潍柴集团谱就“资源节约、环境友好”型企业
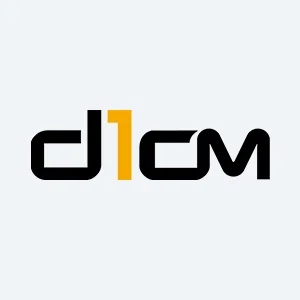
“把建设资源节约型、环境友好型企业作为加快转变经济发展方式的重要着力点。”“十一五”期间,为响应国家节能减排的号召,潍柴集团通过不断的科技创新、增加产品的科技含量,发展循环经济、强化节能管理等系列举措,实现了企业快速发展与履行经济可持续发展社会责任的有力结合。以自主创新促节能减排 创新是潍柴集团成功发展的关键因素。从1998年起,作为传统国有企业的潍柴集团在运行体制、商业模式、技术研发、内部管理等
“把建设资源节约型、环境友好型企业作为加快转变经济发展方式的重要着力点。”
“十一五”期间,为响应国家节能减排的号召,潍柴集团通过不断的科技创新、增加产品的科技含量,发展循环经济、强化节能管理等系列举措,实现了企业快速发展与履行经济可持续发展社会责任的有力结合。
以自主创新促节能减排
创新是潍柴集团成功发展的关键因素。从1998年起,作为传统国有企业的潍柴集团在运行体制、商业模式、技术研发、内部管理等领域,进行了全方位、系统式创新,走出了一条依靠自主创新的内涵式发展道路。通过技术创新,企业产品系列由中速柴油机为主发展到中高速柴油机全面发展,实现了产品从单一市场到多元化市场的转变;高速柴油机由单一配套重型卡车拓展到配套工程机械、大型客车、船舶及发电动力。其中,高速机进军50装载机市场,实现了我国工程机械动力的升级换代;与12米以上豪华客车的成功配套,改变了国内豪华客车长期依赖进口的局面。
据统计,“十一五”期间,潍柴集团累计开发新产品50多项,先后在国内率先成功研发了满足国Ⅲ、国Ⅳ和国Ⅴ排放标准、拥有完全自主知识产权的大功率高速柴油机,主要技术指标与国际先进水平接轨。其中,目前在市场大批量配套的蓝擎国Ⅲ发动机,比国内同类产品节油15%以上。根据行业协会统计,使用潍柴发动机,按照每辆商用车一年运行10万公里计算,年节油可达4800多升,如果按一百万辆计算,一年可节约柴油近500万吨。
2005年,面对发动机本身性能提升已十分有限的现状,潍柴集团率先提出商用车动力总成概念,并通过产业整合成为中国唯一的动力总成提供商。
