科技创新助力双星发展 两化融合引领高端
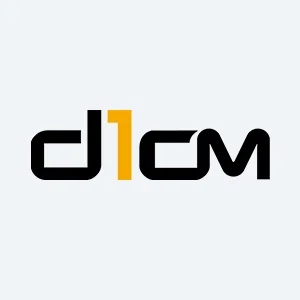
2011年以来,双星机械总公司立足高技术、高质量、高效率的发展目标,加快迈进高端步伐,不断完善企业的软硬件环境,努力实现两化的深度融合,将产品质量“严高细”落实到具体过程,把“细小精”变成行动,实现精益高效生产。此外,公司加快了核心技术创新,增强了技术实力,使双星机械产品适应“高质、高效、低耗”的市场需求,助推双星机械加速高端跨越,不断做大做强。生产过程“两化融合”: 提升生产效率和精细化水平 工
2011年以来,双星机械总公司立足高技术、高质量、高效率的发展目标,加快迈进高端步伐,不断完善企业的软硬件环境,努力实现两化的深度融合,将产品质量“严高细”落实到具体过程,把“细小精”变成行动,实现精益高效生产。此外,公司加快了核心技术创新,增强了技术实力,使双星机械产品适应“高质、高效、低耗”的市场需求,助推双星机械加速高端跨越,不断做大做强。
生产过程“两化融合”:
提升生产效率和精细化水平
工业转型升级要推进工业化和信息化的深度融合,改造传统产业,创新技术管理,实现内涵式发展。双星机械总公司在生产过程中不断增强设备等硬基础,完善技能、控制等软基础,并积极创新推动硬件和软件的相互融合和促进,为提高效率,促进质量精细化,降低员工劳动强度,改善员工工作环境打下了基础。
双星机械总公司为技术人员配备了国内比较先进的三维设计软件、有限元分析软件,缩短了产品研制周期,图纸更加直观,一线安装更加方便,更重要的是可以自动诊断干涉,最大限度避免设计失误。