中联重科工程起重机公司工序改善初显成效
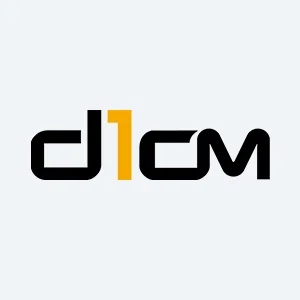
在中联重科工程起重机公司长沙汽车吊结构厂房二跨,以前生产25~80T的转台时,底板与大法兰圈均采用手工烧焊的方式进行生产。手工烧焊在进行转台摆搭后,需吊装到变位机进行底板与法兰圈烧焊,不仅工作量大,而且焊接机器人的利用率也只能达到73%,很不划算。
手工烧焊的问题一直是车间生产的提速障碍,也是让我们焊工很头疼的事。当我们看着先进的机器人焊接设备时,大家冒出了这样的想法:“能不能把这些先进的设备充分利用起来,让机器人编程后代替人工焊接底板与大法兰圈,减少人工的劳动强度?”当我们提出建议后,转台组的工艺人员便开始研究解决方案:如制作专用工装、更改工序等等。
研究过程中,大家发现转台底板大法兰圈的变形量无法保证在可控的范围内,因此可能达不到设计要求。经过工艺人员共同探讨论证后,大家一致决定创新尝试,更改工艺工序。我们车间一线员工、工艺人员,决定实验生产一台55V532的产品,将底板与大法兰圈焊接程序先用焊接机器人进行编程,然后在流入转台前段摆搭,接下来用整体机器人焊接,最后金加工。