FMEA在产品设计中的应用
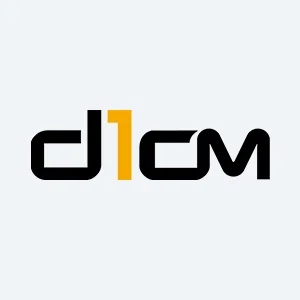
FMEA(Failure Mode and Effects Analysis,即潜在失效模式及后果分析)作为TS16949质量体系的五大工具之一,是一种确保在产品和过程开发(APQP)中对潜在问题予以考虑和阐述的分析方法,它最直接的结果是跨功能小组的集体知识的文件化。 FMEA的概念和应用 企业在产品设计过程中使用FMEA的主要目的是发现和评价产品或过程中潜在的失效及其失效后果,找到能避免或
FMEA(Failure Mode and Effects Analysis,即潜在失效模式及后果分析)作为TS16949质量体系的五大工具之一,是一种确保在产品和过程开发(APQP)中对潜在问题予以考虑和阐述的分析方法,它最直接的结果是跨功能小组的集体知识的文件化。
FMEA的概念和应用
企业在产品设计过程中使用FMEA的主要目的是发现和评价产品或过程中潜在的失效及其失效后果,找到能避免或减少这些潜在失效发生的措施,将上述整个过程文件化。它是对设计过程的更完善化,以明确必须做什么样的设计和过程才能满足客户的需要。所有的FMEA的重点在于设计,无论是用在设计产品还是过程。以下主要阐述如何应用FMEA、FMEA的应用领域以及设计FMEA的作用。
1. 如何应用FMEA
适时性是成功实施FMEA的最重要因素之一,我们首先要明白,FMEA是一个“事发前”的行为,而不是“亡羊补牢”。为了达到最佳效益, FMEA必须在设计或者过程失效模式被无意地纳入产品或过程之前进行,事先花费时间适当地完成FMEA分析,能够更容易地、低成本地对产品或过程进行修改,从而减轻事后修改的危机。
2. FMEA的应用领域
FMEA被展开时,一般有3种案例,每个案例都有不同的领域和重点。
⑴新设计、新技术或新过程。该FMEA的领域是完成设计、技术或过程。
⑵修改现有的设计或过程(假设现有的设计或过程已经有一个FMEA)。该FMEA的领域应该在于修改设计或过程,有可能因为某修改和市场上历史反映而有交互影响。
⑶在一个新的环境、地点或应用上,利用了现有的设计或过程(假设现有的设计或过程已经有一个FMEA)。该FMEA的领域是对现有的设计或过程在新环境或地点上的影响分析。
总的说来,FMEA是一个应该被执行的程序,它并不只是简单地把表格填满,而是通过有效地执行该程序,以消除风险和计划能确保客户满意的适当控制。
3. 设计FMEA的作用
FMEA分为设计FMEA和过程FMEA,在此主要阐述一下设计FMEA在实际工作中对整个设计过程的支持,并因此来降低失效风险。
⑴它有助于对设计要求和设计方案进行客观评价;
⑵有助于制造、装配、服务和回收要求的最初设计;
⑶提高在设计和开发过程中,考虑潜在失效模式及其对系统和车辆运行影响的可能性;
⑷为全面、有效的设计试验和开发项目的策划提供更多的信息;
⑸根据潜在失效模式对“客户”的影响,对其进行分级列表,进而建立一套设计改进、开发和验证试验的优先控制系统;
⑹为建立和跟踪降低风险的措施提供一个公开的讨论形式;
⑺为将来分析研究售后市场关切情况、评价设计更改及展开更先进的设计提供参考(如经验等)。
FMEA的实际应用案例
笔者任职的公司从2006年开始宣贯TS16949标准,并根据工作性质的分工,对相应的人员进行了5大工具的培训,在新产品设计制造过程中贯彻执行TS16949标准,感觉获益颇丰,也有效地避免了很多潜在的隐患。
1.FMEA在产品设计初期的准备
设计初期的主要信息来源(设计输入或称设计意图)主要来自客户的要求和需求(包括客户的抱怨、期望以及对前期产品质量问题的反馈)、销售或者售后维修人员对市场存在问题的反馈、车辆配置的要求等;我们将前期收集的问题进行汇总并进行可行性分析,组建核心小组,将设计输入需求归纳后建立初步方案并进行评审。
2.FMEA在产品设计过程中的应用
成立项目核心小组后,建立FMEA文件编号,并进行设计责任的划分,确定相关部件设计工程师(编制者)的信息,以便查询,下面以我公司9.5t转向前轴设计为例说明。