同时,公司投入巨资,引进有智慧“大脑”的精度高、加工效率高的大型龙门铣、龙门加工中心等高端加工设备,为生产提供了硬件保障。
高端设备需要高端人才,为了充分发挥先进设备优势和潜力,双星机械总公司分床种、分岗位、分层次对员工进行操作技能培训,培养了一大批设备操作能手;加大对现有设备的创新改造,创新工装、刀具,促进了生产高效化、产品精细化。去年以来,公司组织设备管理小组对公司现有设备的加工精度、加工效率等系数逐一摸查,对20多台设备改造进行了立项和改进。如,公司先后开发应用了加工中心“自动导圆程序”,提高了效率,解决了“拐点”的质量难题;应用了“旋转坐标编程法”,实现了自动计算坐标,保证了尺寸的准确性和工件的互换性;应用了“宏程序”,防止了回切、回程撞刀现象的发生。同时,针对高端工件加工难度增大的情况,引导鼓励员工创新刀具100多项,并引进先进刀具30多种。如,加工中心在加工平板硫化机滑极时,由于材质较硬,用普通刀具很难加工,质量也得不到保证,车间工艺小组购买了波刃铣刀,先粗铣后精铣,不但产品质量提高一个等级,还使加工效率提高2倍多。
通过推动“两化融合”,有效提高了质量和效率、降低了成本,提升了企业的“高端制造”水平。
生产设备“两化融合”:
适应“高质、高效、低耗”市场需求
“创双星机械品牌,必须创造自己的核心技术,创造自己的特色产品。”双星机械将高质、高效、低耗融入产品设计制作,创造出能耗更低、质量更精细、效率更高的产品,实现所产设备的“两化融合”。