通过对焊后变形数据进行三坐标划线仪检测,测得在该方式下未金加工状态时,大法兰圈的平面度能够控制在生产、设计要求范围内。同时,实验中的底板焊接变形度、焊后金加工等,每道工序均能实现很好的控制。实验的成功给予我们极大的信心,因为这表示有望在25~80V产品的结构件上实现全面机器人焊接。到那时,不仅能够给我们车间一线操作者带来“福利”——减低手工烧焊大法兰圈的劳动强度;同时,也使得车间里的焊接机器人得到更高效率的利用,缩短生产节拍、保证焊缝质量,从根本上杜绝由于转台大法兰圈的人工焊接缺陷导致的质量事故。
这只是车间员工在落实工程起重机公司“品质为王”战略决策上走的一小步,接下来,车间将针对生产效率的提升进行更加深入的挖掘活动。
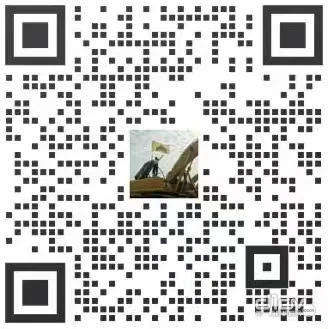
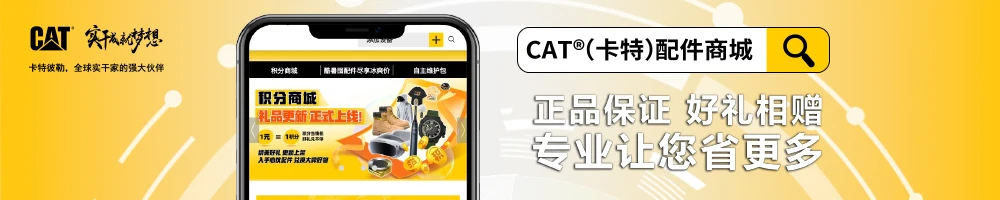
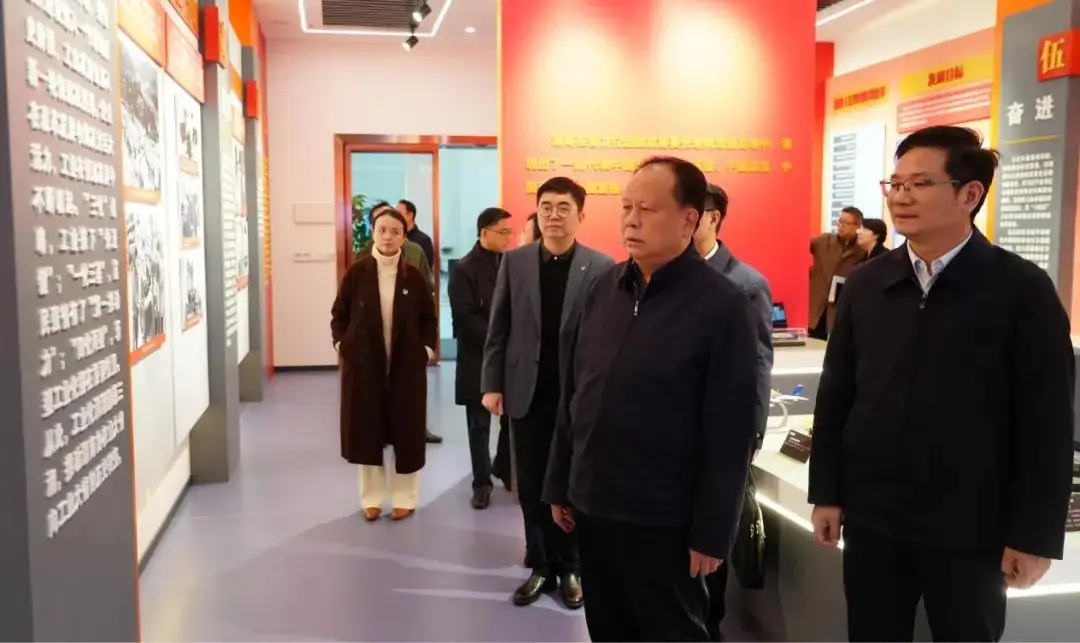
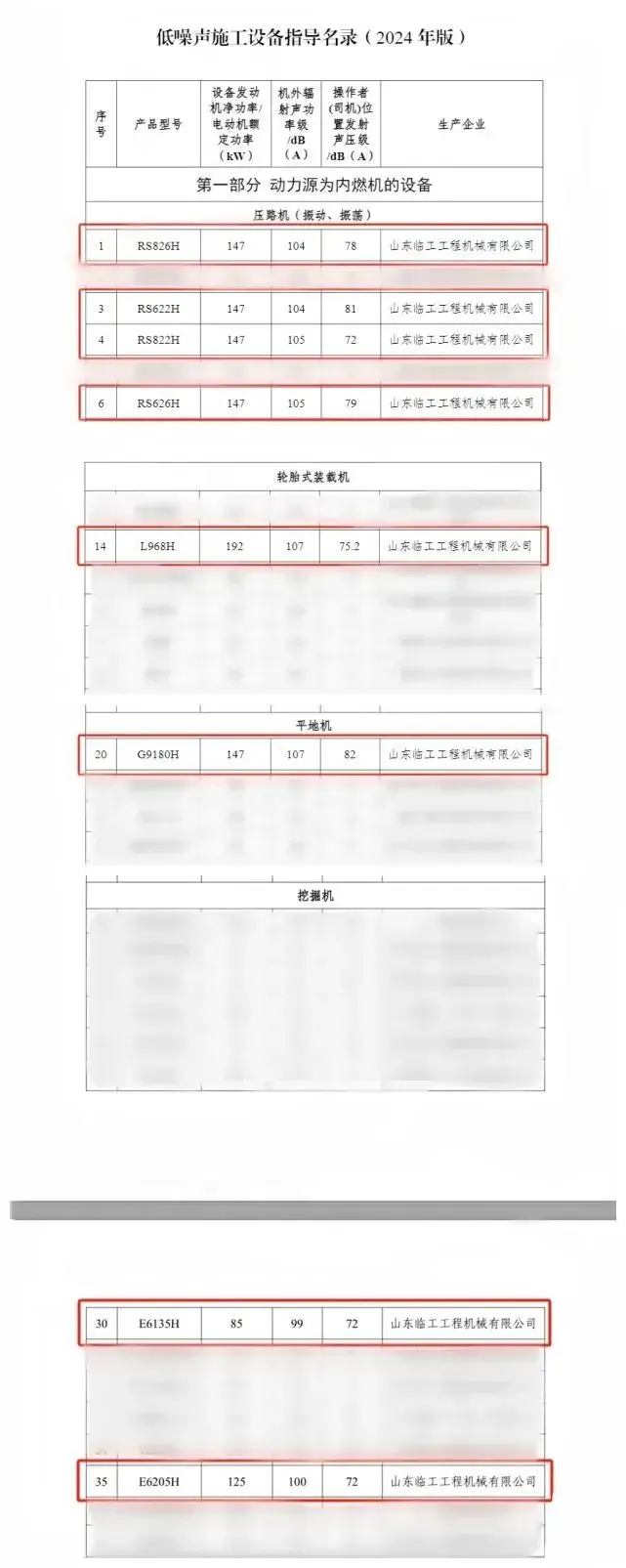
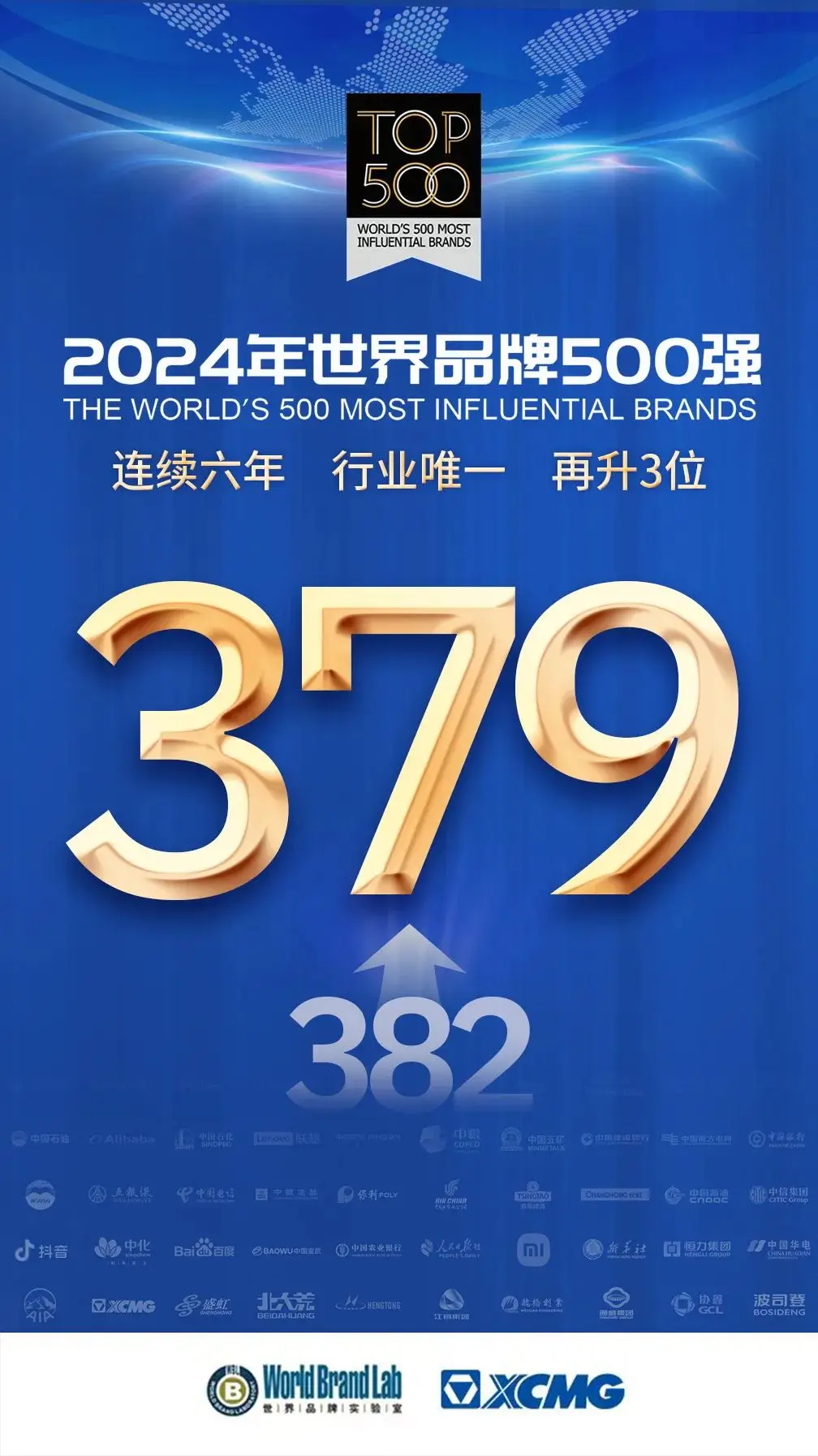
