数字化 智能化 绿色化发展论坛高层对话之二
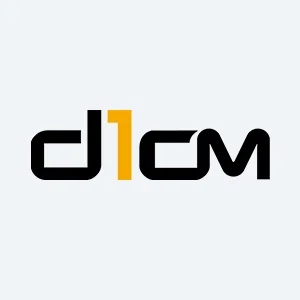
【第一工程机械网 现场报道】2013年11月28日,中国工程机械工业协会四届三次会员代表大会暨第十二届中国工程机械发展高层论坛在山东临沂召开。国务院国资委行业办副主任张涛,临沂市市委常委、常务副市长左沛廷,临沂市人大常委会副主任、临沂经济技术开发区党工委书记徐福田,中国工程机械工业协会会长祁俊,副会长兼秘书长苏子孟出席会议。协会副会长、常务理事、理事单位负责人,所属各专业分支机构负责人以及来自工程
【第一工程机械网 现场报道】2013年11月28日,中国工程机械工业协会四届三次会员代表大会暨第十二届中国工程机械发展高层论坛在山东临沂召开。国务院国资委行业办副主任张涛,临沂市市委常委、常务副市长左沛廷,临沂市人大常委会副主任、临沂经济技术开发区党工委书记徐福田,中国工程机械工业协会会长祁俊,副会长兼秘书长苏子孟出席会议。协会副会长、常务理事、理事单位负责人,所属各专业分支机构负责人以及来自工程机械行业部分会员单位的代表、各相关媒体代表近300人参加了本次会议。
2013年11月29日,在中国工程机械工业协会“第十二届工程机械发展高层论坛”期间举办了“数字化、智能化、绿色化发展论坛”。徐州工程机械集团有限公司副总裁李锁云、沃尔沃建筑设备(中国)有限公司副总裁王业峰、安徽合力股份有限公司部长谢云围绕工程机械行业“数字化、智能化、绿色化发展”发表了主旨演讲。行业重点企业广西柳工集团有限公司、天津工程机械研究院、方圆集团有限公司、机械工业第一设计研究院、日立建机(中国)有限公司、山东常林机械集团股份有限公司、川崎精密机械商贸(上海)有限公司、马鞍山方圆回转支承股份有限公司、长源液压股份有限公司、烟台艾迪液压科技有限公司的高层围绕论坛主题进行精彩对话。
以下是山东常林机械集团副总经理周明辉在“数字化、智能化、绿色化发展论坛”中精彩演讲实录:
我来自山东常林集团。下面,我把山东常林集团的情况简单介绍一下。近日山东常林在临沂完成了70周年的庆典。常林集团现在一共有四大板块,一是工程机械,一是农业机械,一是高精度铸造,一是高端液压。下面我结合今天的题目“智能化”和“绿色化”谈一谈这两年的工作。
山东常林集团在液压板块启动了一个项目叫做IVT变速箱,用于5吨装载机,它是液压和机械混合动力的变速箱,速比可以从0.6到无穷大连续不间断地换挡调整速度。这个变速箱的目标就是想替代现在用的液力变速箱,液力变速箱的效率比较低一些,为了提高效率以及环保,想用比较高效的代替相对低效的东西,常林集团想在这方面做一些尝试。这个变速箱是常林集团领导看到节能减排的压力比较大,看准这个方向让我们实施,最早想在国外引进,但是在国际上都处在研发阶段,基本上没怎么有。个别的有两三家一两家的也在实施阶段,一些数据我们拿不到,后来我们就自主研发,我们做的变速箱核心部分申请了一个专利产品,实现连续不间断的换挡。