“系统优化匹配后,装配潍柴动力总成的整车研发效率提升30%,油耗降低10-15%左右。”潍柴集团技术中心动力总成研究所负责人告诉记者。
2009年,经科技部批准,由潍柴集团牵头组建的中国商用汽车与工程机械新能源动力产业战略联盟成立。联盟旨在通过自主创新的途径,开发一系列电力与电控为特征的核心技术,建立起通用的商用汽车与工程机械混合动力总成技术平台。通过开发两个混合动力系统总成,应用于混合动力装载机、挖掘机、推土机、大型客车、重型卡车、军车等六个领域,使我国的商用混合动力技术达到国际领先水平,并实现产业化。产品实现量产后,在技术适用的范围内,可以达到燃油经济性提高30%以上、排放减少30%以上、制造成本增加低于30%的“3×30”综合指标。
“目前,潍柴生产的气体发动机已达25000台,实现减排6万吨以上。”潍柴集团西港新能源公司负责人指出。
与此同时,“十一五”期间,潍柴开发专项配套产品1710种,新产品产值占总产值的比例由“十五”末的45%上升到目前的58%,潍柴还先后主持和参与了10个国家“863项目”和科技攻关项目,获得产品和技术授权专利577项,完成省级以上新产品鉴定18项。2009年底,潍柴集团被中国企业联合会评为全国首批“自主创新型示范企业”。
近日,潍柴集团被科技部评为第三批“全国创新型企业”。
发展循环经济、强化节能管理
除了顺应行业发展趋势,增加产品节能减排的科技含量之外,潍柴集团通过积极发展循环经济、强化节能管理等措施,实现了社会资源与企业可持续发展的双赢。
“十一五”期间,潍柴集团发动机产量接近200万台,比“十五”期间增长177%,但公司节能量却达到了33.4万吨标准煤,万元产值综合能耗为0.0513吨标煤/万元,比“十五”期间降低了63%。
淘汰落后、高能耗的工艺技术及设备,促进了企业节能减排。“十一五”期间,潍柴集团投资500多万元,完成了3台总吨位为10吨的燃煤锅炉淘汰改造,新上了2台分别为6吨、4吨的燃气蒸汽锅炉,年节标准煤280余吨,有效减少了烟尘及二氧化硫的排放。投资3700万元,安装了系统节电装置,节电率达12%,每年可节电400万千瓦时以上。