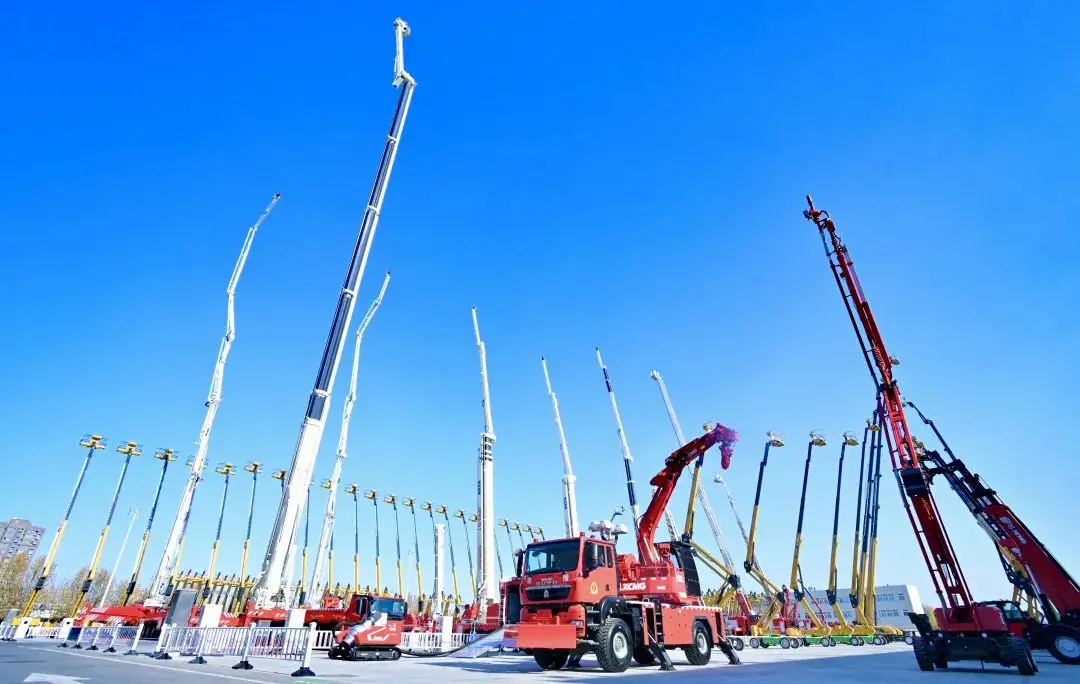
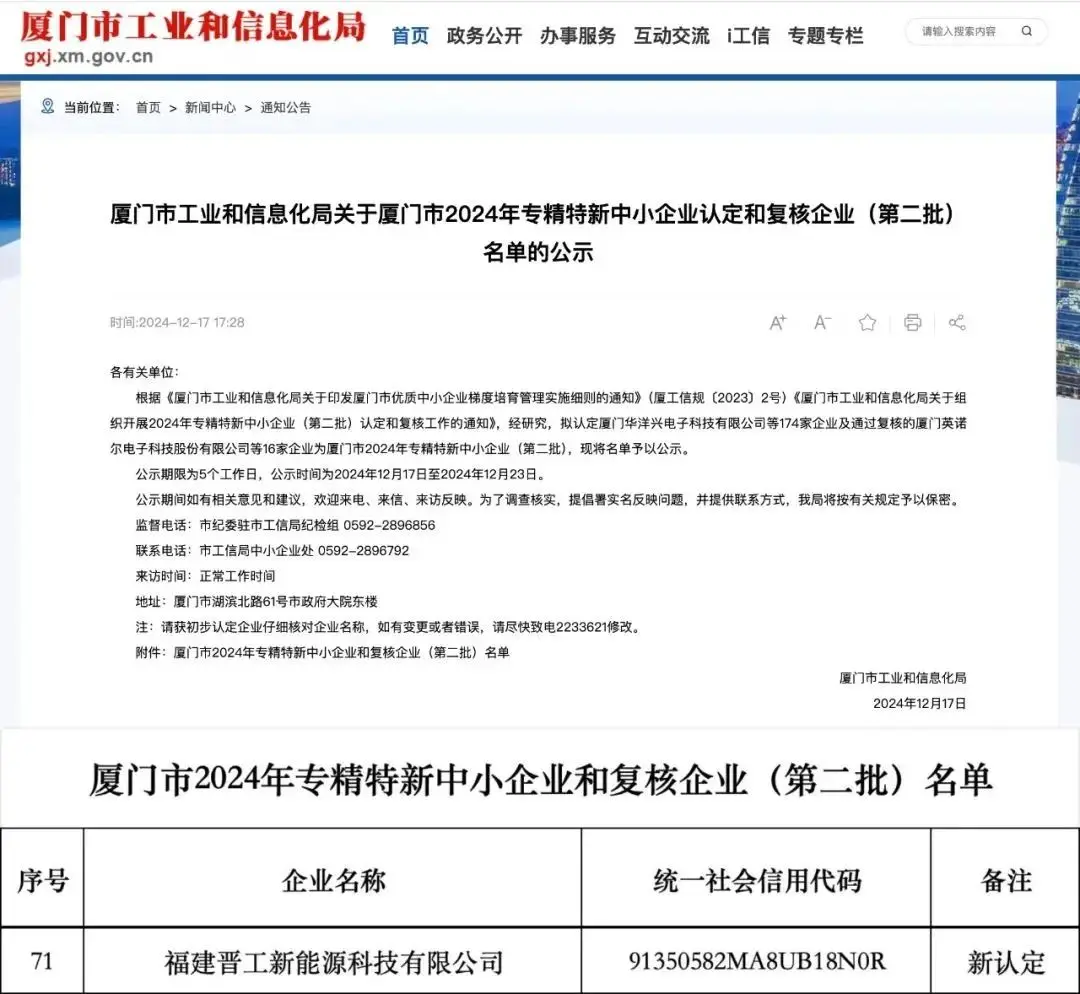
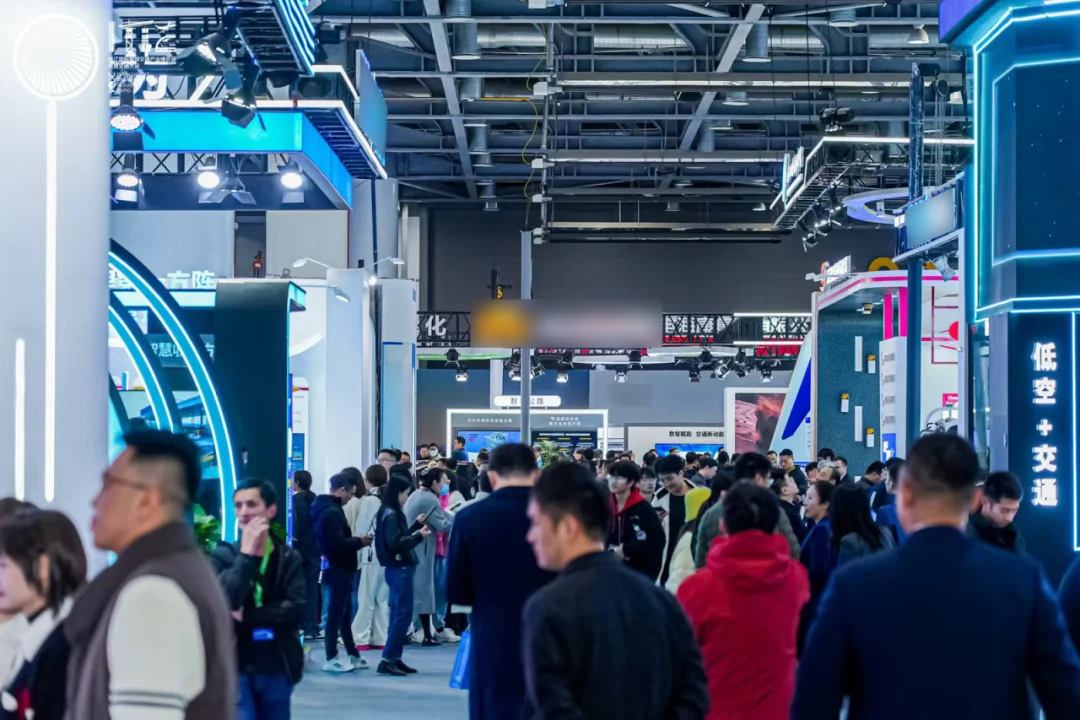
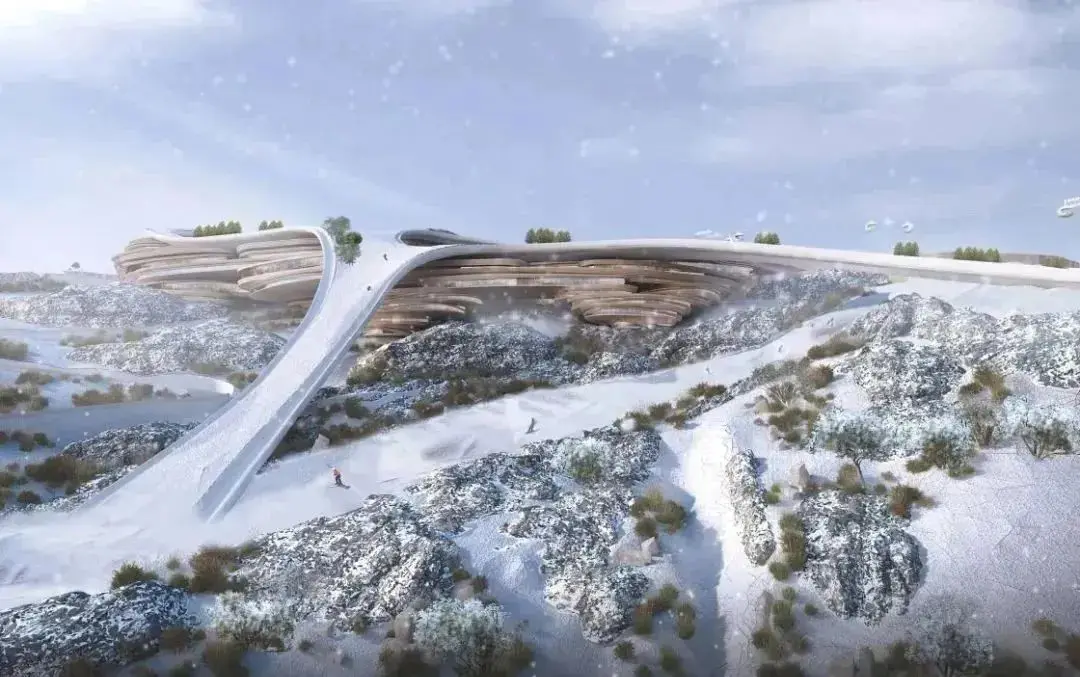
