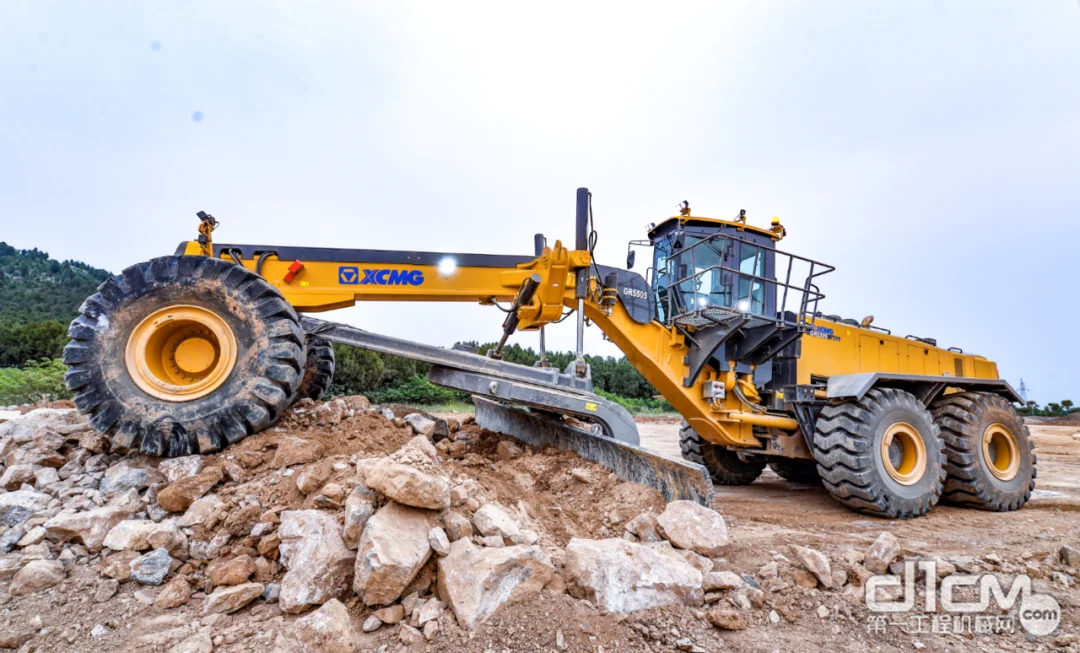
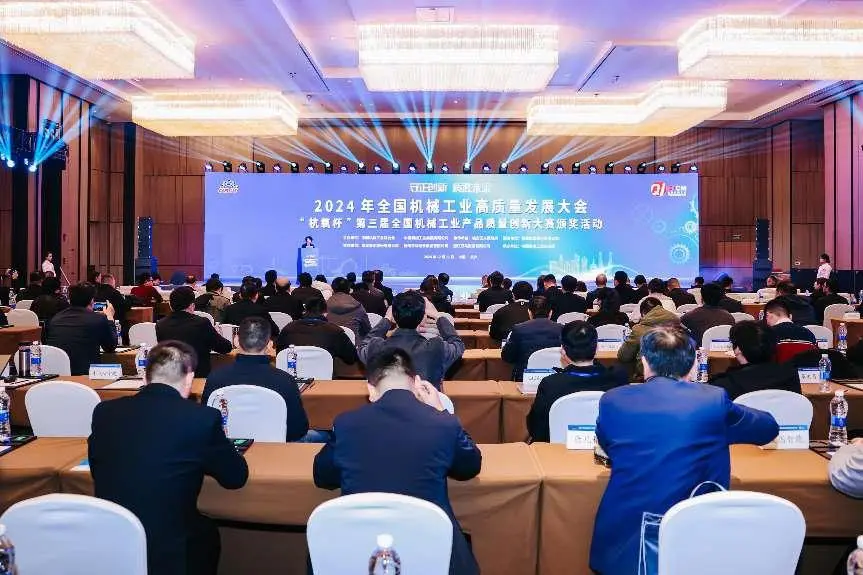