项目小组成立后,将项目小组人员给予适当的分析级别并将设计划分给个人,根据职责将产品划分为系统和子系统,信息填入预先设计的FMEA框图中,前轴主要分为制动系统、转向系统和承载系统,根据分工不同,相应的小组人员必须对照构成的系统、子系统或零组件,决定其特定的活动。在FMEA框图中还应该填入FMEA初次预定完成的日期,注意此日期不应该超过计划的量产设计发布的日期。
其次就是在框图中填入将被分析项目的名称和其他适当的信息(如编号、零件等级等等), 此时应该用尽可能简短的文字来说明被分析项目要满足设计意图的功能,包括该系统运行的环境相关信息。
然后,对设计的产品进行潜在失效模式分析,潜在失效模式是指系统、子系统或零部件有可能未达到或未完成在项目和功能中所描述的设计意图的种类(如预期的功能丧失),这潜在的矢效模式可能是更高一级子系统或系统的潜在失效模式的起因,也可能是比它低一级的零部件潜在失效模式的后果,比如该前轴在转向系统中可能出现运动转向干涉,造成这种失效模式的起因可能是子系统(低一级的零组件)中的转向拉杆与工字梁干涉或者装配中限位螺钉过长或过短,造成整车运行中转弯干涉,转弯半径过大或与轮胎非正常接触。
#d1cm#page#
因此,对一个特定项目及其功能,列出每一个潜在失效模式,前提是这种失效可能发生,但不一定发生。这种信息的来源可以从以下几个方面获取:售后维修人员或销售人员统计的常见故障、客户(设备使用者)在使用中抱怨或意见,以及以往运行不良的研究、关注点、问题报告等。而针对这些失效会造成什么后果,即失效模式对功能的影响,应该跟客户感受的一样,重视并分析它。这里的客户也许是内部的客户(比如职责不同的同事),也可能是外部最终的客户,应该清楚地说明该失效模式是否会影响到安全性或与法规不符,还要考虑不同级别的系统、子系统或零部件之间还存在着系统层次上的关系。一个零件的断裂也可能引起总成件的失效,最终导致客户的不满。比如在重卡前轴上收集的常见故障有:制动失效、制动发抖或跑偏、前轴吃胎、车轮螺栓失效、轮毂轴承耍圈及轮毂断裂等等,对发生过的失效我们都要一一列举并分析造成这种失效后果的起因,或者说我们要结合核心小组的能力尽可能预见失效的后果。
再者,需要对失效进行严重度和频度的核定。严重度是对一个假定失效模式的最严重影响的评价等级。例如前轴轮毂强度不足断裂,导致整车停止运行,客户严重抱怨严重度等级自然就很高;装配结合面密封不严,导致漏油影响美观但车辆可以运行,这个严重度等级就稍微偏低了。至于频度,是指在设计的寿命中某一特定失效起因或机理发生的可能性,它主要是靠一个频度级别直观地显示出实效发生的几率,设计人员如何在设计初期让几率高的失效模式降低或引起足够的重视。
最后,需要重视的就是我们已经分析或总结了各种的潜在失效模式和后果,以及频度严重度等,有什么建议或措施来避免或减少这些失效,需要在框图中填写建议措施和完成日期。建议措施的目的是经由设计改进来增加客户的满意度,直观的做法就是减少严重度、频度。如轮毂断裂的失效结果,造成这种失效的起因可能是零件材质的选用不当造成,在某种工况下强度不足断裂或者结构设计时,存在薄弱环节,导致在薄弱环节处断裂。那么建议措施就可以参照以往的成功设计来选取材质和设计结构,或者进行强度试验来探测强度,最终达到减少其断裂或者发生频度的目的。
3. 成功实施FMEA的条件
要成功实施FMEA,首先要重视事实也就是已经发生的失效;其次需要团队协作,包括项目小组内部的互相协作,更包括外部人员的互相协作,互通有无,总结所有人的智慧和经验才能做出最切合实际的分析,如果只是简单的填表式的分析,则这种失效分析根本不具有参考价值。
4. 后续应用FMEA的完善措施
针对前期我们应用FMEA做失效分析的工作工程中,需要改进的方面有:
⑴之前对产品的潜在失效模式分析不够全面,获得的信息输入不完整,造成此类事情的原因是与客户的沟通不够完善,后续需要加强联系以获得更加全面的信息;
⑵对潜在失效模式的建议措施比较单一,现行的控制预防措施也比较单一,在遇到失效发生的情况下解决问题的手段比较简单,长远的解决方案比较少,后续的工作中应加以重视。
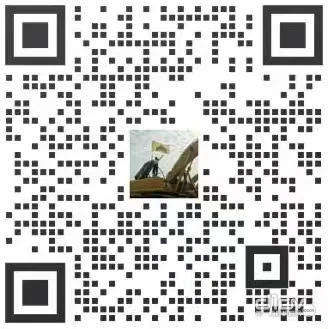
期待你的精彩评论