汽车起重机吊臂汽车起重机吊臂
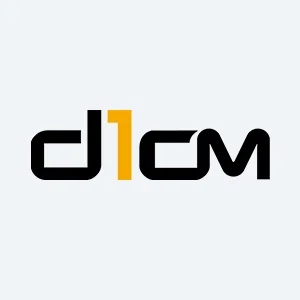
吊臂是汽车起重机最重要的工作部件,吊臂的设计直接影响着起重机的起重性能。吊臂结构质量一般占整机质量的13%~15%,而且随着大吨位汽车起重机的开发,这一比重会更高。如何在不影响起重性能的前提下减轻吊臂质量,改善整机性能是设计吊臂要面对的关键问题。目前,行业内所采取方法主要有两种:⑴应用高强度材料;⑵改进吊臂结构,采用多边形(甚至大圆弧、椭圆形)吊臂来替代四边形吊臂。 随着大吨位起重机产品
随着大吨位起重机产品的不断开发,高强度钢板被大量应用,吊臂强度也大幅上升,但若发挥全部材料的强度,吊臂结构变形也会加大。变形增大的结果,将使吊臂轴向力引起的弯矩成为一个无法忽略的因素。所以,在非线性条件下,就需要应用新的算法,在考虑吊臂的变形情况下对吊臂进行重新设计计算。
吊臂设计非线性计算
1.几何建模
为了实现吊臂计算程序化、通用化,需要将吊臂几何形状、物理状态等参数化,这主要包括以下3部分:⑴吊臂截面几何形状,通过角度、边长等尺寸进行确定;⑵确定各节臂质量、长度以及重心位置;⑶确定性能参数,包括单绳起升速度、起升滑轮组倍率等。
2.非线性迭代计算流程
以柳工QY70型汽车起重机吊臂为例进行计算。该起重机主起重臂由基本臂和4个伸缩臂组成,伸缩方式为顺序加同步伸缩方式。
先对吊臂进行受力分析。在变幅平面内,吊臂所受载荷有:⑴吊重;⑵臂架自重;⑶起升机构钢丝绳拉力。计算吊臂上各危险截面弯矩时,要加上各力在轴向上的分力与轴向力臂的乘积。
