我国机械再制造产业:仍具有巨大的提升空间
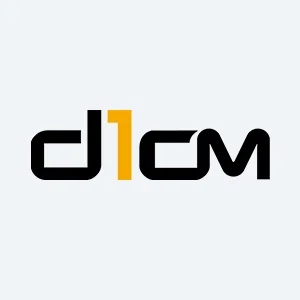
9月16日,北京西五环外,中国人民解放军装甲兵工程学院机械产品再制造国家工程中心迎来了一大批客人。展厅里,各种汽车、坦克、飞机的发动机逐一陈列,我国再制造领域“领军人物”——82岁的徐滨士院士声如洪钟:“这是坦克发动机,500多小时就要大修,我们找出它的16个短板,采用不同工艺予以强化,经过1100小时的台架试验,工艺水平、污染物排放、燃油都在指标范围之内,效益非常明显。”10年前,徐滨士开始倡导
9月16日,北京西五环外,中国人民解放军装甲兵工程学院机械产品再制造国家工程中心迎来了一大批客人。
展厅里,各种汽车、坦克、飞机的发动机逐一陈列,我国再制造领域“领军人物”——82岁的徐滨士院士声如洪钟:“这是坦克发动机,500多小时就要大修,我们找出它的16个短板,采用不同工艺予以强化,经过1100小时的台架试验,工艺水平、污染物排放、燃油都在指标范围之内,效益非常明显。”