双星机械每年都引进工艺和设计方面的高端人才,发挥其优势,攻克技术难题。同时,联合外部力量,加快新产品开发。如,双星橡机公司与山东大学合作研发,大胆采用光纤传导,突破行业两板控制的传统模式,改用一板控制,成功解决了轮胎动平衡试验机的程序控制难题,使设备技术性能达到行业领先水平。
高质量、高效率、低能耗是双星机械设备研发过程中信息化运用的一大特点。如,双星铸机公司V法线的电器控制实现多工位辅助控制,不仅控制更简便,而且效率更高;双星橡机公司新研发的智能自动化液压双模硫化机,配以触摸屏,实现人机对话、实时监控、故障显示,向无人化操作迈进,工作效率和硫化质量进一步提高,得到了市场的广泛认可。
双星机械总公司还跨行业创新、反思维创新,对原有产品进行智能化、自动化、信息化改造,提高产品的效率和性能。如,在半钢四模硫化机、双模硫化机上试验安装了显示屏,对成型机增加温控报警系统,显示剩余硫化时间、温度、压力、延时硫化时间等技术参数。通过“嵌入”信息化,客户可以随时一目了然地掌握设备的运行情况,这一创新提高了产品市场竞争力;双星锻压公司对太阳能冲床控制程序进行创新优化,实现了设备操作的远程编辑与控制,客户编好程序通过局域网传到车间现场即可实现预冲压演示,并根据演示现场修改程序,不仅减少了客户的生产成本,还提高了生产效率。
“两化融合”促进了高端产品研发,增强了各经济实体的市场竞争力。2011年以来,双星机械总公司共研发出20多个新产品,其中填补国内空白的Z425水平分型脱箱射压造型线,具有生产