在回转平面内进行受力分析。吊臂所受载荷有:⑴吊重偏摆载荷;⑵风载;⑶臂架自重;⑷起升机构钢丝绳拉力。同样,计算吊臂各危险截面弯矩时也需要考虑上述载荷的轴向分力引起的弯矩。
迭代过程假设吊臂仰角不变,通过臂端挠度的变化来进行反馈迭代。
通过赋初值,先计算各危险截面处弯矩和横向力,然后通过材料力学求挠度和转角公式,求各节臂的挠度和转角,通过累加,由此可求出吊臂总的挠度。将此挠度和初始挠度比较,如果满足设定条件,则输出各截面的弯矩、横向力和轴向力,如果不满足,则将此挠度赋给上一次的挠度,并返回重新计算弯矩、横向力,并求出新的总挠度。以此循环,直至前后两次循环得出的挠度满足我们设定的条件,则认为吊臂已经平衡,所得出的值为在吊臂变形平衡后的值。回转平面计算思路与变幅平面相同。
在循环过程中,是以总挠度的变化作为判定条件的,而总挠度是通过求各节臂的挠度和转角来求得的,挠度和转角的计算公式通过实际模型用材料力学公式推导求得。
3.进行强度、局部稳定性校核
用非线性迭代方法求得了各危险截面的弯矩、横向力和轴向力,由此则可以求出吊臂截面上各点的应力值。严格按照起重机设计规范GB/T3811的有关内容,进行吊臂局部稳定性和强度的计算,并用各自的许用应力进行校核。
有限元分析计算
1.有限元模型建立
有限元模型的建立,既要如实反映结构特征,又要尽量降低模型的复杂程度,本着这一原则,我们对吊臂进行了简化。因为吊臂主要受压弯作用,我们用梁单元beam181建模。