10年前,徐滨士开始倡导再制造产业的发展,将这些技术从国防军事领域延伸到民用等更广泛的领域。
机械产品再制造国家工程中心副主任蔡志海在接受记者采访时表示,再制造是一种对废旧产品实施高技术修复和改造的产业,通过对损坏或待报废的零部件进行再制造加工,使再制造产品质量达到或超过新品。与制造新品相比,再制造可节省成本50%,节能60%,节材70%,减排80%。
但目前来看,再制造产品的市场认可度还不高。对此,蔡志海表示,解决这一问题,“主要是要加大宣传力度,在销售网络和终端用户范围内推广普及再制造产品的知识。要结合资源节约、发展循环经济和建设节约型社会的系列活动,用生动事例宣传再制造在建设节约型社会中的地位和作用,正确引导社会各界尤其是领导干部、新闻媒体对再制造的认识,宣传再制造产品等同于新品,鼓励消费者使用再制造产品。按照法律要求,各级政府机关要带头采用再制造产品,为公众做表率。相关大专院校要开设再制造方面的课程或学术讲座。”
在机械产品再制造国家工程中心门前广场,十多辆再制造汽车从北京出发,目的地是拉萨,通过5000公里行程,实地测试汽车零部件再制造产品各方面性能指标。
中国国际贸易促进委员会汽车行业分会会长助理杨士敏在接受记者采访时强调:“此次再制造‘北京—西藏行’活动,就是为了提高市场认可度。从国家层面上进行宣传,赢得对再制造产品的支持,打消大家对再制造产品的顾虑。同时,通过再制造产品的展览展示以及再制造渠道的建立,提高公众对再制造的认识水平,推动整个产业发展。”
车队中,一辆重达十多吨的红色重汽豪泺最为惹眼。车厢里还陈列着两台再制造发动机。济南富强动力有限公司的销售总监白旭明告诉记者,这两台都是再制造的发动机。在目前国家推出的“以旧换再”政策之下,消费者购买每台车,政府都会补贴近2000元。再加上旧机折算的1万多元,相关政策对再制造产品销售会有直接拉动。