常林集团也考虑控制模式,它肯定是自动控制的,不能用手动换,肯定要电控的,电控有两种方式来控制,一种是横功率的方式,当然跟油门踏板相关的横功率的控制,再就是横车速的控制。在横车速的情况下,踩到了一个油门,角度不变的话无论是上坡还是平地,车速都是不变的。横车速上坡可能会慢一点,平地可能会快一点。目前我们把这个产品的样机做出来了,有的液压件还没到位,目前我们还没有装在机器上去试,大约在明年把这个搞出来,让它在机器上跑一跑。在智能化方面,我们想让这个机器充分地试验,比如说跑1000小时、2000小时需要半年的时间,驾驶员可能比较累,我们准备往机器上搞远程驾驶或者是轨迹的自动驾驶都可能,跑的目标是试验这个车,但是我们可能会采用智能化的手段,要不然驾驶员一天开8小时也是很辛苦的事情。#d1cm#page#
以下是川崎精密机械商贸(上海)有限公司总经理陈爱民在“数字化、智能化、绿色化发展论坛”中精彩对话
各位领导,中午好。川崎液压件属于川崎重工七个子公司之一,公司从1916年开始生产液压件。川崎最早起步是在船用液压件,川崎液压件在全世界的船用液压件份额占到35%。第二块是产业机械上,产业机械到中国来得比较早,当年的宝钢和武钢轧机上用的液压件是川崎的。我们经常在中国目前出现的是工程机械。川崎生产液压件接近100年的历史,我们总部在日本的神户,在美国、英国、印度、韩国以及中国分别有制造工厂和销售公司、服务公司。我们在苏州2006年成立了独资子公司,2009年在国家政府、商务部国产化的要求下,川崎在工程机械行业协会以及挖掘机分会的领导和指导下,我们把技术转让给中国的春晖集团,川崎在春晖成立了一个合资公司。从某种意义上讲,我们在中国用的液压件说是日本的品牌实际上全是在中国春晖和川崎苏州工厂制造的。
我们讲到绿色和环保,再制造这一块川崎也下大力度做,2011年我们在上海成立了再制造和售后服务中心。今年7月份,我曾经陪着国家工程机械制造项目的各位领导去了美国公司看了一下怎么在美国跟卡特彼勒进行20年左右的液压再制造的工作。我就简单介绍这些情况。
川崎液压初入中国的情景
今天非常高兴的是刚才王院长说到了中国挖掘机的历史,我也有幸是一个见证者之一。1992年川崎来到中国的时候,中国有五大品牌挖掘机厂,他们的产量是国家配置的,生产出来的都是很畅销的。当时我们来介绍国际上川崎的液压系统时,大家一般不买。当时我们就讲到了节能,中国的挖掘机主要做功率控制,不做流量控制。功率控制的结果是什么?挖掘机无论开不工,只要发动机点火了,它就一直在烧,当时的说明书上建议,建议大家不要连续使用3小时或者5小时,当时我们介绍要进行流量控制。流量控制的目的是什么?当我使用它的时候,它会启动,当我不用它的时候,整个的流量会到最小,这是要做的事情。从1992年开始我们给大家介绍。五大品牌挖掘机逐渐比较少的原因有很多,有合资等等,有一个原因还是产品相对落后。大家后来为什么都买川崎的产品?有一个原因就是这个。