按实际各节臂的臂长、搭接长度、滑块位置画线,然后将先前建立各节臂二维截面属性赋给各节臂。吊臂头部和滑轮都进行了简化处理。对模型进行定义单元类型、材料属性等,然后进行网格划分。
2.加载和添加约束
按实际受力进行分解后加载到吊臂,包括吊重轴向和横向分解力、钢丝绳拉力和重力等。臂与臂之间耦合了x、y、z三个方向的自由度,并对吊臂后铰点处进行了约束,除了y方向的自由度不约束外,其它5个自由度都进行了约束,另外对变幅油缸下铰点和钢丝绳也进行了约束。加载约束后,用通用求解器进行求解,得出计算结果。
3.计算结果与有限元计算结果比较
选取两种工况进行比较,一种是全伸臂,即臂长为44.2m,仰角79°,吊重为10t,起升滑轮组倍率为3的情况;另一种是第一节油缸全伸,二节油缸伸1/3,即臂长为27.5m,仰角79°,吊重为20t,起升滑轮组倍率为4的情况(比较结果见表1、表2所示)。通过比较可以发现,非线性计算方法和有限元模拟两者得出的结果相近,说明本计算结果准确。
实验验证
在现场进行实验验证时,需要有选择的采用在吊臂上贴电阻应变片来测量吊臂的应变,应变片布置跟程序计算所选危险截面上的各点一致(实测结果与计算结果比较见表3),最大误差不超过20%,考虑到实际测试过程中风载、砝码重量、臂架上翘量、应变片位置的完全准确性等等各种误差因素的累加,计算结果与实测结果可接受,表明程序计算结果真实可靠,对设计研发提供很大帮助。
本文使用了以非线性迭代算法开发的汽车起重机吊臂设计软件,对柳工QY70型起重机产品的吊臂进行了计算,而且在选取相同工况的情况下进行了有限元模拟,最终比较结果得出两者误差在5%左右。