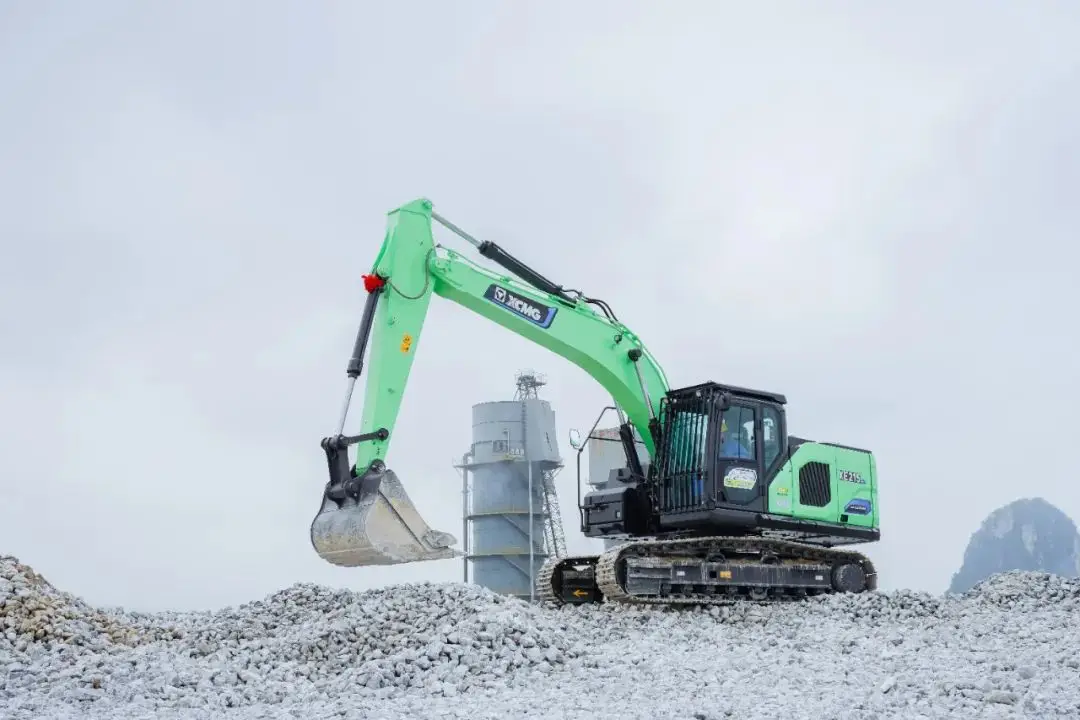
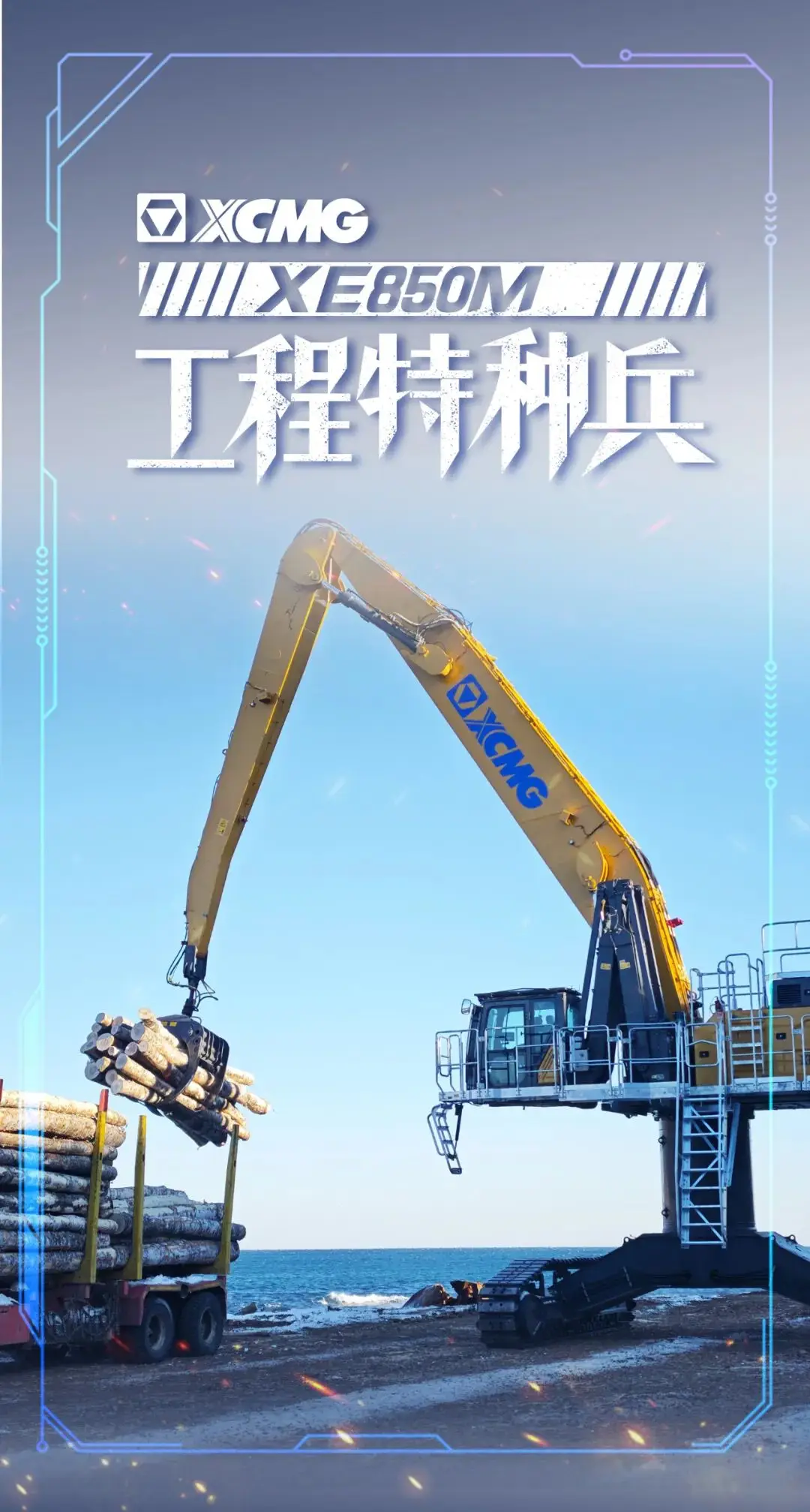
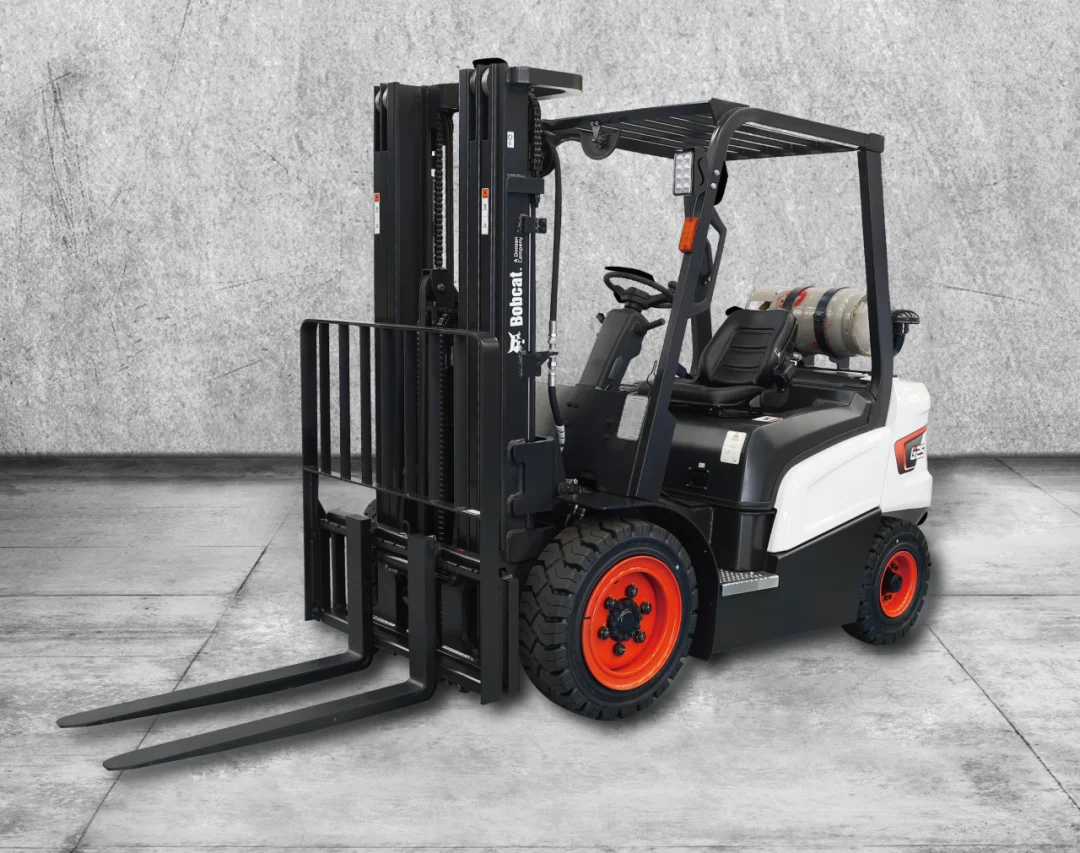
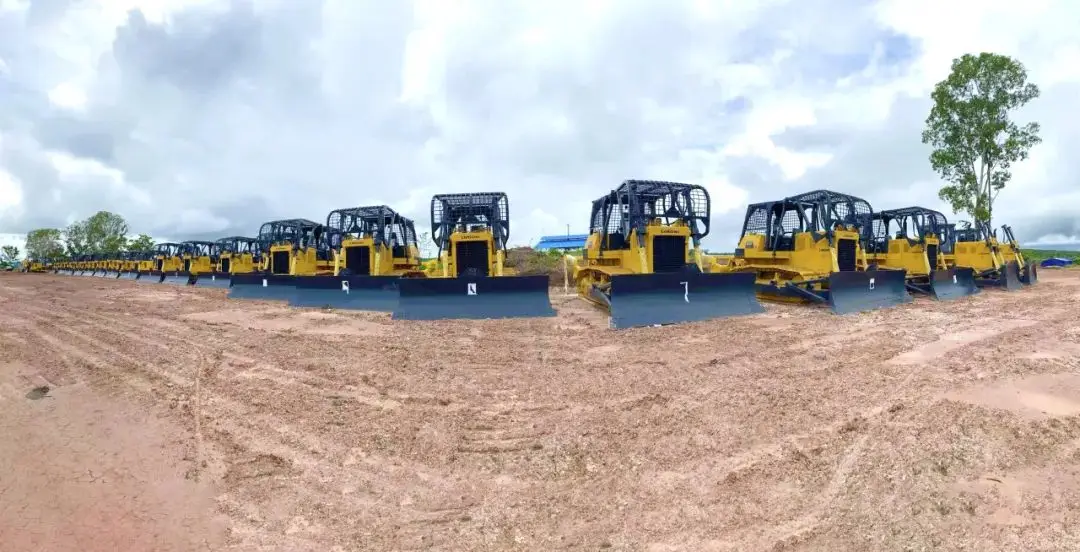

期待你的精彩评论