作为川崎的产品,中国的很多场合让我说川崎是不是生产的液压机都去供,我是反对的。为什么反对?人家可能说你卖东西为什么不想多卖?实际上挖掘机是耗费大量资金和能源的行业。我们秘书长让我在2008年行业说话的时候就曾经说过,大家都是重复建设,挖掘机行业就是重复建设,如果这样以后,整个行业是受不了的。为什么这么讲?我们又回到主题,川崎第一步是把负流量系统带进了中国,在流量控制上,中国的挖掘机基本上可以跟国外的品牌走入同一品牌。1995年我们开始把电控系统导入到中国,川崎的液压件都是量身定制,每家产品都是不一样的。你们如果到我们公司参观,光油泵的生产喷油盘这一个开口有上千种,整个大库上面都是。它的生产过程中,1980年我们就建成了全世界第一个全自动化生产线,从设计到出货是全电控生产出来的。如果没有这样做,做不成。
系统升级 绿色环保
我们进行了区别化生产的同时,电控实际上就是一个最后关键,电控都是川崎做的还是同质化生产,所以我们不建议做电控。1995年我们为什么带到中国?在竞争中,国内品牌无法跟国际品牌竞争,国际品牌是有电控的。电控的是需要多大功率就出多大排量,中国没有办法做。1995年我们首先把电控敞开给各个主机厂用,所以也就有了现在很多做挖掘机的电控系统,可以说雏形都是川崎的,这也很好。我们为什么没有独占这个?我们只做我们控制的这一块。
很多人跟我建议说你不要做那个了,找一个厂合作一下,你个人都发财了,现在做电控的很多是大老板。第二代电控进来的时候,我们隔了很多年没做,2005年又晋升到一个新的时代,所以我们有了电控的正流量,不是说川崎不拿这个技术进来,而是根据市场的需求跟大家合作开发新一代电控的正流量。电控系统对主机的贡献最少节能10%以上。这是我讲的系统方面,每家不一样。
再讲到川崎的泵,川崎的泵跟我们的老大哥各走一方,第一台循环泵是1968年出来的,刚出来的系统叫KV系统,1980年我们又出现AV系统,到1990年开始出现K3V、K5V、K7V、K8V,每三年都会有一个新的控制系统出来,现在的K7V和K8V跟最初的效能比提高70%以上。其他的泵可能停留在90年代,川崎的泵现在已经到了更高的年代,每一代不一样它都有变化。我曾经在一个展会上看到有人做我们这样的东西,他做得很新,我问他为什么要改,他不知道,他说我就这样做。实际上不是的,我们就是一个小小的动作使噪音降低了5个分贝,这个成果很不容易。我们有很大的试验厂,在那里面我们有360个角度无噪音室对发出噪音的每一点进行检测,这样才知道这样一个去掉有什么好处,降5个分贝有很大的贡献。我们是执行元件,我们要怎么样降噪和节省能源,这是泵的方面。