通过现场试验验证,结果也相吻合。这表明本计算方法是切实可行的。
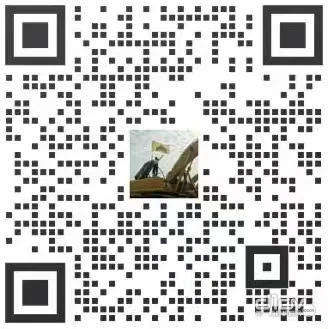
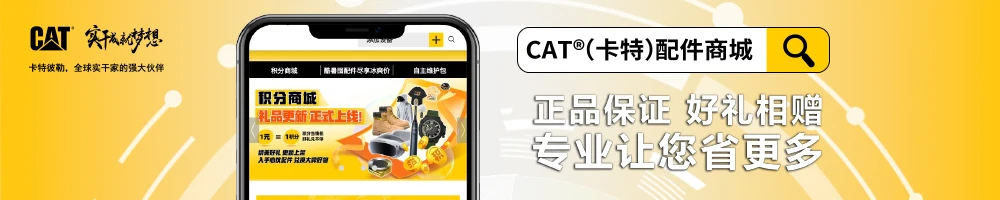
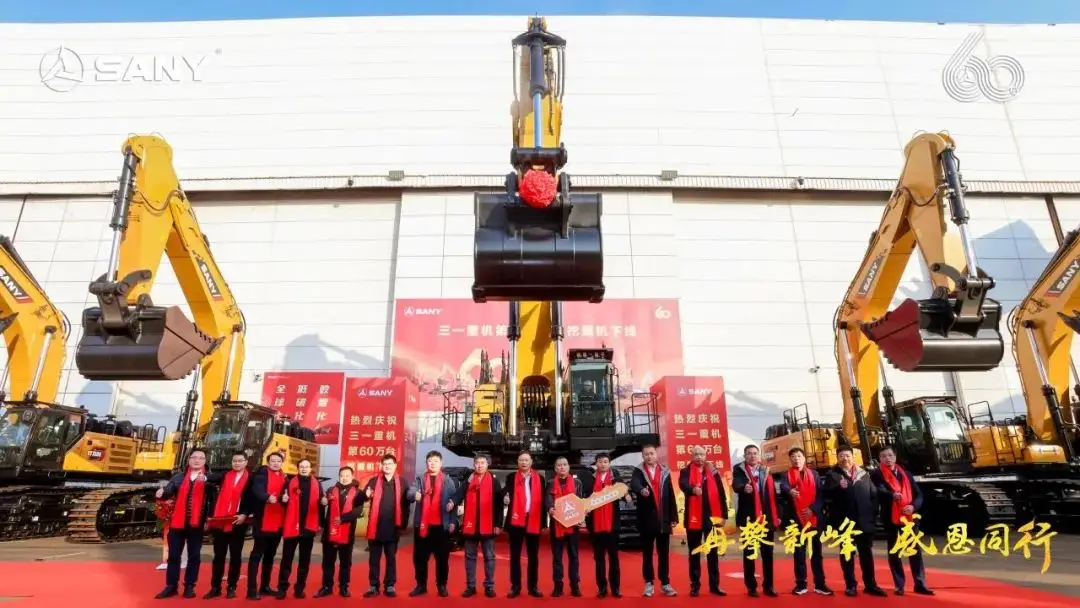
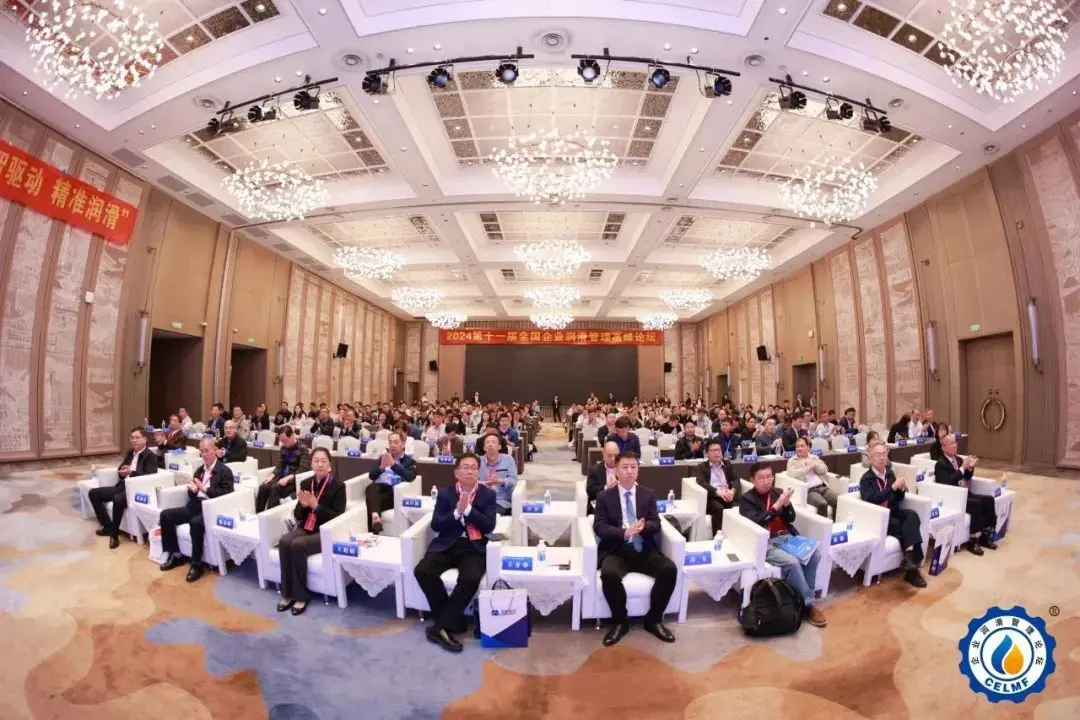
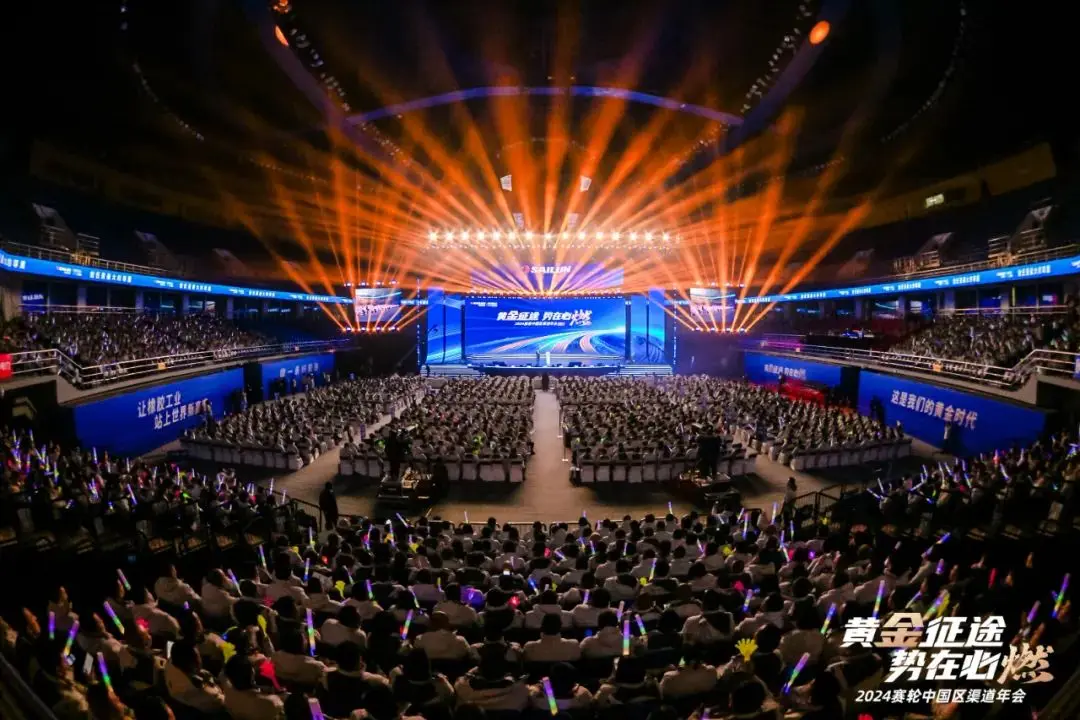
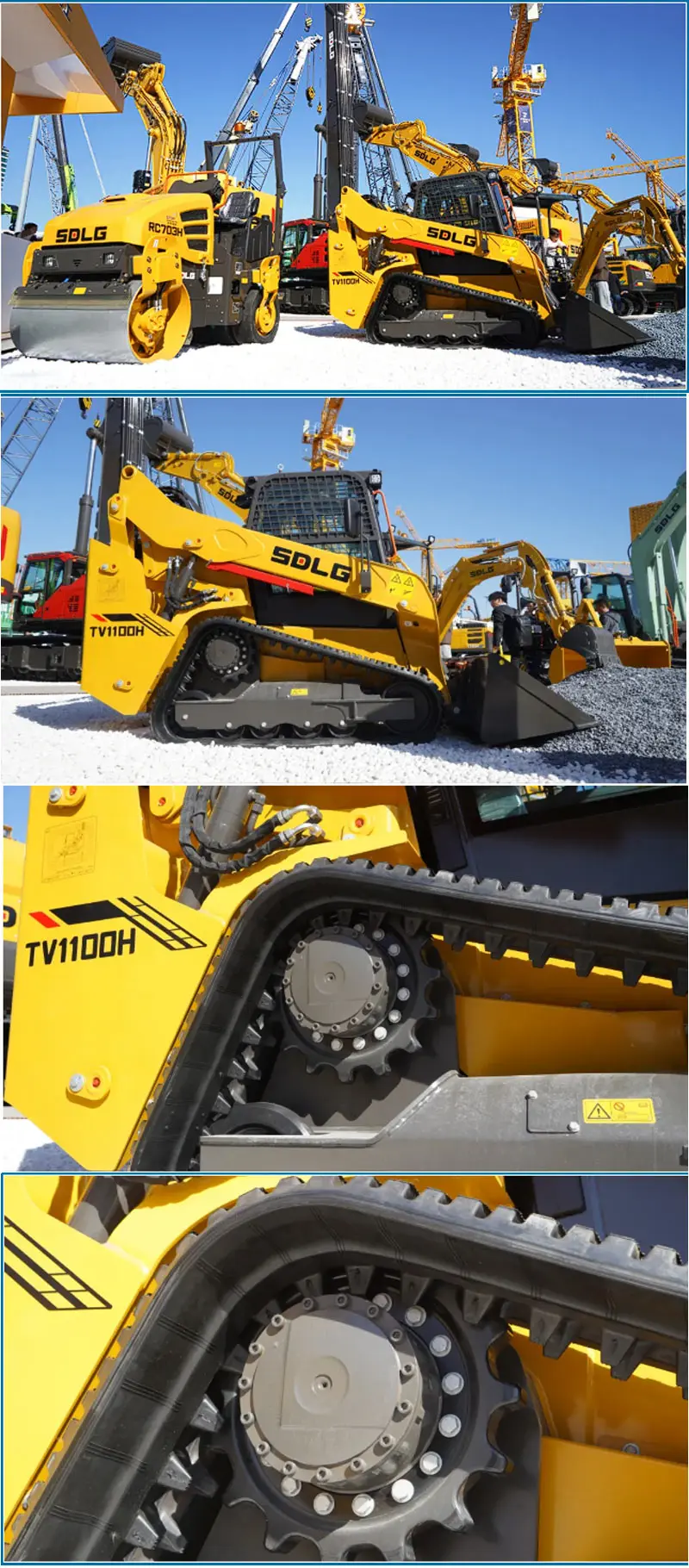