智能化、效率高、造型质量好、环保节能等优点,可代替小批量工件传统手工造型;具有完全知识产权的半钢四模定型硫化机,较传统双模硫化机效率提高1倍以上。“两化融合”,产品高质、高效、低耗,提高了双星机械市场竞争力,树立了过硬的名牌形象。
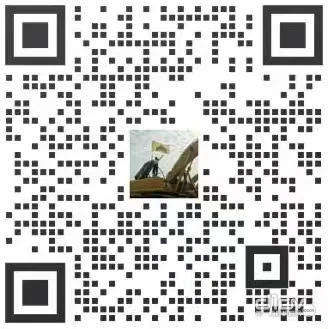
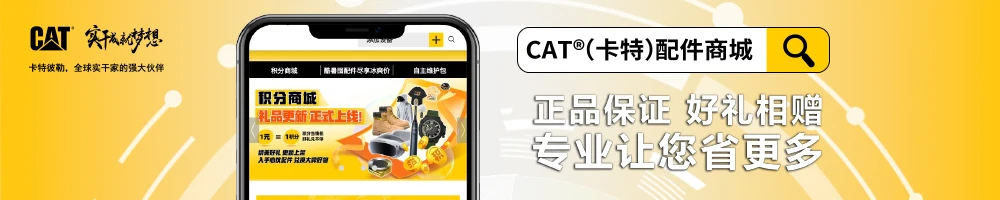
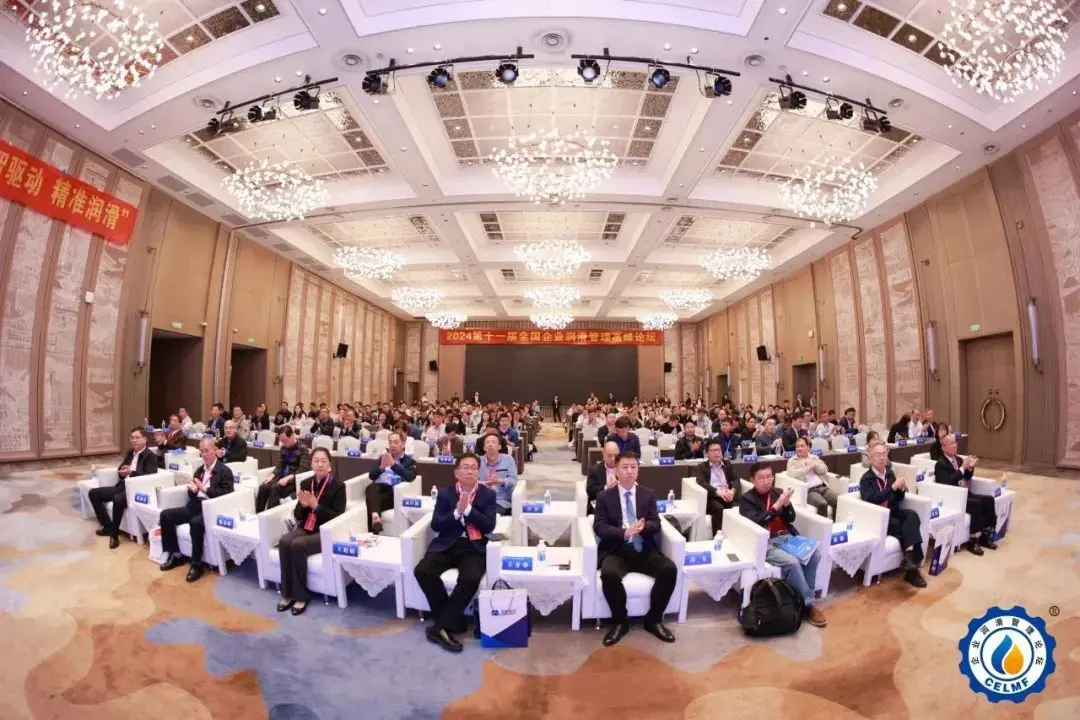
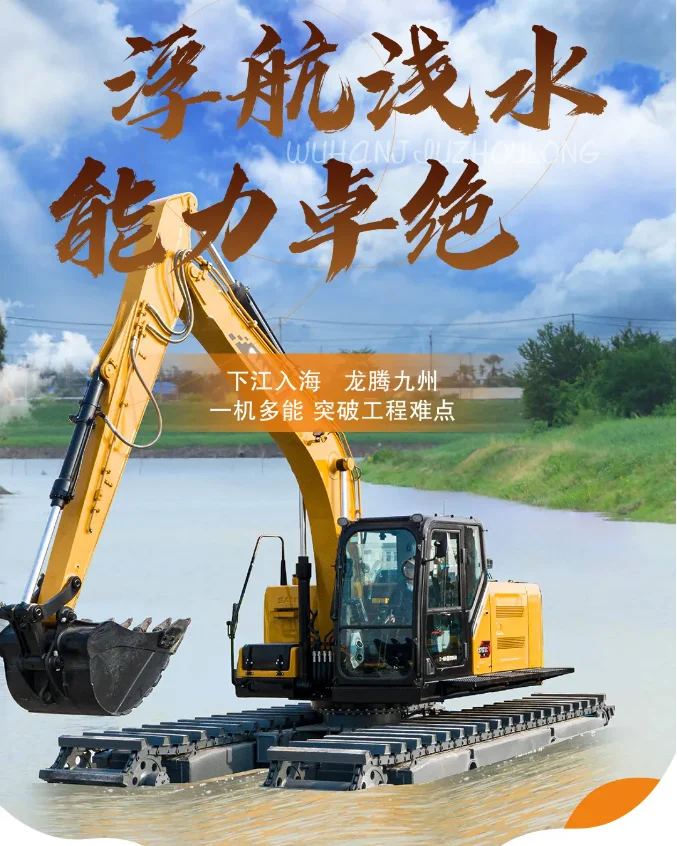
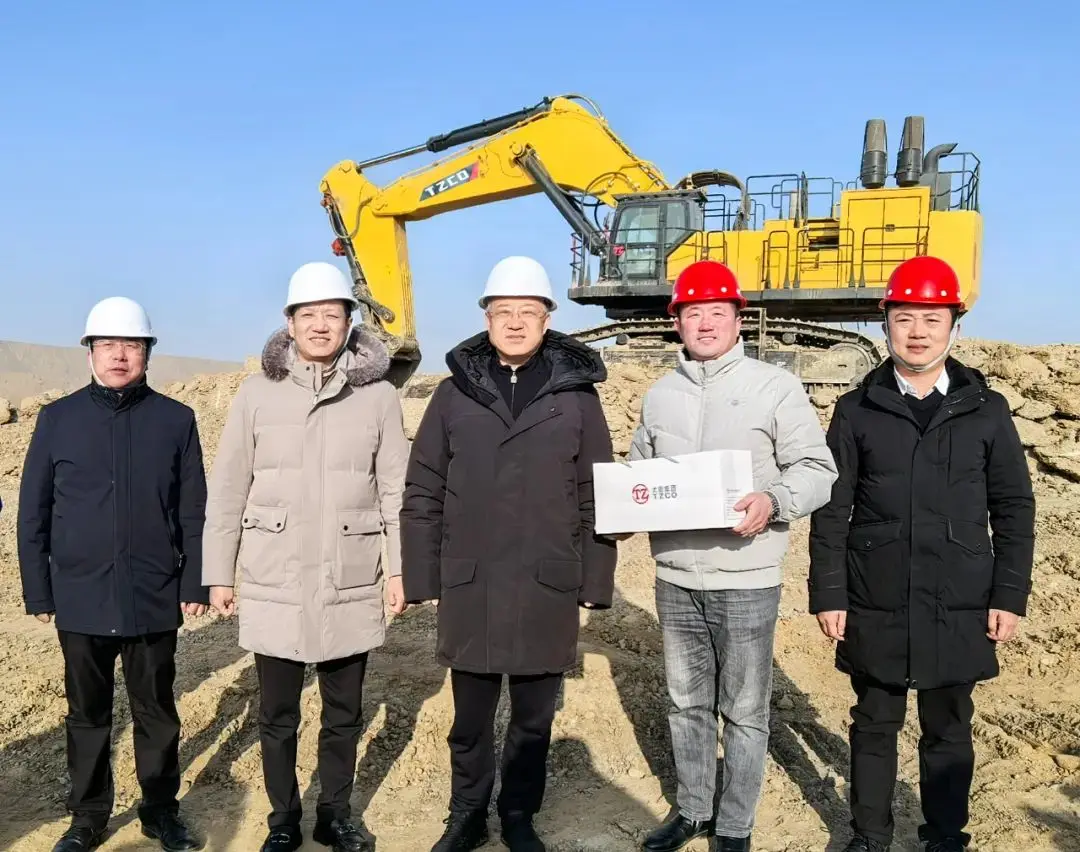