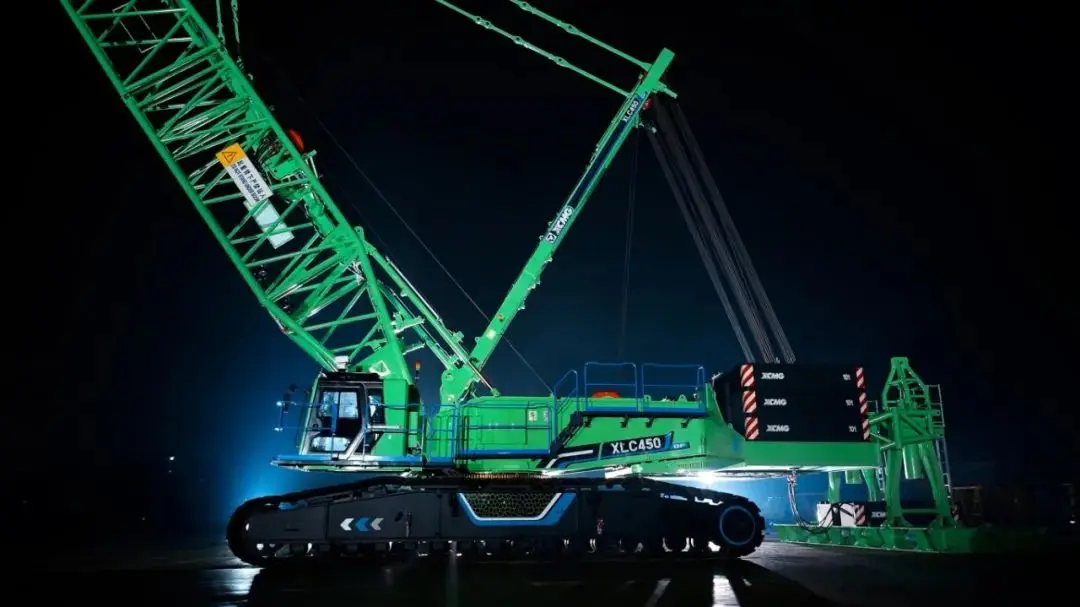
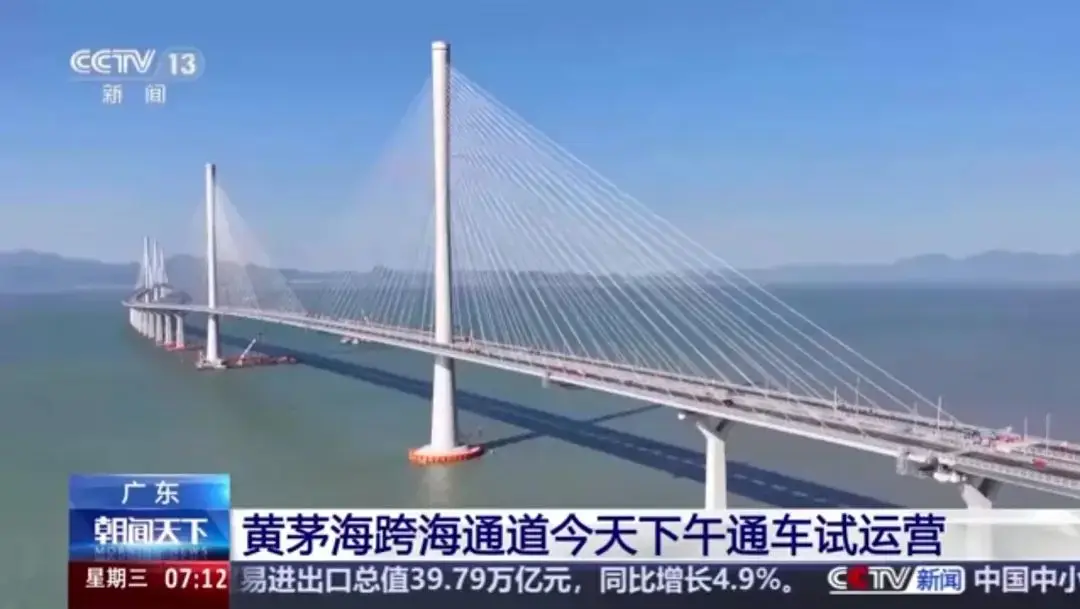