在新建工业园区的照明系统安装了瑞斯照明节电控制装置,在不降低车间内部照度的前提下,节电13%以上。投资200多万元在空压机站安装变频装置,节电率14%以上。在各生产厂、各能源管网,通过给水泵安装变频调速装置,节电率达到20%。在企业铸造系统,通过安装自动控温的两段式煤气自动烧嘴,杜绝煤气消耗“无功”浪费,从而有效降低了炉窑煤气单耗。用 LED灯光源替代传统金卤灯,节电率65%以上,年可节电2300万千瓦时以上。
工业废水的再生回用是潍柴致力于保护生态环境、实施循环经济的一项长期持久的工作。
在潍柴集团老厂区,潍柴建有日处理水量4400吨的废水再生回用系统,工业废水全部进污水站并实现“闭路循环”,该系统年回收废油100多吨,年减少工业废水排放量120万吨,年中水回用150多万吨,年节水150万吨。在“十一五”期间建成的新工业园区,建设了日处理能力1000吨的废水再生回用系统,采用分质预处理、再综合处理的先进工艺,年回用中水36万吨、节约新鲜水36万吨。企业经处理回用的中水广泛用于各大系列柴油机的试车循环用水、生产工艺用水、厕所冲冼水、消防用水等生产与生活杂用,既减少了新鲜水消耗,又改善了环境、减少了污染。