主阀上面产生的能耗主要是回流的背压,这个已经降低了40%。作为液压件的厂家,我们不断追求的就在这里。昨天领导也都介绍到混合动力,挖掘机的整个混合动力上有几个部分都可以做,一是回转,还有就是动力下降,以及在泵的后端电机什么的也在做,这些川崎都在做,我们可以降能耗25%。我们是跟着主机厂走的,有了他们的发展才有我们的发展。
在加工的过程中,在实验台上就进行了动力的回收,这个实验台可以把动力回收30%,这是一个主机厂必须要做的。因为我们是全自动化的生产线,我们有一套检测的系统,都有专利,我可以检测到电动机是不是在正常工作或者在休息,如果它不工作可以让整个系统全部停下来,这个技术在2011年商务部中日交流上谈到了。作为一个执行元件的厂家,川崎不断努力地朝前走,只要有了新的技术,苏州、春晖是同平台在工作,新技术会源源不断地介绍给客户。能看到挖掘机的发展,作为我们工作20多年的人是很开心的,大家会沿着数字化、智能化、绿色化发展走得越来越好。#d1cm#page#
以下是马鞍山方圆回转支承股份有限公司总经理鲍治国在“数字化、智能化、绿色化发展论坛”中精彩对话
各位同仁、媒体的朋友们,大家中午好。首先非常感谢行业协会给方圆支承包括我本人这么一个机会,可以在这里跟大家交流。方圆支承是一个很老的企业,往前面去追溯它是一个国有企业,建于一九六几年,我们开始做这个产品是从1983年。回转支承也是一个舶来品,国外有100多年的历史,我们有70年的历史差距。根据这些年的发展,方圆支承跟随着主机的发展提升也比较快。
我们的产品分为几类,有支承产品,还有液压杆产品,还有支承的前端等等。绿色化发展方面,我们最近做了涡轮增压器关键零部件子公司成立。它刚刚起步,销售收入占集团公司中5%以下,还没有形成一定的规模,后期可能是一个比较良好的产业方向。
前几年我们涉及到的领域比较多,前些年主要在工程机械方面,包括大家熟悉的挖掘机、起重机和泵车、混凝土。最近几年我们拓宽了市场,像风电领域、太阳能领域。
方圆支承数字化和绿色化体验
这一次的会议主题是数字化、绿色化、智能化发展,配套件我们是最终的执行部件,谈智能化确实远了一点,数字化和绿色发展在座的企业可能做得多一点,特别是数字化的研发和数字化的检测以及后面的数字化生产过程比较多一点。方圆支承在今年年初投入了数字化的检测试验中心,这对我们数字化的研发有一个很好的支撑。刚才日立的卢部长也提了,他把研发和检测试验融合在一起,方圆支承也是这么做的。从客户提出要求到数字化的建模和分析,最后出现一个理论化的设计结果,根据理论化的设计结果经过试验检测中心以及工况的检测,之后就会评数字检测技术能够得到真正使用工况的情况,特别是在新产品开发产品交付之前可能更清楚地告诉客户我这一块的使用寿命包括承载极限是多少,而且对今年上半年的业绩产生了较好的影响。