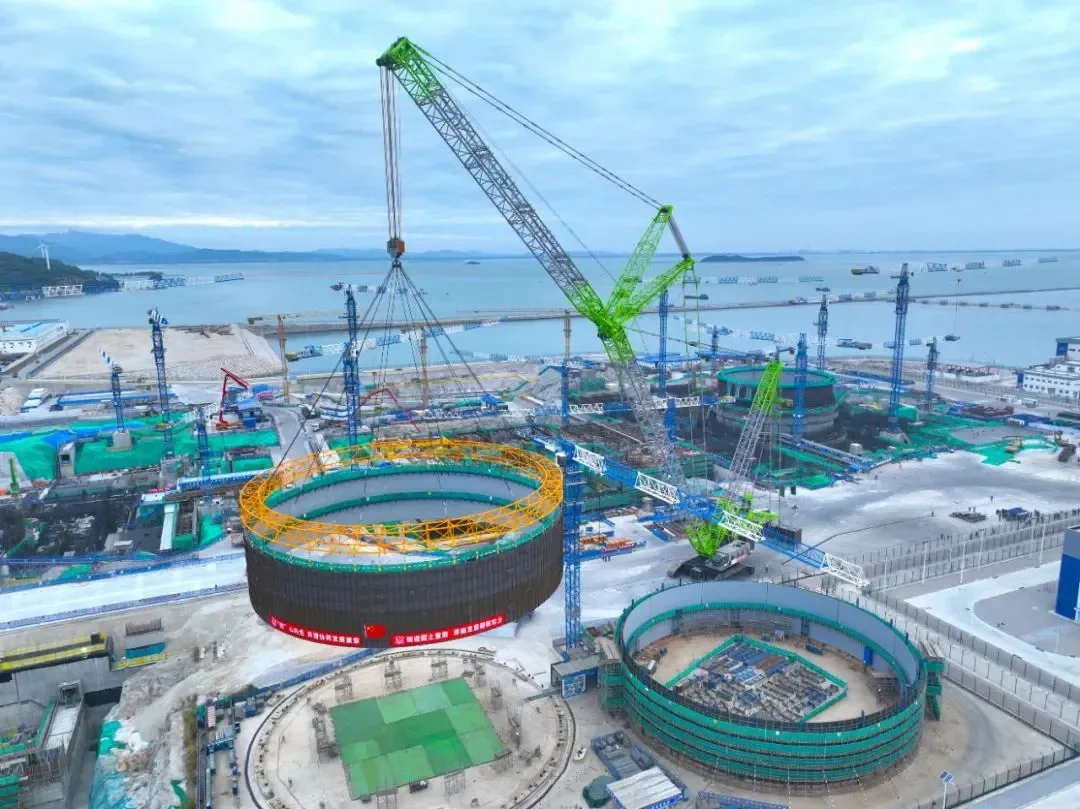
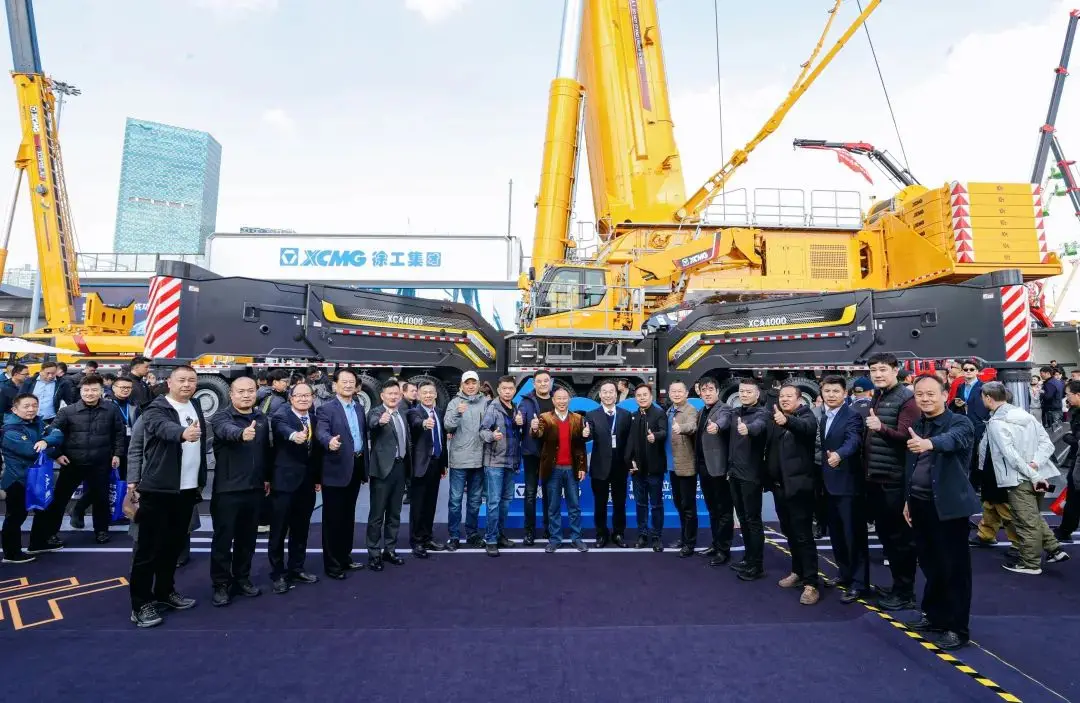