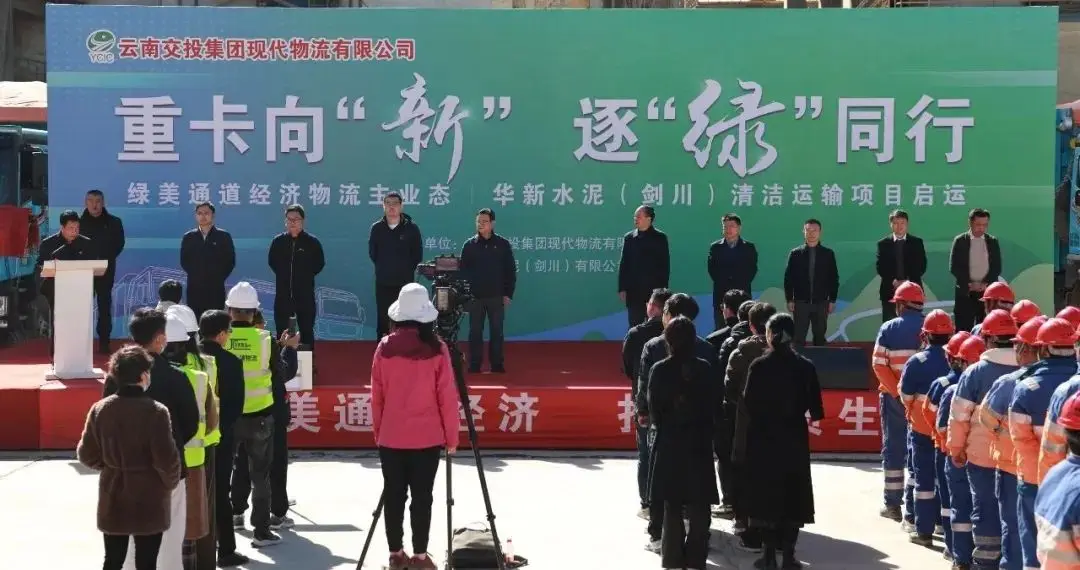
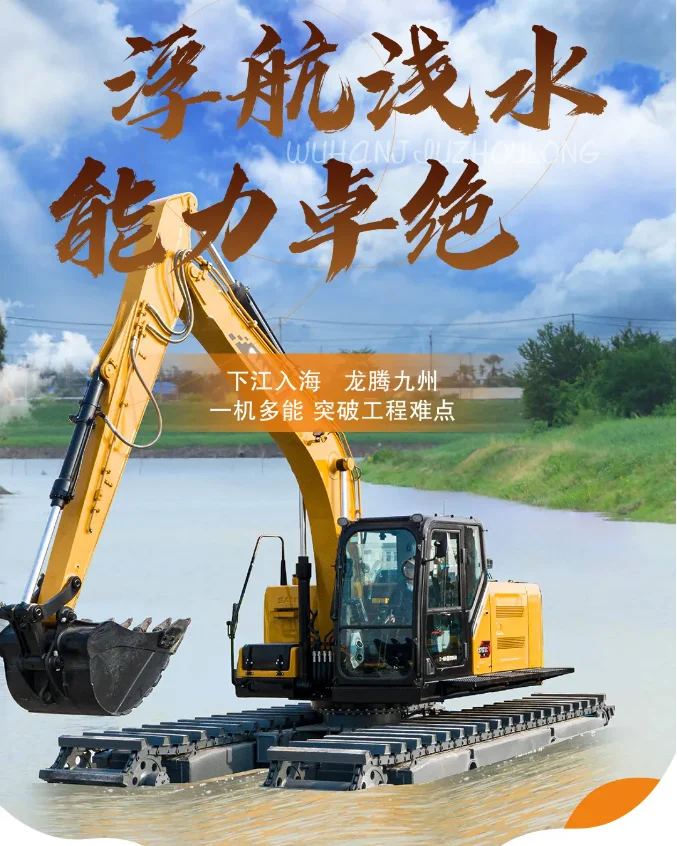
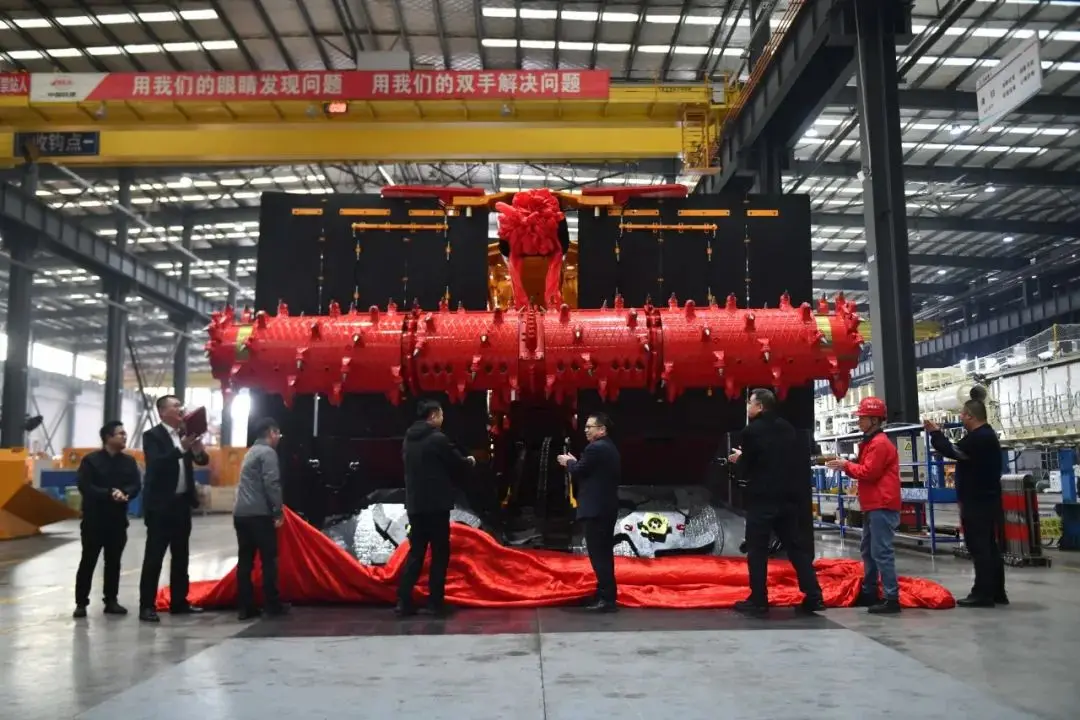
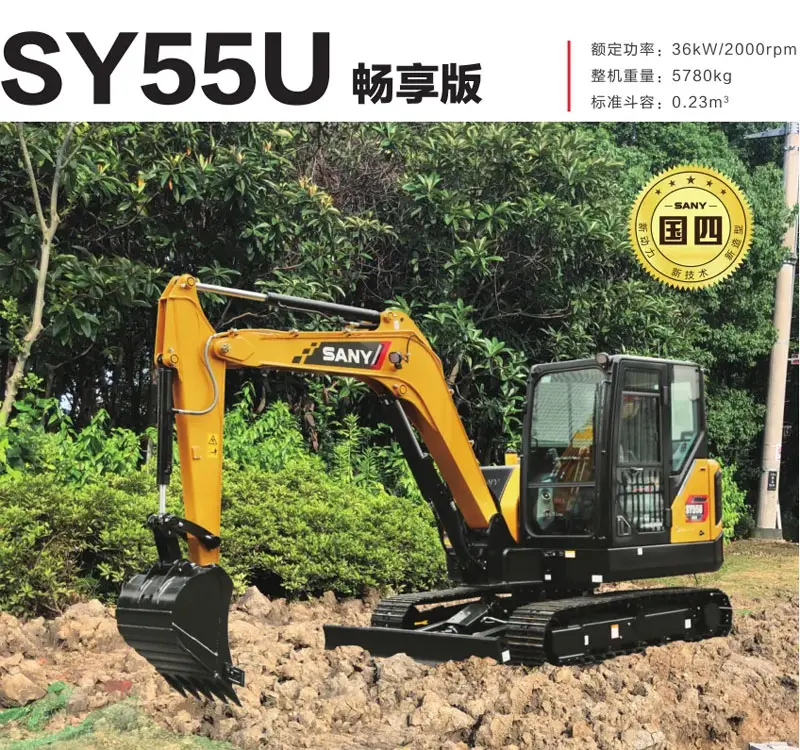
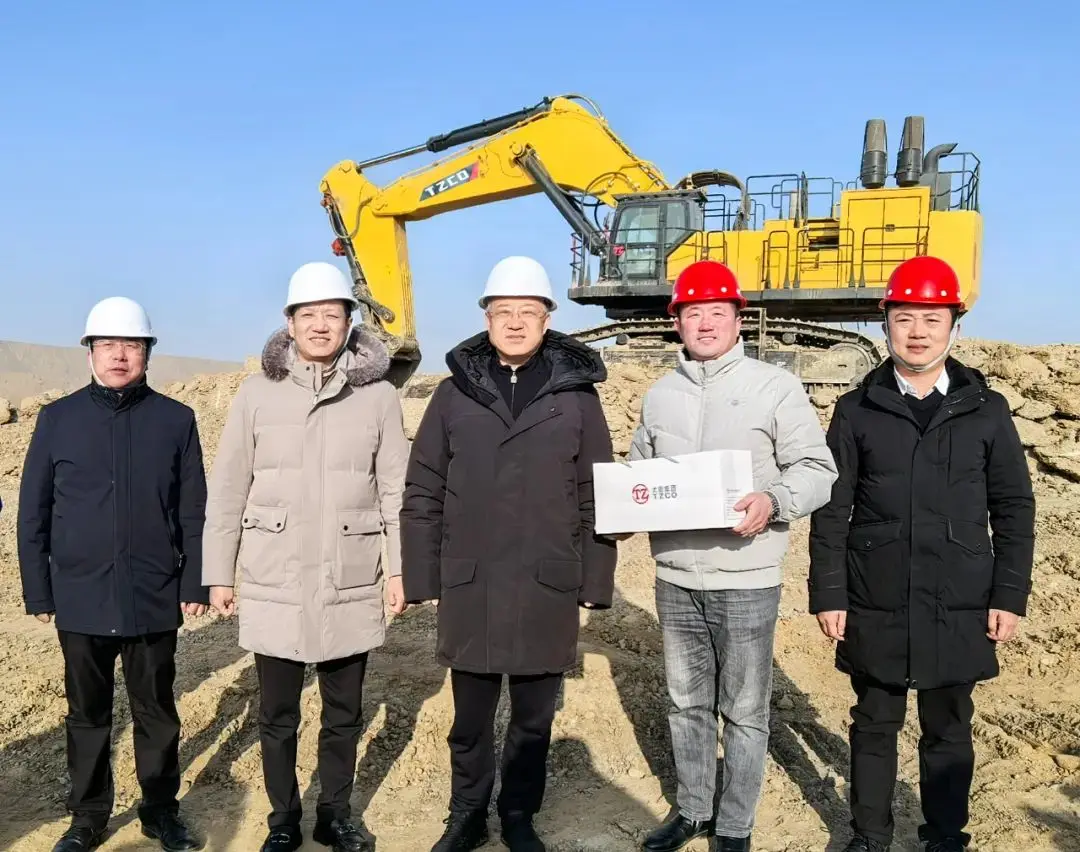
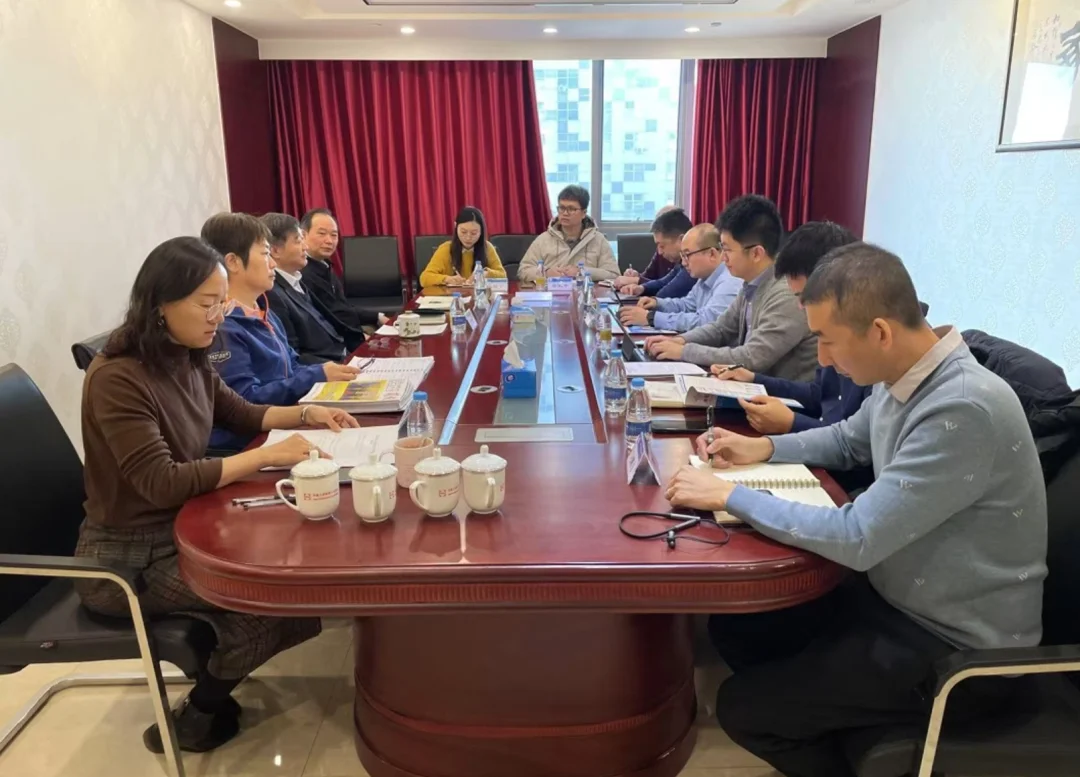
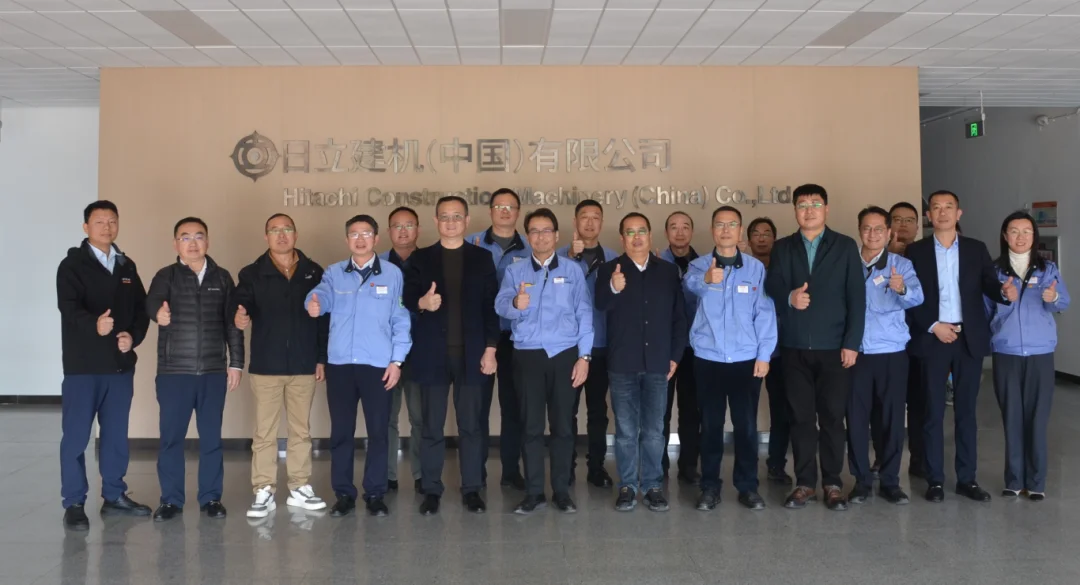
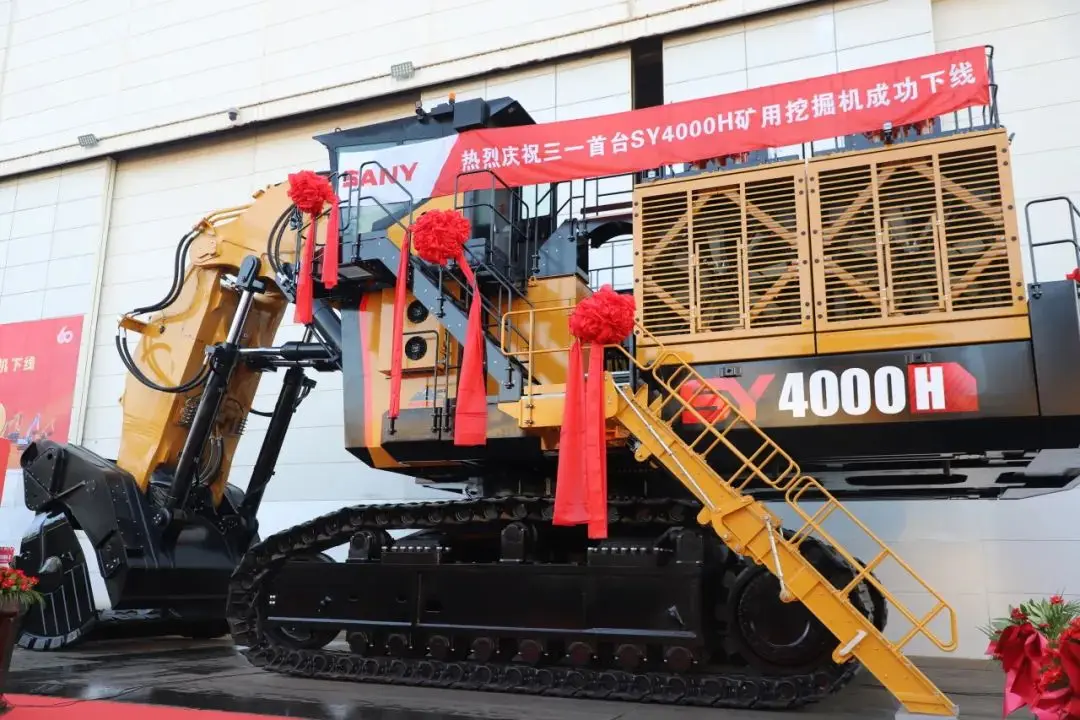
期待你的精彩评论