9月19日,途经河北邯郸、河南郑州,行驶1210公里后,车队安全到达陕西西安。在陕西省政府门前的广场上,朦朦细雨给围成弧形的车队洗尘,广场上的喷泉、成群的鸽子和再制造的车队交相辉映,构成了一幅美丽的画卷。
车辆行驶3天,谈起驾驶再制造汽车的感受,驾驶长城哈弗H6的一号车司机李敬表示,“目前看来,再制造车辆行驶过程中与新车并无大的差异,高速公路行驶中油耗每百公里低于7升。”
在西安举行的圆桌会议上,机械产品再制造国家工程研究中心总工程师张平、上海新孚美变速箱技术服务有限公司总经理迟永波、中国重型汽车集团有限公司总经理助理、济南复强动力有限公司销售总监白旭明、上汽集团上海幸福瑞贝德动力总成有限公司销售经理朱冬华、康明斯(襄樊)机加工有限公司再制造新业务发展经理胥晶晶以及中国汽车工业协会汽车零部件再制造分会秘书长谢建军以对话的形式,就再制造产业发展、再制造产品质量的检测和分级等问题进行深入交流。
会上,最受关注的问题是再制造产品质量分级制度。朱冬华提出,以目前我国再制造产品实际发展情况来看,是否可以对再制造产品质量进行分级处理。比如一台车只剩10万公里即将报废,这个时候使用再制造发动机,质量、性能及售后服务却都与新品相同,可能会造成浪费。