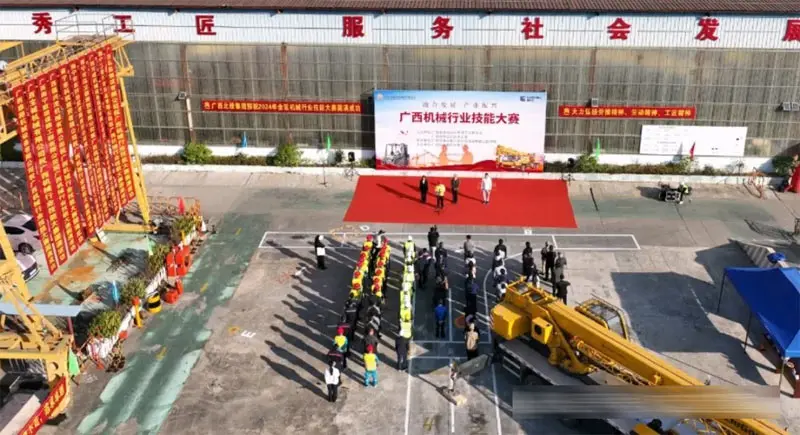

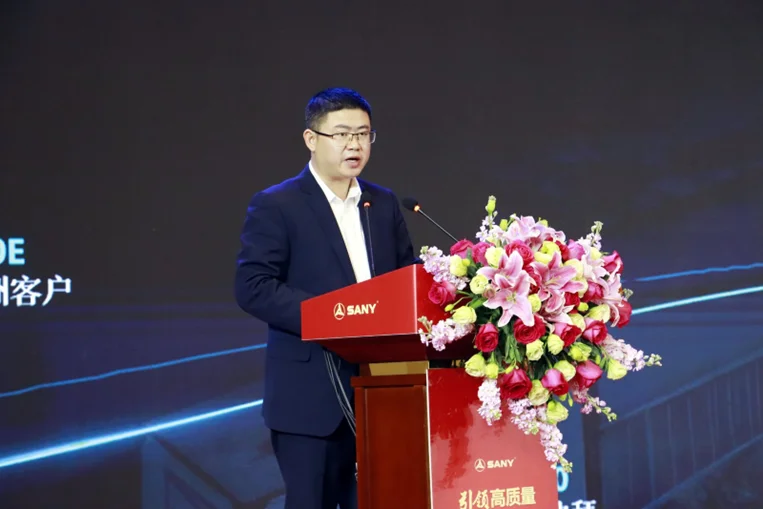
期待你的精彩评论