积极实施节能技改,不断挖掘节能潜力。潍柴集团根据生产需求及蒸汽供耗现状,有效调整蒸汽管网配送布局,更新管网保温材料,不断优化蒸汽管网结构,保障企业蒸汽损失不断降低。“十一五”期间,投资近200万元,对工业锅炉实施自动变频改造,对交换站实施给水、温度等自动调节改造,节电率30%、节煤率8%。对于各能源系统管网,每年都投入专项资金进行大修或技改,杜绝各种能源“跑、冒、滴、漏”,其中检测并整改的柴油管道泄漏一项,年减少柴油损失400余吨。#d1cm#page#
“十一五”期间,潍柴集团在潍坊新建了四个工业园区,占地3000余亩。潍柴特别注重新项目的节能减排基础建设,以铸造工业园为例,按照“可持续发展”和“循环经济”原则,工艺设计中充分选用低能耗、节能型的生产设施,并采用余热利用技术,安装冲天炉高温烟气余热利用系统、蒸汽冷凝水回收系统,实施余热、余能回收利用,有效减少园区采暖蒸汽及天然气消耗。其中的80吨热风富氧冲天炉,铸件综合废品率控制在1.8%以下,吨铸件耗焦220千克,较国内平均水平年可节约焦炭4.7万吨;通过余热利用技术将烟气二次燃烧,铁水温度达1500-1550℃,熔化效率提高45%;通过旧砂回收利用技术,使废砂再生率达到85%以上;利用全密封布袋除尘技术,烟尘去除率达到99.8%。在加工工业园区,高度重视节能减排的基础性建设,全部采用低能耗、节能型设备,保障了新建园区的能源利用达到最优。
2008年,我国汽车零部件再制造试点工作正式启动,作为14家试点企业之一,潍柴成为第一批“吃螃蟹的人”,开始了自己的探索之旅。
目前,结合潍柴产品特点,潍柴集团投资10亿元,全套引进欧美的再制造工艺、设备和标准,建成了高起点、专业化、规模化的发动机再制造基地,一期设计年生产能力2万台。
“达到2万台生产能力时,将回用金属1.63万吨,节约标准煤3.56万吨,减少二氧化碳排放62000吨。”潍柴再制造公司总经理李峰告诉记者。
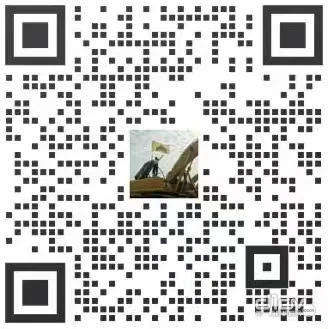
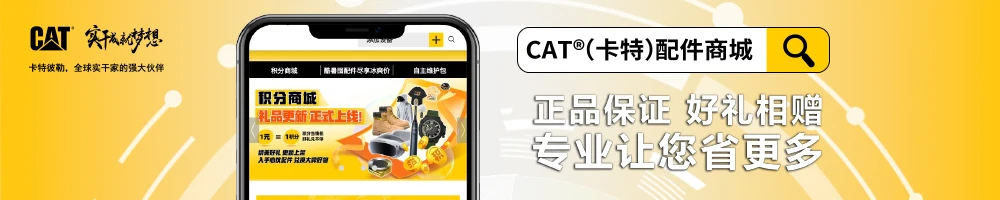