绿色化发展的消耗是不是很合适,你的设计是不是最优的,这是最主要的。我们在今年上半年根据这种研发和测试的流程,曾经优化了一块建筑塔式起重机,当时我们也没有很好地去研究它,也是一个借鉴,借鉴在什么地方?当时国外的一个客户给我们提出了在材质和加工工艺上的要求,然后我们跟中国通用产品进行比较,发现它确实不同。它对材质有要求,普通的建筑起重机在180-200的硬度,但是他提出要达到230-260,而且在后续加工那一段由以前的3个多毫米提升到5个多毫米,但是整个的设计结构很紧凑,整个材料节省能达到30%。今年上半年跟客户沟通以后,得到了客户的认可,现在已经进行批量生产。
数字化的研发和数字化的检测试验,可能是助推零部件企业今后发展的一个方向。
第二个方面是数字化的生产过程。目前支撑生产线的是5条,其中主要的生产工序有17道,其中15道工序是完全数字化的加工,包括数字化的反馈、存储、工艺的传输都是数字化的,有2条可能时间久一点,经过后期的改造,13道工序是数字化,其中还有4道工序还没有实现,后期进行逐步地提升。在加工过程中,我们特别对关键工序包括承载性能等明显关键的部分,我们在加工单元自主开发了加工工艺、实时检测扫描、存储的功能,它通过5-10秒钟的扫描存储作为基础档案保存3-5年,对于今后的工艺研究也带来很大的好处。
智能化。刚才几个主机厂提得比较多的是主机的智能化有待于执行构件智能化的提升。今年下半年我们通过跟高校进行了合作,特别是我们服务的超大型装备比如风电以及24小时不间断运转的领域,它要求实时检测和性能故障的传输。在这一块,我们通过检测实验室配备了一些机能,通过传感器能够检测到这些信号,能够和主机在中央处理器对接,带来的是远程对这个部件的实时监控,包括信息的搜集。#d1cm#page#
以下是长源液压股份有限公司总裁黄春江在“数字化、智能化、绿色化发展论坛”中精彩演讲实录:
我来自于长源液压。长源液压历史比较长,只是名字改了一下,以前是国有的合肥液压件厂,2003年改制变成了民营企业,我跟工程机械这个行业打交道比较多一些,时间比较长,产品线比较丰富一些,我们每年做动力产品、控制产品以及执行产品80万件,应用的面也比较广。结合今天这个会议的主题,我们在近两三年也在做这样的尝试和探索。
中国工程机械智能化水平还停留在探索和尝试阶段