胥晶晶表示,在我国,再制造技术和产品刚刚进入初步发展阶段。这个阶段中,最重要的是让消费者对再制造产品产生足够满意和信任,使再制造产品在消费者心中树立良好可靠的形象。所以,为了再制造产品的品牌和整个产业的长久发展,首先要保证质量。在产业发展进入成熟期后,质量分级制也可以作为一种探索的选择。
针对再制造产业的未来,张平在接受记者采访时表示“前景光明”。随着我国汽车保有量的增加,大量汽车步入大修阶段,也到了必须要考虑大力发展再制造产业的阶段。对此,白旭明提出,“要让中国汽车大修成为历史”。这一美好愿景得到参会人员的一致赞同。#d1cm#page#
国家发展改革委环资司循环经济处副处长幺新表示,我国再制造产品具有鲜明的中国技术特色,以表面工程技术为支撑,同时融合了国际上通用的尺寸修理和换件修理方法,中国的再制造产品打上了深深的中国烙印。
蔡志海表示,我国再制造产业与国外相比还有很大提升空间:
一是实施再制造的质量控制体系尚未建立。企业没有充分认识到再制造对象和过程的复杂性,大部分企业在旧件检测、再制造毛坯修复等关键环节没有建立相应的质量控制体系,缺乏废旧零部件质量检测和寿命评估技术,难以保证再制造产品的质量和可靠性。
二是缺乏先进的再制造技术,旧件毛坯再制造率低。大部分再制造企业主要还是采用换件法和尺寸修理法进行再制造,对产品的再制造加工还处于低水平,导致再制造后产品非标件多,用户认可程度低,加工成本高,旧件毛坯再制造率低。最为突出的是缺乏先进的表面工程新技术,大量磨损的关键零部件无法修复,再制造产品的旧件再制造率低。
三是各企业之间互相压价,存在无序竞争现象,致使产品利润日渐降低。同时部分小企业采用价格低廉、质量难以保证的零部件,并采用贴牌大厂产品标识、假冒大厂再制造产品或新研发产品,导致再制造产品质量难以保证。各企业生产规模相差较大,导致生产设备和生产工艺良莠不齐,工人技能和管理理念相差较大,这也是难以保证再制造产品质量的原因之一。