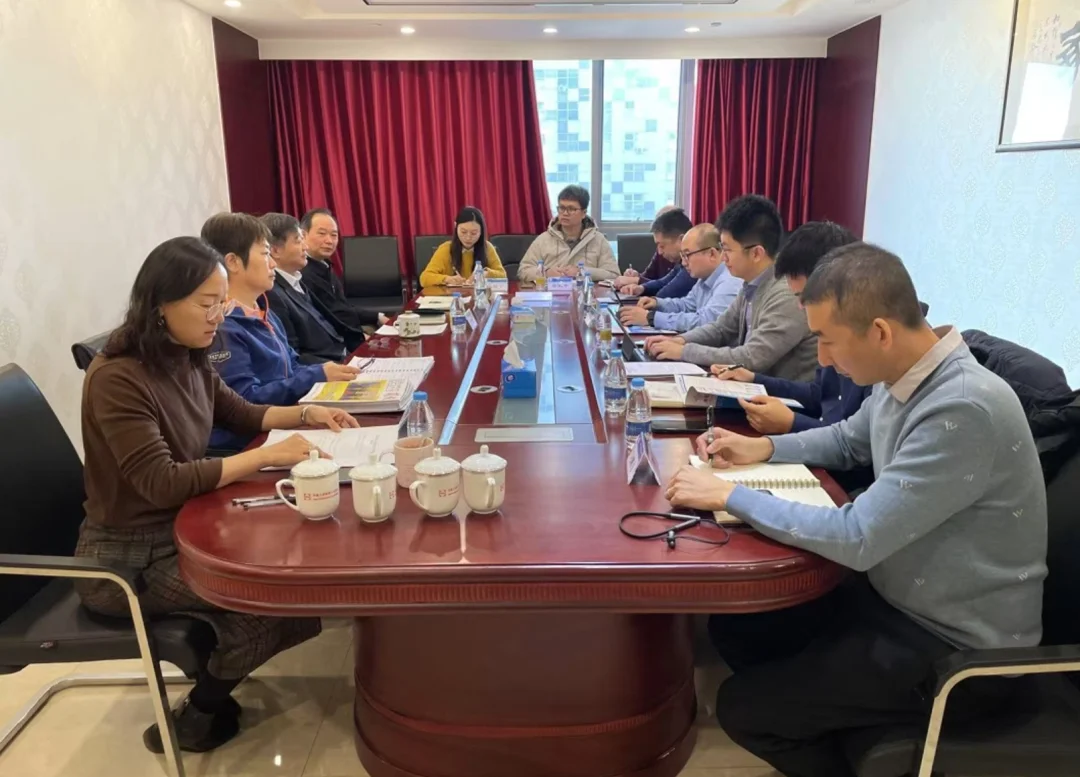
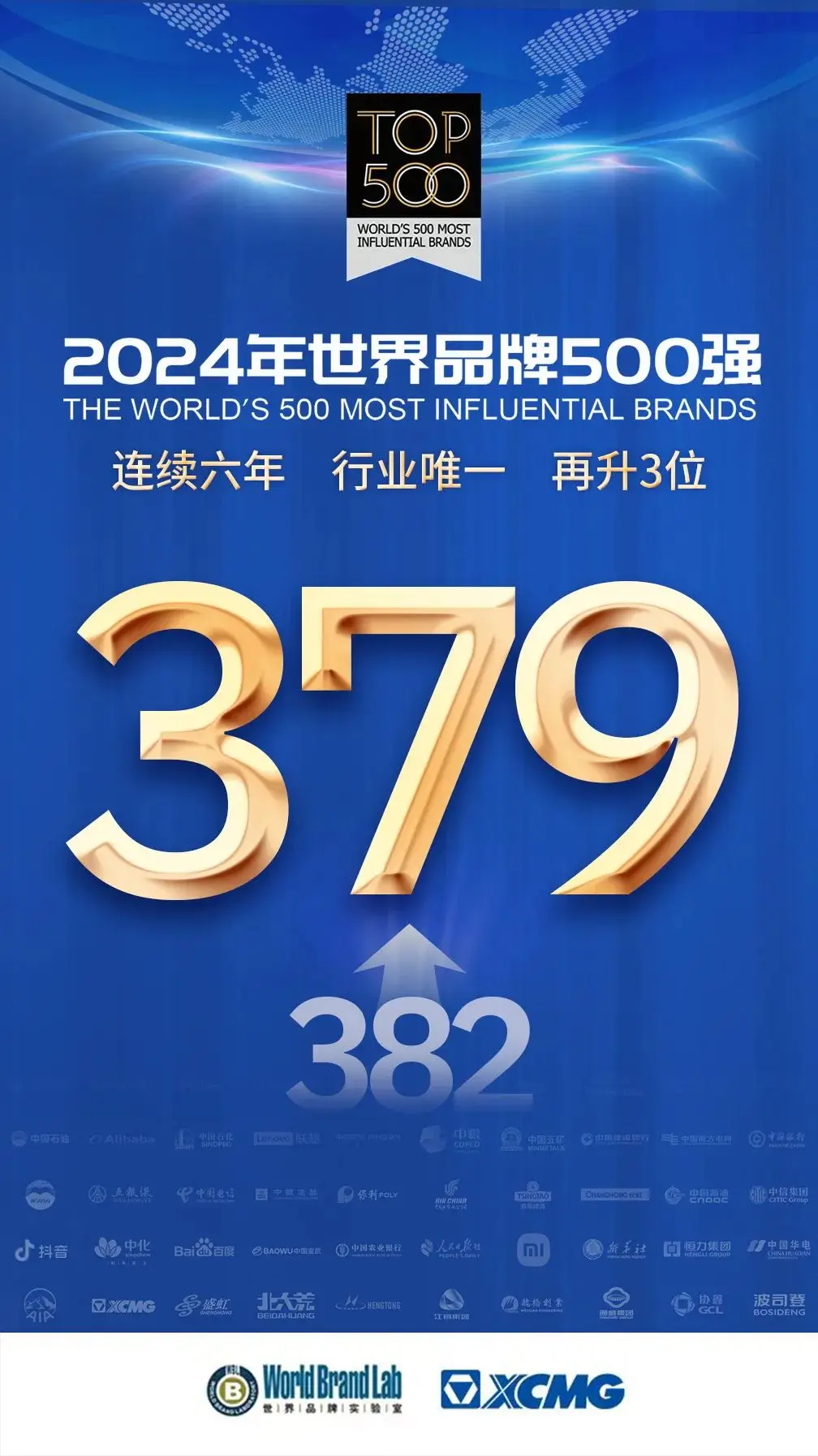
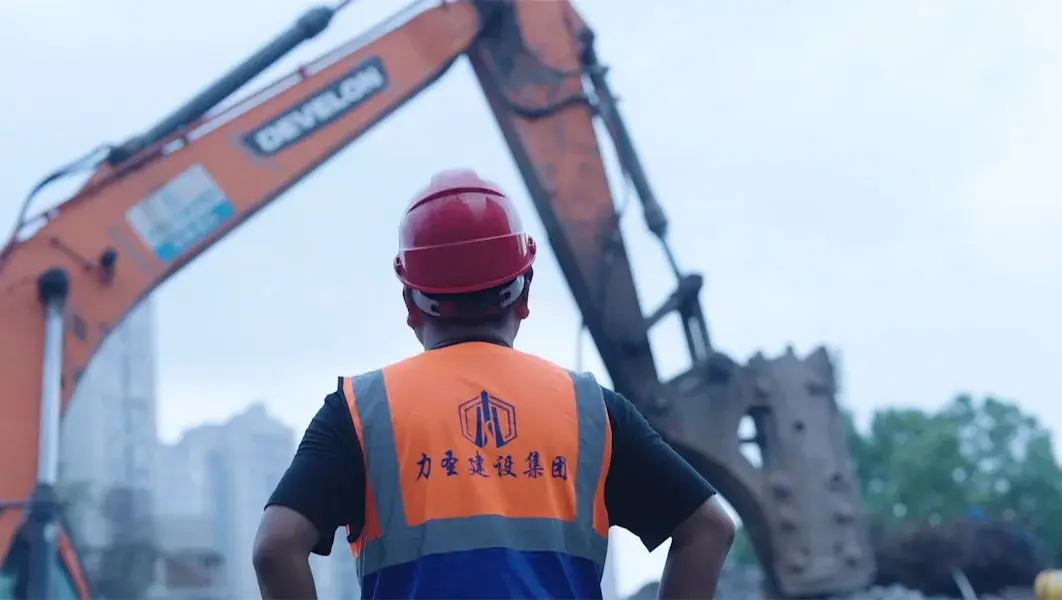

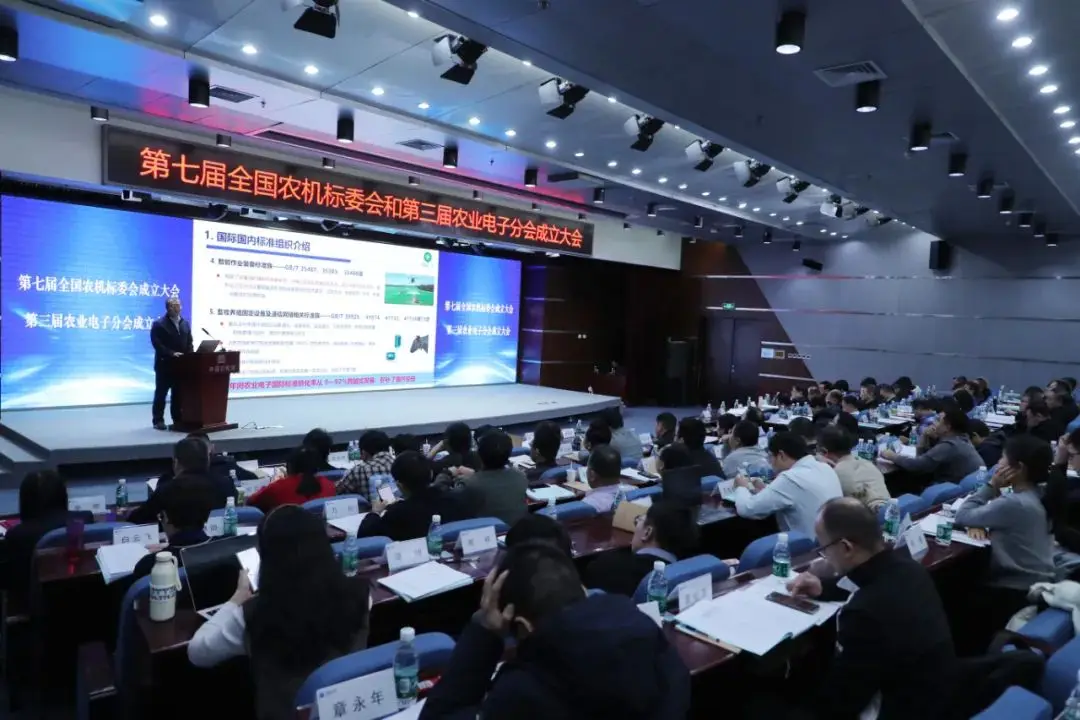
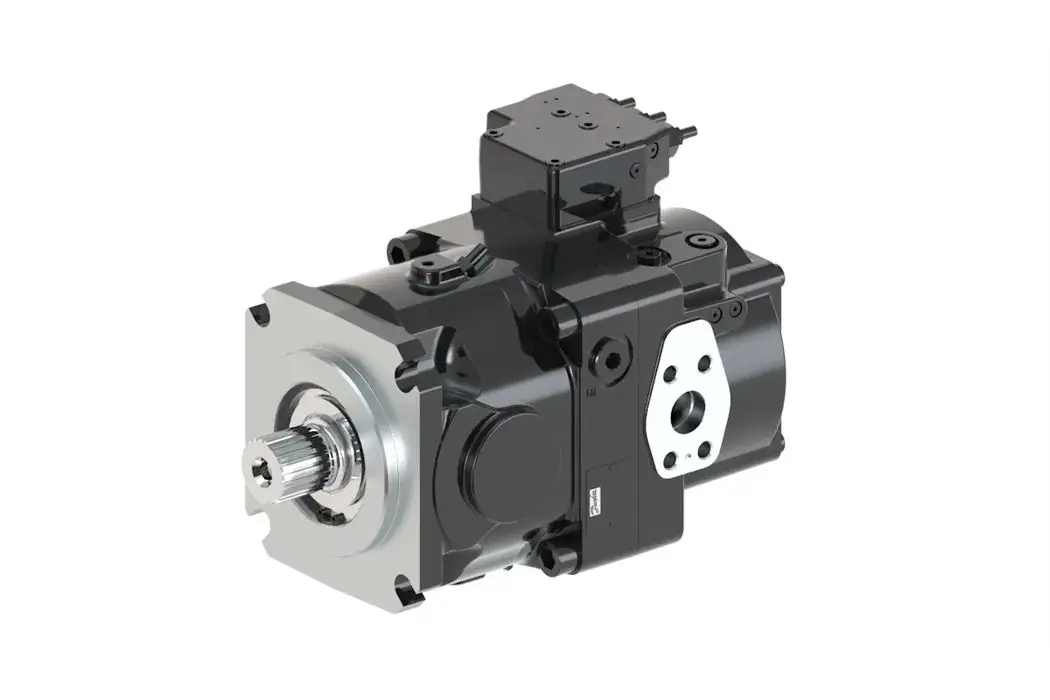
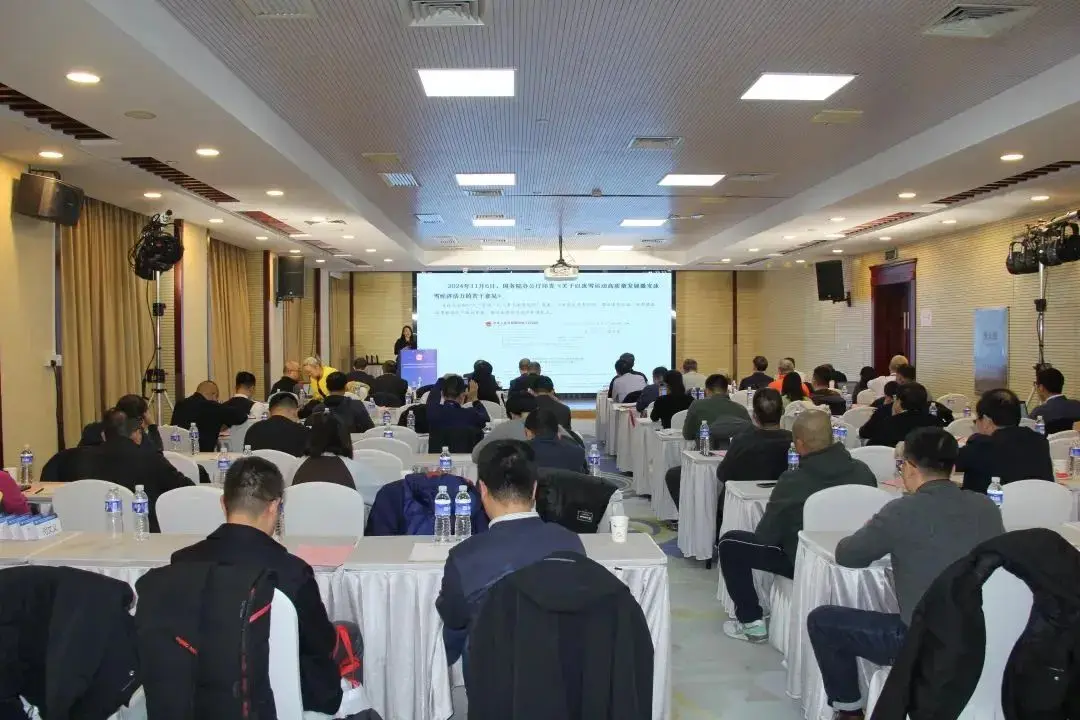
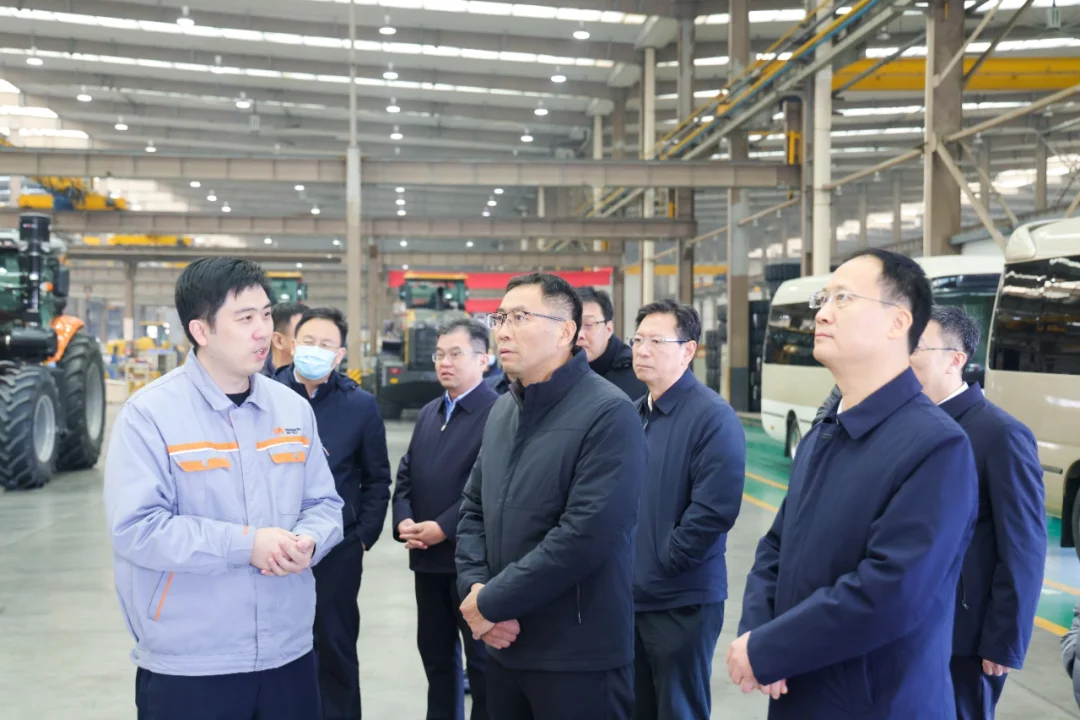
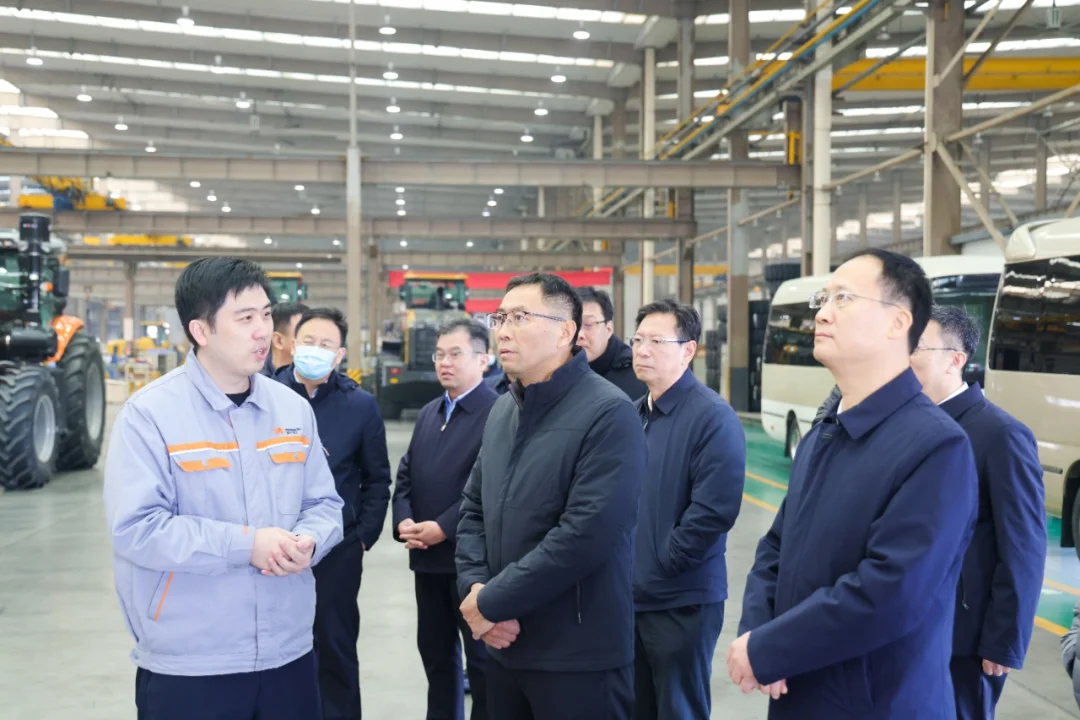
期待你的精彩评论