大家都知道,中国的制造业也不是从今天开始提到这个事,中国的制造未来的发展一定是走绿色化、智能化这个大的方向。我们更多地做一些基础的工作,一是对内,二是对外。对内来说,主要是从材料的综合利用、油品的综合利用,包括设计阶段如何再制造,在信息化方面的投入比如说移动的客户关系管理、在线的智能化监测做符合方向性的投入,也是生存的需要。对外方面,我个人认为中国目前整个工程机械的主机相对来说智能化的水平还是停留在探索和尝试的阶段,真正产业化还非常少,还停留在概念的阶段。这么多年跟工程机械打交道,在整个价值链上实现了联动,主机厂的任何想法和期望都会和供应商共同合作,就是刚才卢部长所说的,其实现在就是这么一种关系。我认为中国目前急需做而且容易成功的有两个方面,就我们的行业和产品来说,一方面我们要做节能,节能和降耗可能是一个重点。为此,我们跟一些主机厂合作,也取得了一些相关的成果,一些主机上能够实现25%-35%,至少两三个行业已经实现了,他跟我们配合,我们给他提供这样的液压产品。我们有一款产品是齿轮泵,齿轮泵有噪音的问题,我们在降噪方面得到大幅的控制,尤其像室内操作的这些行业产品得到了提高。
通过这几年在绿色化智能化方面的投入,不管是从技术改造还是从管理能力上的一些投入,应该说都取得了一些效果,我们感觉到得到了内涵的增长。
我国液压件依赖进口
中国的基础件尤其是液压件是中国制造业的一个痛,痛了很多年,这方面的话题非常多,我个人认为这里面有多种原因,液压件行业属于资本密集、技术密集以及跨学科,的确非常难做,尤其是做高端的液压产品。这里面行业呼吁了,国家也给了一些指导性的意见,说要振兴基础件、主机与配套件同步发展,但是我个人认为力度还不够。国外的液压产品在中国畅销了很多年,中国已经成为全球最大的市场,我们中国的主机有没有想过,我们给他们提供了多少改进、更新、完善、创新的机会,我们给本土企业多少这样的机会。
前几年以挖机为代表的高端液压机的本土化投资越来越大,大家都在关注为什么投资这么多,为什么大家都蜂拥而上,可能看中的是国外产品在中国的利润。这个投资有问题的同时,有没有一个具体的措施去规划一下,怎么样让这个行业既能健康发展,又能实现整个中国在高端产品、高端主机上整个价值链的提高?你做得再大,里面的核心零部件全是国外的,我们能赚几个钱?这是我认为的第一个问题,这个问题是根源问题。我在私下里跟一些同行做交流的时候说,我们抓液压件要像抓军工一样抓,要不计代价地短时间做上去,让它自由发展会很多年,国外的发展已经比你有很多优势和有利的环境,市场占有率已经这么大了。这是从宏观环境上来说能够有这样的机会。
第二从自身的制造厂家来说。液压件的厂家的确要耐得住寂寞,很多产品的不完善,包括不是高端产品质量问题上不去,其实仔细分析原因的话,可能有80%的原因是非主项因素。有些部分质量可能还过剩,有的研发条件可能还过剩,更多地停留在我们不关注的地方,比如毛刺和清洁度,它恰恰是最重要的。
长源液压精细净的生产文化