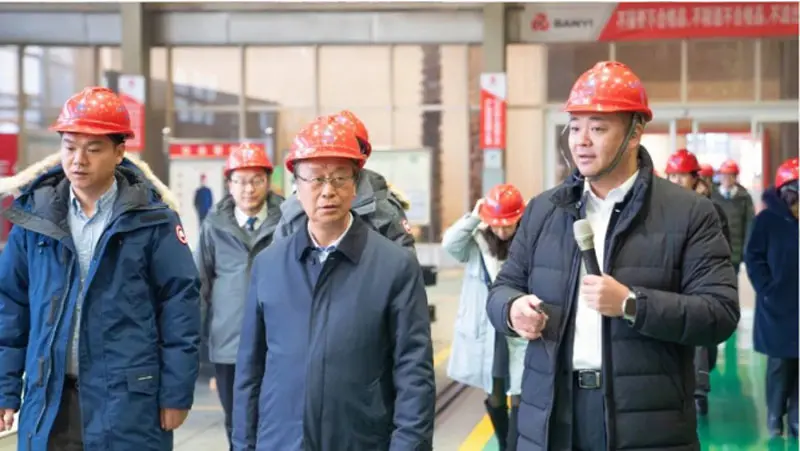
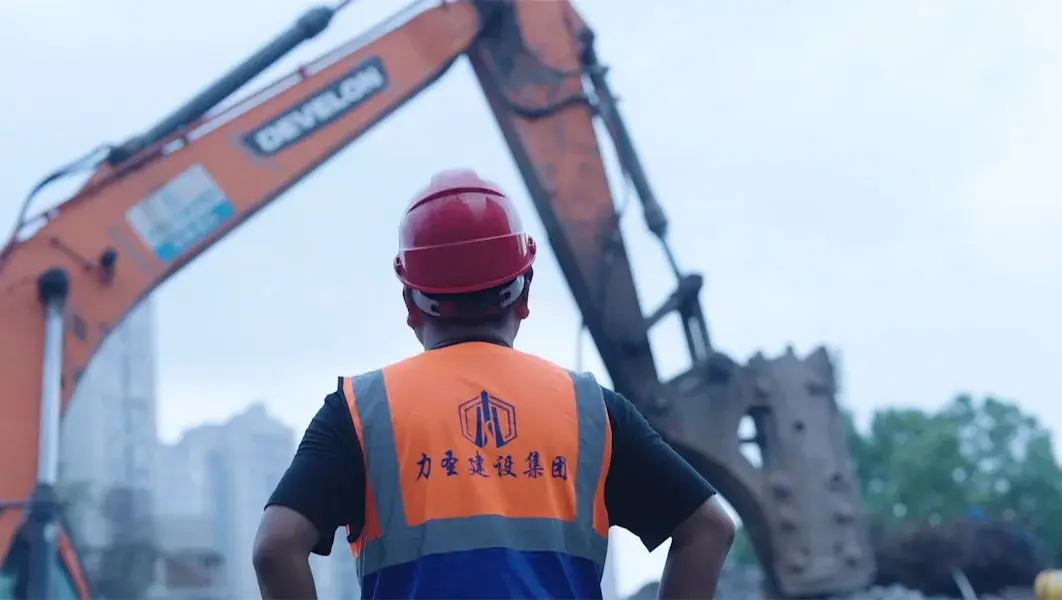
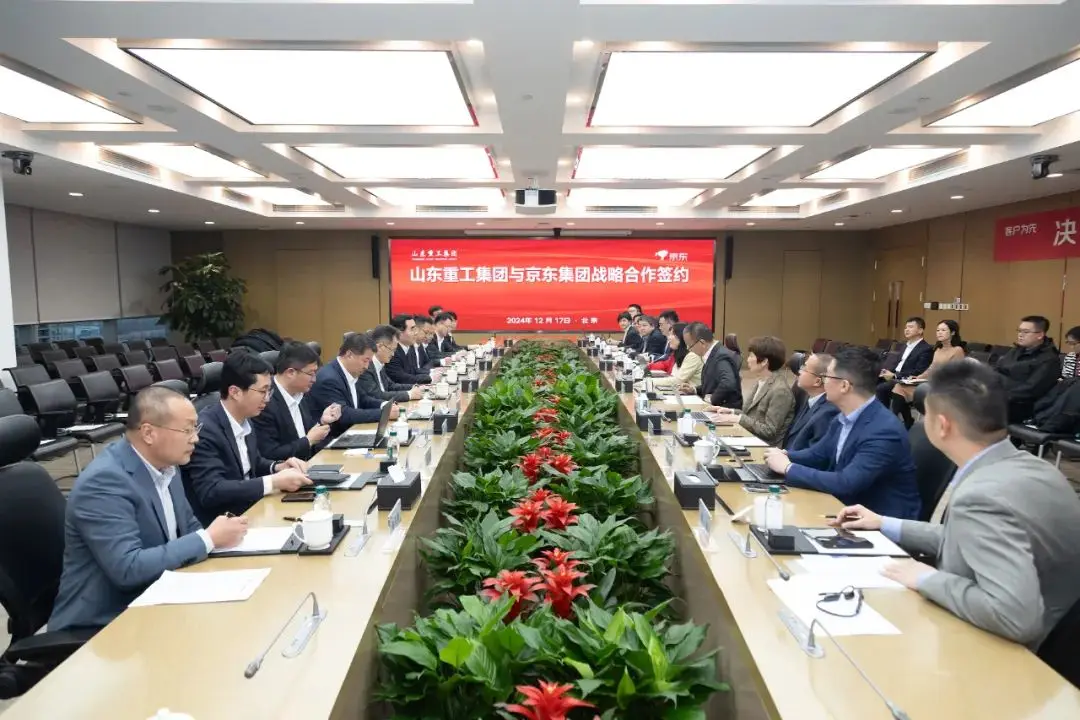
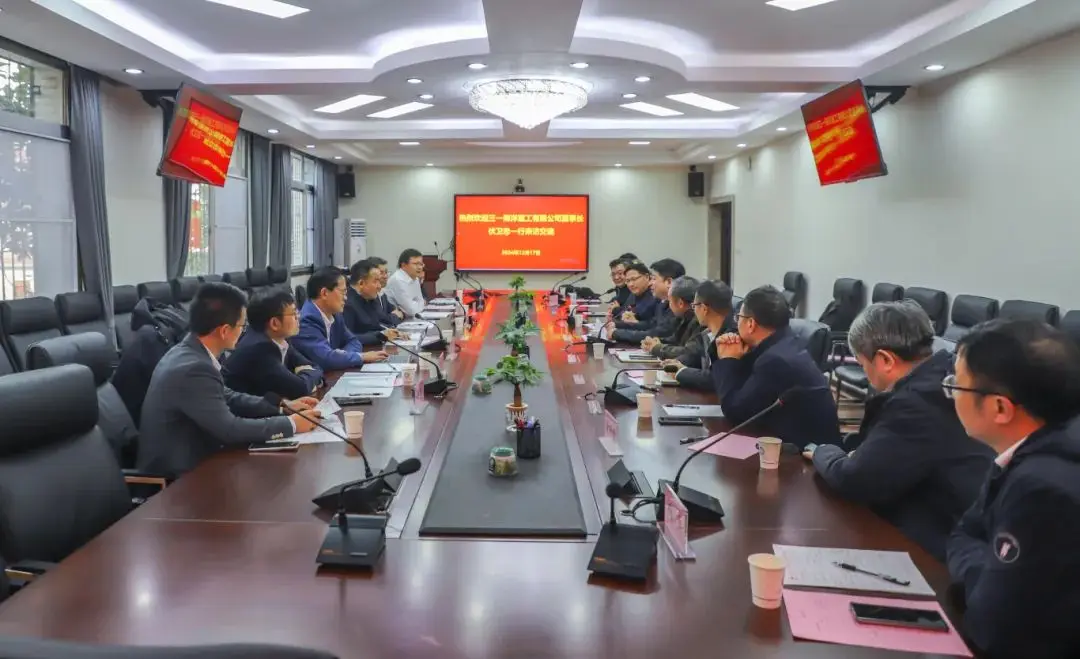
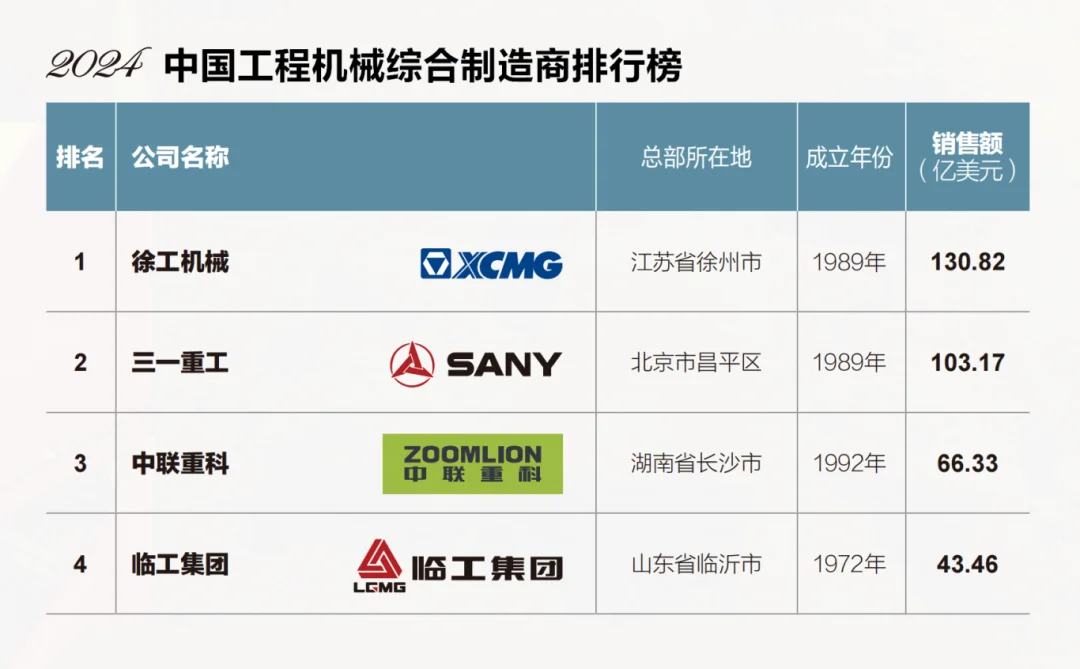
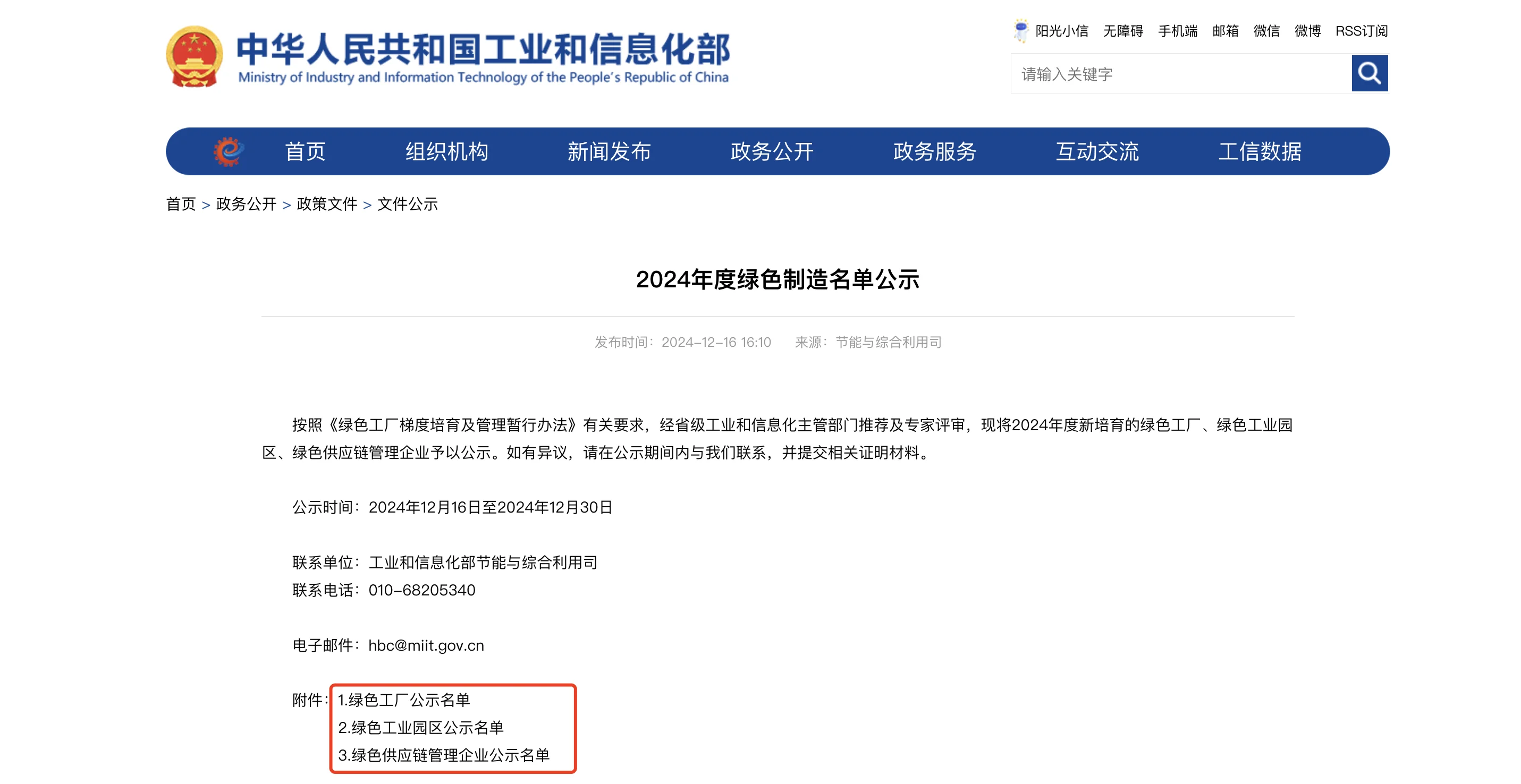
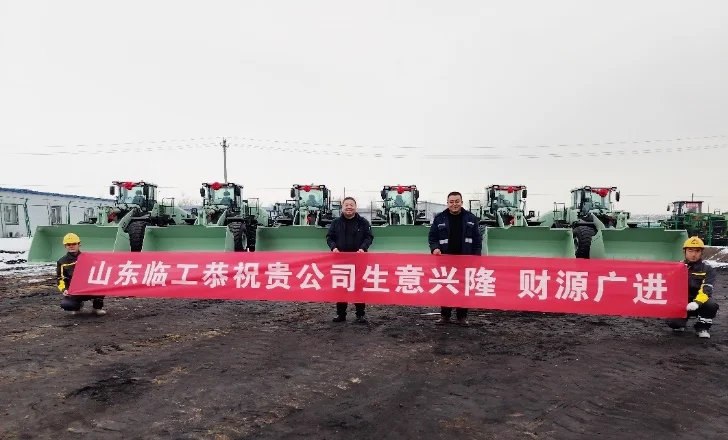

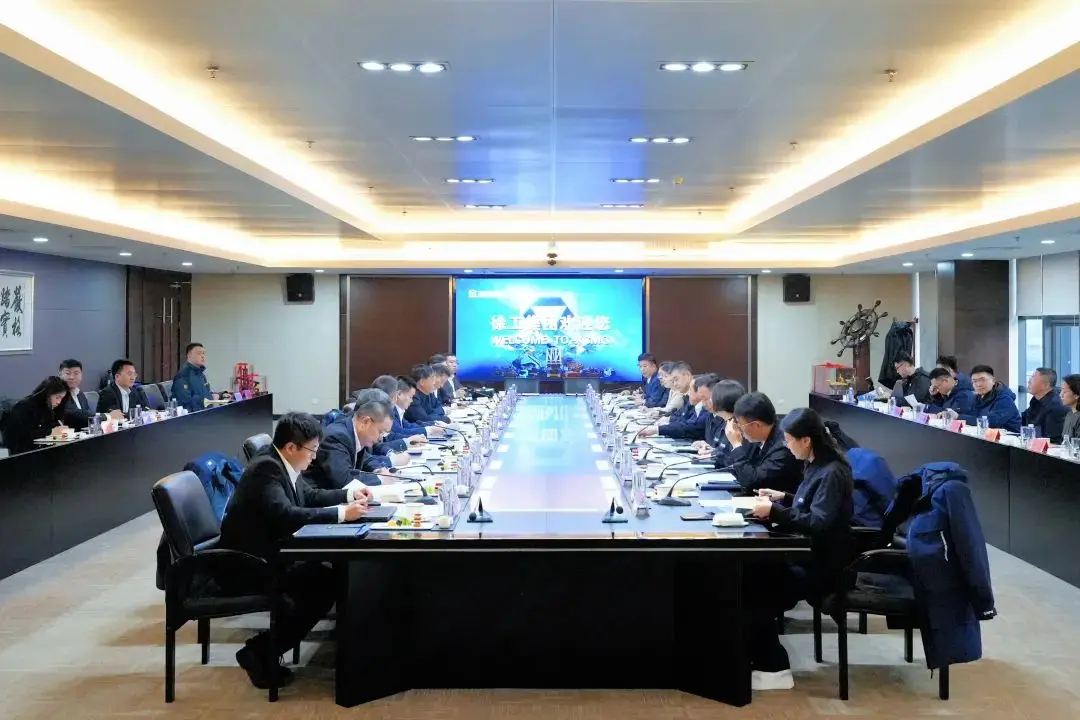
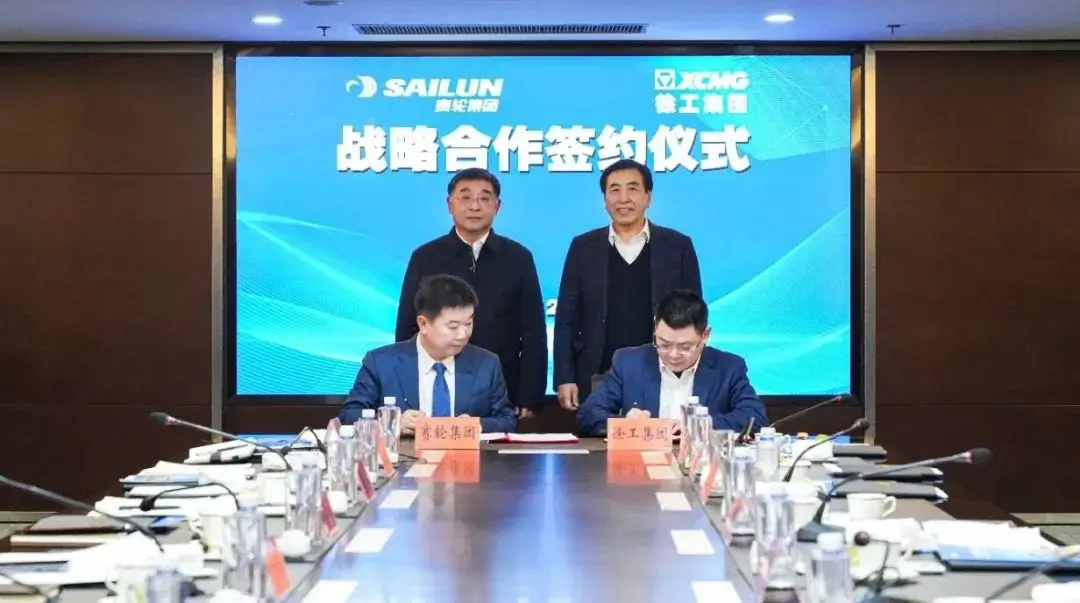
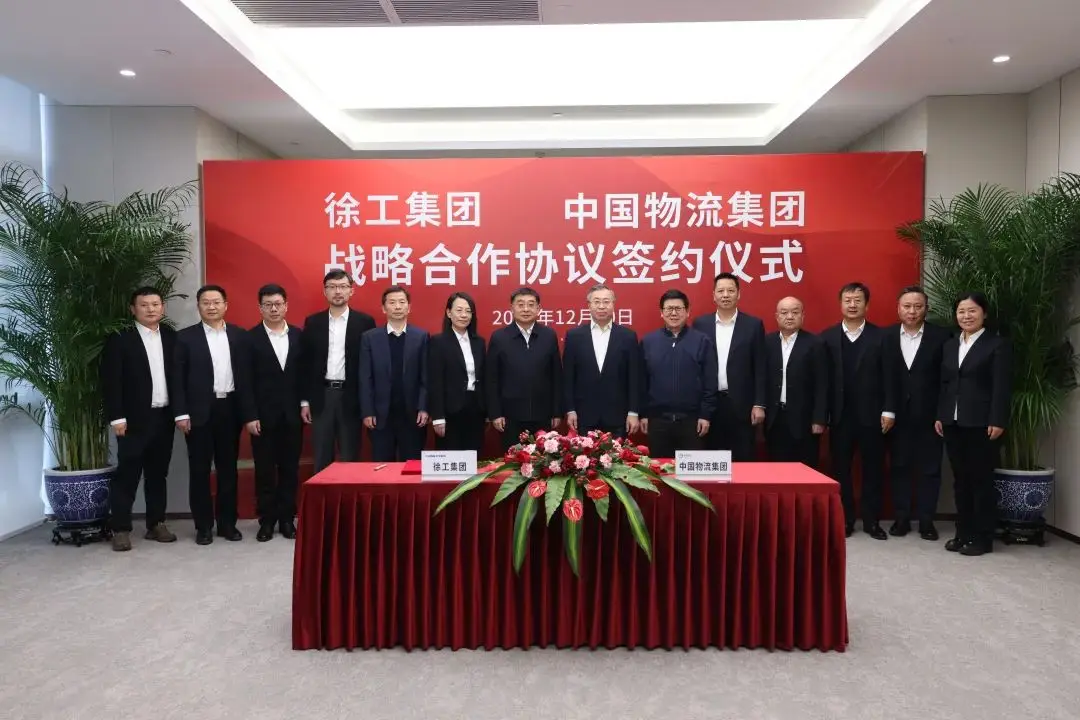
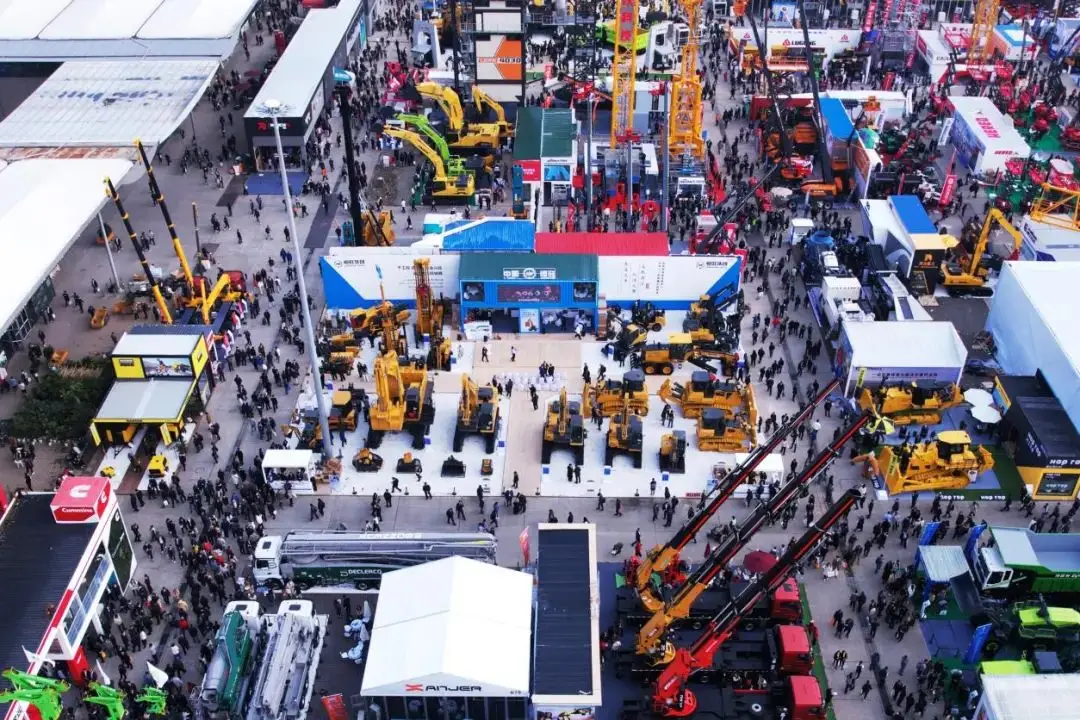
期待你的精彩评论