虽然我国再制造进入产业化发展阶段还不到10年,但国家的政策扶持却非常给力。2005年,国务院发文支持再制造产业发展;2009年《循环经济法》明确了再制造产业的法律地位;2011年国务院把再制造产业正式纳入战略性新兴产业行列。不过,再制造发展过程中仍有一些亟待解决的问题。
幺新表示,目前我国再制造产业受到消费理念、消费者接受程度、市场体系和监管政策不健全等因素影响,发展受到一定阻碍。
张平在接受记者采访时表示,要逐步完善标准体系。比如,再制造厂家可根据自身情况建立企业标准,再通过多厂家联合建立行业标准,最后逐渐建立推广国家标准。目前,企业对于深层次的质量把控还没有具体标准。
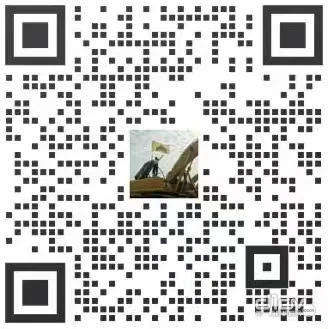
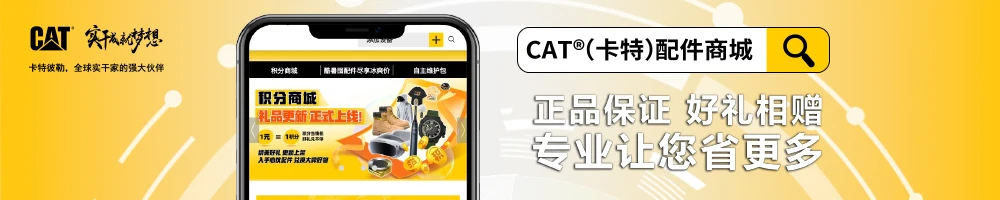
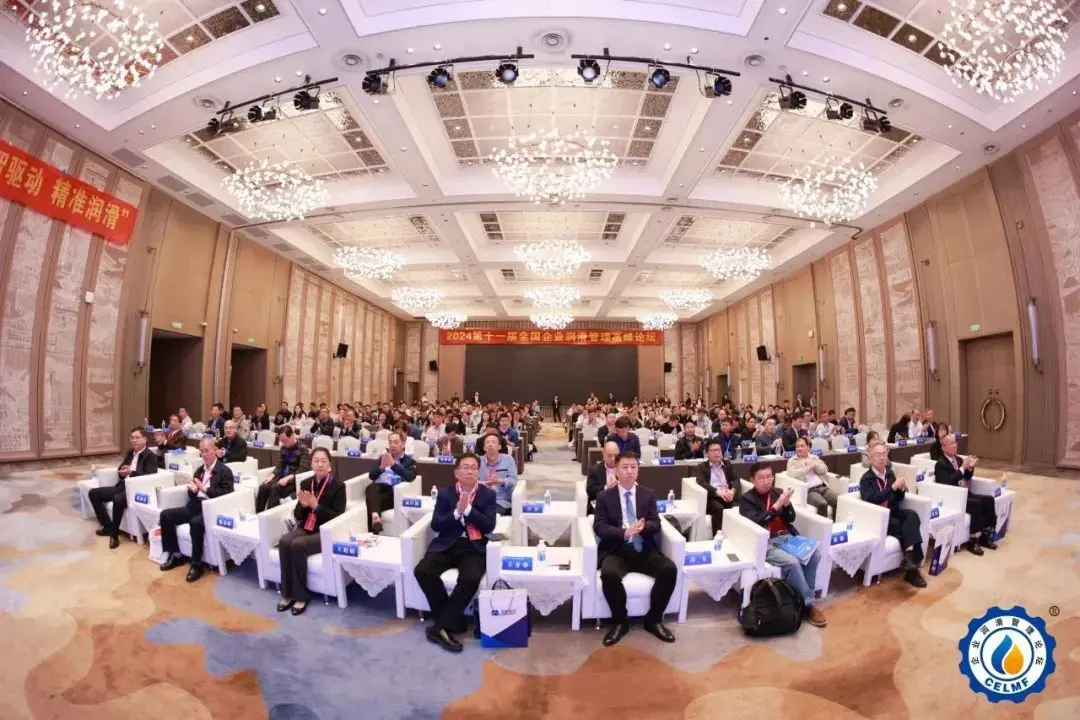