我们公司正在推行这样的技术管理,也就是说要导入精细净的生产文化。“精”是精准,精准一般能达到,很多企业不是自制的,有部分是协作的,这种协作能不能完全地在大量订单在的时候处理好这种交货期跟质量控制门槛的关系?我要求精准,你差一点就不行,只要我认为设计是对的,不能绿色放行,不能签字做例外,否则产品怎么能上去?大部分产品精细的文化的确没有形成。“细”是细节,细节决定成败的确不假。我们在现场很多地方随便一看,很多优秀的企业很多细节还有不到位的地方,这就是跟国外先进同行的差距。“净”就是清洁度,包括对毛刺的抓,这是投入很大短期不容易见效的。我们统计了一下,有些主机上的故障,其实有些行业在70%以上是由于清洁度不行造成的。现在工业车辆行业已经在推行抓清洁度,效果很显著,它分了几个阶段,系统运行一段时间之后查清洁度第一级目标要达到11级,第二级目标要达到9级。作为我们来说,精细净的文化应该导入基础的管理。#d1cm#page#
配套件跟主机的协同发展
怎么样跟主机厂去协同?我个人有一个体会,以前我们学开车的时候师傅会教你如果要开好车,不能光盯着眼前这部车,你要看前面的那辆车。我们跟主机的关系也是这样,以前主机是皮,配套件是毛,皮是在毛上的,主机厂有什么要求配套件马上去执行,我们逐渐地在改变,这样是不行的,我们要关注主机的发展以及最终客户的感受是什么样的要求,这样才能真正理解主机的发展。这次十八届三中全会更明确提出市场为导向,很多创新包括一些想法,以前的的确确有的是停留在形式上、走秀上或者争取国家政策上,这一次我觉得很振奋,大家可能更关注市场的需求,一切以市场为导向。配套件和主机共同关注终端市场,对未来市场的把握一定是精准的。
要实行同步的开发,这一点我们很受益。我们为叉车行业做的一些智能化的产品,比如说OPS就是操作手主动感应系统,在人离开座椅的时候它就停下来不能动,还有SAS这个系统,后轮的摆动包括全液压转向的控制,其实都是要靠液压的最终执行去实现的。昨天谈到挖掘机的转向节能,在势能方面能量是非常浪费的,它的机型节能能达到30%,个别节能能达到50%。
总的来说,配套件跟主机的协同应该共同努力,还要有好的环境。#d1cm#page#
以下是烟台艾迪液压科技有限公司董事长宋飞在“数字化、智能化、绿色化发展论坛”中精彩演讲实录:
大家中午好。烟台艾迪主要有两种产品,一种是液压属具,另一种是液压件。液压属具是从2003年开始生产,我们经过这十年的生产,在这个行业基本上得到了一定的发展,目前每年的产能达到5000到6000台,今年已经过了7000台,50%销售在国内,50%销售在国外。还有液压剪、液压钳包括平地机还处于发展阶段,还没有形成主流,在中国的使用环境还没有完全达到,但是这些我们已经能生产这些产品。
艾迪液压的发展历程
关于液压件,这个历史就比较长一些。1995年到1996年开始。在这个过程中我一直关注液压件,我在日本、韩国、美国很多地区都关注这个事情。一直到2000年左右,我的零部件销售在中国量很大,已经过亿。在那个时间,我就观察到液压件应该有比较好的未来,从2000年开始我们就有一个团队一直做技术的准备,一直准备到2009年,在这个过程中,要做这个事情是很难的,因为我们有方方面面的困难,包括资金方面的、技术方面的。2003年开始做液压锤的时间,我们赚到了第一桶金,2009年我们做了液压件,这个团队准备了接近10年的时间。开始生产的这个过程也是比较曲折的,技术、生产和环境方面有很多困难。我们当时设计这个工厂的时间是按着2万台液压系统的泵、阀、马达设计的。
我们设计这个工厂的时候主要是考虑配套的,但是设计完以后发现没人相信你。我们在开始生产的初期,生产液压件要考察铸造件的问题,我们考察中国没有这个条件,我们又建了铸造工厂,中国的铸造工艺各个方面达不到,从国外找专家陆陆续续把铸造建立起来了,在铸造件行业,我们跟挖掘机的知名品牌搞铸造件的合作。我们在采购设备过程中,我们发现中国采购同样的设备,也要做,后来发现不是每个人都成功,很多人停止了。我们每个月投产的液压泵从5吨液压机用的泵到40吨挖掘机用的泵一个月产1000台左右,这其中95%投入到再制造和售后服务市场,其中有5%做试验,跟一些小型厂或者是非主流的单位做测试,包括我们自己也在做测试。虽然你要做这个事情,要有一个过程,再制造和售后服务的过程中我们发现问题及时地去更改和学习,现在信心越来越强。谢谢大家。
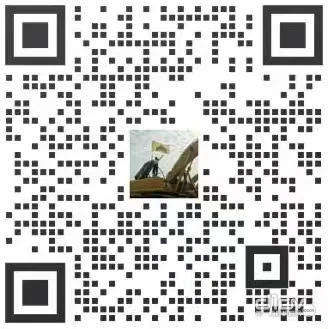
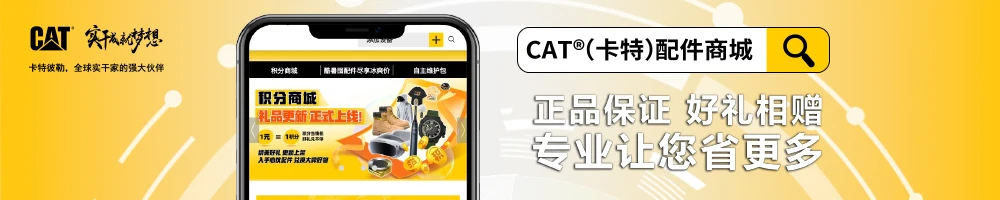
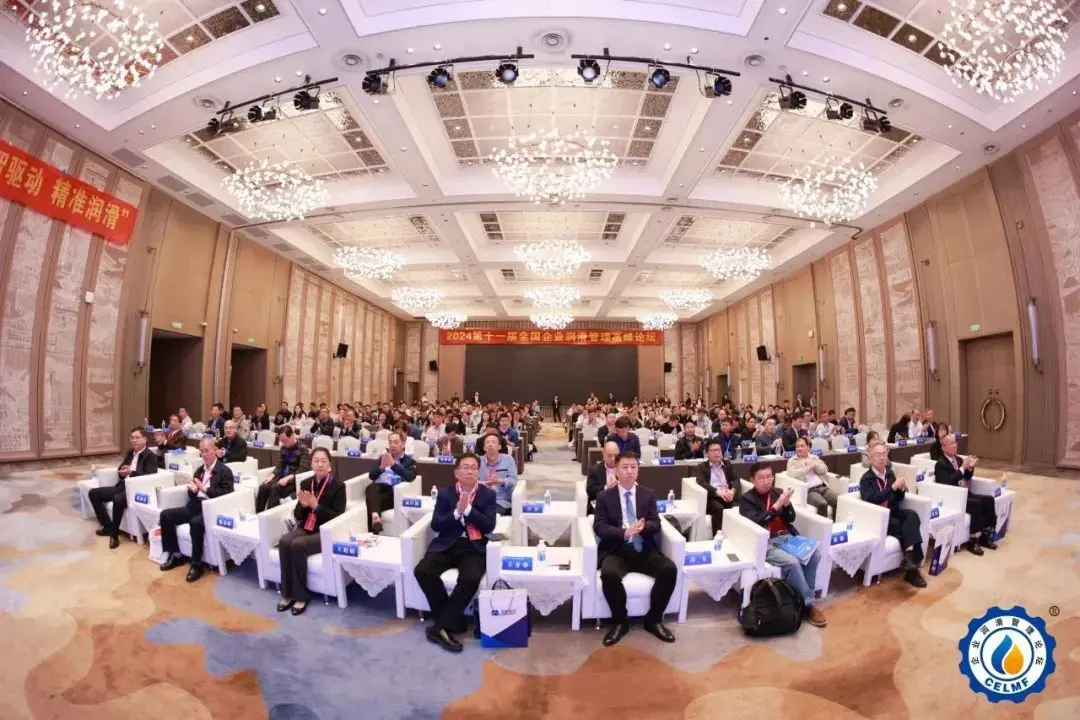
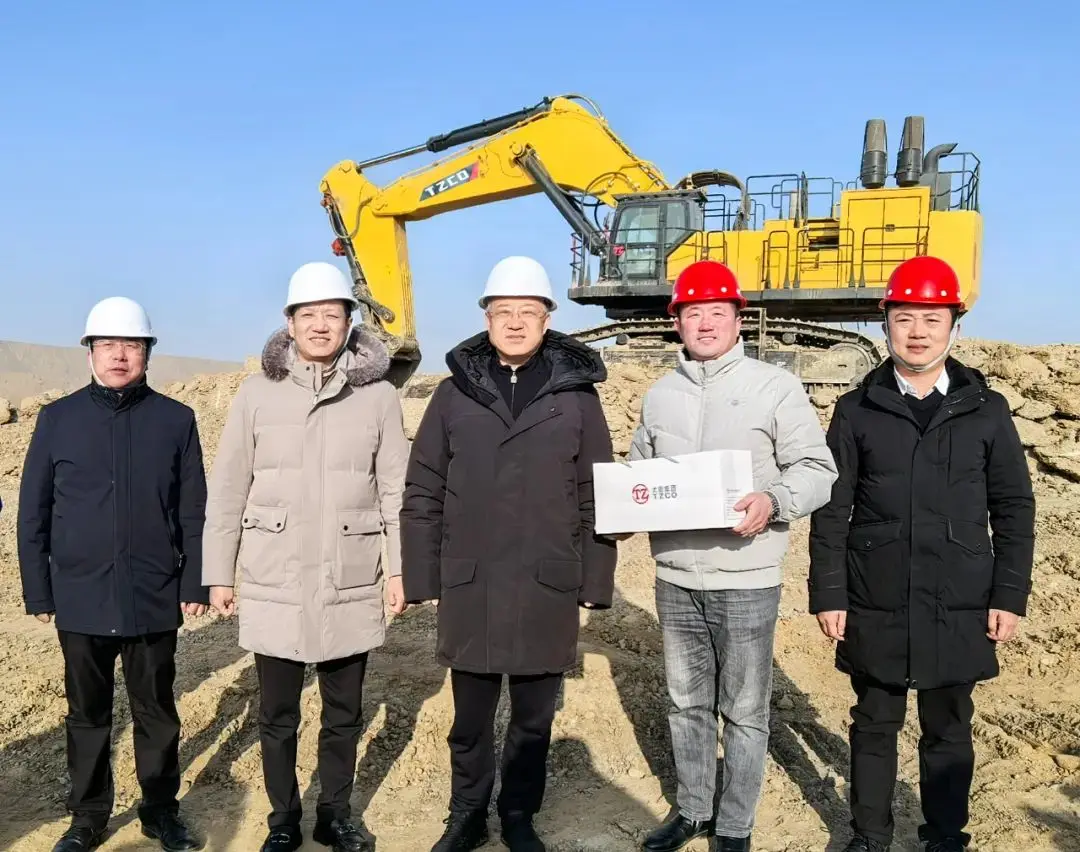
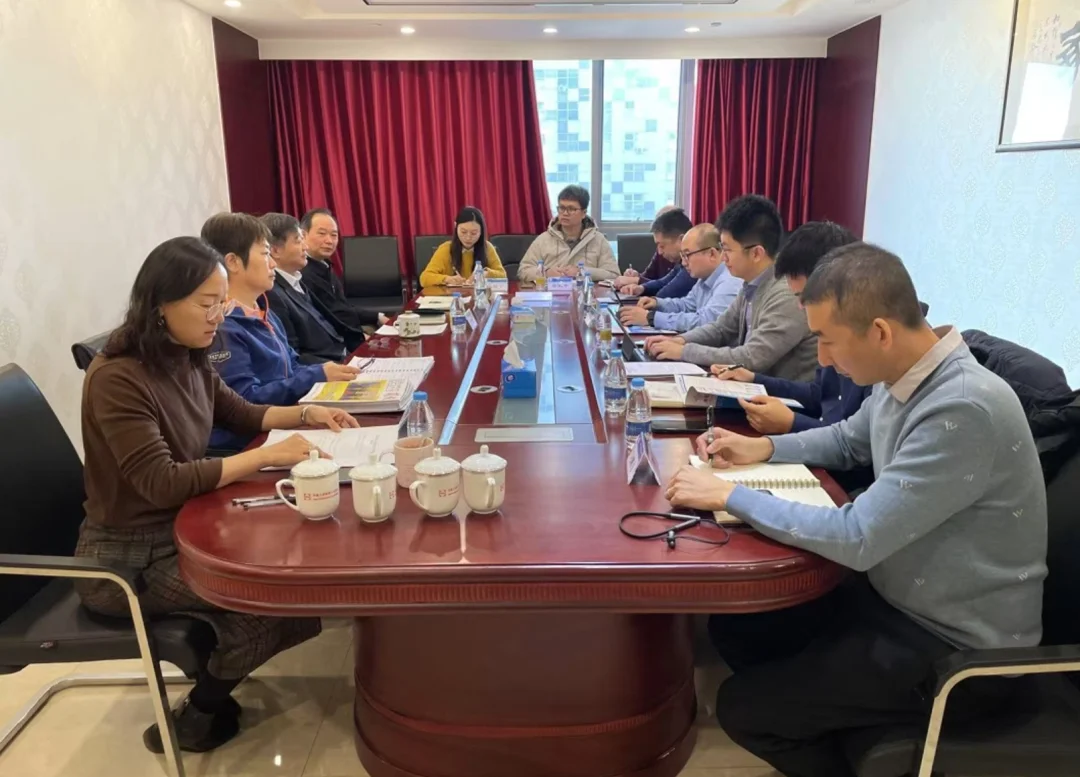
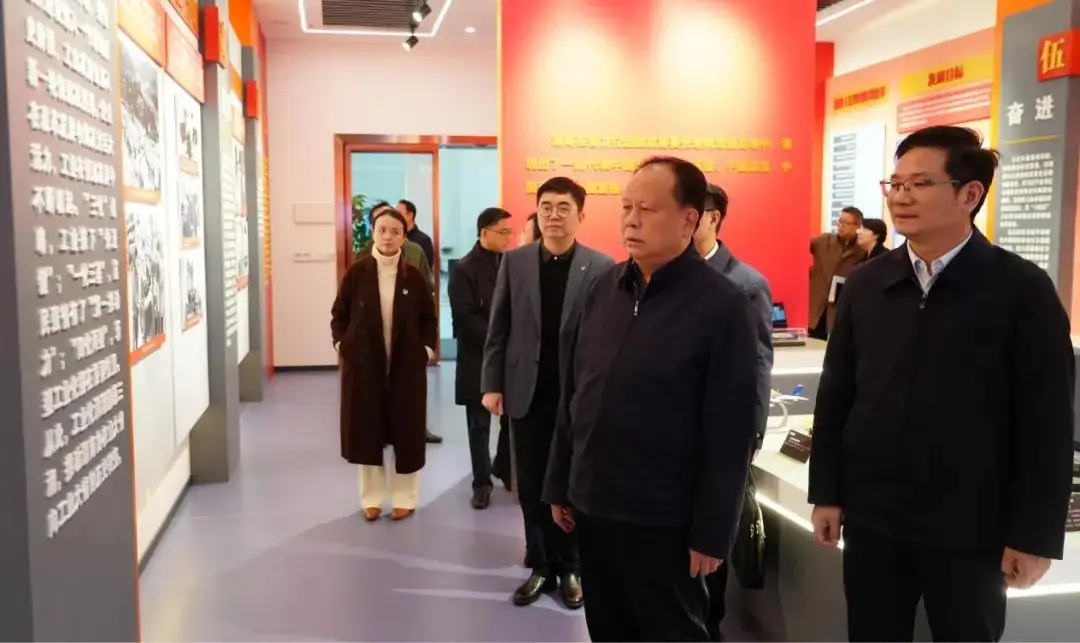
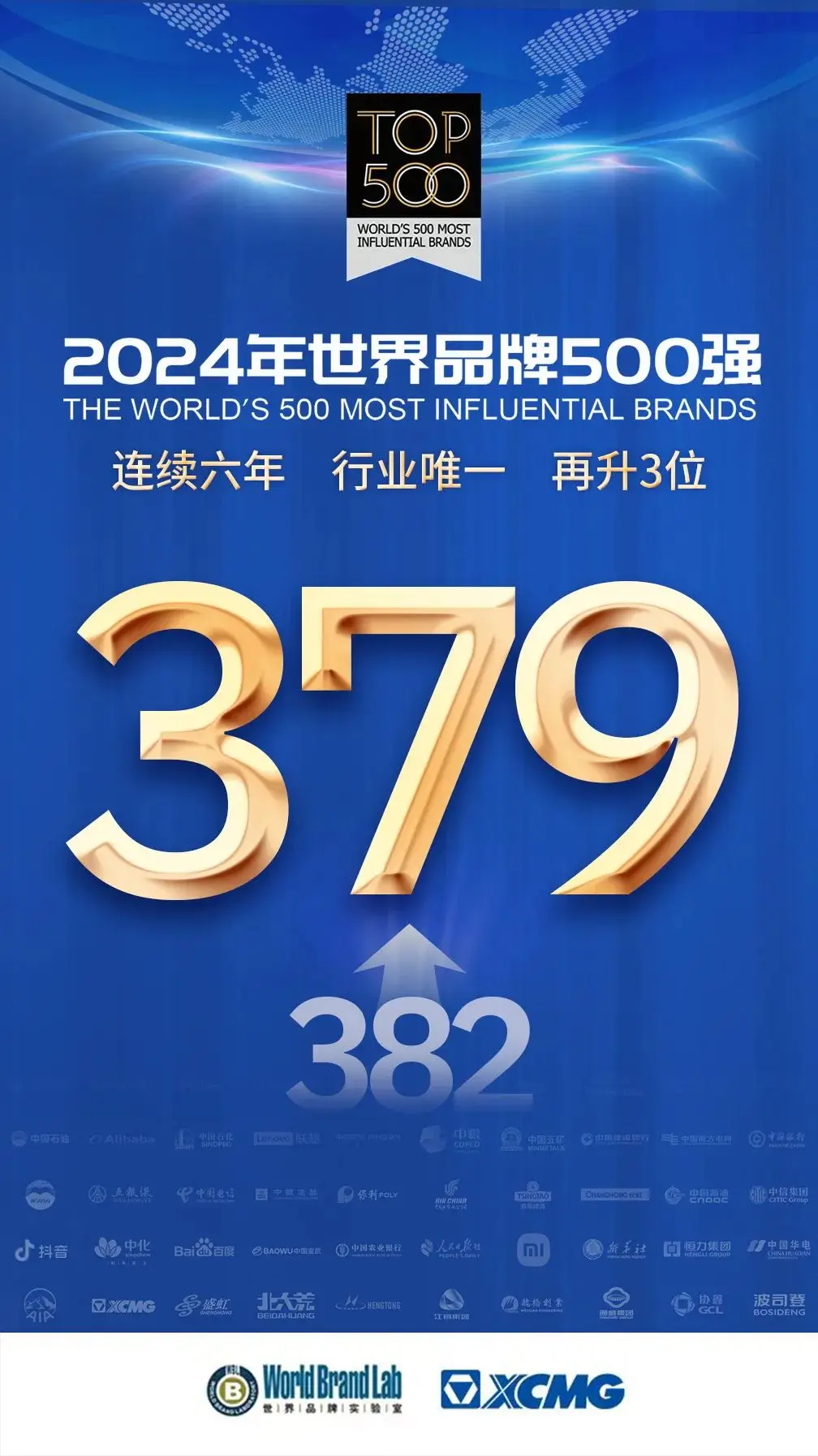
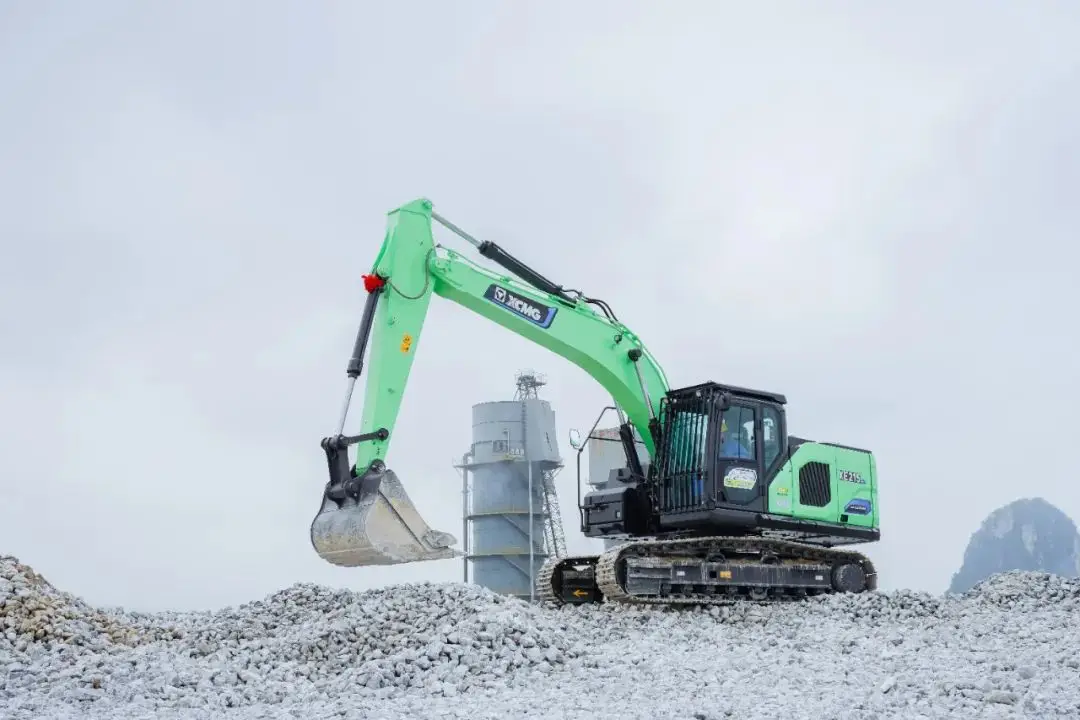
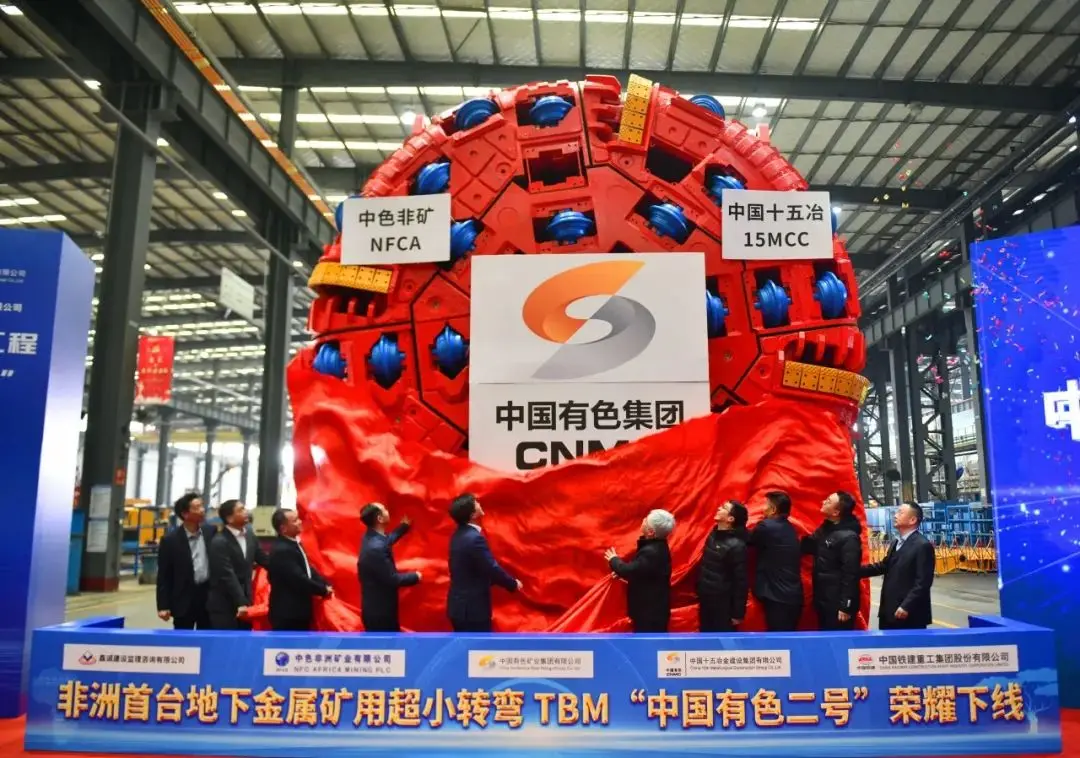
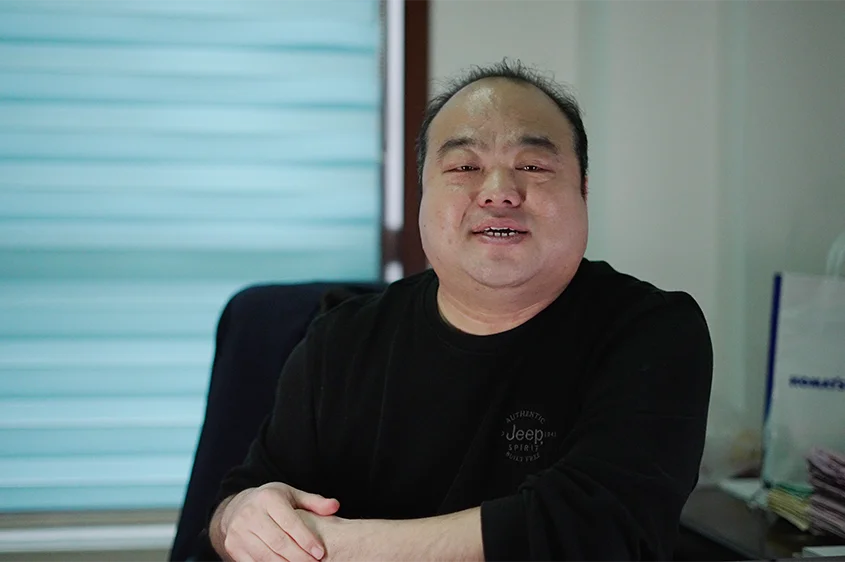
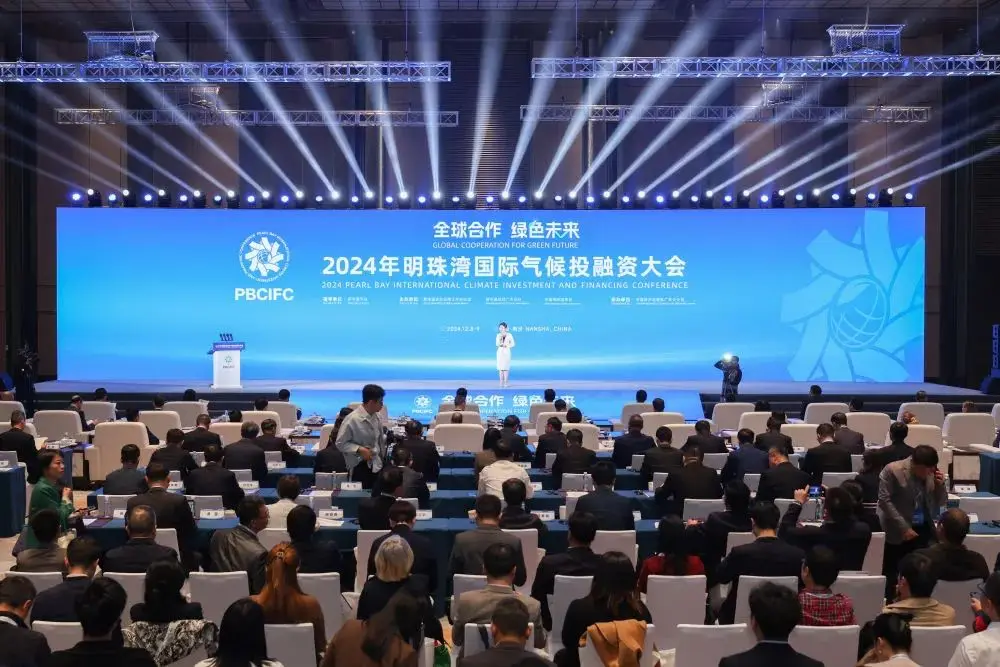
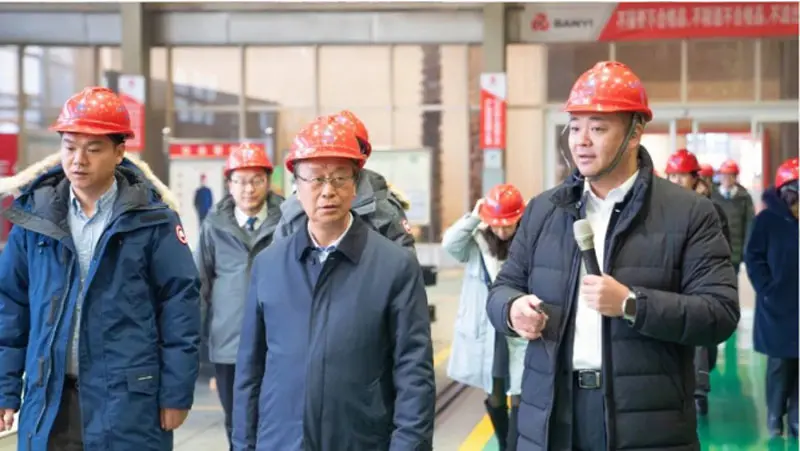
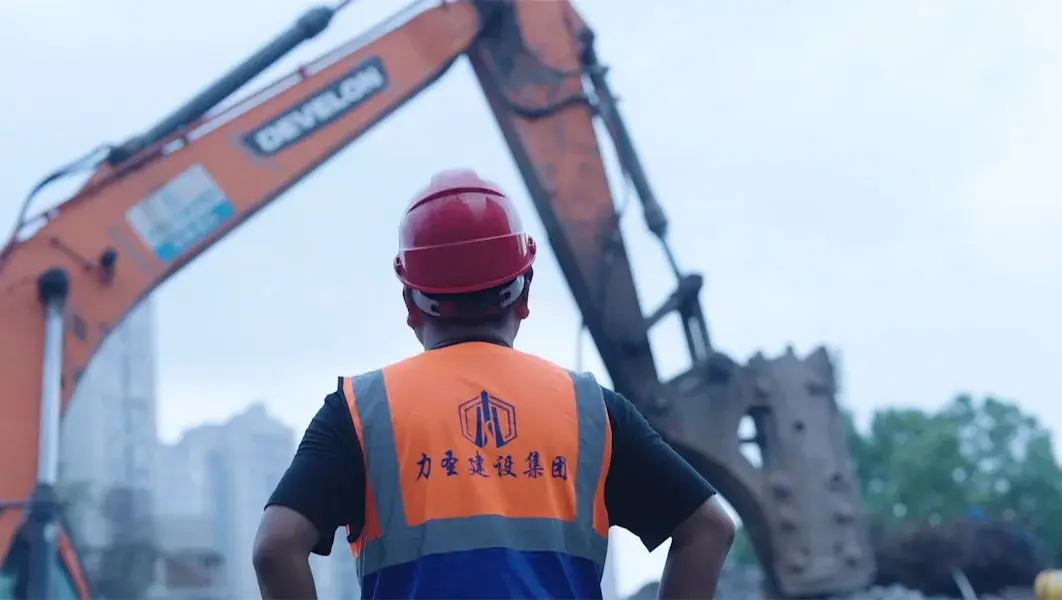

期待你的精彩评论