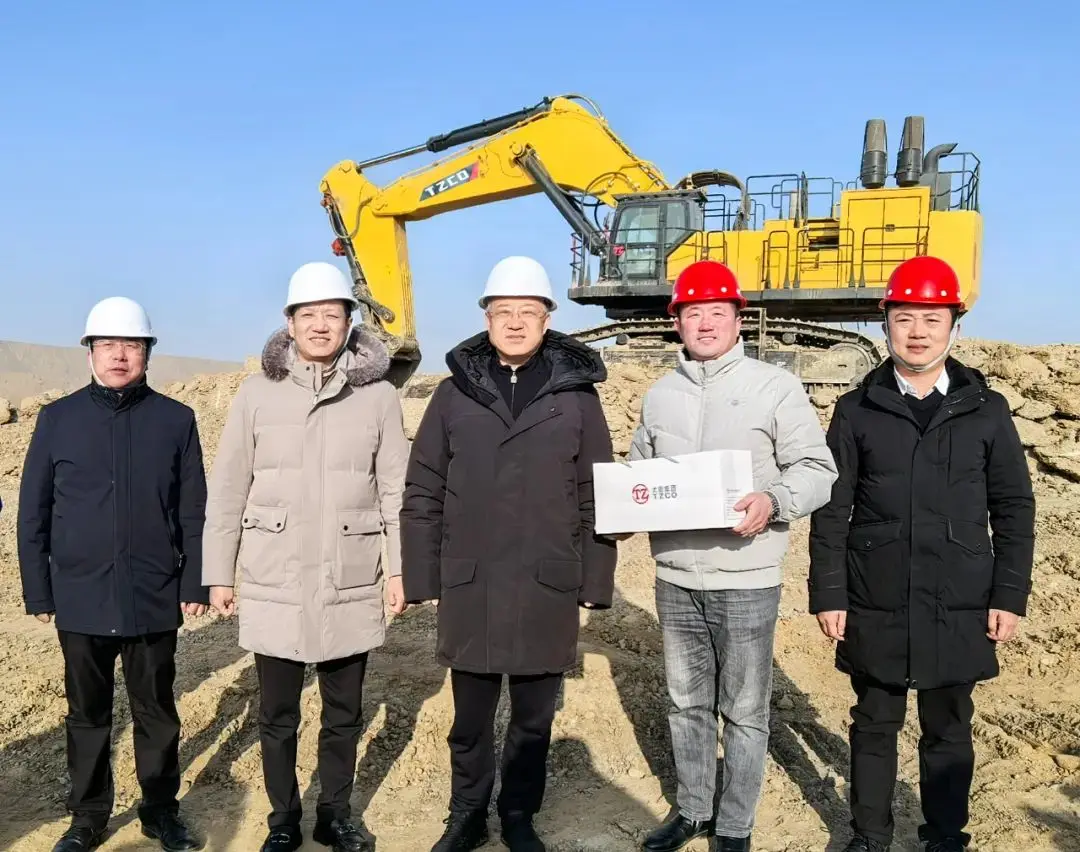
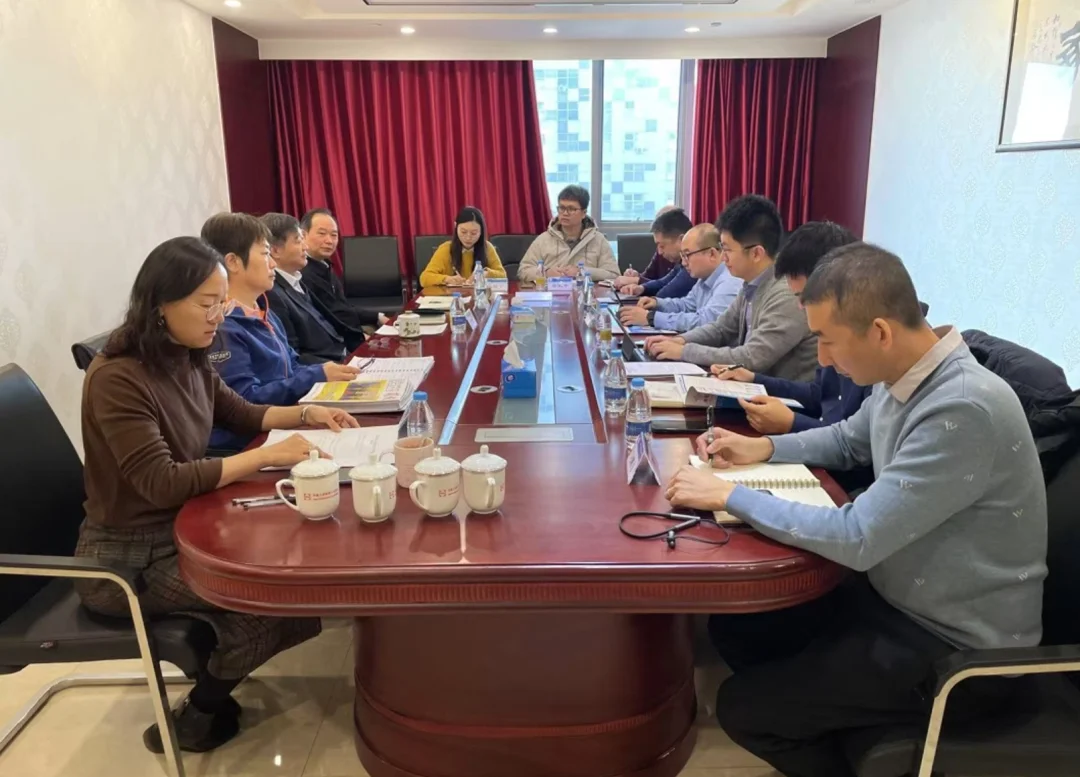
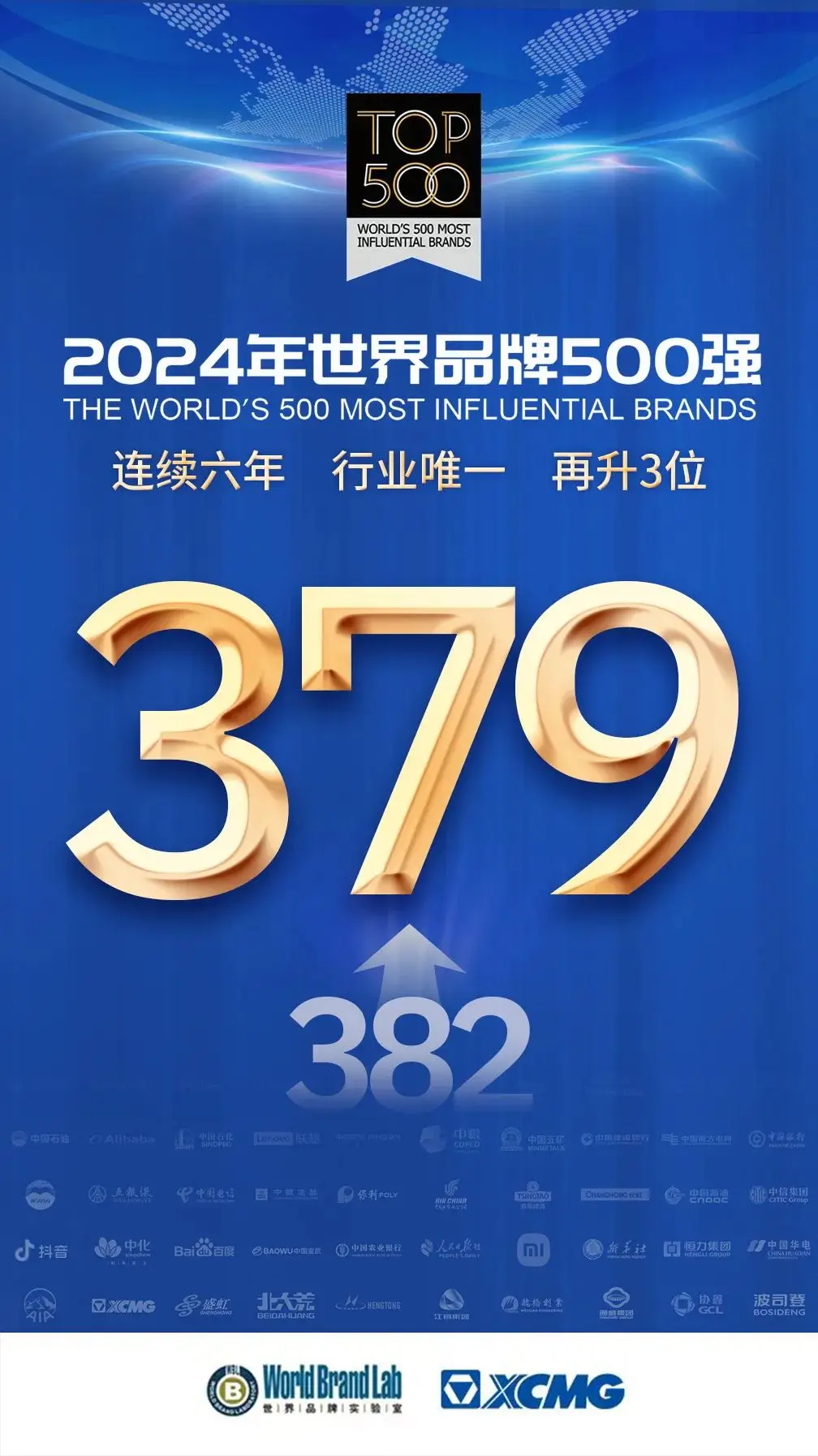
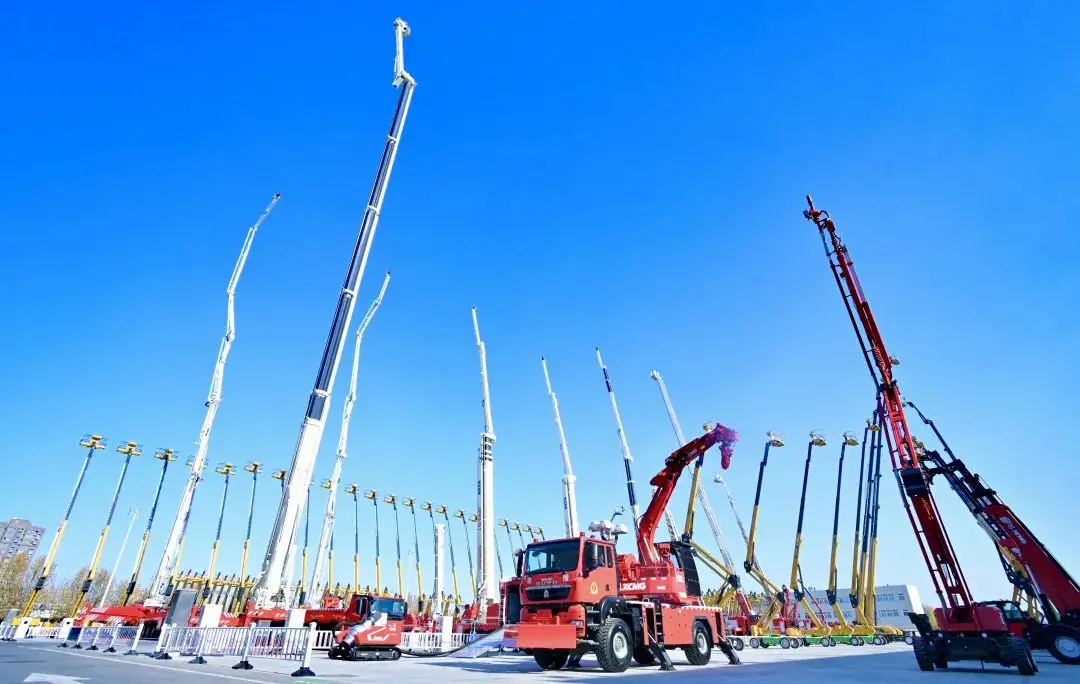
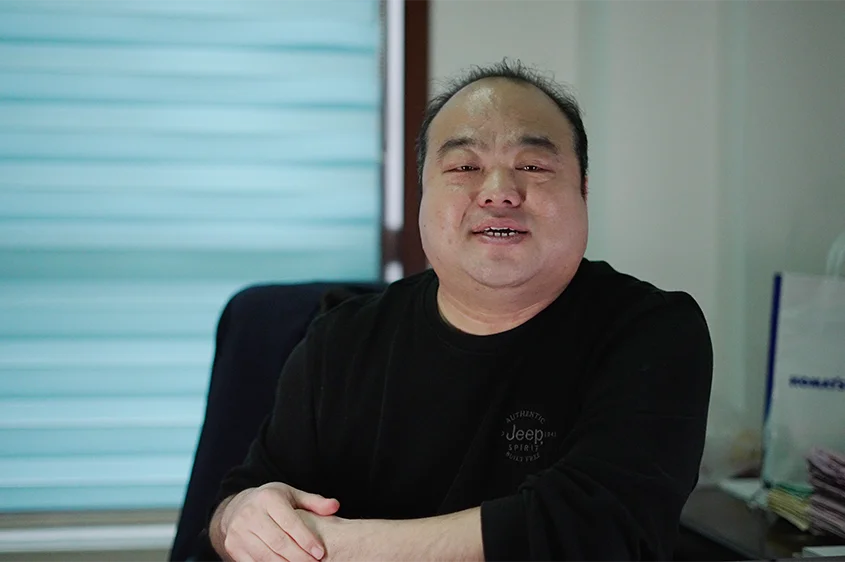
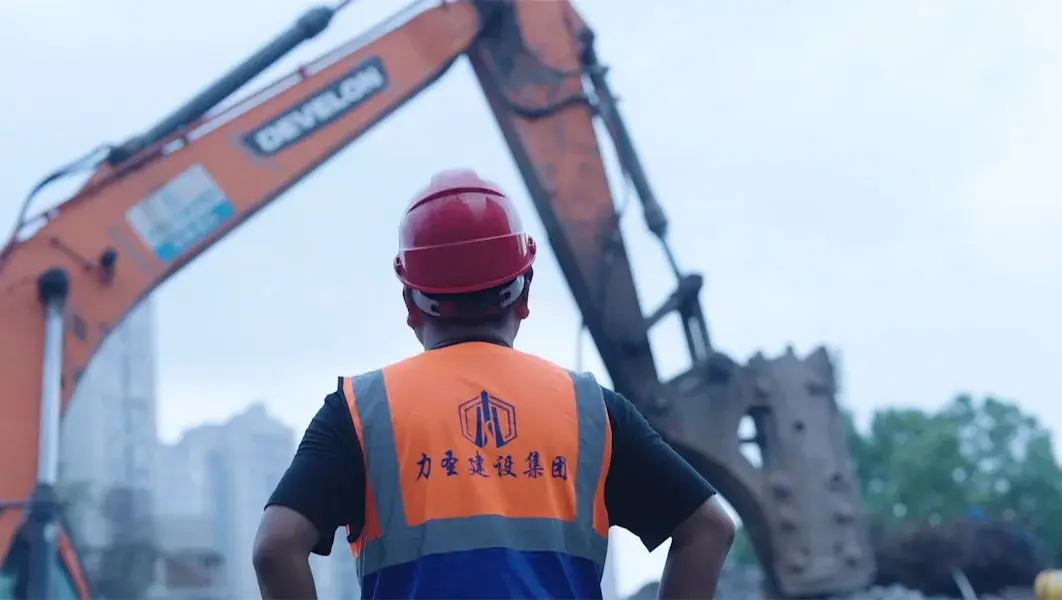

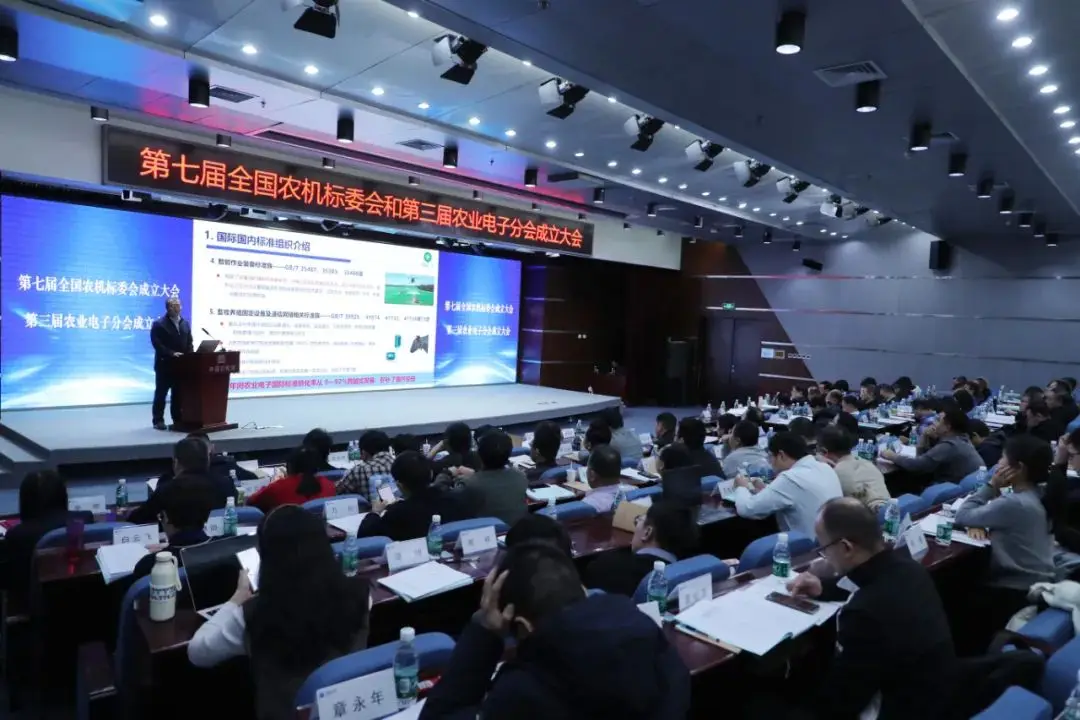
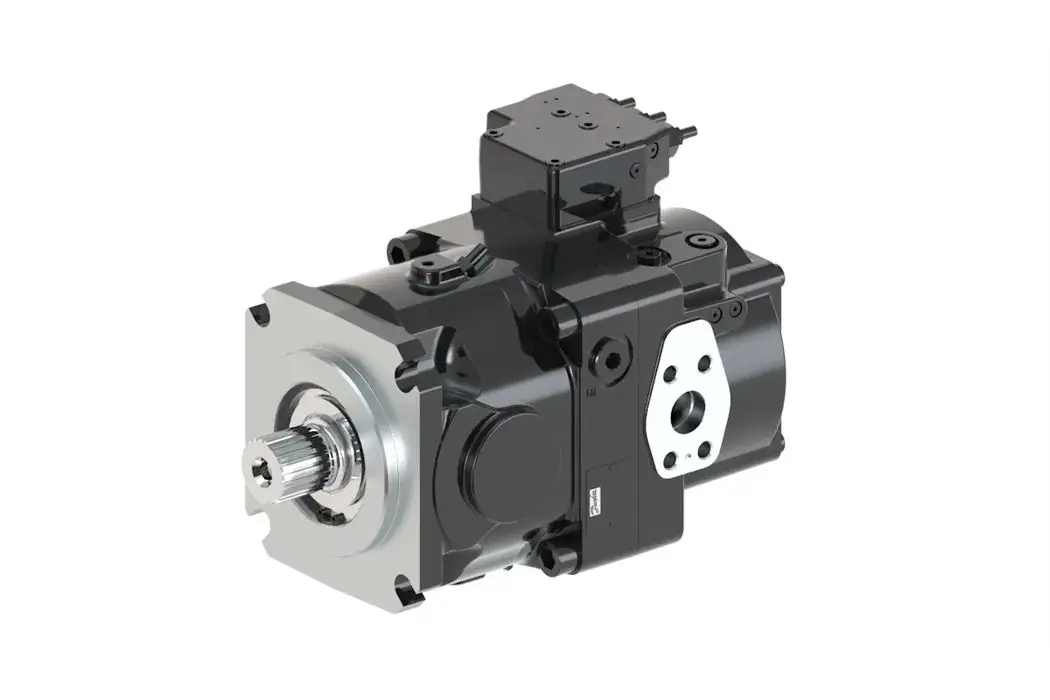
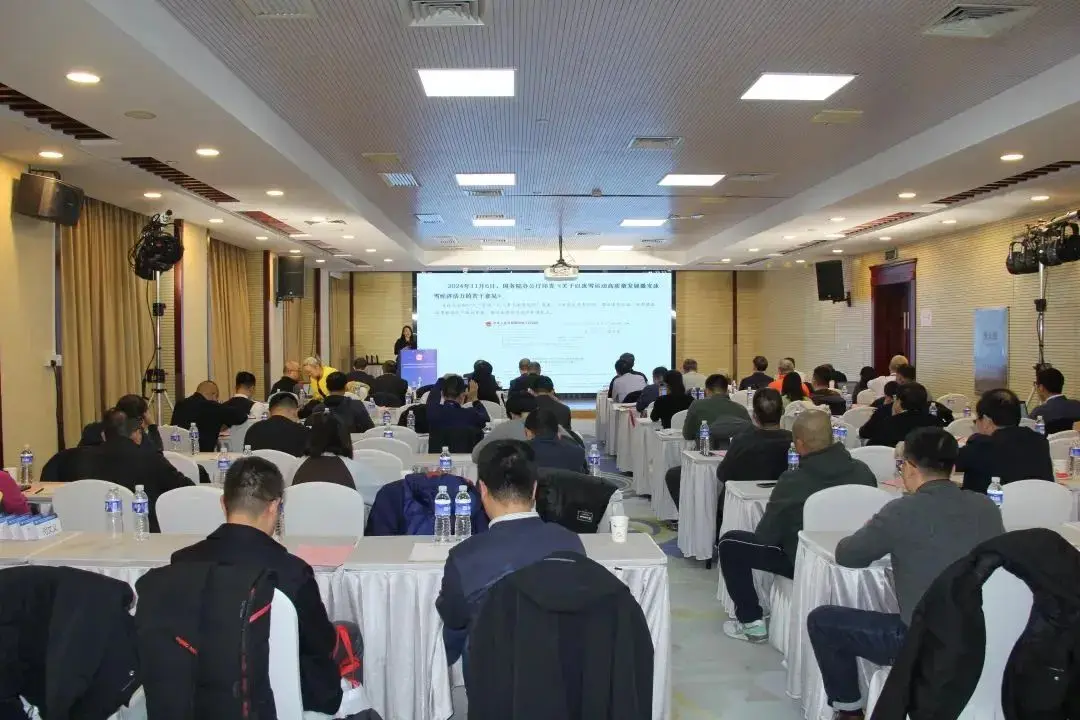
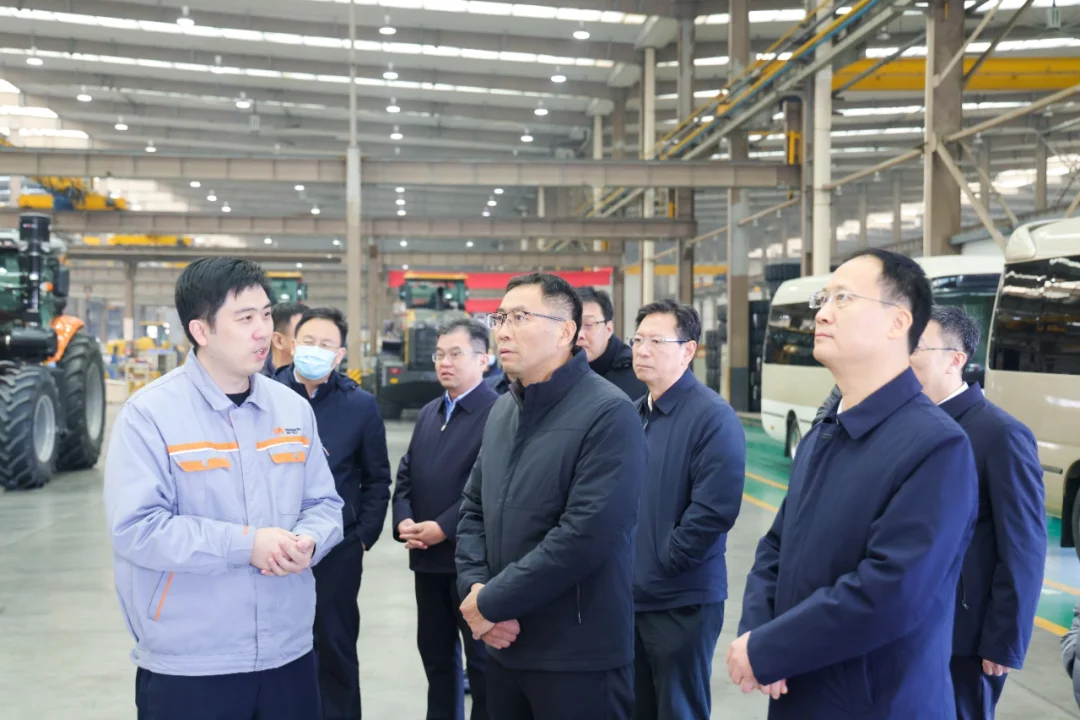
期待你的精彩评论